
8 minute read
Testing, Testing….
Testing, Testing….
UK based Durham Lifting offers a comprehensive range of lifting services including inhouse design and fabrication of modular beams and heavy lifting equipment, a number of testing facilities including a 3,000 tonne test bed and a sales and rental department. Editor Mark Darwin spoke with managing director Amanda Gardiner about its history, recent developments and plans for the future.
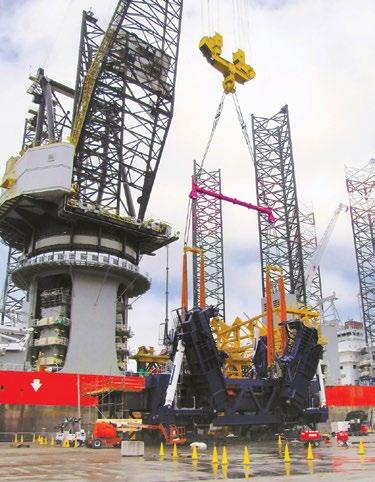
Durham Lifting was established in 1996 by Frank Pickersgill, a pioneer of the modular spreader beam concept.The company has revenues of £6 million, of which sales and rental account for about 30 percent with the rest split equally between fabrication, testing and service.
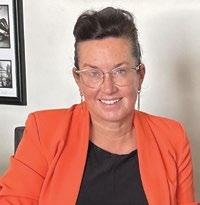
“Durham Lifting excels in providing comprehensive heavy lifting solutions, guiding our clients from concept to completion,” said Gardiner. “With years of expertise dealing with large capacities, we offer various testing facilities capable of handling up to 3,000 tonnes. Our integrated design and fabrication facilities ensure we are the ideal partner for our client’s needs.”
The family-run business has recently undergone a change of ownership. The reins and 100 percent ownership now belong to Frank’s daughter, Amanda - who has been managing director of the company for more than 25 years - and son-inlaw Paul, a qualified design engineer and highly experienced proof load tester who has been instrumental in the development of the company’s new product range. The third generation - in the form of his grandchildren Samuel and Olivia - are also involved in the business.
Durham Lifting is based in Middlesbrough in the North East of England, with a branch in Newton Aycliffe. Expansion of the company has seen the launch of the branded product Multisec, easily recognisable by its distinctive pink modular spreader beams and frame systems. Two years ago, Multisec began expansion overseas with distributors in Europe and East Asia and these will be added to in the future.
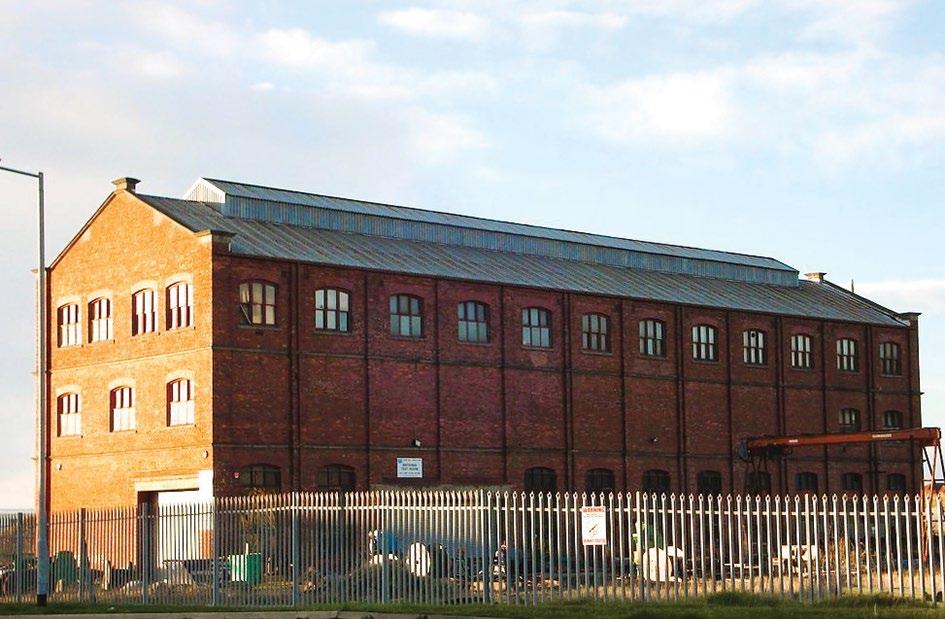
So how did you get into the industry?
