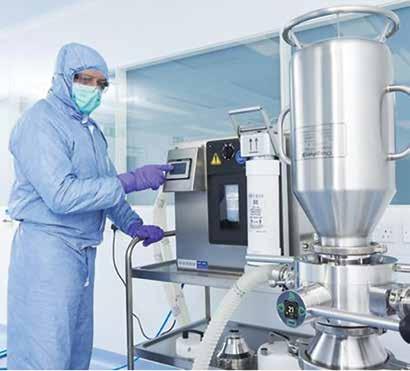
11 minute read
SBV Technology and Eradicating the Risk of Contamination in Aseptic Manufacturing
Containment is key during aseptic processing and this has led to the development of new transfer methods that are both enclosed and minimise the requirement for operator intervention. In this article, the author discusses modern containment methods and the advent of split butterly valve technology to improve production processes..
Christian Dunne, Global Product Manager ChargePoint Technology
Advertisement
(Figure:1)
Introduction
The global CMO Market is growing at a CAGR of 12–13 per cent between 2018 and 2022. The growth is attributed to increased outsourcing of generic drugs by Big Pharma companies. Additionally, medium and small pharma and biopharma companies, who do not possess adequate infrastructure, will also outsource, thereby driving the market. Presently, non-sterile drug manufacturing dominates the global CMO market. However, the sterile manufacturing market is expected to grow at a higher rate (15 per cent) than the non-sterile market (9 per cent) thru 2022.
Aseptic Processing
Manufacturing environments contain many potential sources of contamination which present significant hazards during the manufacturing of biopharma products. It’s important for firms to ensure successful containment to prevent endotoxins, microorganisms or particles entering the manufacturing environment as this could put patient safety at risk.
Equipment, materials, and people within the manufacturing environment can all offer potential sources of
contamination if not suitably controlled. In response to this need we have seen multiple technologies starting to be developed, intended to allow the safe and sterile transfer of sterile APIs, biologics and biosimilars during processing. Isolators and Restricted Access Barrier Systems (RABS) have become commonplace technologies used to meet these needs in recent years.
Regardless, both of these solutions have their drawbacks. Isolators are typically challenging when it comes to transferring materials in and out of the chamber and this can cause productivity delays during the startup and shut off processes. Furthermore, RABS offer lower integrity chambers and this solution also requires sterilisation or manual cleaning processes such as Steaming in Place (SIP) between uses and this has increased time pressures which can cause delays.
Aseptic SBV enables decontamination to take place in a closed environment. Once sealed, a gap is created between the two discs and Hydrogen Peroxide (H2O2) gas can then be flushed through this enclosure which decontaminates the space. Chemical Indicators (CIs) are used to validate and reassure the users that full coverage of the enclosure has been achieved. Biological Indicators (BIs) are then used to ensure a 99.9999 per cent,
Dock SIP Cap illustration 1a
also known as a 6-log reduction in bacterial spores has been achieved.(Figure:1)
Case study
Sterile API Addition to a Mixing Vessel
A Contract Development and Manufacturing Organisation (CDMO) specialising in blow-fill-seal technology required a sterile solution for transferring drug substance during aseptic production. Its capabilities extend well beyond manufacturing, with an in-house development team specialising in all aspects of bringing a product to market - from lab scale batches, regulatory filings, scale-up, manufacturing and distribution.
Challenge
The CDMO was looking to solve the issue of charging sterile drug substance into a mixing tank. This is a common problem with all aseptically prepared products.
It was imperative to the process to sustain sterile conditions whilst docking a vessel to the container and then moving solid drug substance to form liquid. The product was sterile filtered as it was passed through the filler to become a completely dissolved liquid. However, in this application, the product being delivered to the filler was a suspension and so this was not a possibility.
The entire process needed to be performed under strict aseptic conditions, in order to remove the need to upgrade the whole room from a grade C cleanroom to grade A or introduce an over pressurised grade-A area around the point of fill.
Conventionally RABs and isolators would have been favoured in this situation due to the benefits which include enhanced sterility assurance. However, these both require a high initial and longterm capital investment and also require significant footprint within a facility so the company decided to search for a solution that was more appropriate to their application.
Application
An aseptic bio-valve product was selected to overcome these aforementioned shortfalls, providing a fully sealed powder transfer attached to the inlet port of the vessel. This valve can be pre-steam sterilised alongside the vessel, unlike traditional conventional connections incl SBVs (see illustration 1a/b). Once connected, it removes any contamination that might have come from the environmental surroundings thanks to the mating faces of the transfer being fully controlled and validated (see illustration 2a/b). (Figure:2) (Figure:3)
SIP through Cap – Pre-Sterilising Active & Vessel illustration 1b

(Figure:2)
The bio valve creates a sealed chamber between the passive and active sections and when these two halves are docked, the sealed compartment is then bio decontaminated with Vaporised Hydrogen Peroxide (VHP).

