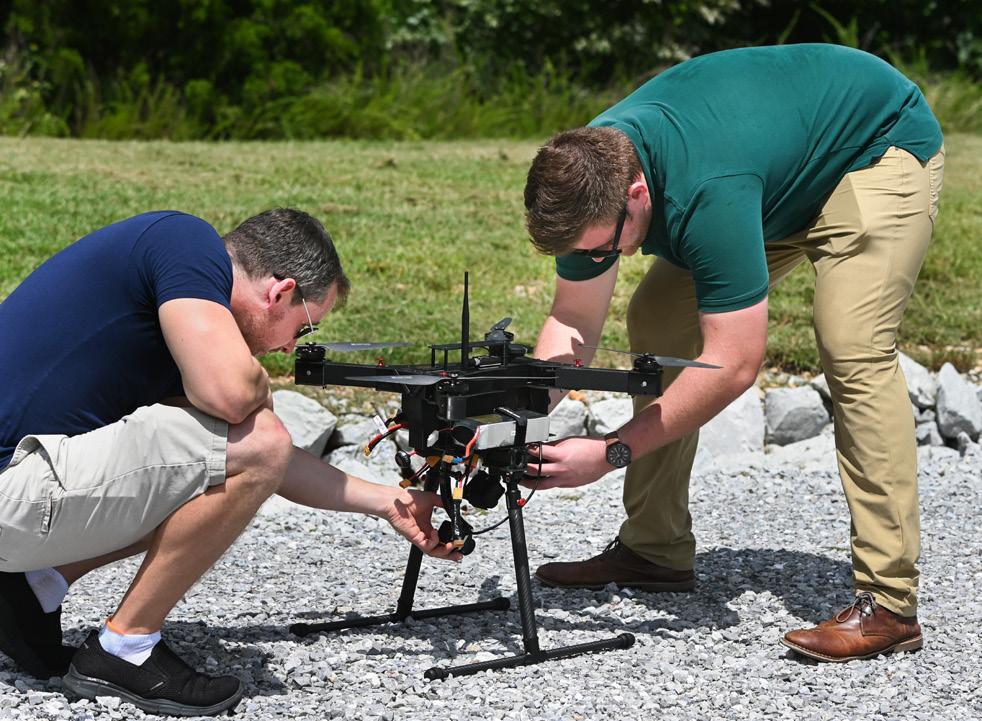
4 minute read
Engineering a solution for powerline maintenance
Associate Professor Zach Ruble (left) and student Corbin Cawood adjust the drone.
POWERLINE PERFORMANCE
By Shawn Ryan
The drone hovers about 50 feet up, buzzing like a fat batch of hornets.
Slowly it glides above powerlines and power poles, its cameras looking down, recording. All around it, powerlines weave in and out of metal structures that look like multi-legged robots from a Transformers movie.
On the ground at EPB’s six-acre Falling Water substation in Middle Valley, Zach Ruble holds a controller. The associate professor in electrical engineering at the University of Tennessee at Chattanooga is not flying the drone; it’s flying itself according to a pre-loaded program. Ruble’s making sure that if the program has a glitch, the drone doesn’t fry itself by flying into a powerline, smash itself into the ground or make some other life-ending maneuver.
It’s important that the drone fly on its own. Eventually, it will soar piece by piece over the 600 square miles of EPB’s coverage area, looking for wear and tear to insulators on top of poles, worn lines attached to those insulators, even rot in wooden poles holding everything.
“You can imagine a human going through 600 miles of powerlines to see whether there was any problem or not and how costly that could be and how effective that might be,” says Daniel Pack, dean of the UTC College of Engineering and Computer Science. “There are some areas where it is very difficult for humans to approach to check the health of those lines.”
IN AIR AND ON LAND
For about a year, six UTC students and Ruble have conducted a research project with the drones— also known as Unmanned Aerial Vehicles or UAVs. The research, done in collaboration with EPB, has taken place not only in the air but on the ground.
The airborne work gathers visual information that’s fed into computer servers on the ground. The computers digest the vast amount of data they receive and learn to recognize what they’re seeing, whether it’s insulators or lines or poles or even vegetation, roads and structures. Step by step—or more precisely, byte by byte—the computers understand what looks the way it should, so they can tell what looks the way it shouldn’t.
“The primary issue we are addressing is how to conduct field inspections more efficiently and more effectively,” says Jim Glass, manager of Smart Grid Development at EPB. “This is a challenge not only for EPB, but for electric utilities across the country. Efficiency improvements are always a goal of every organization.
“UTC’s research team is developing machine learning algorithms to process all this data and identify the potential issues. That means that we get twice the productivity improvement—one for the field inspection and one for the time to review images captured by the UAV.”
SEEMS LIKE SCI-FI
For non-computer-savvy folks, some of what the UTC students are doing may seem to border on science fiction. Science it is; fiction it’s not.
One piece of software—Normalized Difference Vegetation Index (NVDI)—uses infrared light to highlight power poles so they stand out clearly amid vegetation, a serious issue for EPB workers trying to find them while fighting their way through kudzu, briars and other thick greenery.
Once NVDI removes the vegetation, feature detection software pinpoints the exact location of the power pole.
“If you were to take just the images from the drone, there’s going to be a lot of noise in the image. There’s going to be trees; there’s going to be cars; there’s going to be all kinds of things,” says Kirklin Norman, a senior in electrical engineering. “This will help eliminate that, so it makes it a lot more clear for the drone to process that information.”
ESSENTIAL INFORMATION
After all data details are combined, the end result is so specific, it tells, among other things, the exact location of the pole, down to its latitude and longitude. GPS software can be used to find it.
The data tracks whether the pole is steel or wood. If there is a problem, it can determine what the problem is; for example, whether there’s a bad insulator or decaying wood in the pole.
“Many facilities are difficult to reach, which sometimes means difficult to complete all the typical visual inspection steps,” Glass says. “UAVs give us greater flexibility in viewing a piece of equipment and may identify issues that could be missed by traditional inspection methods.”
Traditional methods include a person climbing the power pole to physically inspect the insulators, powerlines and the pole itself. Drones not only increase efficiency, they can reduce the chance of injury for those workers, Ruble says.
Knowing the source of the problem will make it easier for EPB to make repairs, he says.
“It will do a lot of good to know what the problem is before you send out a team,” Ruble says. “If we can resolve that issue, they can know exactly who they need to send out and then whatever problem they have, they can fix much quicker than normal.”
Saving time can be crucial during emergency situations such as tornadoes or storms like Hurricane Ida, which devastated parts of the Gulf Coast while its remnants flooded New York, New Jersey and surrounding areas in September.
“Last year, when the tornadoes came through the Brainerd area, I drove through there. It was pretty torn up,” says Corbin Cawood, a master’s student in computer science and part of the project team.
“There were some roads and areas where power lines were running, and they were down and inaccessible. The earlier you can find these components that are missing or faulty and replace them, the better things are for people.”

— Jim Glass, manager of Smart Grid Development, EPB