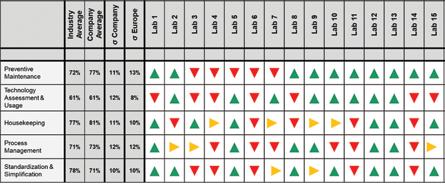
5 minute read
Ensuring Efficiency in Packaging Process should be a top Priority for Pharma Packaging Companies
Figure 2: Maturity assessment of 15 corporate labs
the QC labs are. All enablers are scientifically derived and proven to have a direct impact on the labs’ overall outcome performance levels. The enabler questions are structured in three main categories; namely the Maintenance & Quality System, the Planning & Steering System and the Management System. All three categories are again divided in total 13 subcategories. Due to their proven positive effect on performance, the enablers act as a starting point and toolbox for defining particular improvement initiatives. Further information about the QC benchmarking approach can be found in article in issue 47 / 2022.
Advertisement
The maturity levels of the 15 sites reflected the variability in the respective performance levels (cf. Figure 2). Especially the sub-categories Housekeeping, Process Management and Standardisation & Simplification showed a significant variability in maturity, while having an overall high degree of maturity on the corporate level. This indicated that certain successful practices already exist in those fields among some labs, while other QC labs have a significant improvement potential in the same field (Figure 2).
A subsequent project has been initiated to systematically identify successful practices that already exist in the lab’s network and at facilitating the corresponding knowledge transfer among all labs. Thereby, one strives for an optimal use of existing improvement opportunities.
When analysing the benchmarking data, it became apparent that one of the major challenges for QC labs is the complexity they face. Large variations in the number of different tests to be performed and fluctuating test volumes inhibit the standardisation of lab layouts and the associated processes. Furthermore, the labs face the problem of limited available floor space. Having this challenge in mind, five labs were selected for the further analysis. The labs were selected according to their maturity levels. Three labs with a comparably high maturity and two with a rather low level of maturity had been selected for further on-site investigation and documentation of the status quo. The idea behind that selection was to enable a knowledge transfer from advanced to less advanced labs and consequently make effective use of existing successful practices which then should result in an increase of the overall maturity and performance on a corporate level.
Another field of action that had been identified during the QC benchmarking was the site’s handling of quality events. Especially in the share of CAPAs overdue and reoccurring deviations, mayor differences had been observed. Consequently, the event handling process was analysed on both, the corporate and site level. The overall event handling process was defined in detail in a global standard operating procedure. When examining the local translation and implementation of that global SOP, two distinct bottlenecks had been identified. This was the initial impact assessment (IIA) and the root cause investigation (RCI).
For the initial impact assessment for example, a hard deadline of three days was defined by the global SOP. This deadline did not account for local specifics of the different sites. In dedicated site interviews it was noticed that depending on the complexity of the different sites, the three days are not sufficient for a profound IIA. In this respect, two phenomena had been observed. Firstly, in some labs IIAs had been performed on rather superficial level. This resulted then regularly in rather ineffective RCIs and CAPAs, considerably increasing the share of reoccurring deviations. Secondly, some other labs tended to perform a profound IIA, which often resulted in overdues in complex sites. This resulted consequently in backlog and started a vicious cycle that leads to growing shares of CAPAs overdue.
Having this results in mind, a more flexible setup of local guidelines was advised that allows the consideration of a site’s complexity in implementing global standards. The set IIA deadline should be feasible for all sites. Otherwise, there is an inherent risk of evasive operational behaviour with negative consequences such as the previously mentioned increase in reoccurring deviations and CAPAs overdue.
These examples show how patterns in benchmarking data can be analysed, their root-causes be identified and consequently lead to effective and practical improvement actions.
Outlook
Data is the basis for all improvement initiatives. It provides one with a holistic picture of the status quo, allowing the identification of improvement potentials. The systematic identification, adaption and implementation of successful practices contributes significantly to a company’s journey towards operational excellence. Continuous improvement requires that deficien-
cies are made visible and the effectiveness of improvement actions is verifiable. This article thereby showed two distinct examples for how improvement initiatives may be built based on benchmarking data. St. Gallen’s holistic approach on measuring performance allows companies to define strategically improvement initiatives that lead to stable and long-lasting enhancement of a company’s performance.
In the next journal issue, the St. Gallen team will conclude their article series with a summary of the operational excellence research field in the context of the pharmaceutical industry and provides an outlook to futures trends and current research activities in that field.
Literature is available at www.pharmafocusasia.com
AUTHOR BIO
Matteo Bernasconi is a research associate at the University of St.Gallen. At the Institute of Technology Management, he works in the Operational Excellence team with a special focus on the pharmaceutical industry. Currently, his academic work concentrates on preventive risk quality management and data-driven decision-making.
Gian-Andri Steiger is a research associate at the University of St.Gallen. At the Institute of Technology Management, he works in the Operational Excellence team with a special focus on the pharmaceutical industry. Currently, his academic research focuses on quality assurance excellence in the pharmaceutical industry.
Marten Ritz is a post-doctoral researcher at the University of St.Gallen. At the Institute of Technology Management, he leads global collaboration projects to support pharmaceutical companies in developing KPI strategies and implementing quality metrics programs. His academic research focuses on aligning OPEX initiatives across manufacturing and QC lab in pharmaceutical production.
Thomas Friedli is a director at the Institute of Technology Management. He leads a division of 14 PhD students and two post-docs. His research areas include strategic management of production companies, management of industrial services, and operational excellence. He is editor, author and co-author of numerous books and articles.
www.quantysclinical.com
104 Beds 4 LCMS/MS Over 40 Methods
ACCREDITED BY
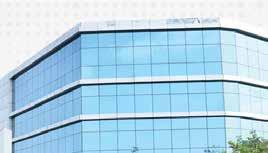


ANVISA
Agência Nacional de Vigilância Sanitária
GCC
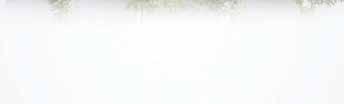
Ph-II & Ph-III with INDICATIONS IN

Cardiology Neuropsychiatry De-addiction Oncology
Email: info@quantysclinical.com Call: +91 2836 253330
EXPERIENCE IN CONDUCTING BIOEQUIVALENCE STUDIES ON
INJECTABLES LIQUIDS TRANSDERMAL PATCH
TOPICAL CREAMS ORAL SOLIDS INHALERS, ORAL & NASAL SPRAYS
OTHER SERVICES
In-Silico studies Trial Monitoring Bioanalytical Services Medical Writing
Plot No. 668, 671, 672, New Area Kandla Special Economic Zone, Gandhidham, Kutch-270230, India