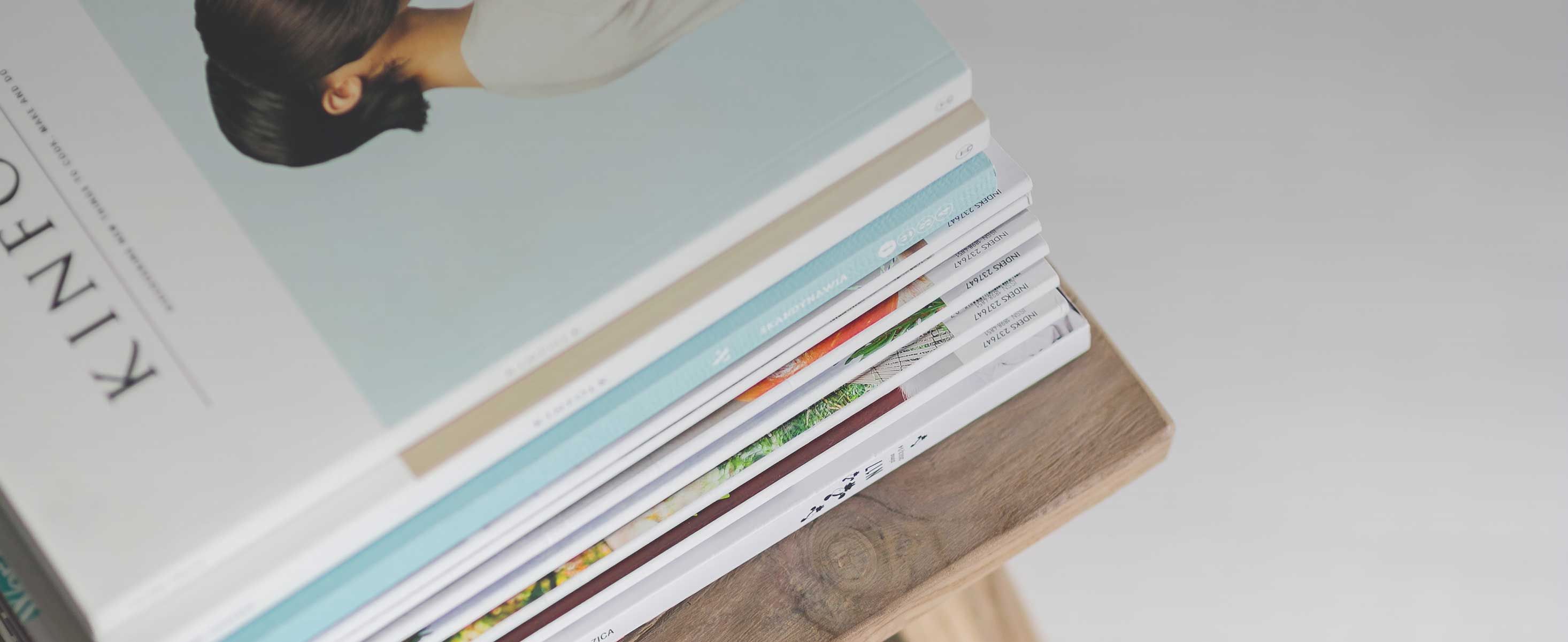
7 minute read
HAZARDOUS FUELS/MITIGATION WORK
criteria above to apply for Firewise recognition. Firewise Communities USA is a tremendous accomplishment to achieve, but it also is paramount in continuing education on the latest preparedness research and materials. Check out: (http://firewise.org) - for QR code see 6.14 on page 169.
FIRE ADAPTED COMMUNITIES Fire Adapted Communities is the concept that communities are knowledgeable and engaged participants in fortifying infrastructures and landscapes that reduce the need for extensive protection actions and enable the community to safely accept fire as part of the surrounding landscape. It is reached by building a foundation using the above programs. More information can be found at (https://fireadapted.org/) - for QR code see 6.15 on page 169. Division employees are encouraged to become an affiliate member of the Fire Adapted Communities Learning Network to keep updated on the issues that impact our involvement with the communities in Utah at (https://fireadaptednetwork.org/) - for QR code see 6.16 on page 169.
WILDFIRE MITIGATION EDUCATION TRAILER The Wildfire Mitigation Education Trailer is designed to be used for indoor/outdoor events and is an excellent platform for the distribution of materials. There are brochures and pamphlets stocked in the trailer. A nearby power source is necessary for the trailer to operate. It is housed in the Salt Lake/Clearfield Warehouse. To schedule the trailer, contact your area WUI staff that has access to the google calendar. Utilizing the trailer will help Division personnel take an active role in wildland fire preparedness in their counties and areas.
HAZARDOUS FUELS/MITIGATION WORK
Fuel reduction projects are a significant part of the Division’s work with communities and cooperators. These projects may be on federal, state or private lands. Typically, the removal or modification of fuels on private lands occurs only after five basic steps: 1. Completion of a Community Wildfire Preparedness Plan (CWPP) 2. Acquisition of grant funding for identified projects - collaborate with Area WUI Coordinators 3. Development of scope of work 4. Signed permission forms from involved landowners 5. Cultural/archaeological clearances obtained
The completion of fuels work can be accomplished through the utilization of state/county resources, local contractors or inter-agency MOUs. Fuels reduction projects may utilize several methods to achieve the desired outcomes of a project, including hand removal with chainsaws, herbicide application, burning, or mastication. Chainsaw operation and burning activities will be accomplished using established standard operating procedures. Herbicide use will follow safety measures and protocols defined by herbicide applicator licensure and the manufacturer’s label instructions. Mastication will be employed with the protocols that follow.
