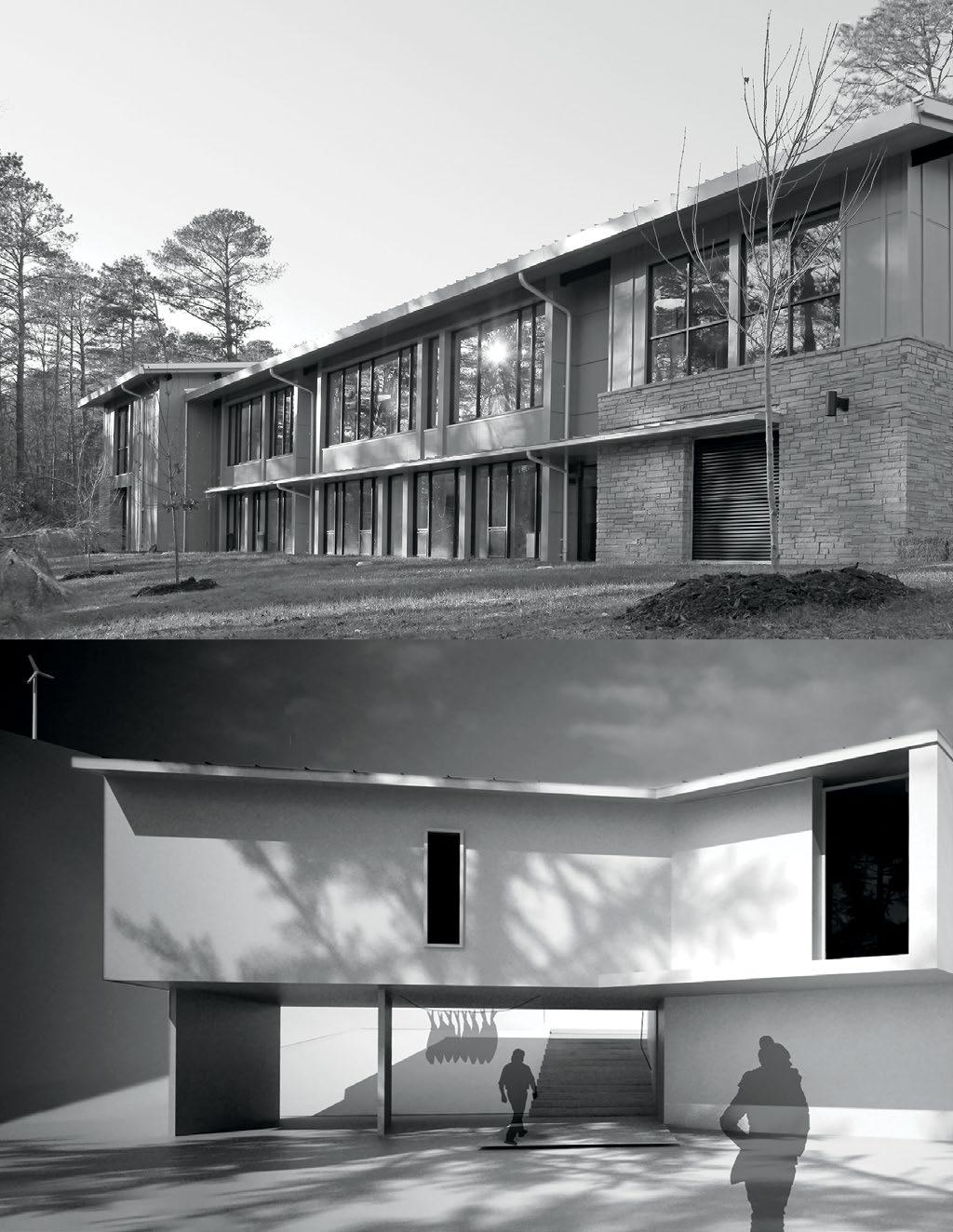
9 minute read
Francisco Gomes
measuring sustainability
FRANcisco
Advertisement
gomes
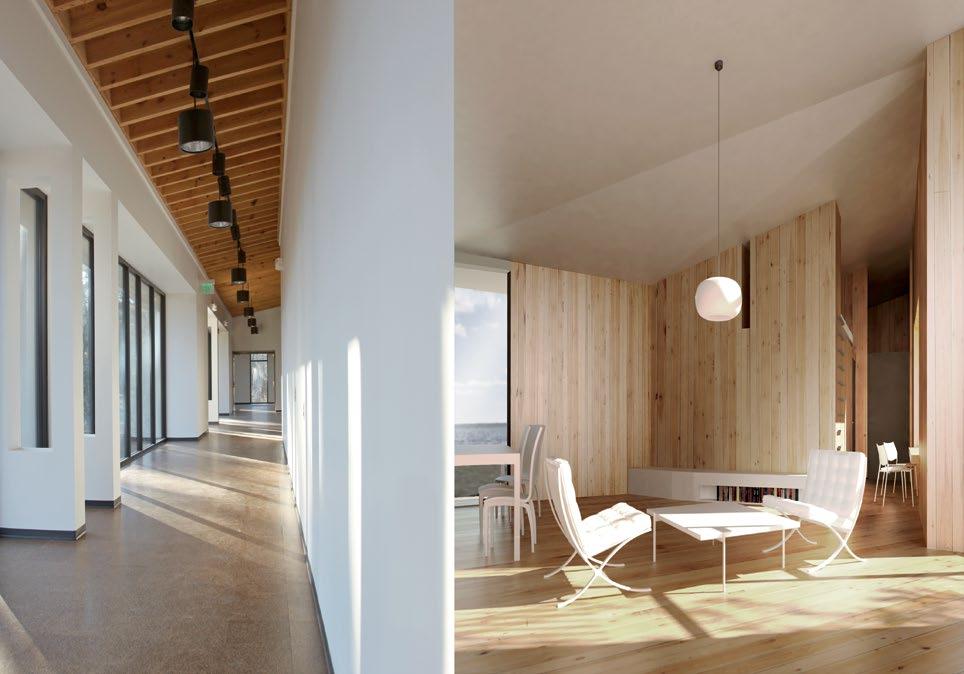
