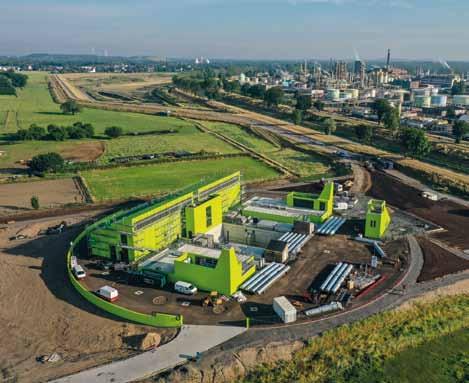
5 minute read
Abwasserkanal Emscher Bauabschnitt40
Porr Abwasserkanal Emscher Bauabschnitt 40
Im Ruhrgebiet entsteht im Rahmen des Projekts »EmscherUmbau« ein Abwasserkanal, der Teil eines bedeutenden Strukturwandels der Emscherregion ist. Der Bauabschnitt 40 ist ein 10 km langes Teilstück dieses Kanals, bestehend aus zwei parallelen Tunnelröhren, die im Tübbingverfahren hergestellt wurden. Die Herausforderungen an Sicherheit und Logistik waren enorm: Daher wurde im Bauabschnitt40 Pionierarbeit geleistet, denn der Vortrieb, überwiegend im Emschermergel, wurde mit zwei Erddruckschilden realisiert und war in besonderem Maße durch den extrem kleinen Innendurchmesser des Tunnels von 2,60m und den daraus resultierenden Platzverhältnissen massiv eingeschränkt. Dabei kam eine der kleinsten Tunnelvortriebsmaschinen (TVM) der Welt zum Einsatz.
Advertisement
Blick auf die Emscher und den ersten Startschacht SD.033. © Porr GmbH & Co. KGaA
Das Generationenprojekt
Die Quelle der Emscher liegt in Holzwickede bei Dortmund, in Dinslaken fließt sie in den Rhein. Da der Steinkohleabbau ein stetiges Absinken der Landschaft um bis zu 30m und mehr mit sich brachte, konnte erst nach dem Ende des Bergbaus mit der Verlegung unterirdischer Abwasserleitungen begonnen werden. Unterirdische Rohrleitungen hätten dem Druck durch die Bergsenkungen nicht standgehalten.
Der Abwasserkanal Emscher (AKE)
Die Industrialisierung des Ruhrgebiets wäre ohne die Emscher nicht möglich gewesen. Ihre Renaturierung hat eine große Bedeutung für den Strukturwandel der Region. Seit 1992 läuft das Generationenprojekt Emscher-Umbau, das größte Flussumbauprojekt Europas, bei dem Neuland betreten wurde. Grundlage der ökologischen Verbesserung von 350 Flusskilometern ist eine der modernsten, abwassertechnischen Infrastrukturen.
Der Bauabschnitt 40
Von der Bernemündung in BottropSüd führt ein 10 km langes, als Doppelrohrtrasse mit Tübbingausbau ausgeführtes Teilstück zum Pumpwerk Oberhausen-Biefang. 199 Mio. e Investitionssumme flossen in das Einzelprojekt, das von der ARGE Emscher BA 40 zwischen Dezember 2013 und April 2019 realisiert wurde. Der Tun-
neldurchstich der beiden TVM ist im Juni 2017 in der Baugrube des Pumpwerkes Oberhausen erfolgt. Während des Vortriebs waren mehrmals die Autobahnen A42 und A3, diverse Versorgungsleitungen, Bahntrassen sowie Strommasten zu unterfahren. Die Bauausführung oblag der Porr GmbH & Co. KGaA sowie der Porr Bau GmbH. Der Zweirohrkanal war erforderlich, da er eine Tiefenlage von mehr als 25m und einen Förderstrom von mehr als 3m³/s aufweist, denn im Fall eines Kanalausfalls reicht die an anderen Stellen vorgesehene Lösung, das Abwasser alleine über provisorischen Druckrohrleitungen weiterzupumpen, nicht aus. Zusätzlich zum Zweirohrkanal wurden 14 Schächte in Schlitzbauweise mit bis 20 m Durchmesser und bis 40 m Tiefe sowie zwei Druckluftvortriebe DN1600 mit einer Gesamtlänge von rd. 760 m und zwei Mikrovortriebe DN600 mit einer Länge von 100 m errichtet. Für den Innenausbau der Schächte wurden 2.200 t Stahlbeton und rd. 22.000 m³ Beton verbaut. Für einen optimalen Korrosionsschutz des Betons wurden einige Schächte mit chemikalienbeständigen PE-HD Platten versehen.
