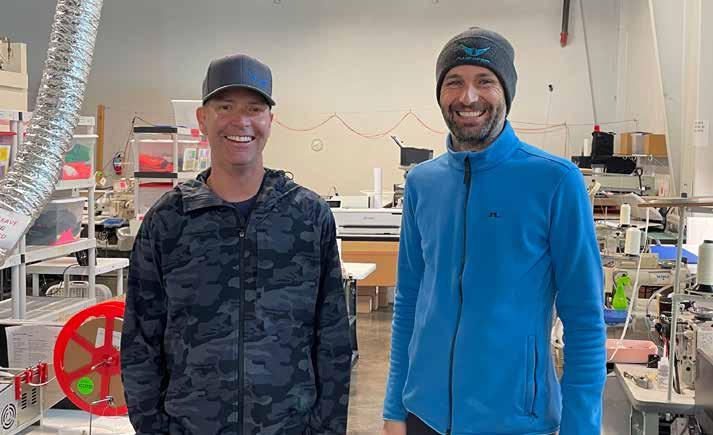
4 minute read
Homegrown Innovation
Behind the scenes with Fluid Wings
by Steve Mammano
: The early days of Fluid Wings are a story of two highly experienced pilots looking to push the limits of the sport. Founders Kevin Hintze and Scott Roberts met in 2008 while both being heavily involved in the industry. Hintze learned to fly in 1996 at the Point of the Mountain in Draper, Utah and worked for SuperFly and Cloud 9 for many years. He is an accomplished aerobatic pilot and had the opportunity to fly various prototype wings over the years. Roberts is a highly experienced competition canopy pilot with countless days at the drop zone and a master’s degree in engineering. Both have always loved spending time tinkering with the designs of their wings to produce higher performance and modifying current designs.
Soon after meeting, the two began dreaming of a paraglider design that could provide a high starting altitude without towing. Towing came with many logistics and was not always immediately available. The idea was to make a wing that could be jumped from a plane at the drop zone in order to have a long flight and go lap after lap. This had been attempted before by a flying pioneer named Jimmy Hall. Hall called it “para-diving” and had rigged a system to jump a standard paragliding wing from a plane. Hintze and Roberts wanted to design a wing specific to this application, which had not previously been done. They dubbed this endeavor “Project Mayhem.” After three months of design and sewing, they created the Rubicon, a full-size glider meant for ground launch testing. This was then scaled and redesigned to be deployable, which resulted in the Cloudchaser.
When the day came to jump the Cloudchaser, both were a bit nervous. After some back and forth on who would try it first, they decided to draw straws. Kevin took it up in the plane first. “It was not great. It malfunctioned,” Kevin says, laughing about it now. “I got down safely, we did some modifications on the ground, and then it was Scott’s turn. The jump went great, and it was a success.” Hooked on the excitement of flying something they had made from scratch, they began work on improving the wing. The Cloudchaser 2 was a work in progress that was never completed. Instead, they decided to focus their efforts on higher-performance swoop parachutes.
From there, the two began working on more skydiving canopies, paragliders, and speedwings. This was purely a hobby to make something enjoyable to use. Kevin was working as an instructor full-time in Utah and commuting to Florida on some weekends to test and design with Scott. Eventually, they decided they had to commit one way or another to formally starting a company. On one trip to Florida, they decided to flip a coin and make a choice. The coin landed, and Fluid Wings was born.
Development
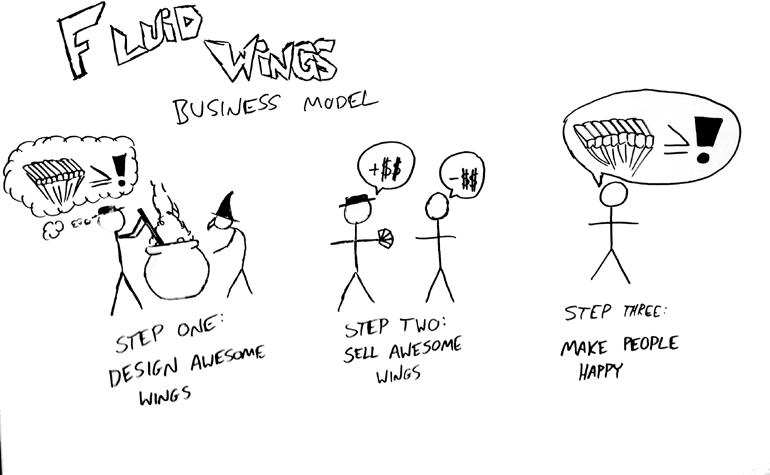
Kevin returned to Utah in his station wagon, fully loaded with sewing machines—so loaded that the rear suspension blew out. Upon returning, he began working on the Sandy, Utah headquarters of Fluid and hired their first Utah employee in 2015. They knew that there had been few innovative products to break onto the skydiving scene in recent years and that an opportunity awaited.