FIG 1 Interiors ©2021, Gomes + Staub PLLC.
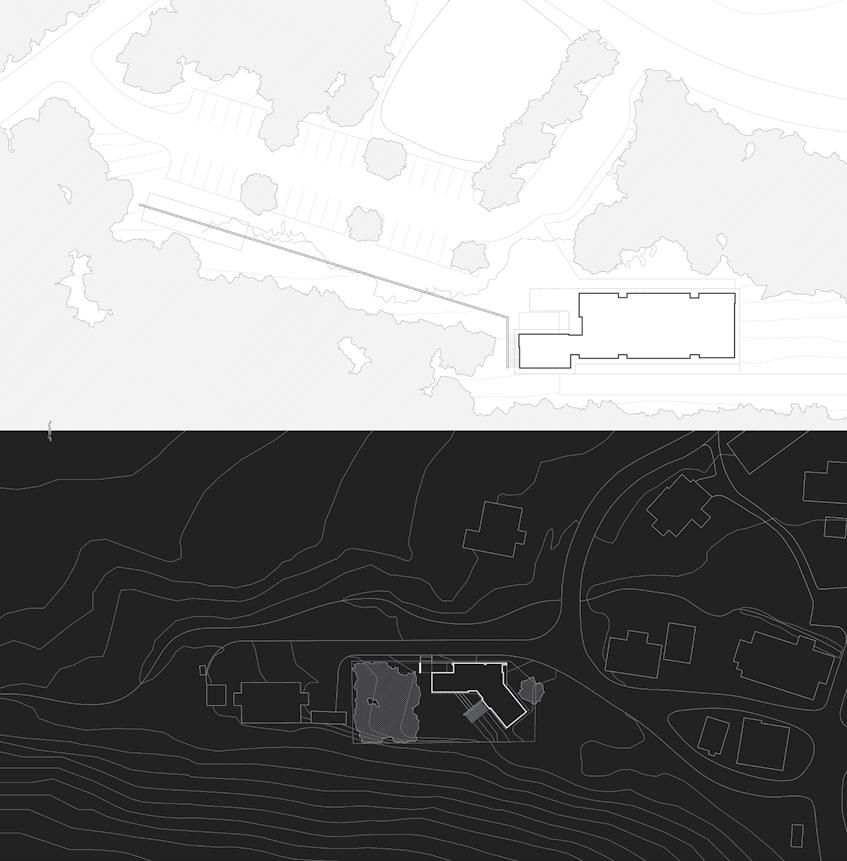
FIG 2 Site Plans ©2021, Gomes + Staub PLLC.