Ausbau in Tübbingbauweise
Das Besondere an dem Projekt sind die im Tübbingausbau aufgefahrenen Kanäle (DN 2600). Statt des üblichen Rohrvortriebsverfahrens, bei dem die Röhren aus massiven Stahlbetonrohren hergestellt werden, wurden sie von einer Tunnelvortriebsmaschine mit mehr als 100.000 hochsäurebeständigen Betonsegmenten, sogenannten Tübbings, ausgebaut. Die geologischen Verhältnisse in der Tiefenlage bis zu 45 m sowie die langen Vortriebsstrecken waren maßgeblich für die Entscheidung, dieses aus dem Tunnelbau bekannte Verfahren erstmals bei einem abwassertechnischen Infrastrukturprojekt einzusetzen. Jeder Tübbingring ist in sechs gleichgroße Segmente mit einer Breite von 1.180 mm, einer Dicke von 25 cm und einem Gewicht von 1,10 t geteilt. Da die langen Fließzeiten des Abwassers im späteren Betrieb die Korrosionsgefahr erhöhen, wurden die Tübbings im Bereich der Schächte mit einer zusätzlichen ca. 1 cm dicken Polymerbetonoberfläche verstärkt. Das Auffahren der Röhren erfolgte zeitgleich mit einem horizontalen Abstand von 3,10 m. Dabei fuhren Tunnelvortriebsmaschinen in Längsrichtung um mindestens 50 m versetzt. Der Bohrdurchmesser betrug 3.397 mm. Mit Blick auf die spätere Nutzung waren die Anforderungen an die Dichtigkeit der Tübbingfugen und die Ebenheit der Oberfläche extrem hoch. Zur Qualitätskontrolle und sicheren sowie exakten Steuerung der Tunnelvortriebsmaschinen wurden während des Vortriebs mehr als 5 Mrd. Messwerte von den Vortriebsmaschinen, rd. 35.000 Messungen entlang dem Tunnel sowie die Daten der mehr als 100.000 Tübbingsteine teilweise in Echtzeit verarbeitet und überwacht. Der Innendurchmesser des Kanals von 2,60 m liegt an der Grenze des technisch Machbaren für den Tübbingausbau mit einer Tunnelvortriebsmaschine. Zum Einsatz kam hierbei die Herrenknecht ErddruckschildVortriebsmaschine (EPB-TVM). Die zu durchfahrende Sedimentschicht ist eine heterogene Mischung aus Sand-, Ton- und Mergelsteinen, die hohe Drehmomente beim Abbau verursachen. Daher wurde der Boden während des Vortriebs mit Schaum konditioniert. Bis zu 582m bewältigten die Maschinen pro Monat.
Funktionierende Logistik
Bei einem derartigen Tunnelprojekt war eine funktionierende Logistik von großer Bedeutung. Stillstandszeiten aufgrund fehlender Materialtransporte mussten vermieden werden. Da die Nachläufer der Maschine keine Stellflächen boten, konnte nur wenig Material auf Vorrat gelagert werden und musste »just in time« geliefert werden. Da bei einer Strecke von 10 km Wartezeiten unausweichlich gewesen wären, wurde sie in drei Vortriebsabschnitte geteilt und die Startschachteinrichtung inklusive Vortriebslogistik zweimal umgebaut. So konnte eine reibungslose Versorgung der Schildmaschine gewährleistet werden.