“My father was a crane engineer at British steel and Kone Cranes, then partnered up with a company called Ken Elder Engineering,” said Gardiner. “At 13 I needed something to do during the summer holidays and ended up answering the phone and running errands etc... When he became a director of Ken Elder Lifting, I became more involved and began working full time. I was running the hire department at 19 - dealing with some very big equipment even then - and became a managing director in 1996 at the age of 23. Growing the business has been challenging and has included lots of learning and great fun. I love being surrounded by a great team who share the passion for everything we do.”

Historic building
The company’s head office is housed in the iconic Britannia Test House building which was purchased in 1991. It dates back to the early 1920’s, when it served Teesside’s rapidly growing industrial base which included shipbuilding and railways to satisfy demand for accurate testing and certification of materials.
The Test House initially focussed on assessing the mechanical properties - tensile strength, hardness, and resilience - of materials such as iron and steel. However, it soon evolved into a hub of innovation, collaborating with engineers, metallurgists and scientists to refine testing methodologies. This led to the establishment of industry benchmarks for material quality and performance as well as influencing local, national and international standards resulting in Britannia Test House’s reputation as a pioneer in precision testing.
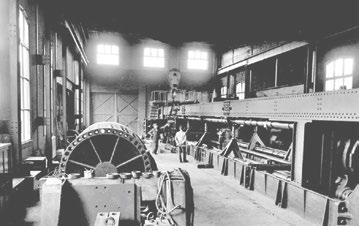

The current three storey brick building is the sole surviving remnant of the Britannia Steelworks, once owned by the revered company Dorman Long which in 1967 merged with South Durham Steel Iron Co, Stewarts and Lloyds to create British Steel and Tube just before the steel industry was nationalised becoming the British Steel Corporation.
Dorman Long constructed many of the most iconic bridges of the twentieth century including Sydney Harbour Bridge, the New Tyne Bridge, and the Tees Newport Bridge in Middlesbrough as well as the Forth Road Bridge in 1964, the Severn Bridge in 1966 and the Humber Bridge in 1981.
The massive Avery test machine in the Test House that is still going strong today at Durham Lifting was commissioned to test girder beams up to 1,250 tonnes for the 134 metre high Sydney Harbour Bridge construction of which opened in 1932.
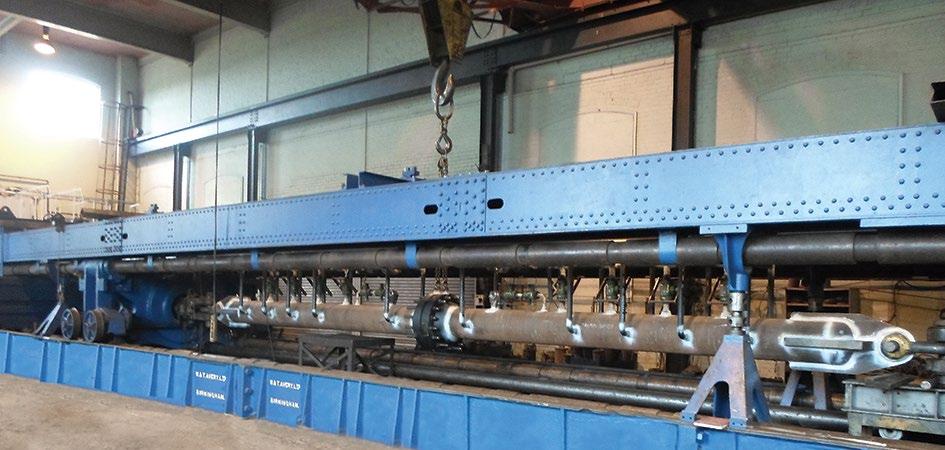
Testing
“The need for testing has never been higher, proving equipment before it is put into use is a vital requirement to prevent future failures or accidents,” said Gardiner. “Testing proves the concept and Durham Lifting always ensures it knows how the equipment is used to ensure testing simulates working conditions. We take great care and pride in our work to ensure accuracy. A ‘factor of safety’ is applied to all products manufactured inhouse, and testing the equipment as used provides a safe approach to prove calculations.”
“Having the engineering skills inhouse means we can adapt to any situation,” she said. “No day is ever the same - we may carry out a jack/hydraulic test off pulling heads on the shop floor, a mobile crane in the yard, on the 1,250 tonne Avery bed, or off an A frame. If we are site testing, we might do a bollard test, winch test, or use waterbagsthere are so many variations to what we do, and our engineering support strengthens our offering. We have an adaptable approach to all that we do, to test the new 1,600 tonne Multisec Monopile beam we had to extend the 3,000 tonne test bed to test 32 metres.”