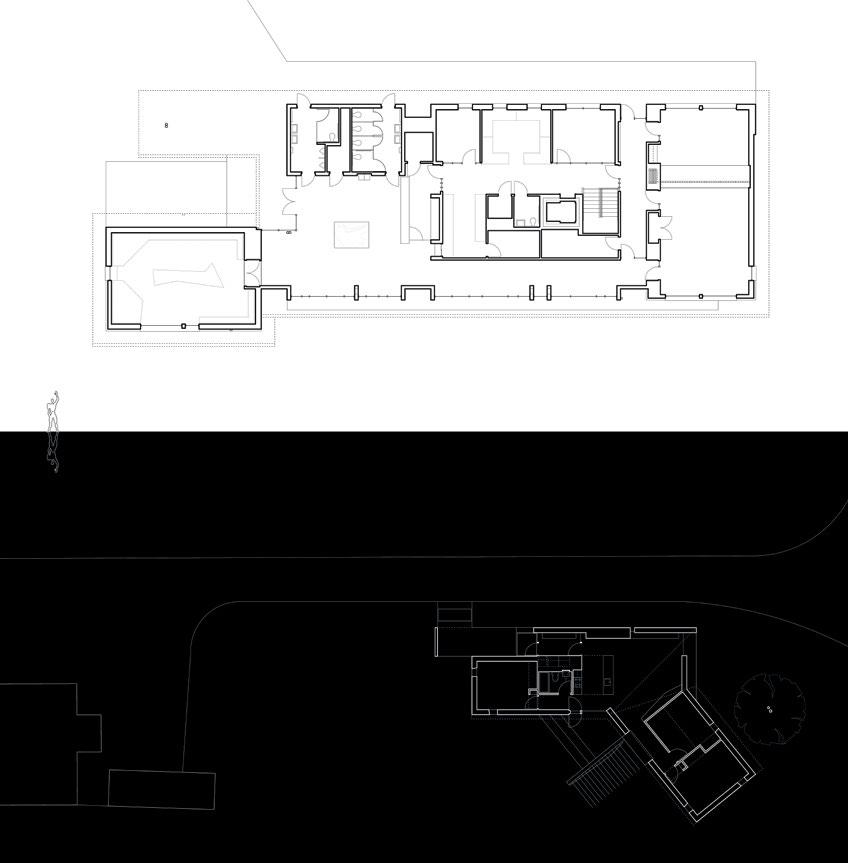
FIG 3 Main Level Plans ©2021, Gomes + Staub PLLC.

FIG 4 Lower Level Plans ©2021, Gomes + Staub PLLC.

FIG 5 Transverse Sections ©2021, Gomes + Staub PLLC.
