
9 minute read
PROGRAM AREAS
ENVIRONMENTAL PROTECTION MANAGEMENT
The UTMB Environmental Protection Management Program (EPM) is governed by environmental laws, regulations, Environmental Protection and permits; facility operations; and technical services for hazardous materials and waste disposal. This includes integration of environmental compliance into business objectives to ensure the programs achieve ownership, Management Services collaboration, and support necessary for compliance.
300000 250000 200000 150000
100000 50000 0 Total Chemical Waste (lbs) Generated by UTMB Galveston Campus Total Chemical Waste (lbs) Generated by UTMB Campuses FY 2022
142365 191928 210878 206475 266726 Galveston Campus
Offsite Clinics
Angleton Danbury Campus
Clear Lake Campus
League City Campus
FY 2018 FY 2019 FY 2012 FY 2021 FY 2022 1172
2023
11414
20108 50
112 46 39
1671
Online Waste Pickup Requests FY22
1424 266726
0 50000 100000 150000 200000 250000 300000
UTMB Health League City Campus Clear Lake Campus Angleton Danbury Campus Offsite Clinics Galveston Campus
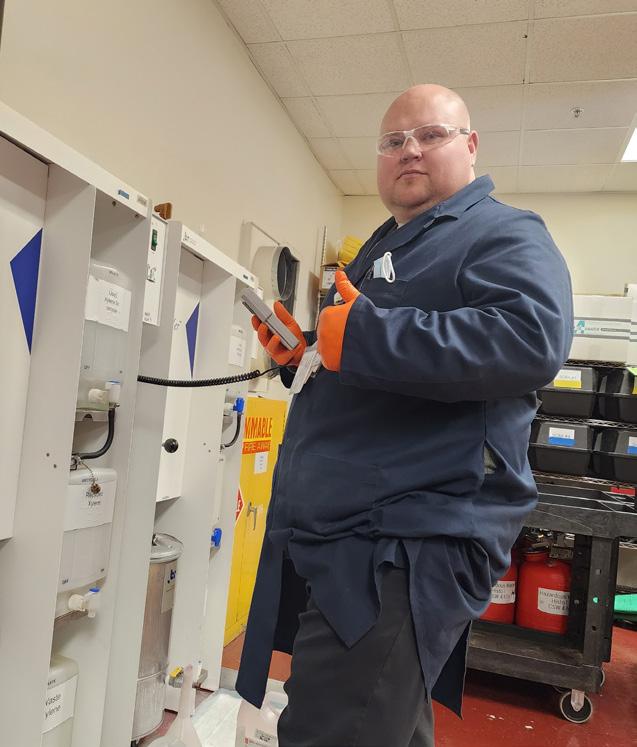
Jordan Sweet, EHS Specialist, working with the distillation system Sergio Garcia, Sr. EHS Specialist, and Meagan Thibodaux, Principal EHS Specialist, loading medical waste onto truck
Pollution Prevention
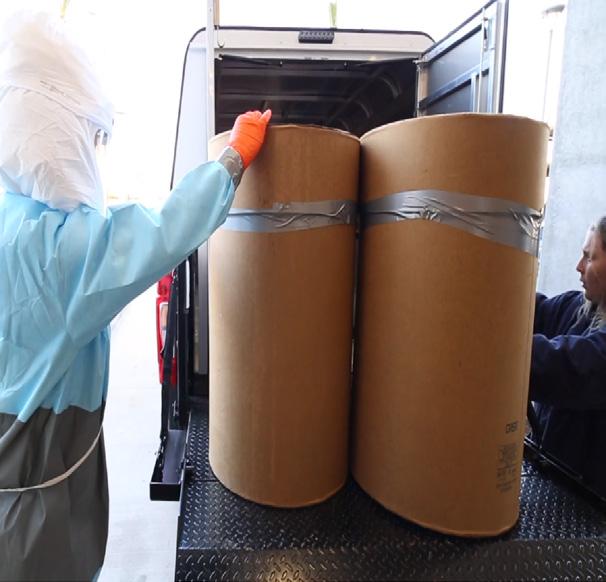
The UTMB Galveston campus is a large quantity generator of hazardous waste, generating over one hundred thousand pounds a year. Because of this generator status, the Texas Commission on Environmental Quality (TCEQ) requires UTMB Galveston to have projects and programs in place for Source Reduction and Waste Minimization, also known as Pollution Prevention. One project that not only reduces waste, but also reduces the amount of product purchased in clinical laboratories is solvent distillation. In FY22, the EPM program recycled over 1,631 liters of alcohol, and were able to produce 98% pure alcohol to provide back to Histopathology and Dermatology once alcohol for recycle is generated and distilled. On average, from scientific wholesalers, a liter can cost around $150 per container. This process saved disposal of 430 gallons of alcohol in FY22 and saved clinical labs approximately $244,650 in new product.
