
6 minute read
Regulatory, Quality and Communication
CUSTOM-MADE MEDICAL DEVICES: DIFFERENCES BETWEEN THE MANUFACTURER AND WHO ADAPTS A MEDICAL DEVICE
by Clariscience
Until before the entry into force of the Medical Device Regulation (EU) 2017/745 (MDR), opticians have always been regarded, at least in Italy, as manufacturers of custom-made devices. In fact, prescription spectacles have always been considered a device to be manufactured on the basis of a written prescription from a qualified doctor indicating its design characteristics, and intended to be used only for a specific patient.
Although the definition of a custom-made medical device has not substantially changed following the entry into force of the Regulation, the publication of the MDCG 2021-3 Questions and Answers on Custom-Made Devices (March 2021) guideline may have paved the way for a significant change in the eyewear industry with regard to the manufacture of prescription spectacles.
The Medical Device Coordination Group document introduces the concept of an adaptable medical device and a new player, the person who adapts a medical device, i.e. the healthcare professional who assembles, forms and adapts an adaptable device for a particular patient.
According to the guideline, an adaptable medical device is defined as a mass-produced device that has to be adapted, adjusted, assembled or shaped, usually by a healthcare professional, at the point of care in accordance with the manufacturer’s validated instructions, to suit an individual patient’s specific anatomo-physiologic features prior to use.
Among examples of mass-produced adaptable medical devices, the guideline mentions spectacles . Although the situation has yet to be officially defined, this possible change of scenario makes it worthwhile to investigate what the differences are between the role of the manufacturer of custom-made devices and that of the person who adapts medical devices, as well as what regulatory obligations have to be fulfilled and what tasks fall to each.
The obligations of a manufacturer of custom-made devices as set out in Regulation (EU) 2017/745 are as follows. Manufacturers of custom-made devices shall:
Draw up, keep up to date and keep available specific technical documentation for competent authorities.
• Draw up the appropriate declaration required by the Regulation.
• Properly label the device and provide it with instructions for use, conveying all relevant safety and performance information to users.
• Establish all conditions for the correct use, maintenance, storage and transport of the device.
• Establish, document, implement and maintain a risk management system.
• Track the device as prescribed by the UDI system.
• Register as a manufacturer of custom-made devices and register the device in the European database EUDAMED.
• Register in the Database of Manufacturers of Custom-made Medical Devices of the Italian Ministry of Health and enter the list of devices (It. Legislative Decree of 5 August 2022, no. 137 - art. 7).
• Carry out a clinical evaluation and have a PostMarket Clinical Follow-Up (PMCF) system in place.
• Have a quality management system (QMS) in place to ensure that the device complies with the Regulation.
• Have implemented sufficient financial coverage measures to meet claims for damage caused by the device (Product Liability pursuant to Directive 85/374/EEC).
• Have (at least) one person responsible for regulatory compliance.
• Have a post-market surveillance system (PMS) in place.
• Having defined a vigilance system.
Let us now look at the responsibilities of who adapts a medical device. It should be noted that that - unlike the manufacturer of custom-made devices - Regulation (EU) 2017/745 does not list it as an economic operator and does not mention it at all.
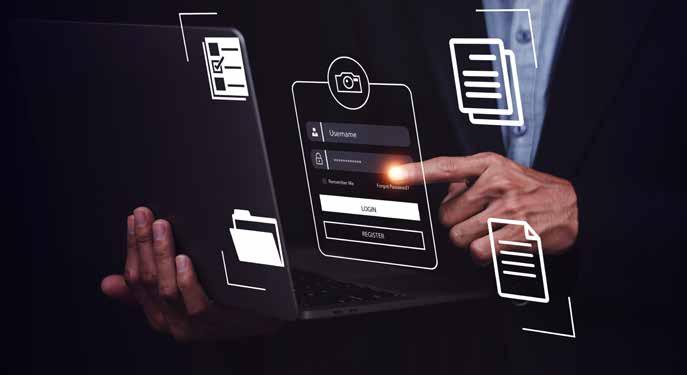
Since the Regulation does not set forth explicit obligations, it is assumed that who adapts a medical device is also a distributor of medical devices (as is any optician who sells frames, contact lenses, accessories, etc.) and, therefore, that the obligations that follow apply to all devices the optician makes available.
