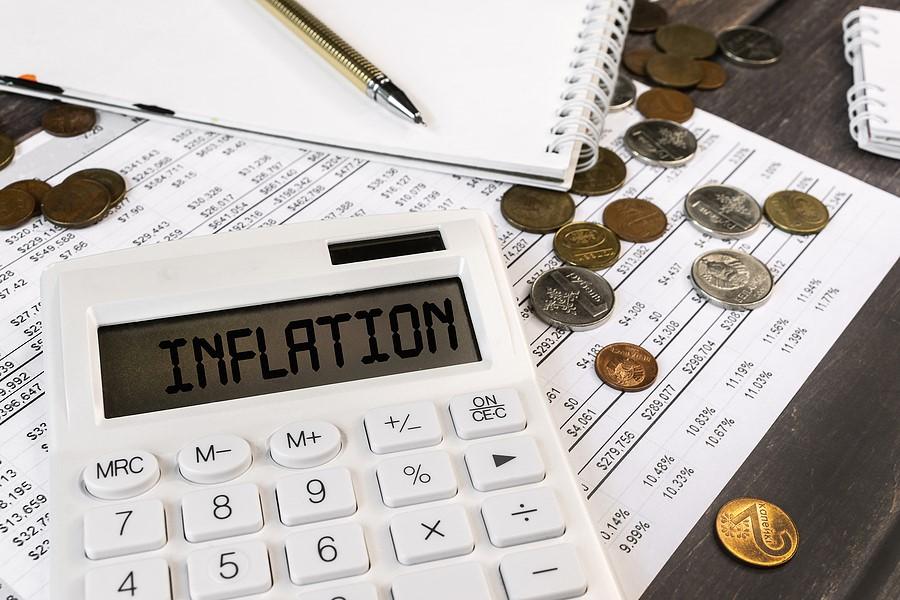
3 minute read
PERSPECTIVE
Perfect Storm: COVID-19 Pandemic and Rampant Inflation
Robert T. Yokl, President/CEO, SVAH Solutions
We went through almost two years of supply and labor shortages (not that these challenges are entirely solved) during the pandemic and now we are dealing with rampant inflation that is taking the wind out of our sales. Yet, what seems to have taken a back seat during these trying times is that “cost is our enemy and we must always be on the attack.” Before the pandemic, supply expense cost management was one of our primary missions in supply chain/value analysis, but now it seems to be of secondary concern. There seems to be an assumption that most supply chain professionals believe that their group purchasing organizations’ offerings have their supply expenses under control. Nothing could be further from the truth!
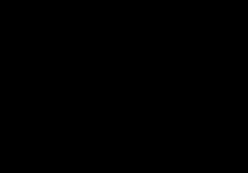
GPOs Are Only One Answer To The Supply Expense Savings Triangle
What most supply chain professionals don’t realize is that price is the smallest element (minimum 1:250 ratio) of the “Supply Expense Savings Triangle” (Figure 1) whereas customization and utilization is where the optimal savings opportunities reside for your healthcare organization. Let me explain in detail what I’m talking about.
Perspective
Robert T. Yokl
Figure 1
Customization is a technique where you don’t standardize on one product, service, or technology, but instead you tailor the product, service, or technology to your customer’s exact requirements. By applying this strategy, you will discover that your vital few customers (20%) will have higher or different requirements, while the majority (80%) of your customers will have lower or consistent requirements which translates into overall lower cost vs. standardizing on one product, service, or technology organizationwide. For example, we had a client that standardized on nitrile non-allergenic gloves (.19 each vs. 0.9 for latex) house-wide when only their hypersensitive employees required these expensive gloves. Once a policy was put in place by this hospital on who should be using their non-allergenic gloves, our client saved thousands of dollars annually through this customization, not standardization. You might think this concept is upside down, but the proof is in the new savings on each product, service, and technology you are purchasing.
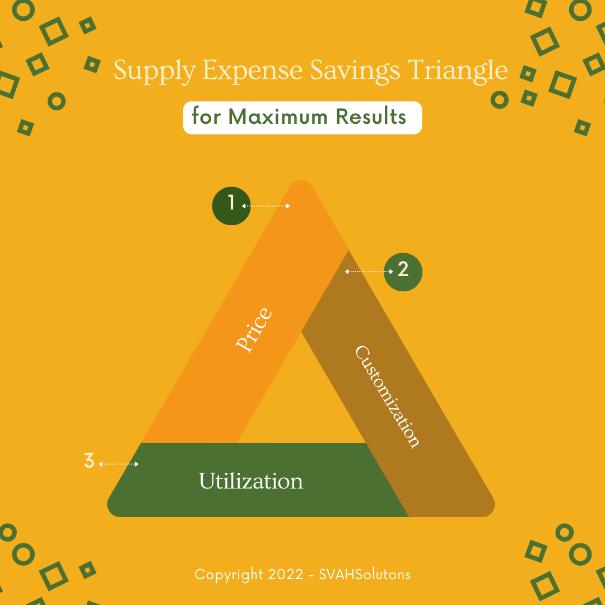
Supply utilization management (SUM) on the other hand is the measurement, monitoring, and control of the wasteful and inefficient consumption, misuse, misapplication, and value mismatches in a hospital, system, or IDN’s supply streams. Historically, we have documented SUM savings of one million dollars per 100 occupied beds for our clients who embrace this concept. Case in point: A university teaching hospital client of ours is projecting $500,000 in implemented SUM savings for their new laundry/linen service contract based on KPI metrics that we provide them compared to their peer cohort. These SUM savings are just the tip of the iceberg!