New Pharmaceutical Waste Regulations
This year, the TCEQ passed new regulations regarding the management of hazardous pharmaceutical waste. In conjunction with the new Generator Improvement Rules in 40 CFR 262, the new 40 CFR 266 Subpart P regulations focus on the management of pharmaceuticals in a healthcare facility, and more defined requirements for record keeping and reporting. These updated regulations allow holding hazardous pharmaceutical waste for up to one year, regardless of generator status and regular generator status accumulation time limits, as well as no longer having to count total weight of hazardous pharmaceuticals toward the TCEQ Annual Waste Summary. A major change in the regulations focuses on empty containers. In standard hazardous pharmaceutical regulations, any waste container that contained EPA listed waste was still considered hazardous and managed as such. In the new Subpart P regulations, dispensing pharmaceutical containers - blister packs, stock bottles, etc. – are no longer managed as hazardous waste. A major process change took place at the Correctional Managed Care (CMC) Pharmacy in Huntsville. Prior to these new regulations, all empty containers of listed waste were managed as hazardous waste, primarily empty Warfarin bottles and blister packs. These new regulations will greatly reduce the volume of hazardous waste being shipped from the CMC Pharmacy due to stock containers and will focus primarily on the management of true RCRA Hazardous Waste Pharmaceuticals. All UTMB campuses and clinics may operate under these Subpart P regulations regarding pharmaceutical waste. All remaining hazardous waste must be managed according to generator status and the new Generator Improvement Rules that were adopted by the TCEQ in February of 2022.
CMC pill distribution window
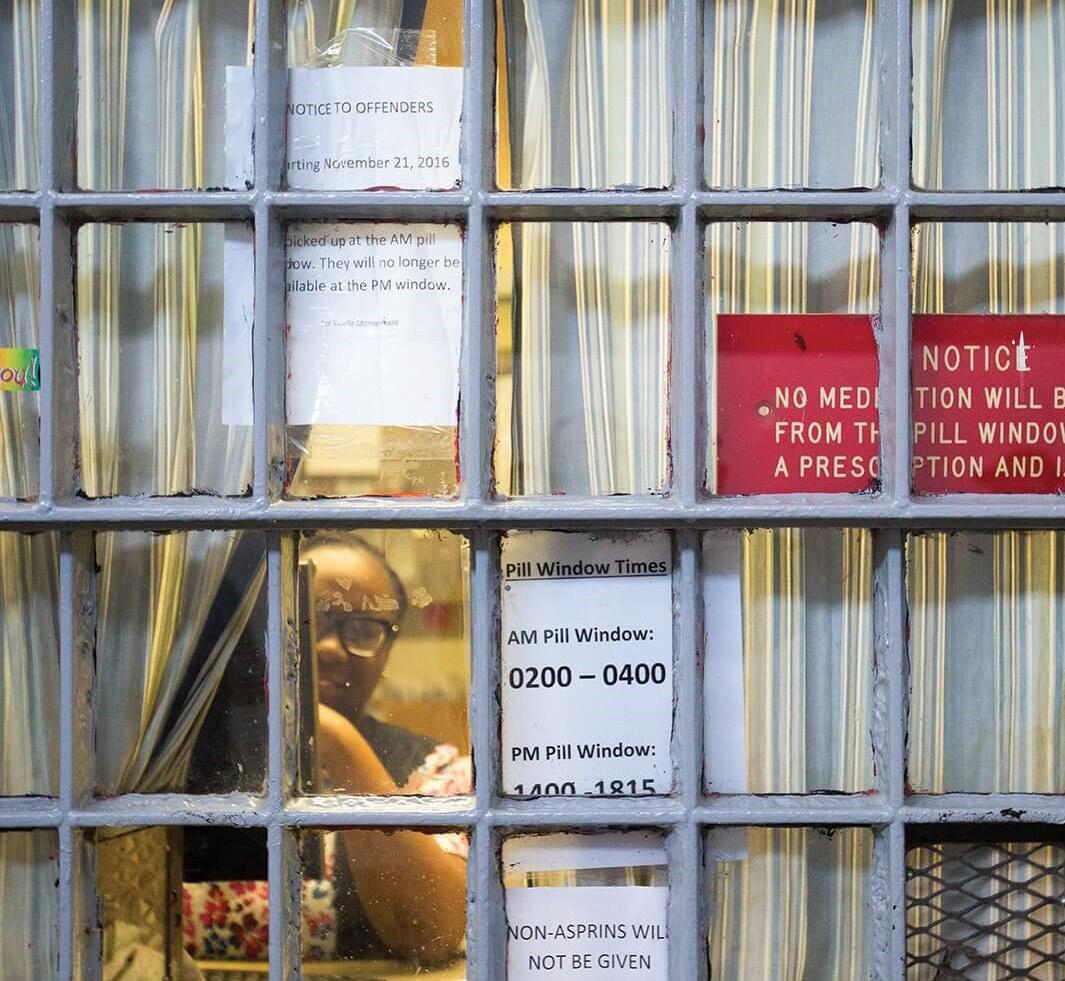
Improving Laboratory Cleanout Procedures
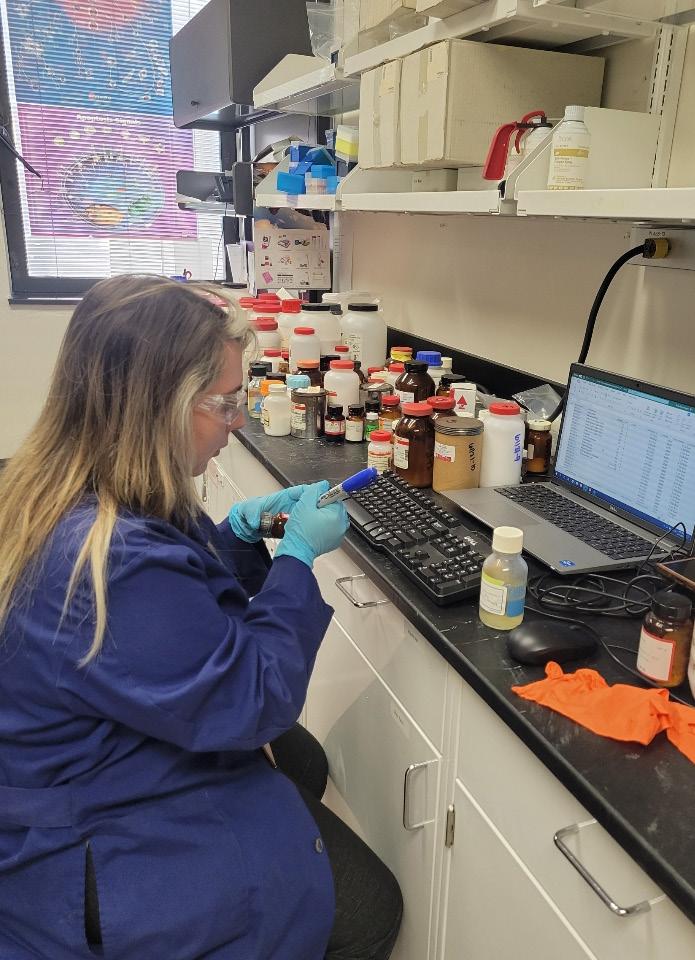