• Check that the device has been CE marked.
• Check that the medical device is accompanied by the information to be supplied by the manufacturer.
• Check that the declaration of conformity has been drawn up.
• Check (for imported devices) that the importer has identified themselves in the labelling.
• Ensure that the storage/transport conditions comply with the conditions set by the manufacturer.
• Send to the manufacturer and other economic operators (distributors, importers, authorised representatives) all safety and performance information relating to the medical devices.
• Check that the manufacturer has assigned a Unique Device Identifier (UDI) to the medical device.
• Ensure an appropriate level of traceability of the medical devices (for 10 years in the case of lenses and frames).
• Avoid making the device available if it is believed to be not in conformity with the MDR requirements. Keep a register of complaints, non-conforming devices, recalls and withdrawals.
• Inform the competent authority if it is believed that the medical device presents a serious risk or is falsified.
• Cooperate with the manufacturer, economic operators and competent authorities to ensure that the necessary corrective actions are taken. In the event of a serious risk, provide the competent authority with precise information on noncompliance and corrective actions taken.
• Provide the information and documentation available to demonstrate conformity of a medical device at the request of a competent authority.
• At the request of a competent authority, provide samples of the device free of charge.
One can easily see how the obligations and responsibilities of the manufacturer of custom-made devices are significantly more burdensome than those of who adapts a medical device.
In summary, while who adapts a medical device has to fulfil product verification and post-market surveillance obligations only, the manufacturer of custom-made devices - similarly to the manufacturer of medical devices - is required to draw up, update and maintain specific technical documentation, to manage risk appropriately, to carry out a clinical evaluation, to register the device in national and EU databases, to take out insurance coverage, as well as to operate according to a documented QMS, as well as to appoint a person responsible for regulatory compliance.
Summarizing, the position of the optician with regard to the manufacture of prescription spectacles has still not been clearly and officially defined by the competent authorities.
The obligations and responsibilities of the optician, at the light of the Regulation (EU) 2017/745, might therefore undergo significant changes in relation to future, and much awaited, EU and/or national provisions.
Clariscience, as an independent and highly specialized consultancy agency, offers a panel of integrated services designed to help its customers from the medical device and IVD sector, in achieving and maintaining regulatory and quality compliance and succeeding on the market through a clear and inspiring scientific communication.
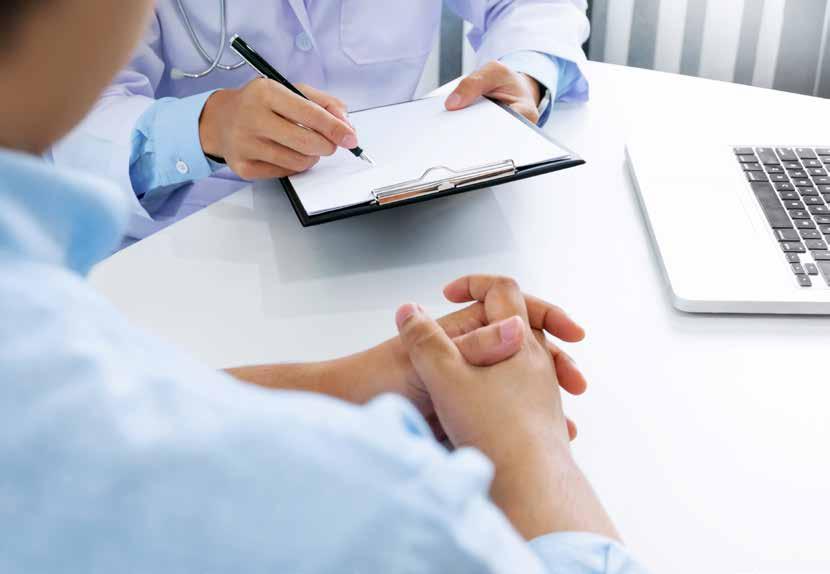