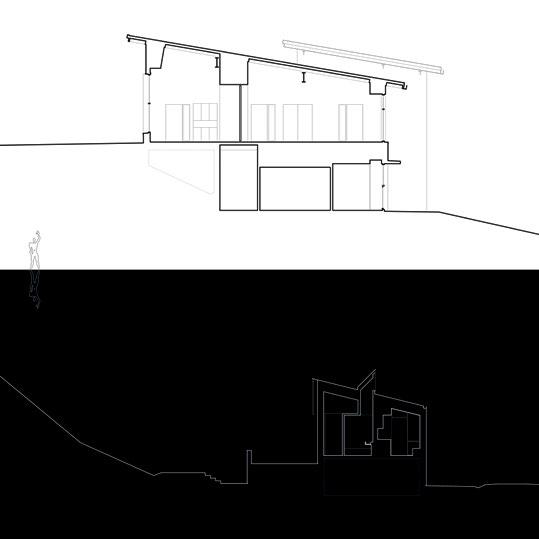
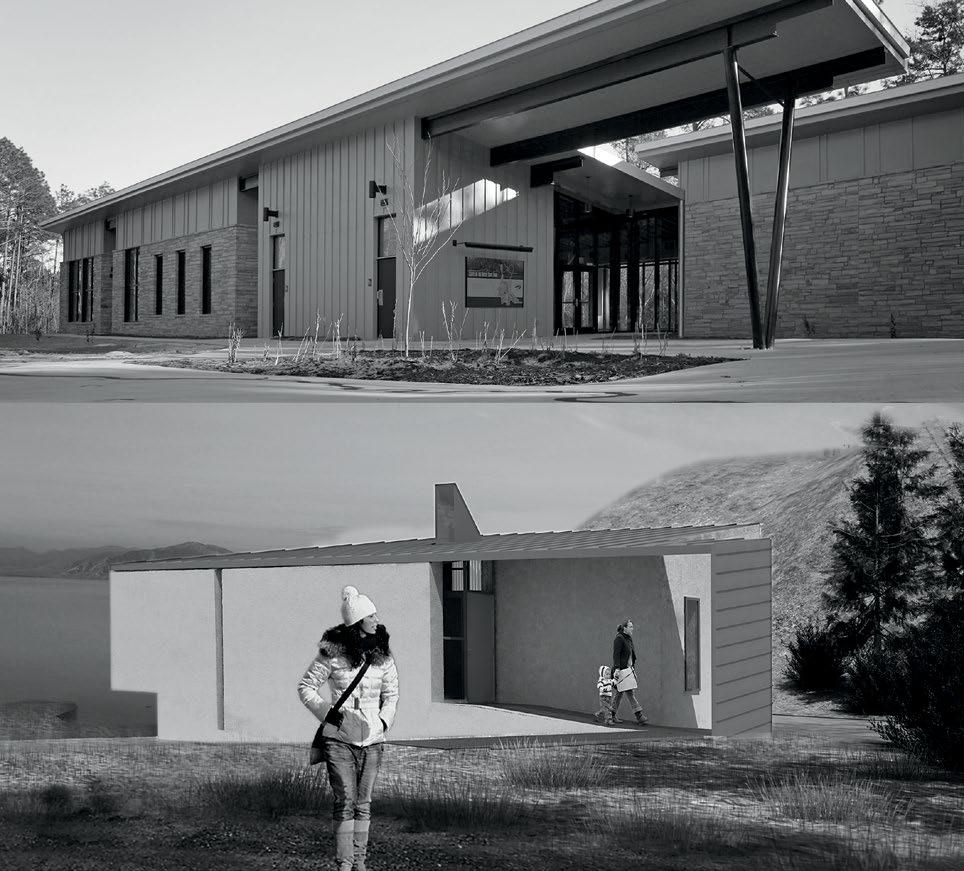
FIG 7 Entries ©2021, Gomes + Staub PLLC.