Meagan Thibodaux, Principal EHS Specialist, checking chemical labels during a lab cleanout In FY22, the EPM program goal was to create a more robust tracking and segregation process for laboratory clean outs by improving the laboratory clean out procedures. Laboratory clean outs are considered chemical pickups with greater than fifty chemicals from a single laboratory at one time, including laboratory moves and close outs. The overall goal was to ensure that all EPM personnel were trained to properly identify and process chemicals at the point of generation, confirm the lab cleanouts are processed appropriately, and performed in an efficient manner. The measured outcomes to complete the goal were as follows: • Create a living highly hazardous list for reference for unapproved and approved pickups in the EPM Hazardous Waste Database. • Update the data in the EPM Hazardous Waste Database to better track the lab cleanout process. • Monitor and determine legacy laboratories (chemical inventory) – formally communicate Lab Cleanout Procedures to the Chemical Safety
Committee in collaboration with Occupational Safety and Radiation Safety programs to improve monitoring and identification of legacy laboratories. • Train EPM staff on in-lab chemical processing to better identify hazardous waste, hazardous and non-hazardous solid waste codes, segregate by waste stream, inventory, and list chemicals into the EPM Hazardous
Waste Database. During the fiscal year, 39 full laboratory clean outs and closures were performed by the EPM personnel, and accounted for over 215 hours of staff time.
PROGRAM AREAS
FIRE & LIFE SAFETY PROGRAM
The Fire and Life Safety Program (L&FS) has a systemwide mission to provide employees, patients, and visitors with a safe physical environment. To do so, we are actively involved in the built environment from design of facilities, their construction, activation, maintenance and even final decommissioning. We identify potential problems, champion effective solutions and track them to resolution. During the useful life of our facilities, we conduct routine inspections and testing of Life Safety features to ensure code compliance and that they will function properly in times of an emergency. The L&FS group also serves as the liaison to local fire officials, the Joint Commission Life Safety surveyor, and is responsible for fire emergency planning. We help develop departmental plans as well as building-wide and institutional responses to emergencies.