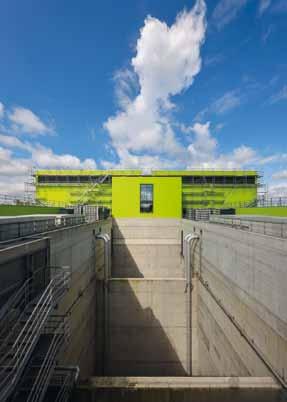
Bick aus dem Vorstollen in Richtung Tübbingtunnel © Porr GmbH & Co. KGaA
Eine weitere Entlastung erfolgte mittels des erstmalig in Deutschland eingesetzten Zwei-KomponentenRingspaltmörtels. Dabei wird der Mörtel nicht über einen Mörteltank auf die Maschine gefahren, sondern über eine Transferleitung direkt von der Mischanlage in den Mörteltank auf der Vortriebsmaschine gepumpt. Damit er in der Transferleitung nicht hart wird, wird er in zwei Komponenten getrennt. Die A-Komponente besteht aus Wasser, Zement, Steinmehl, Bentonit und einem Stabilisator. Der Mörtel bleibt sehr flüssig und kann so gepumpt werden. Während des Verpressvorgangs wird am Ende der Leitung im Schildschwanz, der sogenannten Verpresslisene, die B-Komponente bestehend aus Wasserglas hinzugefügt und dient als Beschleuniger, damit der flüssige Mörtel schnell erhärtet und die notwendige Bettung der Tübbingröhre gewährleistet ist. Um ein Entmischen der A-Komponente in der Mörteltransferleitung zu verhindern, musste eine hohe Fließgeschwindigkeit bei möglichst kleinem Querschnitt erzielt werden.
Technische Herausforderungen
Da aufgrund des kleinen Querschnittes kein 2-etagiger Aufbau der Tunnelvortriebsmaschine möglich war, betrug die Gesamtlänge der EPB-TVM am Ende 90 m. Alleine die Förderschnecke maß 8.80 m, der Schildmantel der Vortriebsmaschine knapp 15 m. Daher wurde ein aufwendiges Arbeitssicherheits- und Rettungskonzept ausgearbeitet, denn das Arbeiten in den engen Röhren sowie in der beengten Maschine stellte große Herausforderungen an das Bauteam. Die lichte Höhe im Nachläuferbereich betrug rd. 1,60 m, die Durchgangshöhe auf dem Laufsteg lag bei rd. 1,20 m. Zwischenzeitlich begleitete ein Sportwissenschaftler die Vortriebsarbeiten, um Schäden am Stütz- und Bewegungsapparat der Mitarbeiter*innen vorzubeugen. Mit jedem Vortrieb vergrößerte sich die Fluchtweglänge. Im längsten Abschnitt betrug sie 1.200 m. Unmittelbar nach dem Durchfahren der Tunnelvortriebsmaschinen mussten die neun Hauptschächte aufwendig als Rettungsschächte begehbar gemacht und mit Rettungstreppenturm sowie einem elektrischen Aufzug ausgestattet werden, ein Rettungssanitäterteam begleitete ständig die Vortriebsarbeiten. Ein Personenortungssystem, Brandmelde- und Löschsysteme, Rauchschotts und eine Kommunikationsanlage ergänzten das Sicherheitskonzept. Wenn Ende 2021 die letzten Kanäle angeschlossen sind, werden alle diese Mühen belohnt und das Versprechen der Emschergenossenschaft wird eingelöst sein: Wir geben den Menschen ihren Fluss zurück. Glückauf.
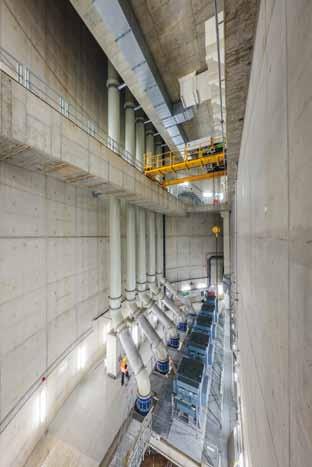
Blick ins Innere der Vortriebsmaschine kurz vor dem Ringbau © Porr GmbH & Co. KGaA
DIPl.-Ing. IrIna mElzEr WEItErE InformatIonEn Porr GmbH & Co. KGaA D-40472 Düsseldorf info@porr.de www.porr.de