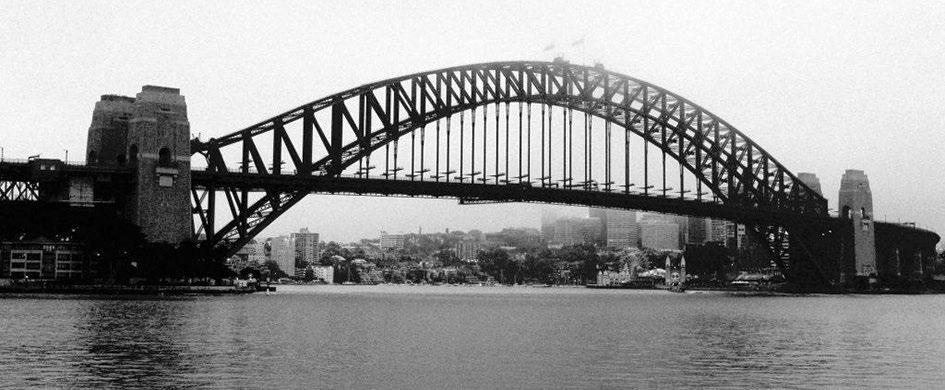
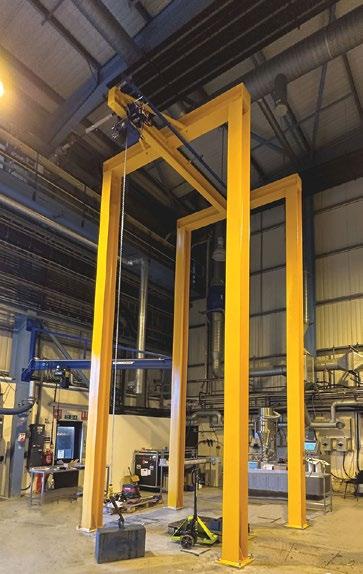
Multisec
Multisec produces a wide range of products including modular spreader beams, lifting frames and associated components. The standard beam range - available ‘off the shelf’ - ranges from the 13 tonne Multi13 to the 250 tonne Multi250. Each beam is made up of two end units and two drop links with interchangeable struts bolted in between to shorten or lengthen the beam. The Multi 250, for example, has a maximum load of 250 tonnes for a span of 16 metres reducing to 135 tonnes on a 22 metre span. All equipment is manufactured inhouse by its EN1090 accredited fabrication facility.
Multisec also designs and manufactures bespoke equipment. A recent example of this is the delivery of the 1,600 tonne capacity Monopile beam for an offshore wind project in Taiwan, its largest in terms of length and capacity. It was designed and produced in less than two months. Weighing almost 30 tonnes, the beam has 32 metre lifting centres and comprises two metre end units with drop links and a combination of three eight metre, and one four metre struts.
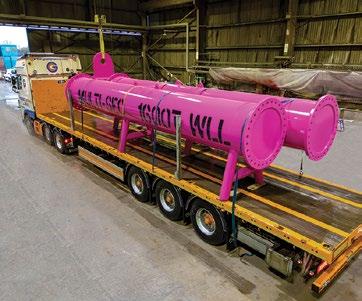
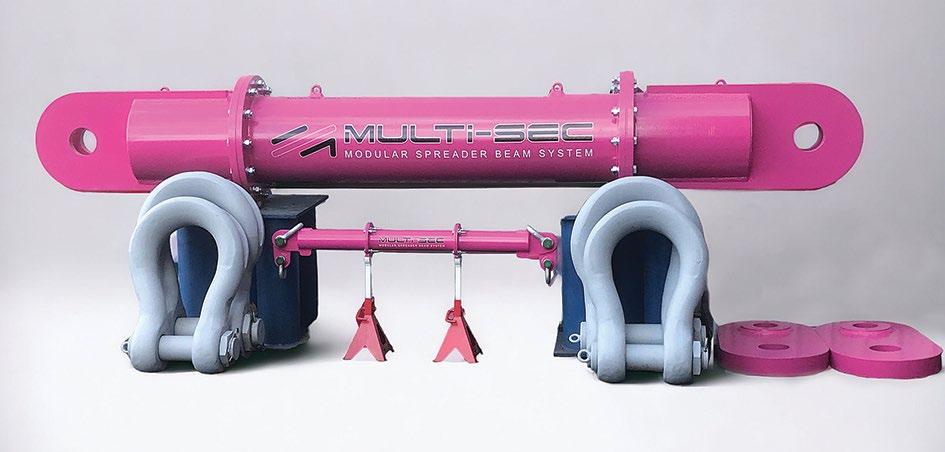
Hire
Heavy investment into Multisec spreader beams has enabled Durham Lifting to offer a large hire fleet from 10 to 800 tonnes available off the shelf, as well as Dyneema type slings, shackles and wire ropes to support the local growth in offshore wind, infrastructure, hydrogen and mining.