(Figure:3)
Illustration 2a
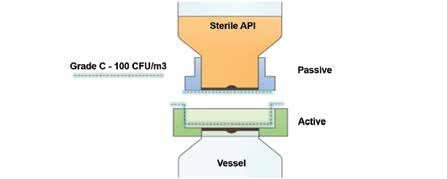

Illustration 2b
This process thereby removes any biological contamination to a validated 6-log reduction. Furthermore, once fully mated, the discs can be opened which allows the product to be transferred from transfer container to vessel, free from the risk of contamination. This allowed the process to be performed with enormous cost and production benefits and still within a grade C space, although the process needed to be fully validated first to ensure that the initial expected benefits could be confirmed.
Validation
Firstly, microbiological validation must take place. This produces a validated decontamination cycle which enables the H2O2 gassing phase. Following this, there follows four phases which the generator will run to ensure that a fully validated gassing cycle is achieved every time.
Firstly, it’s important to condition the chamber to reduce the humidity and Acceptance criteria for the cycle included: provide an ideal condition for biological All CI strips used in the cycle must have changed colour. kill. Following this dehumidifying step, The positive control BI must demonstrate growth. the VHP is introduced to the chamber At least one BI from each location must not demonstrate growth. gradually for increased decontamination. The VHP concentration is then maintained in order to deactivate any microchange was analysed to confirm that even now boast improved sterility assurance, biological activity within the chamber. vapor distribution has taken place. The a greater ease of use for operators, and Finally, once biological decontamination BIs were then relocated to a Spordex low maintenance which has certainly is completed, the VHP is removed from culture media and placed in an incubator improved the CDMO’s process. the system so that no harmful levels of (between 55-60OC. They were then kept As the requirements of complex APIs residue are left. Typically, the acceptance under observation for seven days and continue to evolve, it will become increaslevel is 1ppm although in this instance analysed for potential microbial growth). ingly important for technologies in the 0.4ppm was the achieved level. The Once the cycle was developed it was sector to be agile in order to adapt to new CDMO used a lower residue limit to then performed three times to form the demands and changing customer needs. ensure they had a robust system with no Performance Qualification (PQ) for this chance of contamination of the product element of the process. Multiple media due to gas residue. runs were performed prior to validation
The complete decontamination cycle can take as little as four minutes. For this particular application, the process was only being performed once a day and to ensure a robust cycle was produced, additional time was added to each of in order to fully validate the system and proving successful, these were then carried forward with three media runs at PQ. The sterile hold achieved greater than 10 days with product transferred to the container and with the bio valve positioned in the AUTHOR BIO the critical phases, ensuring that deconclosed interlocked location. The sterile tamination was confirmed, and gas was hold period was achieved for the passive aerated from the system. This resulted section (product in transfer container) in a 41minute full cycle. (Table:1) for 48 hours.
Primary cycles employed Cis to control H2O2 distribution. When Conclusion Christian Dunne is the global acceptable CI levels were achieved BIs The installation is now fully operational. product manager at ChargePoint were introduced to confirm full decontamination was attained. Once both the As well as benefiting from low capital equipment cost, a smaller footprint and Technology for the sterile containment solutions. For the past 20 years Christian has been BIs and CIs were collected, their colour improved installation, the CDMO can creating innovative solutions for the pharmaceutical, biotech, cell therapy and fine chemical industries to Parameter/Phase Dehumidification Conditioning Decontamination Aeration overcome high potency containment and aseptic processing challenges. Time, hh:mm 00:10 00:00 00:06 00:25 His technical expertise spans high containment isolators, grade A (ISO5) Airflow, SCFM 16 N/A 9 16 sampling & dispensing facilities, together with R&D and production Injection rate, g/min N/A N/A 4.0 N/A filling line restricted access barrier systems (RABS) and isolators. Humidity, mg/L 2.3 N/A N/A N/A