Accomplishments
• Fire sprinkled Levin Hall Auditorium in less than 2 months • Replaced entire fire alarm in the Clear Lake Campus
Hospital • Replaced half of the fire sprinkler system in Trauma garage • Fire Sprinklered >90% of Moody Medical Library • Replaced all aging sprinkler heads in ADC hospital and modified for efficient service • Interconnected Life Safety network with: ◦ Infant abduction system ◦ Active shooter system ◦ Fire alarm/all-clear Everbridge notification • Upgraded voice notifications in Pharmacology, Child
Care building, and Keiller buildings • Continued support of JSH modernization project • Updated 150 departmental fire safety programs • Texas State Fire Marshal audit of TDCJ, Hospital
Galveston
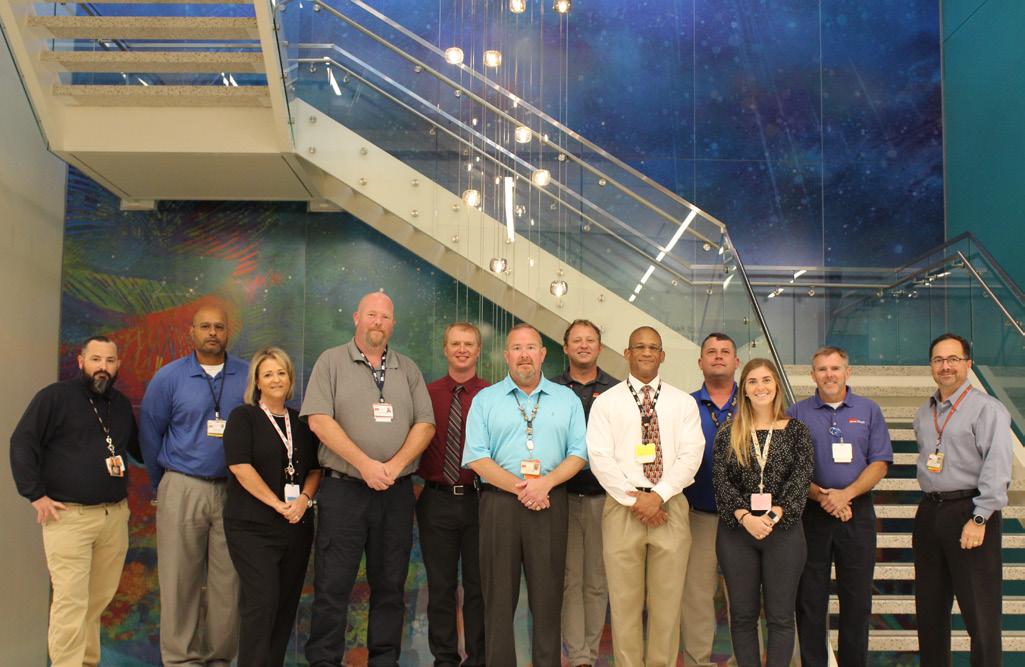
Life & Fire Safety Team
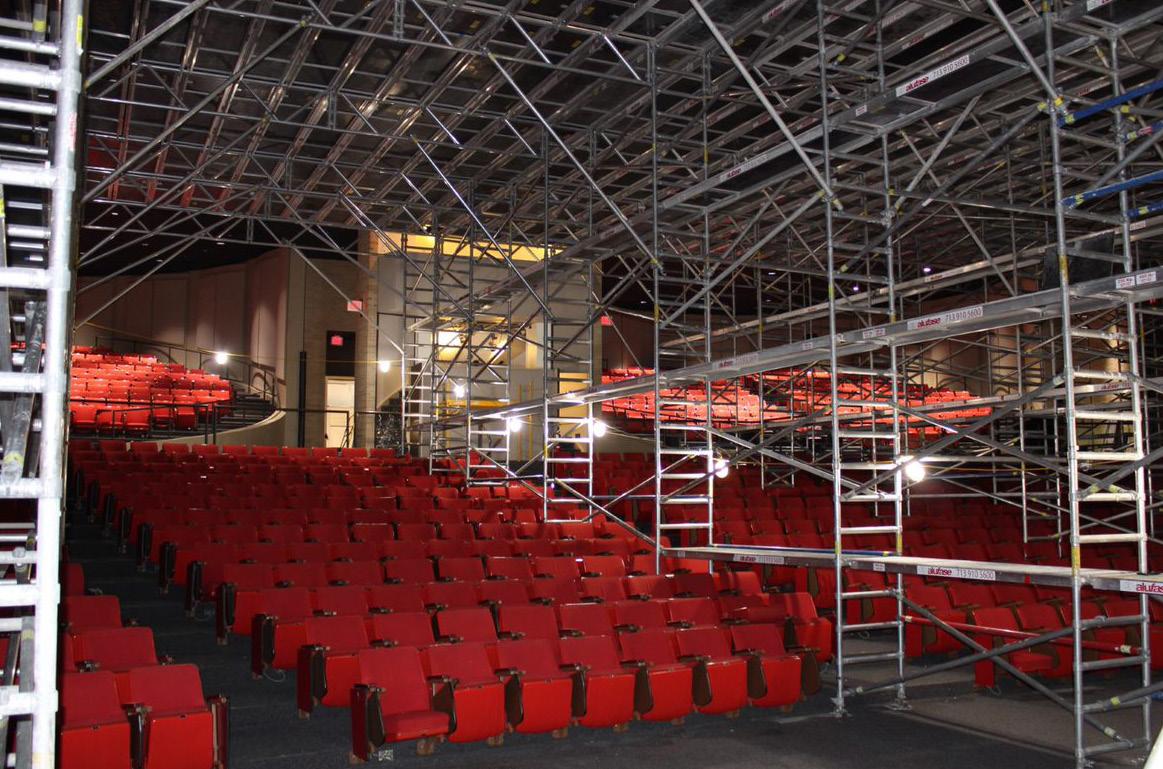
Levin Hall Auditorium sprinklering progress
• Completed Joint Commission survey • CDC audit of fire systems for GNL/Keiller/BCU • Hands-on OR fire safety drills • On-boarded new life safety vendors • Updated fire doors in Jennie Sealy and CSW to reset automatically after fire alarms • Updated mass notification systems to allow outdoor announcements and all-clear