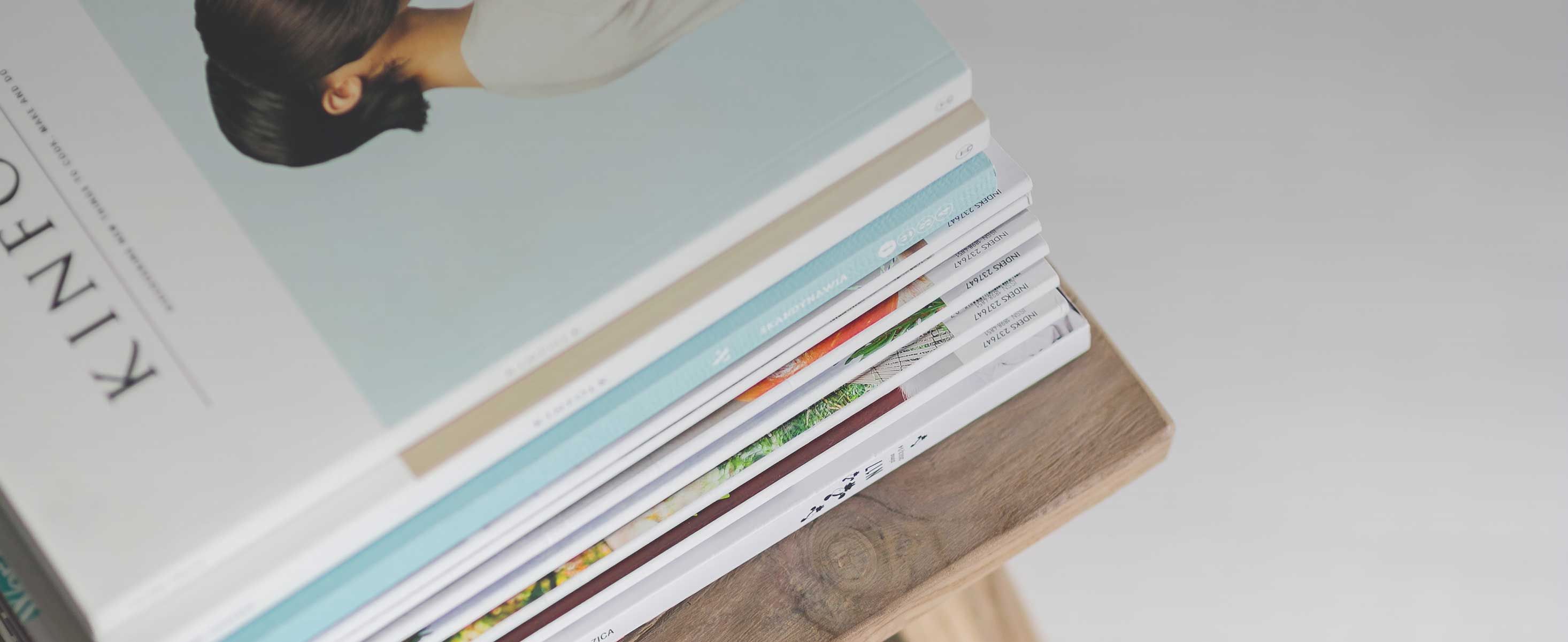
2 minute read
Metrology as a fundamental aspect of simulation, and by extension the design process
SECTION 3 Key Themes
Metrology as a fundamental aspect of simulation, and by extension the design process
Advertisement
Trends & Drivers TD3 TD6 TD10 TD15 Research Themes RT3 RT5 RT7 RT11 Capabilities & Enablers CE1 CE3 CE4 CE5
Modelling and simulation are established engineering techniques and are often used as part of the design process to evaluate the function and performance of engineering designs. By using known variables such as the geometry of a part, the material qualities, operational environment and loading conditions, it is possible to simulate a part and predict with significant accuracy, how the part will behave in service. The same ideas can be applied to manufacturing processes to simulate the tool workpiece interaction and predict the impact on the finished part. However, quantifying all variables in the manufacturing environment presents a substantial challenge.
Metrology is a key element in overcoming these challenges. However, it not just the case that the manufacturing variables must be measured once and then used in isolation as values in a calculation. A historic database of previously measured data can be used to develop a model, but variables change in real time. Closed loop control requires a process to be continually monitored, with an estimate of the data uncertainty, to account for the dynamic situation. A holistic approach to manufacture which integrates metrology into all stages of design, production and evaluation must become the norm. Consequently, advances will come in stages with the development of true digital twins being a long term goal. Generating this data can present a significant barrier at the research stage. Companies can often be reluctant to share process data and performance results due to commercial sensitivities. Crucial to overcoming this barrier is the formation of strong partnerships between academia and industry. Research teams must be supported by competent and sympathetic business engagement teams who can help guide the process and develop robust contractual agreements which build confidence. The ability to simulate manufacturing processes presents opportunities across many fields but it will be fundamental in facilitating agile manufacture, optimally choosing the right machine and process within a set of given performance constraints. This is especially attractive to companies engaged in the low volume/one off manufacture of extremely high value components. In these scenarios, there is little opportunity to observe the manufacturing process and make incremental improvements; there is a need to get it ‘right first time’. In these situations, any time saved in the design, machine set up and machining stages can represent significant productivity gains with waste, cost and lead times all reduced. Companies engaged in low volume/high value manufacture are often tier 1 and 2 suppliers to high value industries such as aerospace and defence. The ability to pass these cost savings up through the supply chain may provide a significant competitive advantage when attracting new business.
Key message
The ability to accurately simulate and predict the outcome of machine/ workpiece interactions presents a substantial opportunity for manufacturers. Embracing this technology will enable more efficient, agile manufacture to reduce waste, cost and lead times.
Key message
Developing true digital twin systems presents a significant challenge due to the vast number of processes, materials and environmental conditions which must be understood. Crucial to achieving this is the ability to gather real world data from a broad range of manufacturing environments. Universities must build strong partnerships with industry where both parties have a willingness to share data and have close interaction if this is to be possible.