
9 minute read
Breaking barriers
Breaking barriers
With its latest crane, the 400 tonne lr 1400 SX, Liebherr’s Nenzing plant has made a significant leap in capacity. Will North spoke to Gerhard Frainer about what this new crane tells us about the strategy between the company’s two crawler crane factories.
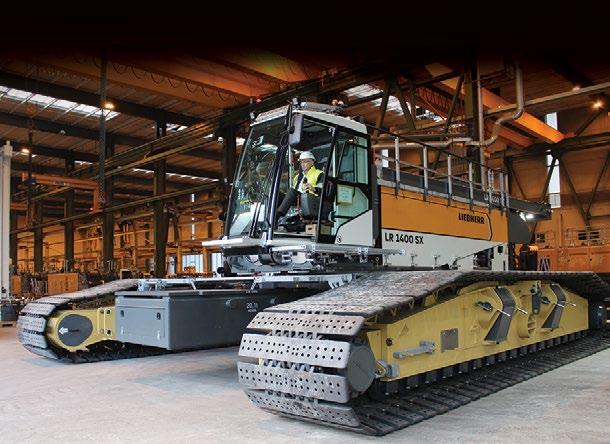
For many years, crane buyers have perceived a clear distinction between Liebherr’s crawler crane production facilities. Those under 300 tonnes were built in Nenzing, Austria, while larger cranes were manufactured in Ehingen, Germany, where the company also builds its all Terrains, rough Terrains, and telescopic crawlers. The latest launch from the Austrian plant confounds this simple view. The new LR 1400 SX has 100 tonnes more capacity than any previous Nenzing crawler crane and 50 tonnes more than Ehingen’s LR 1350. As Gerhard Frainer, managing director sales at Nenzing, said when announcing the crane: “This is a big step for our location.” So, what does this mean for the two plants? Will it mean that while Liebherr’s rival Tadano integrates its two German facilities, Liebherr will open up competition between its two factories?

At first glance, it may look as if this is the case, with Ehingen’s 350 tonner falling between Nenzing’s 300 and 400 tonne units, seemingly in competition with each other. However, this only holds true in nominal capacity terms. “In reality we have different starting points, as our cranes are used in different markets, by different clients, and for different applications,” says Frainer. Ehingen has always focused on lift cranes, while Nenzing has its roots in maritime and heavy-duty cycle cranes. The Austrian plant grew out of company founder Hans Liebherr’s 1970s decision to split maritime crane fabrication from the construction cranes built in Germany. A few years later his son, Hans Jr., purchased the assets of struggling duty cycle crane manufacturer Menck, with the first duty cycle Liebherr crane, the HS 870, launched at Bauma 1980. Duty cycle cranes feature components and booms strengthened to handle the stresses of working with tools such as vibro hammers and long term repetitive work often in arduous conditions. “We had customers using a HS duty cycle crane as a lifting crane, on construction sites,” says Frainer, “where the demand was for a less costly version for simpler lifting duties.” So Nenzing developed its LR range to meet the needs of these users, designed as multipurpose devices, able to take on a wide range of jobs cost effectively, while being easy to transport and assemble. The apparent 300 tonne line between the two plants held for a long time, as it reflected customer needs. But over the years, those requirements have changed. “It goes back maybe two Baumas ago (2016),” says Frainer. “Customers approached us and said, ‘Hey guys, it's time for a larger LR 1300. Jobs are getting bigger, loads are getting heavier, so we need a bit more lifting capacity.’”
It’s not just that individual loads, such as concrete beams and other prefabricated elements for bridges, or the tilt-up wall panels, are getting bigger. So too are the hanging leaders used to support tools like hammers, that many customers want to use with Nenzing cranes.