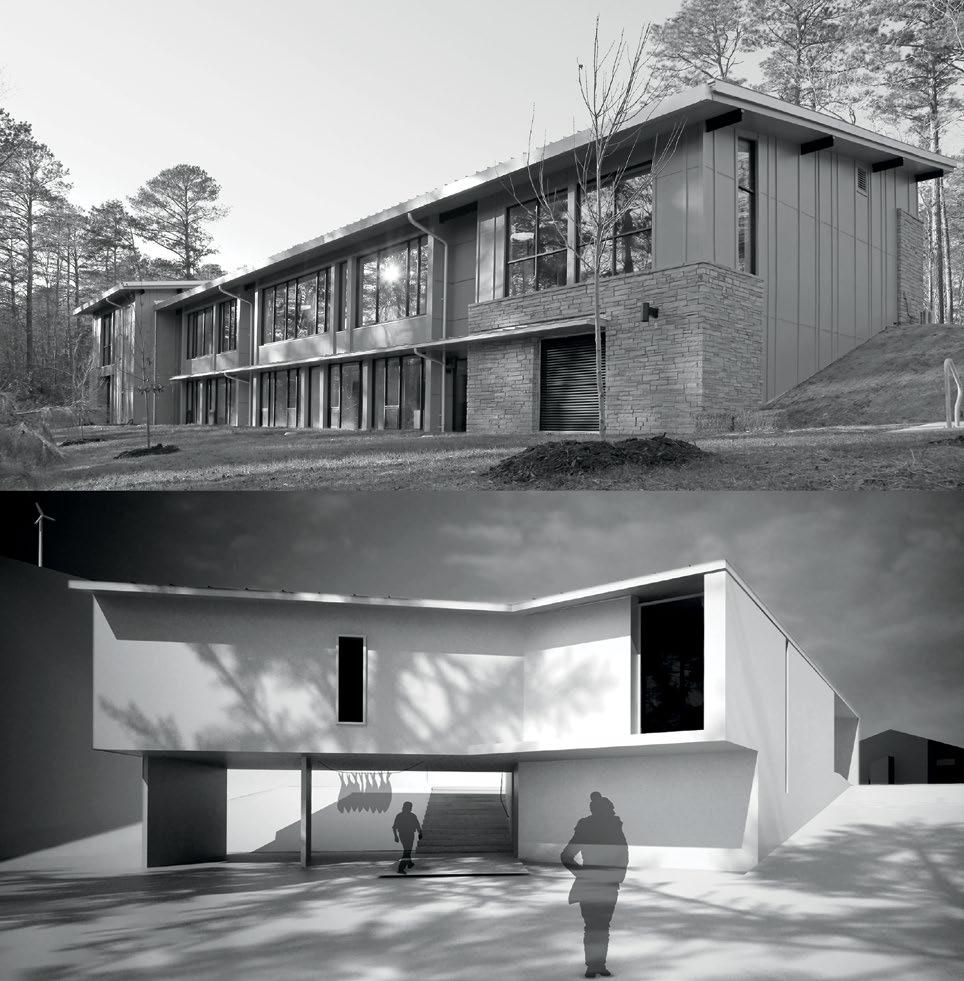
INTRODUCTION
The temptation to greenwash our buildings is irresistible, for no rational person denies the broad environmental and societal challenges created by the ever-accelerating material activity of humankind. However, our continually evolving priorities in the making of sustainable architecture also enable this misdirection. Change creates uncertainty, which in turn undermines confidence in our decisions. How should we best measure the impacts of our projects?
Two architectural projects by Gomes + Staub, both designed for public clients and both engaging sustainability certification regimes, are presented here in paired images: 1 one built project, a 10,100 square-foot LEED-Gold certified state park visitor center,2 and an unbuilt small house for an existing community on the Aleutian Islands, which was authored for a competition mounted by the Atka Housing Authority in accordance with the Living Building Challenge guidelines.3
The standards themselves are well documented and publicized, so no comprehensive characterizations of the two certification systems will be attempted.4 While the focus of this essay is the impacts of these systems on design decision-making, their worth as a tool for distilling best practices and their social role in publicly signaling commitments to sustainable practices—of clients, governments, and design professionals—is also valuable.
There is a tremendous amount of thought and care invested in the necessarily imperfect certification systems available, and this essay reflects on their impact on design decision making. Through the lens of these projects, two types of observations follow: doubts about the wisdom of particular decisions influenced by pursuit of the standard, and, perhaps more importantly, thoughts on where the collective gaps may currently exist in certification regimes.