Expanding coverage
Over the past five years the company has adopted a strategic approach to grow the areas of the business where its strengths lie. This includes creating the Multisec brand and appointing more distributors to reach international markets.
“Last October we announced a new strategic partnership for the Multisec spreader beam products with Mercia - a partnership which will see the two businesses collaborate on crane and supply projects, working closely together to develop product ranges and create a solid base for research and development,” said Gardiner.
Durham Lifting has invested heavily into its testing capabilities meaning its facility can accommodate testing up to 3000 tonnes making it one of the largest test houses in Europe. This investment has seen not only the testing capacity grow but also the company’s fabrication offerings allowing Durham Lifting and Multisec to fabricate higher capacity beams.
“We have recently completed our journey for F4OR fit with ORE catapult and have recently been awarded this accreditation,” she said, “which is a great achievement for the team.”
The future?
“We are a family run business that has developed and grown in many sectors. We have developed a brand and are proud of the quality service we provide to our clients, old and new. The aim is to grow what we have, continue to train and develop our team and grow overseas trade.”
“Currently, we are engaged in works for the Dogger Bank wind farm project, focusing on innovative winching solutions for blade lifters. Additionally, we have embarked on exciting new projects from Norway including tests on equipment capable of handling up to 2,000 tonnes, designing lifting frames for subsea applications, creating Multisec beams and refurbishing cranes that have been dormant for 30 years. We are witnessing growth across all departments, with our team demonstrating exceptional engineering skills and work ethic. I am immensely proud of their achievements and the progress we are making.” ■
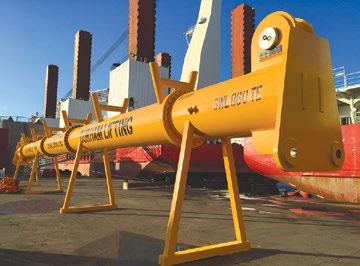
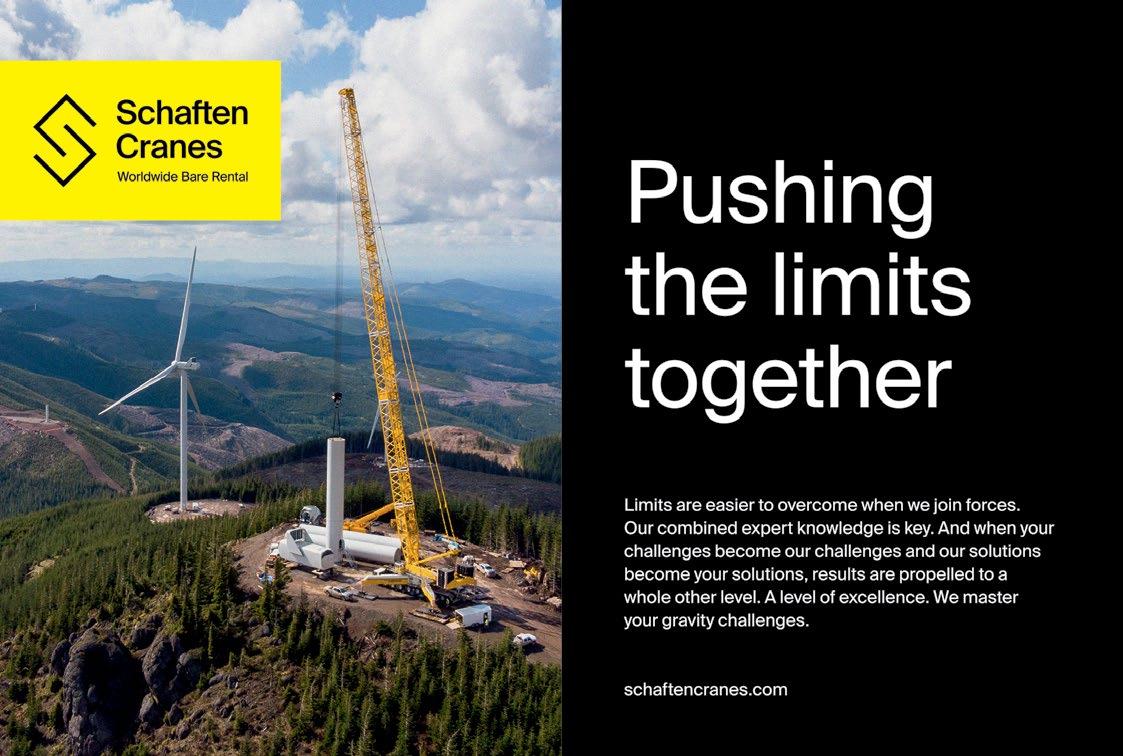