“From the beginning, our goal has been to create a wing that is great to fly. Building Fluid as a company has allowed us to pursue this goal,” says Kevin.
Starting with an entry-level canopy, the Fluid lineup has since grown to its current offering of eight canopies and become a serious contender in the competition canopy market. While other U.S.-based manufacturers work on skydiving and BASE parachutes, Fluid remains the only U.S.-based glider design and R&D company. With bases in Sandy, Utah and Deland, Florida, and a staff of passionate pilots with a desire to innovate, the company is preparing to impress the airsports industry in the near future. The Fluid factory in Sandy is an efficient, bustling warehouse with many moving parts. Computers with open screens of three-dimensional glider designs show constant work and improvement. Walking through, one can see the rolls of material being hot-knife CNC’d, collected, organized, sewn, and packaged. Once a wing is completed, it is labeled, packaged, and sent to the awaiting pilot. The whole process from idea to reality occurs within a few rooms. Employees can choose their hours, allowing them to coordinate their work day with good flying times. Consumers can rest assured that their Fluid products are designed, tested, and made by fellow pilots.
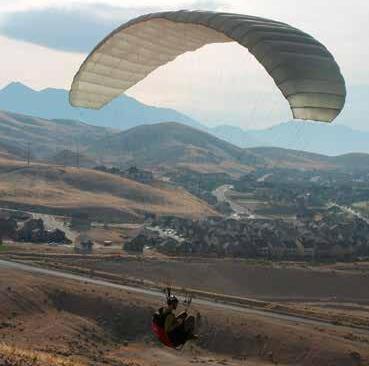
“The inspiration and design are completely based on the need of the pilots and feedback from them,” Kevin says. Since they are based near the seemingly endless flying opportunities near Salt Lake City, employees can easily and quickly test their wings. “One of our test pilots is out with a prototype right now. He works full time designing and assisting in the factory, and then still has time to go out and test them,” he says. With their ability to design a canopy on the computers and sew it all in-house, it is reasonable to go from an idea for a wing to flying a prototype within a few short days. Modifications and improvements, however, are never done.

For example, the Loki, Fluid’s first speedwing, served as a launching point for new products in this category. An updated version, the Loki 2, was recently released. Although it is possible to launch into the market with a high-performance model, Fluid found it is easier to bring a low-performance design to the market first. Based on this experience, it is now easier for them to work on higher performance speedand miniwings. Fluid is currently working on exciting projects that will join the Loki 2 in their wing lineup in the near future.
Future of the Company
Having always been a paraglider pilot at heart, Kevin is looking forward to expanding into the glider market within the next year and beyond. Due to high production and labor costs in the U.S., paraglider production is not possible on home soil. The company began researching expanding to foreign production in 2019 and has since formed working relationships with factories in Europe and Asia. Tracking down manufacturers willing and able to create the desired product for Fluid proved difficult.
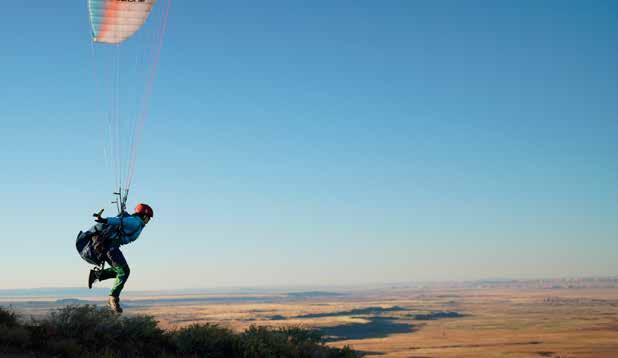
“The wing manufacturing business is pretty hush-hush,” Kevin says, “Other companies are