announcements • 772 ATG findings, with 730 closed (95% correction rate) • Implemented a risk-based EOC tour process • Inspecting all above-ceiling firewalls in healthcare for deficiencies. Identified 1,000 items and corrected 75%, resulting in a more successful TJC audit • Created and implemented bi-lingual fire safety training for kitchen staff
Future
• Add fire sprinkler system to School of Allied Health Sciences • Complete Life Safety upgrades for Moody Medical Library • Initiate new fire door safety program and execution of new electronic system for tracking • Hardening and ensuring continuity of campus fire alarm and mass notification/life safety network • Streamlining of above-ceiling work process
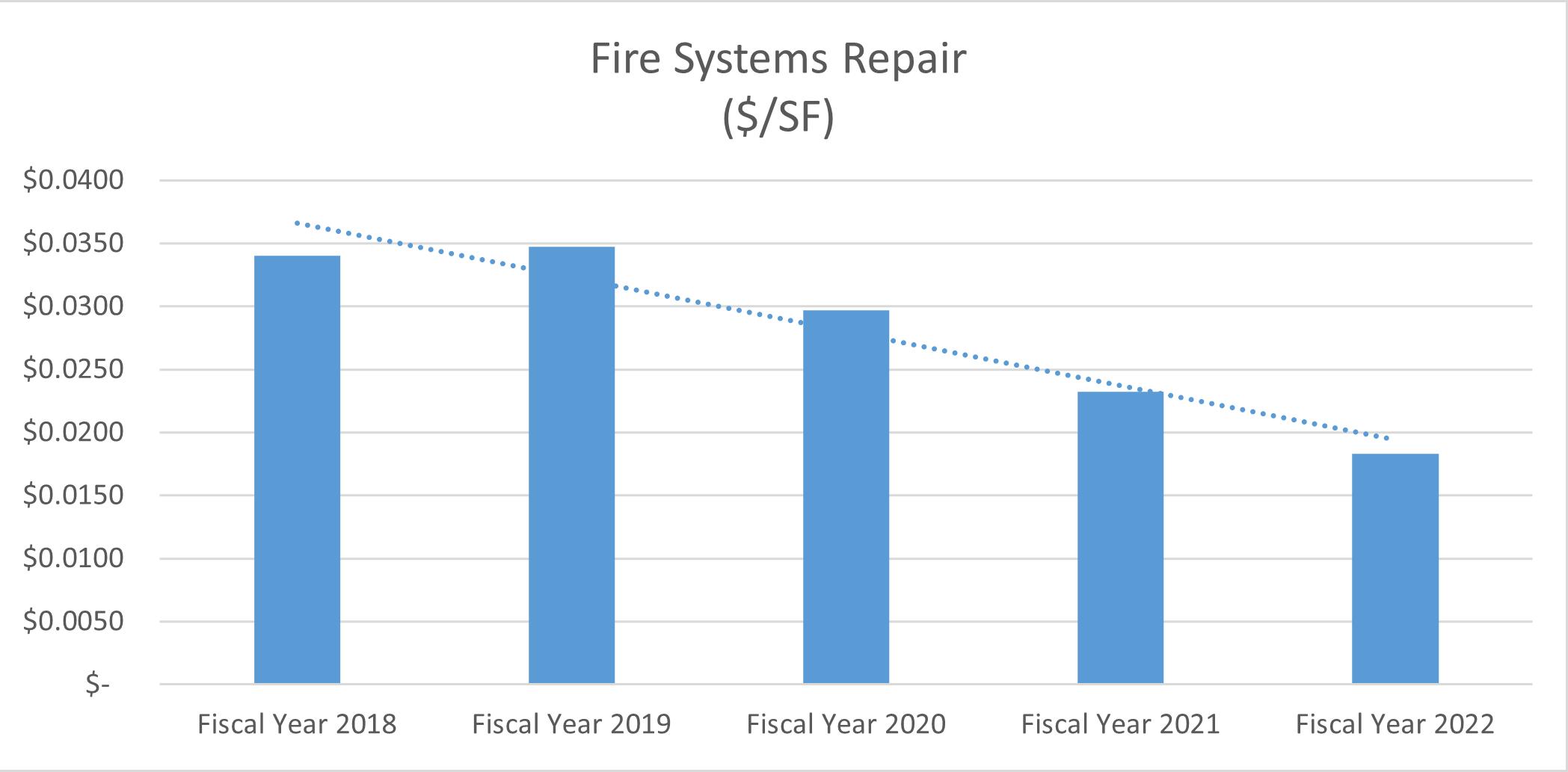
As a part of our ongoing efforts to be good stewards of UTMB resources, EHS constantly strives to reduce costs through competitive bidding of services, close attention to work service, efficiency, and effective maintenance strategies. This has allowed us to do things like reduce the rate of repair costs while the institution has grown.

