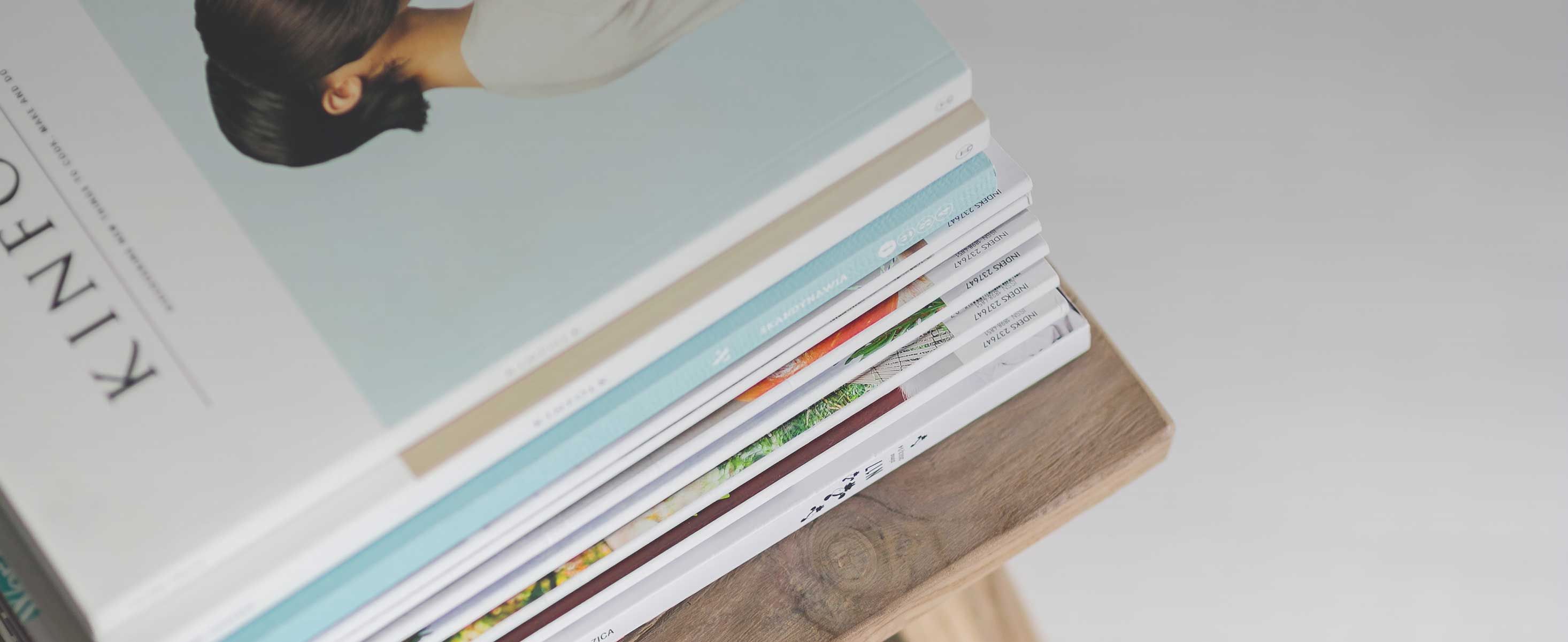
2 minute read
CROSSROADS CARE CROOKES & SON TRADITIONAL JOINERY
Crossroads Care, which delivers over 70,000 hours of home care each year and supports over 700 patients every day, used the help provided by the Digital Innovation Grant scheme to develop a new patient care management system.
Designed to provide families of those receiving care treatment with peace of mind, as well as reducing the administrative burden upon its care staff, the new patient management system delivers real-time updates, as well as replacing its paper-based systems with an electronic alternative.
Advertisement
Since developing its new patient management system, the Rotherham-based charity has not only succeeded in reducing the amount of time carers spend filling in forms, it has also helped to improve the way it communicates with its patients and their families, having successfully developed a family app, allowing family members of those receiving care to share details of carer’s visits with their loved ones. Updated in real time, the app can also inform patients if they are being delayed, as well as helping Crossroads to manage its staff more effectively, helping to reduce the amount of time its care staff spend travelling between appointments.
“Crossroads is a unique organisation that delivers a range of care support to people living across South Yorkshire. The funds we received have helped us to implement a new way of working, which has helped us to improve communication between patients, their families and staff. It’s been a genuine game changer for our organisation and one that is already helping hundreds of people every day.”-
Faye Warner, Chief Operations Officer, Crossroads
Care
The Digital Innovation Grant helped family-run Crookes Joinery to successfully boost its production capacity by over 50%. Father and son team Robert and Lee Crookes specialise in traditional windows and doors used in historical buildings.
In recent years, the company recognised that changes in the way wood is treated can mean that the wooden frames it manufactures can provide an eco-friendly alternative to uPVC double glazing. Having spotted a niche in the market, and with rising demand for the company’s wooden framed doubleglazed windows, which can last for more than 60 years, Lee and Robert recognised that they needed to embrace new forms of technology in order to fulfil their growing order book.
The grant was used to purchase software for a programmable CNC tenon machine, previously purchased by the business, allowing the traditional mortice and tenon joints to be automated. The result proved to be immediate with production increasing by 40% and crucially, the accuracy of the machine eliminated the need to hand finish the joints. As a result of the investment, the company now has the confidence to explore purchasing other time-saving devices to boost its production, and to meet demand it is hoping to train the next generation of joiners by recruiting new apprentices.
“Specialist equipment can be a significant business investment, and as a small family-run business, we knew that although purchasing the mortice and tenon machine would help us to increase our levels of production, to make the most of the machine we would also need to invest in the CNC software. It transformed our business almost overnight.”
Lee Crookes, Director, Crookes & Son Traditional Joinery