QUESTIONABLE DECISIONS
GLAZING AND COMPENSATORY TRADEOFFS: Minimizing exterior glazing is perhaps the lowest-hanging fruit of the low-energy equation, especially in warm climates. LEED-NC and the Living Building Challenge each have different requirements for broad access to exterior light and view from interior spaces, which are readily achievable with relatively low quantities of glass. The Atka house, for example, meets the Living Building Challenge guidelines with a glass-to-exterior-wall ratio of only 10.0%. The park visitor center is not so innocent. During design, comprehensive operating energy simulations of the planned structure were created, glazing and overhangs were tailored to their exposures, and the building is considerably more operationally efficient than the base LEED standard under which it was certified. But, some of these efficiencies come via the mechanical conditioning technologies and many LEED points were achieved in the myriad of other categories unrelated to energy. This project was the first LEED-certified project designed by our practice, but has a greater glazing ratio, at 31.8%, than the three prior nonrated and non-energy-modeled commercial projects we completed (averaging 16.9% glazing, including a medical clinic at 12.8%, a rail passenger station at 23.7%, and a multi-tenant office building at 14.3%). Meeting the LEED-Gold certification standards is an endorsement of environmental virtue, but in this case, the energy modeling and innovative low-energy mechanical systems also fostered slippage of established best practices in the office. We ought to use less glazing in our buildings.
ACTIVE ENERGY TECHNOLOGIES AND THEIR PITFALLS: Innovative, active energy technologies tend to be complex and often have unanticipated effects. The park visitor center has an HVAC system that efficiently exchanged heat with the outside environment through a water-source exchanger: a bank of piping coils submerged in a man-made recreational lake within the park. Because the circulating water used in this loop would enter the park ecosystem if the piping ever leaked, using anticorrosives typically employed in the circulating heat-exchange fluid to protect iron piping was not possible, and instead large amounts of plastic piping had to be substituted. Additionally, the control systems and maintenance regimes required for the more complex system were challenging for the park-maintenance personnel operating the building. When viewed comprehensively, achieving the same low-energy consumption for a project with passive rather than active measures is always the better solution.
To meet the Living Building Challenge standard of producing more energy than is consumed, some active equipment is necessary. In the case of our design, this included a wind turbine for electrical power and an array of evacuated solar-thermal tubes linked to an insulated sand-bed thermal mass for heating. For the competition, the control systems were not determined, but one wonders if their inherent complexities and operational challenges might have diminished their expected performance and lifespan.
CROSS-LAMINATED TIMBER AND EXCESS MATERIAL USE: While both projects use Type V construction, the material agendas of the Living Building Challenge prompted us to pursue atypical choices for the Atka house. The cross-laminated timber structure—insulated on the exterior with a lime-washed, rigid, mineral-wool insulation and waterproofed below grade with bentonite clay—was an effort to make a house with minimal cement and plastic content. The effort to remove entire categories of material, however, led to nonsensical use of disproportionate quantities of lumber. We estimate the same house made with dimensional lumber platform framing would use 74% less wood. It is hard to imagine a situation where a building that is permittable as Type V construction (which includes the vast majority of both residential and commercial building projects) could be made with less embodied energy in another construction type than advanced platform framing with solid-sawn dimensional lumber. Wood also has significant disadvantages as a building material— combustibility, susceptibility to mold and rot, insect infestation—none of which are ameliorated by quadrupling the amount of the material in a structure.
NEGLECTED CONCERNS
Many certification systems share an aspiration for comprehensiveness. The point categories of LEED-NC and “petals” of the Living Building Challenge recognize the different dimensions of impact. Just as existing standards continue to evolve over time in response to changing understandings of what defines sustainability, new systems have been developed to address oversights, both perceived and actual, of existing regimes.5 The growing awareness of embodied carbon in construction is an example of an area experiencing significant change in recent years. It seems inevitable that these
will soon be adopted by the various regimes we have for measuring impact. What other important issues are not yet on the radar of our sustainability programs?