As part of the Fire and Life Safety mission, we provide employees, students, patients, and visitors with a safe physical environment to conduct business, study, deliver, and receive care. Our staff efficiently tests and inspects Life Safety features to ensure code compliance and that the Life Safety features function properly during an emergency.
PROGRAM AREAS
RADIATION & OCCUPATIONAL SAFETY
The Radiation & Occupational Safety Program (ROccS) works to ensure the safety of laboratory and health care workers. Our technical expertise covers a wide range of areas including radiation safety, laboratory safety, food & potable water safety, and industrial & construction safety. Services offered include sealed source leak tests, receipt & surveying research radioactive material packages, laboratory safety audits, calibration of survey equipment, food safety inspections and permitting, respirator fit tests, and providing training on a wide range of safety topics.
Accomplishments
• In response to the COVID-19 pandemic, performed 10,229 respirator fit tests • Implementation of EHS Assistant to track personnel radiation doses and document ALARA investigations • Successful planning and performance of a fullscale diesel spill for the EHS On-Call Team,
Texas Department of State Health Services x-ray inspection for the Webster Urgent Care Clinic, as well as mammography inspections for the
Galveston Campus, Angleton Danbury Campus, and
Clear Lake Campus without violations • Successful communication and support of projects
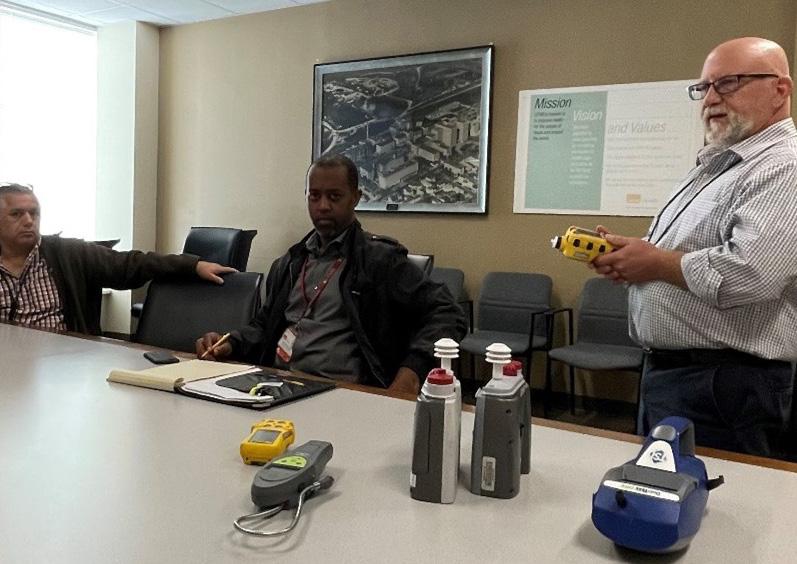
Jim Stone, Principal EHS Specialist, providing training to ROccS staff on the use of air monitoring equipment
to import research laboratory hazards chemical inventories into EHS Assistant resulted in more than 95% of research labs coming into compliance with the requirement • Presented at the College and University Hazardous Materials Conference on “Managing a Respiratory
Protection Program during a Global Pandemic”
Future
• Continue to support ongoing and expanded fit testing needs for health care and research staff at all campuses • Updates to Texas regulations lasers and therapy accelerators which may create impacts to operations • Laboratory safety audit program focus on time-sensitive chemicals and providing resources to researchers to assist them with effective management of risks • Anticipated x-ray and radioactive material inspection of Galveston Campus expected in FY23, requiring staff resources to support