The Need For Even More Savings In 2022
The consulting firm Kaufman, Hall and Associates (KHA) predicts that “2022 is shaping up to be the worst year financially for U.S. hospitals and health systems since the beginning of the COVID-19 pandemic.” KHA also reported, “Hospitals and health systems saw gradual improvement in recent months but inflated labor cost, aggressive staff hiring, and prolonged hospital stays from sicker patients…reverse any gain hospitals saw this year.” That’s why your supply chain expense savings this year is mission critical for the financial viability of your healthcare organization. As we see it, the best way to make these new savings happen beyond price is through customization and utilization management. Your GPO’s contract savings in 2022, if any, will be meager, insufficient, and inadequate to fill the holes in your healthcare organization’s operating budget.
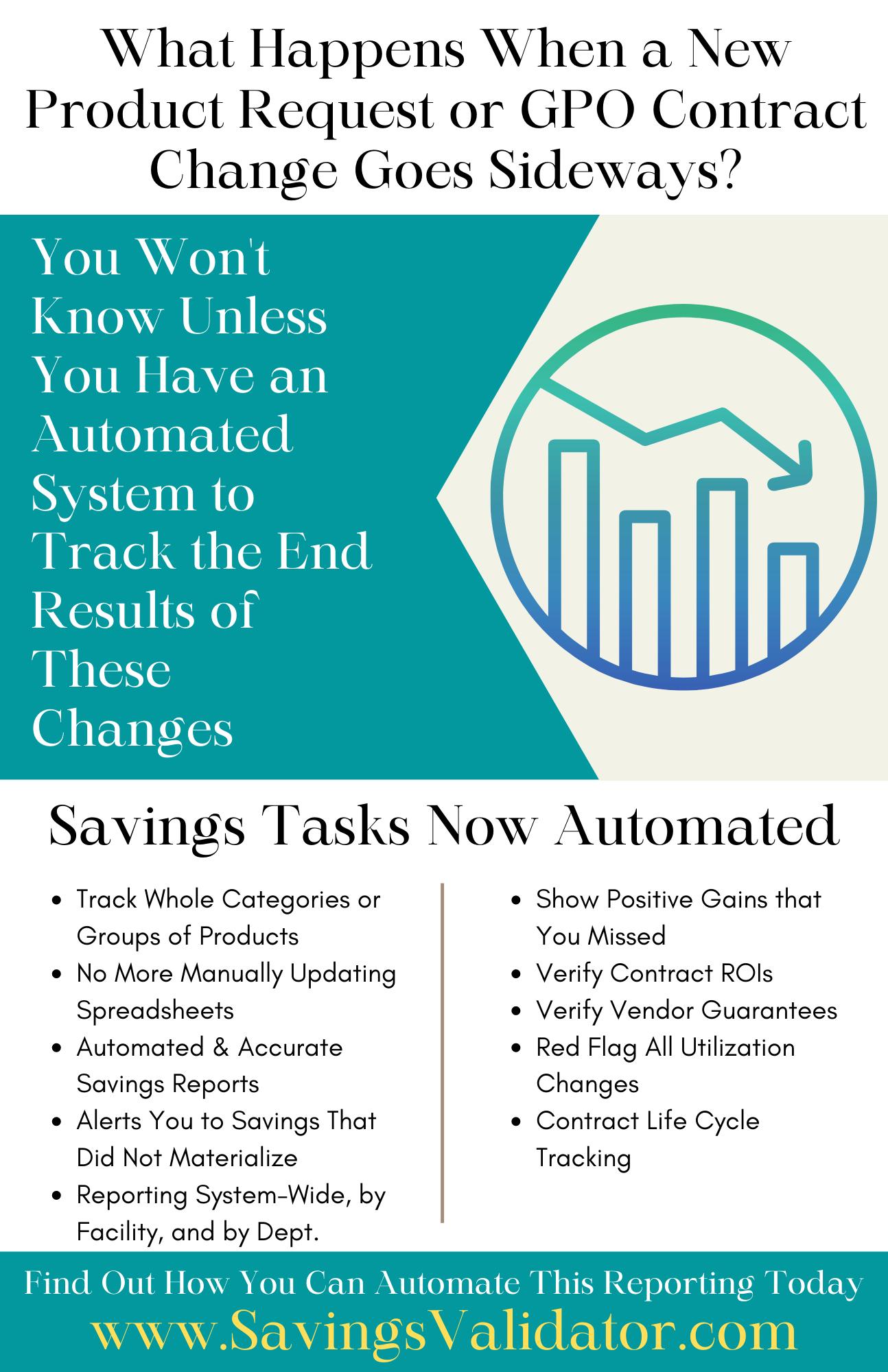
SUPPLY CHAIN
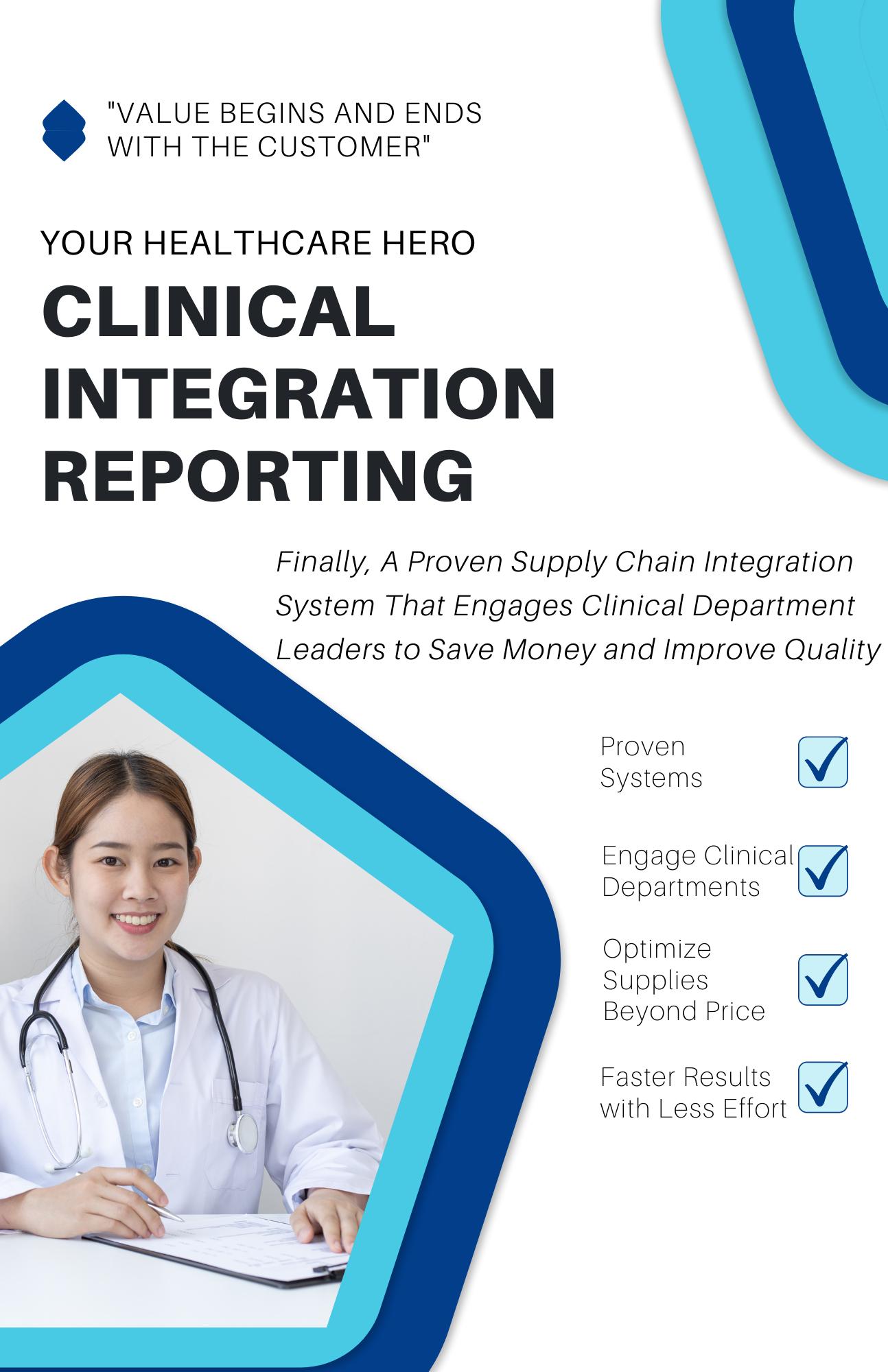