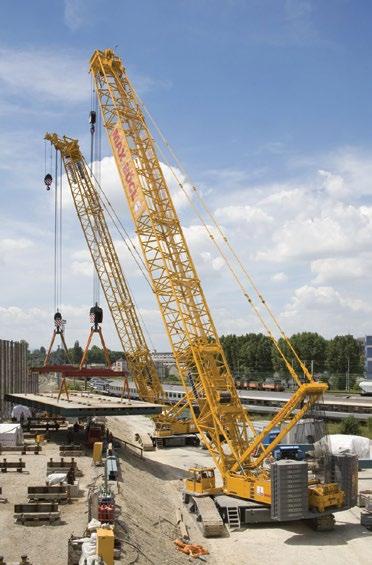
Flexible features
The LR 1300 has been a very successful machine for Nenzing, particularly in North America and as such it became the base model to build on. “That was the starting point: the same features, same functionality, with easy transportation and self-assembly,” says Frainer. Transporting a crawler can often be a challenge, particularly in a market like the US. The superstructure of the LR 1400 SX weighs just 46 tonnes, with A-frame attached. Transporting the crane with the A-frame speeds set-up once on site. Similarly, the luffing jib sections can be transported inside the main boom sections, reducing transport loads. A pure lift crane like Ehingen’s LR 1350/1 is designed for applications involving lifting up and out, on sites where space is limited. To achieve this, the crane offers 12 different configurations of boom, fixed or luffing jib, and ballast system, while cranes like the LR 1300 and LR 1400 SX are more typically used with just the main boom, and offer a more limited number of jib options.
On an engineered lift with an Ehingen machine, site preparation will be part of the project planning. Everyone involved will know that time and space must be allocated to setting the crane up. The LR 1400 SX, and LR 1300.1 SX, are designed to get to work more quickly, and work on more challenging ground conditions. The superstructure is equipped with hydraulic jacks that raise it off the transport trailer and provide a base for unloading and installing the tracks, counterweights, the two hoists and boom sections, all of which can be installed quickly, without the need for an assist crane, with the operator using a remote controller.
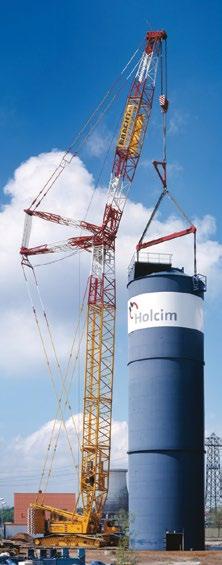
The new crane features Nenzing’s Boom Up and Down Aid, designed to prevent it from tipping, when raising or lowering the boom system, particularly when configured with a luffing jib. It considers the installed boom and jib and windspeed, and warns the operator if they are approaching the tipping point. This has been available on Nenzing cranes for several years. The LR 1400 SX adds an additional protection, the Gradient Travel Aid, which measures the crane’s centre of gravity as it travels on slopes, warning the operator should the crane come close to tipping. While cranes like Ehingen’s LR 1350/1 are expected to work from well prepared platforms, the LR 1400 SX’s designers anticipated that this would not always be the case for its multipurpose machine, which is more likely to be used on rougher, unprepared ground, or even from a barge.

Some of the risks of working on less well prepared sites can be avoided by reducing the crane’s ground bearing loads. The LR 1400 SX achieves this with another new system, ground pressure reduction plates, hydraulically adjusted metal beams, running across the front and back of the crane. They were a key attraction for one of the crane’s first customers, Mountain Crane Services, of Salt Lake City, Utah. Chief executive Paul Belcher says: “The hydraulic ground pressure reduction plates stand out in particular, with their deployment the ground pressure can be reduced by more than half.” He also appreciates the crane's real time monitoring of ground bearing pressures. “Ground conditions can vary greatly on site. Constant monitoring of ground pressure is essential for safety. This feature simplifies our work immensely.”