THE ENVIRONMENTAL COST OF CONSTRUCTION LABOR: If you were asked to create a mason or framing carpenter from scratch, how much carbon would be emitted by that activity? The sixteen years of food, clothing, housing, and education needed to satisfy the US Fair Labor Standards Act just scratches the surface. Labor dominates the financial and scheduling metrics of construction, and though one suspects it holds an equally large role in the consumption of other resources, it is a factor that is conspicuously missing in existing environmental quantifications of construction.
Perversely, this situation mirrors how we account for the use of waste products of industry, such as fly ash or steel slag. Never mind that providing an end-use for these byproducts of energy-intensive processes economically incentivizes their production; the assumption is that because these are waste outputs from other societal activities, we can use them at scale without accountability for their impact. Why would we account for humans and livelihoods in the same way we account for industrial waste?
APPROPRIATE DURABILITY: The varied resources expended in the construction and operation of buildings are the core of many efforts to measure sustainable design and construction, but they are only half of the equation. As was recognized in the early days of the contemporary environmental movement in architecture, project lifespan is the divisor for these carefully tracked expenditures.6
That durability is underattended is not surprising. While scientific constructs for understanding durability exist, we don’t have particularly reliable tools for predicting the lifespan of our building projects. However, if one presumes a minimum thirty-year service life, the projects we are designing and building now will certainly outlast the projected peak of the US population, and will likely see the peak of the worldwide population.7 We may not need nearly as many buildings in the future.
How should we think about durability? We need to make the effort to set explicit intentions about the durability of our buildings and follow up with material-, constructive-, and spatial-planning decisions aligned with these intentions. Shigeru Ban’s work is a good example to follow: buildings intended to be temporary or to have relatively short lifespans are appropriately made with textiles, lumber, or even cardboard tubes. For most buildings, though, long life is an explicit goal and seeking durability with mineral-based materials able to withstand a leak or two without disproportionate damage is a rational approach. Certification systems would gain relevance by incorporating this important aspect of sustainability.
CONCLUSION
The inevitable friction between project intentions and the criteria of any evaluation system—be it a sustainability certification regime, a set of development ordinances, or even a design award program—provides insight into the current state of knowledge and underlying values of our culture. These multiple lenses of evaluation are valuable because they push design teams to step outside familiar decision-making routines. Engaging all of these imperfect systems, including sustainability certifications, matters. Our world is better for our differences, and specialized experience will always exist in the design professions, but more empathy for the full spectrum of evaluation perspectives benefits our built environment.
6 A. Gordon, “Designing for survival: the President introduces his long life/loose fit/low Royal Institute of British Architects Journal , 1972, 79(9): 374-376. energy study,”
3 Atka House credits: Architecture: Francisco Gomes, Dabney Staub, Arman Hadilou While there are many pressing societal challenges—the climate crisis, inequitable 7 socio-economic opportunity, thresholds in computation—the impending end of global population growth is underattended. For many first-world economies it has already arrived and the implications of population decline are especially profound for economic systems dominated by the exchange of services rather than goods.
4 https://www.usgbc.org/leed, https://living-future.org/lbc/ 5 For example, the attention to material toxicities beyond carbon emissions in the Living Building Challenge, the requirement for documenting actual post-occupancy operating energy use in the Passive Building and Living Building Challenge standards, and the education and evaluation of social equity in the SEED program or the Design for Freedom framework of Grace Farms.
The author thanks Thom Palmer for his assistance in preparing the project images. 1 Cliffs of the Neuse State Park Visitor Center and East District Offices credits: 2 Architecture: Francisco Gomes, Dabney Staub, Dave Hardin, Mayowa Alabi, Sarah Dickerson Structural Engineering: Lysaght & Associates PME Engineering: The Wooten Company Landscape Architecture and Civil Engineering: CLH Design Exhibit Design: Design Dimension Cost Estimator: Capital Building Consultants General Contractor: Blue Ridge Enterprises LEED Manager: Francisco Gomes (design phase), Mayowa Alabi/Schema LLC (construction phase)