LONE PEAK CONSERVATION CENTER (LPCC) RESOURCES When not assigned in the National Mobilization System, LPCC resources are available for natural resource management projects. LPCC provides qualified crews of 5-20+ individuals. Crews are equipped with and qualified to use power saws, a variety of hand and power tools and LPCC chippers. Contact LPCC Operations to arrange assistance with natural resource and fuels mitigation projects. • Hourly rate is $26/hour for projects which include all personnel, equipment, vehicle mileage and per diem costs. If overtime is encountered (rare event), there IS NOT an additional charge, it is absorbed in the rate structure. • LPCC will provide basic equipment, saws, pole pruners, brush cutters, chippers and Personal Protective Equipment (PPE). LPCC staff will coordinate actions with a designated Area representative. • The Area will provide a scope of work defining objectives and timeframe which may include photos, maps and emergency contact information. The Area will provide logistical information for the crew supervisor to aid with water needs, trash removal options, human service needs and any other project specific items. • LPCC staff will complete crew time reports (CTR) that must be signed by the Area to verify hours worked. Travel will be itemized to assist the Area in requesting reimbursement from the travel fund. LPCC will provide cost estimates and completion data or photos, if requested, to the Area within thirty days of completion of work. • LPCC will charge for equipment rehab with a maximum of ½ hour of crew time daily. • Travel time will be billed to the project UNLESS otherwise determined by LPCC. • Crews will be used as a labor workforce. Specific timeframes and use parameters for each crew will be established in advance of the expected project start date to alleviate confusion or scheduling conflicts. • The Area will complete a final closeout with the crew supervisor to review work for quality and completeness, as well as approve time documents. The Area must present any dispute action at that time or the project will be considered completed to all previously established standards and budget constraints.
Any issues unresolved in the field can be directed to the LPCC Operations Coordinator for discussion within 45 days of project completion.
MASTICATION EQUIPMENT The Division has purchased and/or manages several chippers, tractors, and masticating heads to dispose of wildland vegetation and hazardous fuels. This equipment can be extremely dangerous. If not used properly these machines can cause serious injury or death. Improper operation can also result in costly damage to equipment. Therefore, anyone operating any of this equipment shall abide by the following guidelines:
Due to the extreme danger involved with the improper use of this equipment, FFSL has decided that only properly trained employees of the Division may operate the equipment. On rare occasions, volunteers who have signed up with the Division may also operate the chippers. However, before operating any equipment, volunteers must attend the same annual training as Division employees and be signed off prior to operation. Volunteers will also be
required to complete and sign a liability waiver before working for the Division. Chippers Prior to operating the chippers each person must participate in the following training annually. • Video training: Vermeer (or manufacturer’s) Brush Chipper Operations & Safety Training • Video training: Vermeer (or manufacturer’s) Knife/Drum Maintenance • Receive copy of the operator’s manual • Understand and explain the following: » Safety decals » Symbol identification » Controls » Safe starting procedures » Shutdown procedures » Transporting procedures » Chipping brush » Winch operations (if applicable)
Each operator will be required to complete an on-site review of each system, and a copy of the review will be maintained in each employee file. On-site review shall be an annual event, prior to operating.
Prior to operating a chipper, the operator and all team members will review the appropriate Job Hazard Analysis (JHA) forms and conduct “tailgate” safety meetings daily. This will help ensure that clear and proper communication between team members takes place during chipper operations.
Ensure that sufficient tools/parts/fluids for repair and replacement are appropriate for the machine that is being operated. These tools/parts/fluids need to be readily accessible in the area of operation. It is important to replace worn parts/ top off fluid reservoirs for safe and efficient operation.
Prior to Operating the Chippers, Operator Will Complete the Following Daily: Engine and Drivetrain • Check battery electrolyte level and cable conditions • Check air cleaner condition • Check engine oil level • Check coolant level • Check radiator for debris
Hydraulics • Check hydraulic fluid level • Check hydraulic components for leaks or damage • Check hydraulic control for proper function
General • Check the drive belts for damage and proper tension • Check all shields • Check and lubricate all fittings • Check the wheel lug nuts • Check tires for proper air pressure • Check tracks for proper fit • Check operation of the taillights when chipper or trailer is attached to a vehicle • Check for debris buildup along the chipper frame, radiator, exhaust & valve covers.
Extremely important - Debris buildup may cause overheating or a fire hazard. • Check the condition of teeth and bolt tightness • Check all bolts after every 40 hours of operation
All Persons Working in and Around the Chipper Will Wear the Following PPE: • Hard hat • Safety glasses or goggles • Hearing protection • Work boots • Gloves (tight fitting) • Respirator/mask in dusty conditions • Long sleeve shirt • Work pants in good condition
Avoid wearing jewelry such as rings, wrist watches, necklaces or bracelets. Long hair should be confined, and any loose-fitting clothing removed or secured prior to chipper/Bull Hog use. TraCTors and Bull hogs Though most of the above information relates to chipper operation, the same principles and practices shall be followed during the operation of a tractor or Bull Hog unit. This type of mastication equipment presents a unique set of safety issues that must be addressed prior to its operation. Safe operation includes consideration of the following: • Pre-operation walk-through • Safety zone in relationship to equipment operation • Uneven ground operation • Use and location of spotters • Operation in and around structures • Restriction of public within area of operation • Ground/soil disturbance • Operator communication • Reference accepted JHA form for the safe operation of mastication units
REFERENCE UCA 65A-8-211: Closed fire season — Notice violations — Burning permits — Personal liability — Exemptions from burning permits UCA 76-6-104 Reckless burning