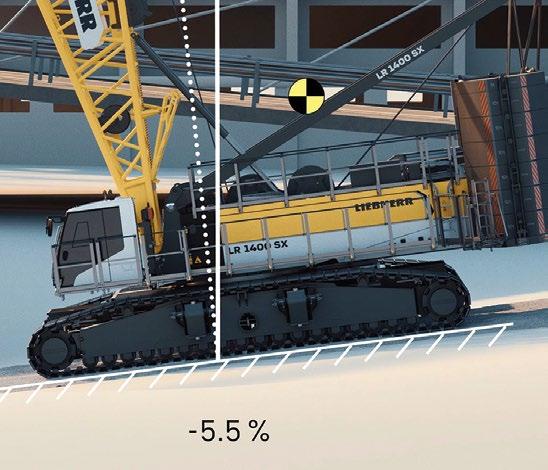
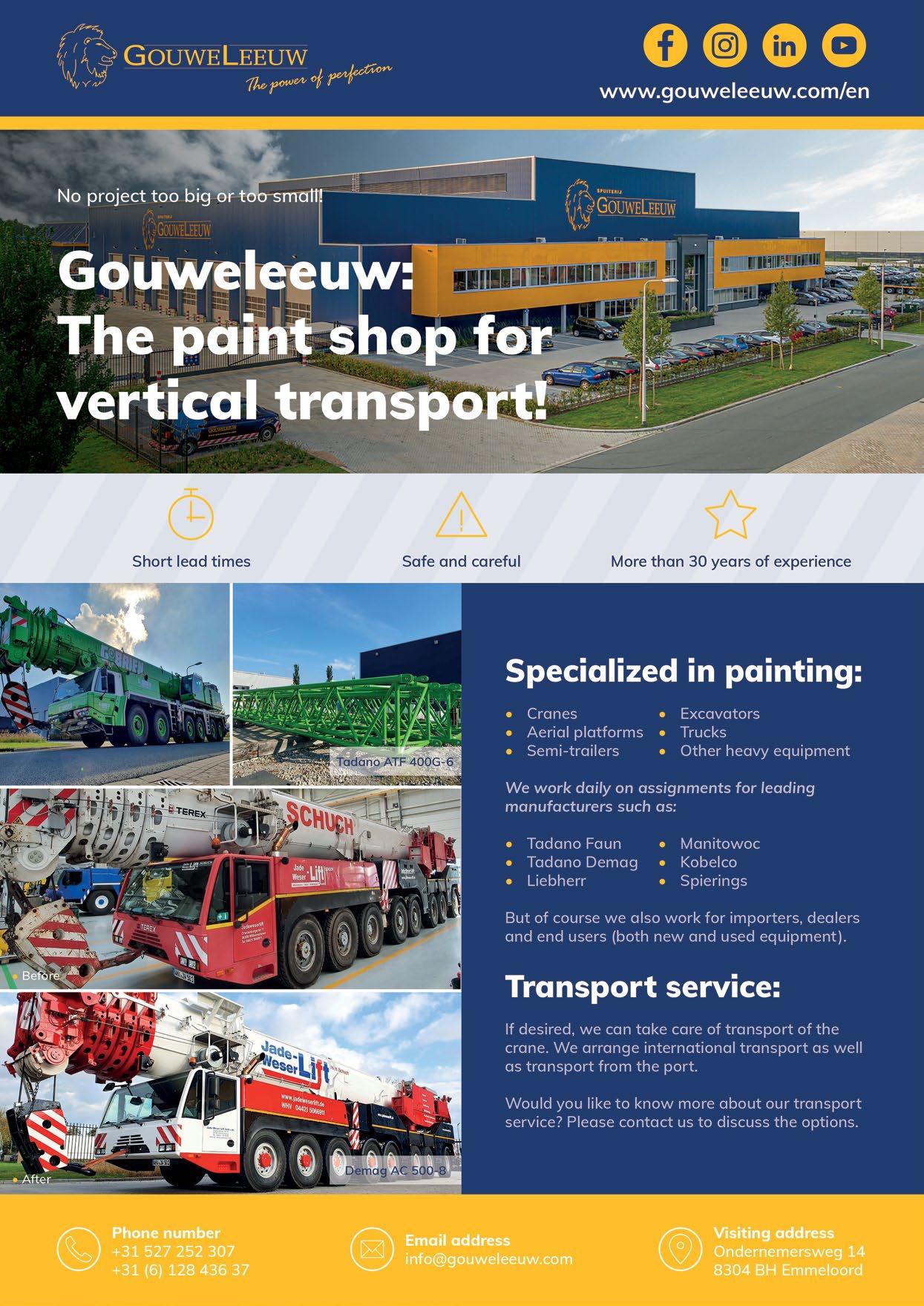
For another customer, Depenbrock, which specialises in hydraulic engineering, the fact that the crane had been designed with barge working in mind was important. Its unit, the first in Germany, will be mounted on the jack-up vessel Simone. “The barge load charts for every configuration and counterweight combination are crucial benefits for working on the water,” says Depenbrock’s Andreas Handel, head of mechanical engineering hydro construction. “The modular counterweight system is very good. If a smaller counterweight is sufficient, the unit can also be used on a correspondingly smaller barge. This makes the use of the LR 1400 SX very flexible.”