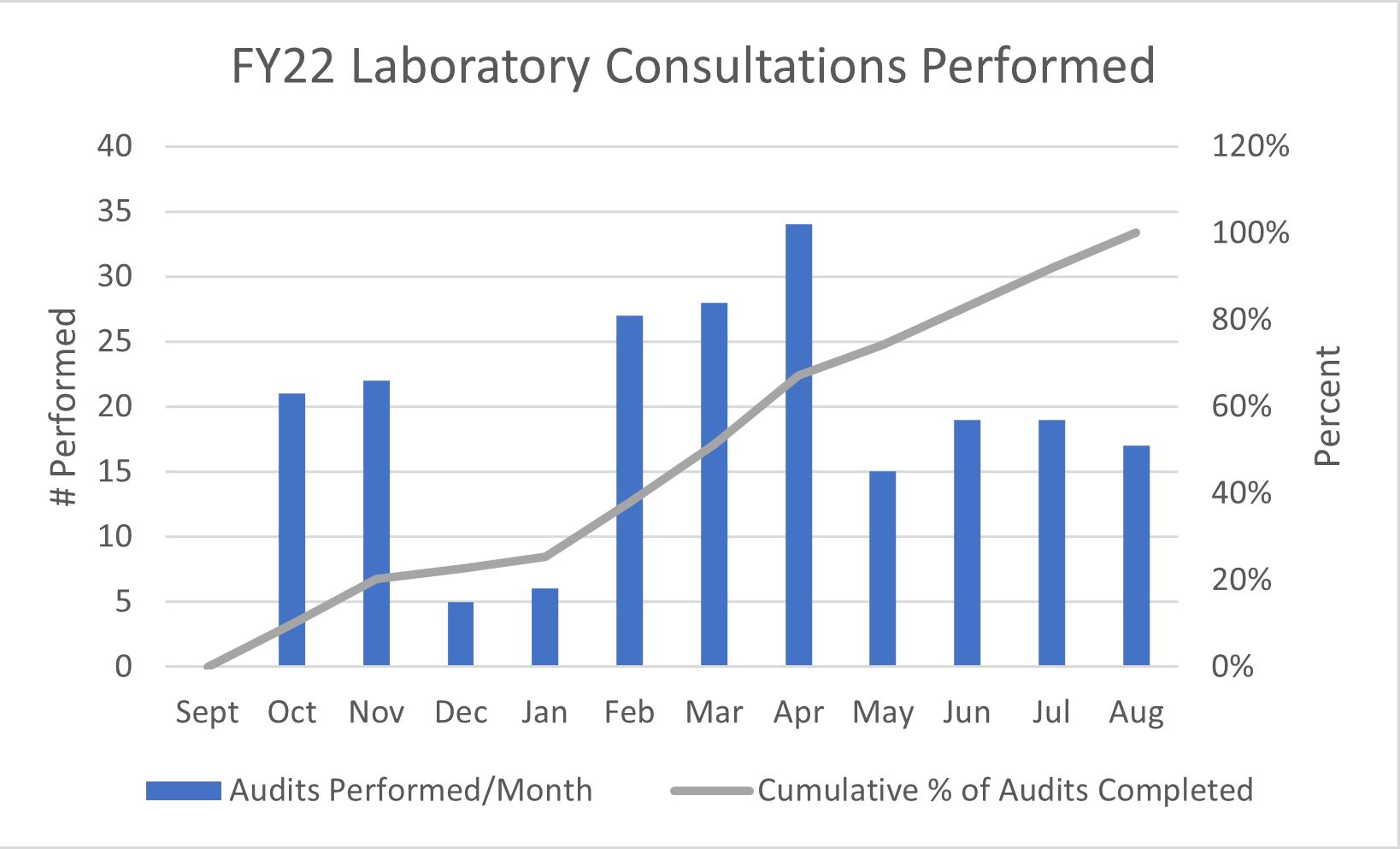

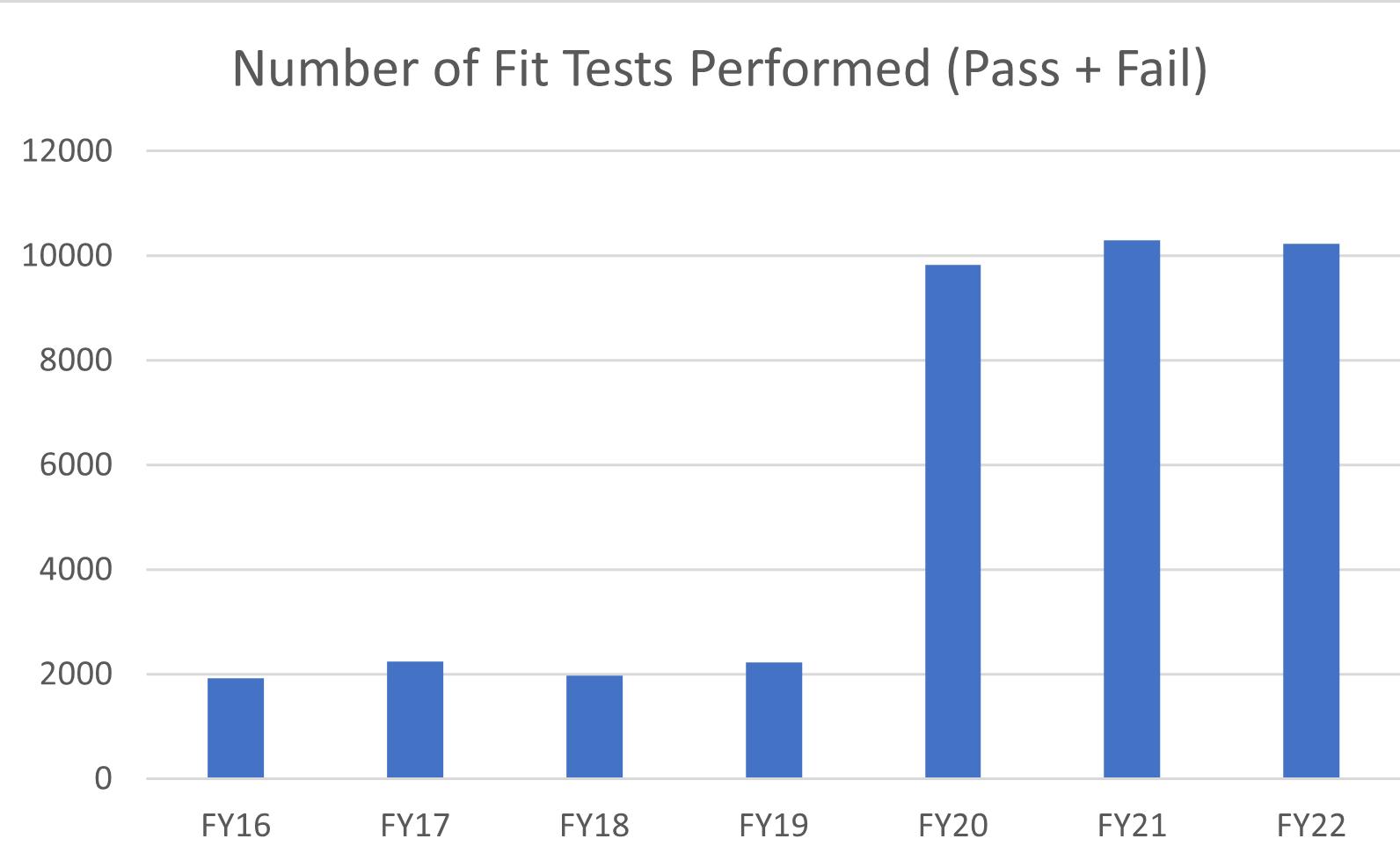
Laboratory Safety Consultations are an important service to ensure the safety of research operations. On an annual basis, each research laboratory is inspected by team members of the Radiation & Occupational Safety Program to ensure all expected safety precautions are being used. These efforts directly contribute to the safe and compliant conduct of research at UTMB.
Despite reductions in research use of radioactive material, the use of ionizing and non-ionizing radiation in health care continues to increase. The number of x-ray machines and dosimetry program participants has steadily increased over the years, primarily the result of UTMB health care expansion. Regulatory inspections remain steady, indicating continued need for EHS resources to support institutional compliance.
Fit testing performed by EHS continues to be in high demand due to the continuation of the COVID-19 pandemic. Fit testing performed in FY22 nearly reached the amount seen in FY21. Earlier appointment times and adding additional days for fit testing at each regional hospital campus help support health care worker fit testing needs.