Meeting the Logistics Needs of Asia Pacific’s Growing Clinical Trials
Karen Reddington, President, Asia Pacific, FedEx Express
A growing middle class and aging population has fueled the ascent of the Asia Pacific region in the global healthcare industry. Now the pharmaceutical sector is responding by tapping more patients in the region for new drug development trials.
Asia Pacific has advantages that makes it attractive for clinical trials: access to a ready and diverse patient pool, lower recruitment costs and favorable policies. The focus of clinical trial researchers is now shifting from developed markets of Japan, Australia, South Korea, Singapore towards emerging economies like Thailand, China, the Philippines and Vietnam. Local regulatory frameworks are course-correcting to keep pace with the industry’s development.
New markets, familiar logistical challenges
In the nearly 20 countries involved in clinical trials in the region, the sites are moving away from the first and second tier cities to smaller ones and remote locations. This poses obvious logistical challenges beyond just connectivity or understanding local provincial customs and regulations. Reliable transit times are essential to ensure irreplaceable patient samples that are delivered in the right condition and on time. Cold chain packing solutions and dry ice deliveries are required, plus robust contingency management to navigate unexpected obstacles. The ability for logistics companies to address these chal

lenges, while at the same time offering cost competitiveness and delivering a high level of service to the pharma customers, is critical.
FedEx is one organisation that is working to achieve this by combining its core network transportation capabilities with specific value-added elements for pharma customers. Its Clinical Express solution for time and temperature sensitive samples is designed to assist laboratories, Contract Research Organizations (CROs) and pharma companies in the overall logistics management of their clinical trials.
Local solutions for market-specific needs
FedEx has also come up with some market-specific solutions. For example, site investigators in Japan require on-site support and adherence to stringent protocols while performing pick-ups from clinical trial logistics providers. To meet this need, it has built a team of 500 trained and certified drivers pre-approved for entry into hospitals. These drivers provide specialised white glove services from samples packing to document preparation, which are unique to Japan.
Sites in Australia require the flexibility to order packaging supplies at the time of booking, instead of ordering supplies in advance. So, FedEx set up a dedicated Customer Service desk to manage these requests and a fleet of 300 drivers to bring packaging supplies and dry ice to the sites during pick-up.
Medical trials in Japan and Korea are dominated by small to mid-sized local pharma players, who require local drug storage centers. In late 2019, FedEx Life Science Center (LSC) in Shinkiba, Japan underwent a major upgrade to serve the complex logistics needs of its pharma customers and contract research organizations (CROs). This facility now features smarter storage systems for keeping clinical trial test drugs or Investigational Medicinal Product (IMPs) in bulk rather than shipping them individually, saving more cost and clearance time. LSC is able to provide economies of scale, making it an important value-added service to customers.
Expertise and innovative technology at the core
The demand for global cold chain logistics is set to grow more than 10% CAGR over the next five years . Logistics service providers are innovating to improve reliability. Solutions like the FedEx Medpak Vi o C shipper box are made from high-grade Vacuum Insulated Material (VIP) fitted with Phase Change
Karen Reddington is president of the Asia Pacific Division of FedEx Express, the world’s largest express transportation company.

Material (PCM) that can maintain temperatures between 2 to 8°C for up to 96 hours. The VIP boxes and PCM panels are reusable, making them cost effective and environmentally friendly. In case of delays during transit, there are storage facilities that allow these packages to ‘hibernate’ temporarily while maintaining their temperature integrity. This solution can be coupled with FedEx proprietary technology SenseAware ® , a near real-time monitoring device which tracks temperature during the journey of the shipment. It can record other key variables including humidity, light exposure, shock events and other environmental factors that could impact the shipments
As we enter the third decade of the century, global health issues continue to remain a hot topic. Pharmaceutical professionals have higher demands of their time as they tackle even greater challenges. By continuing to offer the right support and services to this industry, experienced logistics providers will be able to help in driving vital growth in the years to come.
https://www.technavio.com/report/cold-chain-logistics-market-for-pharmaceuticals-industry-analysis?utm_source=pressrelease&utm_ medium=bw&utm_campaign=t17_wk4&utm_content=IRTNTR40854