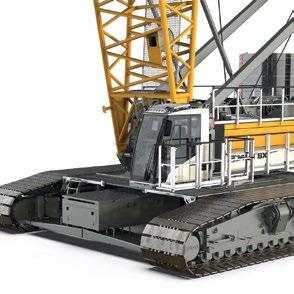
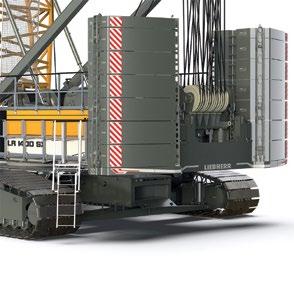
Bigger, and cleaner?
With Nenzing now offering crawler cranes over 300 tonnes, what does it mean for the future? Wolfgang Pfister, head of strategic marketing and communications at Nenzing, is clear that the apparent dividing line was never a formal part of Liebherr’s strategy but acknowledges that it was sometimes allowed to be seen this way. That won’t be the case anymore. “In the future, even different models, size wise, could be possible,” says Pfister. “We want to really have this focus on multi functionality.” As prefabricated loads and the tools continue to grow, there is no reason why two Liebherr 500 tonners might not surface, in the form of a lift crane, like the current LR 1500, and a new multipurpose crane, perhaps an LR 1500 SX? The Nenzing facility has also been responsible for the development of battery powered crawler cranes, with its Unplugged range. This includes both LB deep piling machines, and four LR cranes. Customers can now buy battery powered versions of the 130 tonne LR 1130 and 160 tonne LR 1160, as well as the original LR 1200.1 and LR 1250.1 Unplugged.
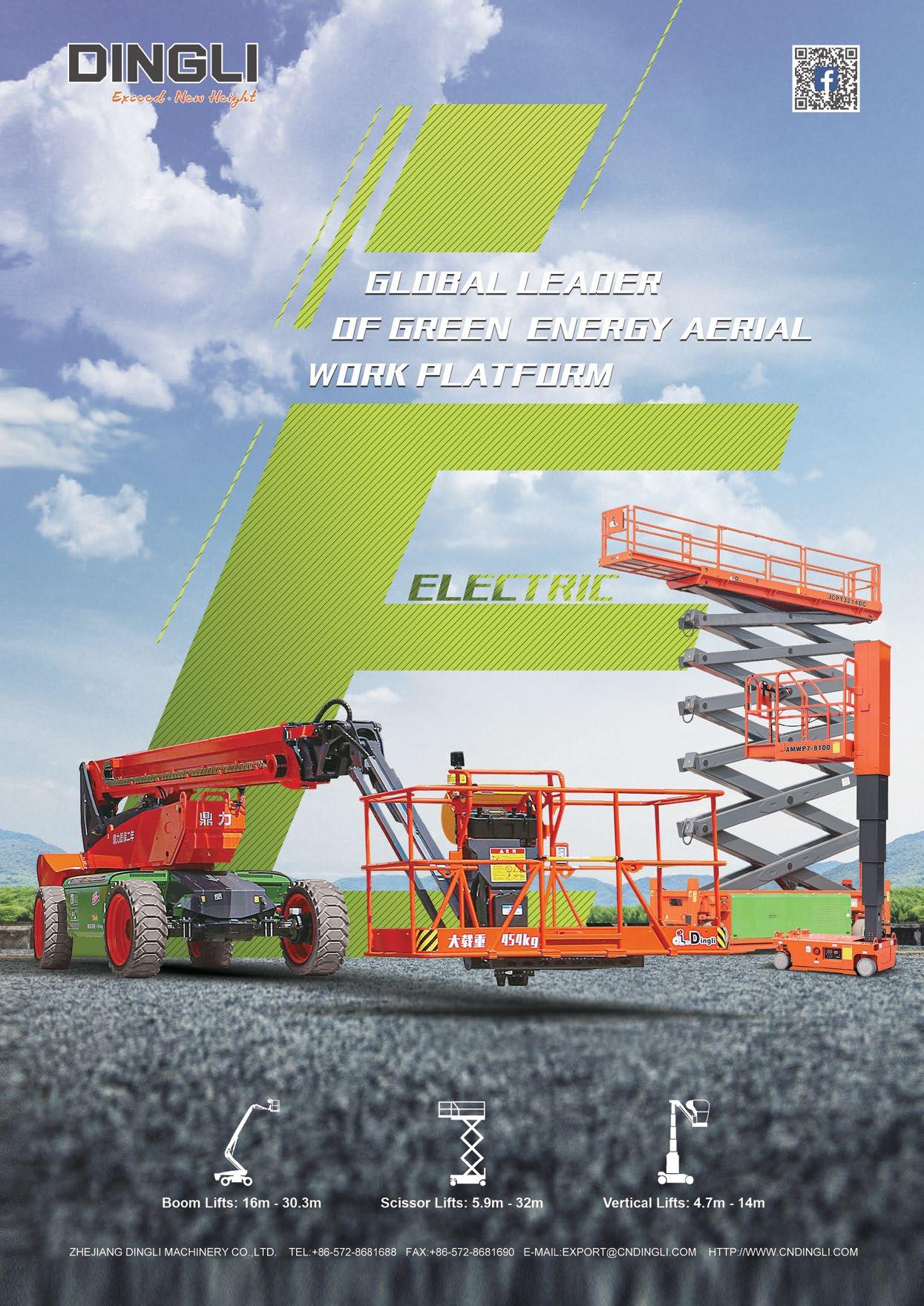
At launch, Liebherr was cautious in its claims for these cranes, stating that the aim was to have sufficient battery capacity to move around site, plugging in when the crane was in position. However, customers, are finding that they can manage a full eight hour shift before recharging. Might we see larger models? Nenzing has yet to launch an Unplugged version of the popular LR 1300.1 SX. “We have gained quite some experience now with the Unplugged machines, and this has been excellent so far on the crawler crane side,” says Frainer. “We are learning even more about how the cranes are used, how and when are they charged, and whether the battery management works the way it should, and so on. This makes it easier for us to consider larger cranes.”
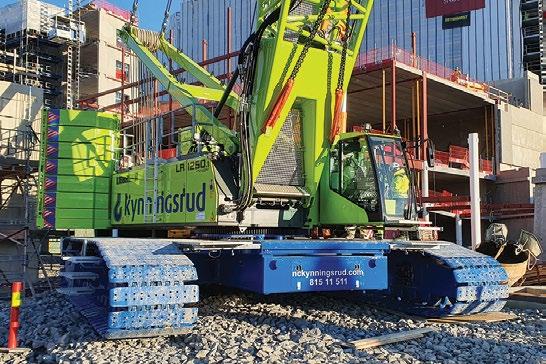