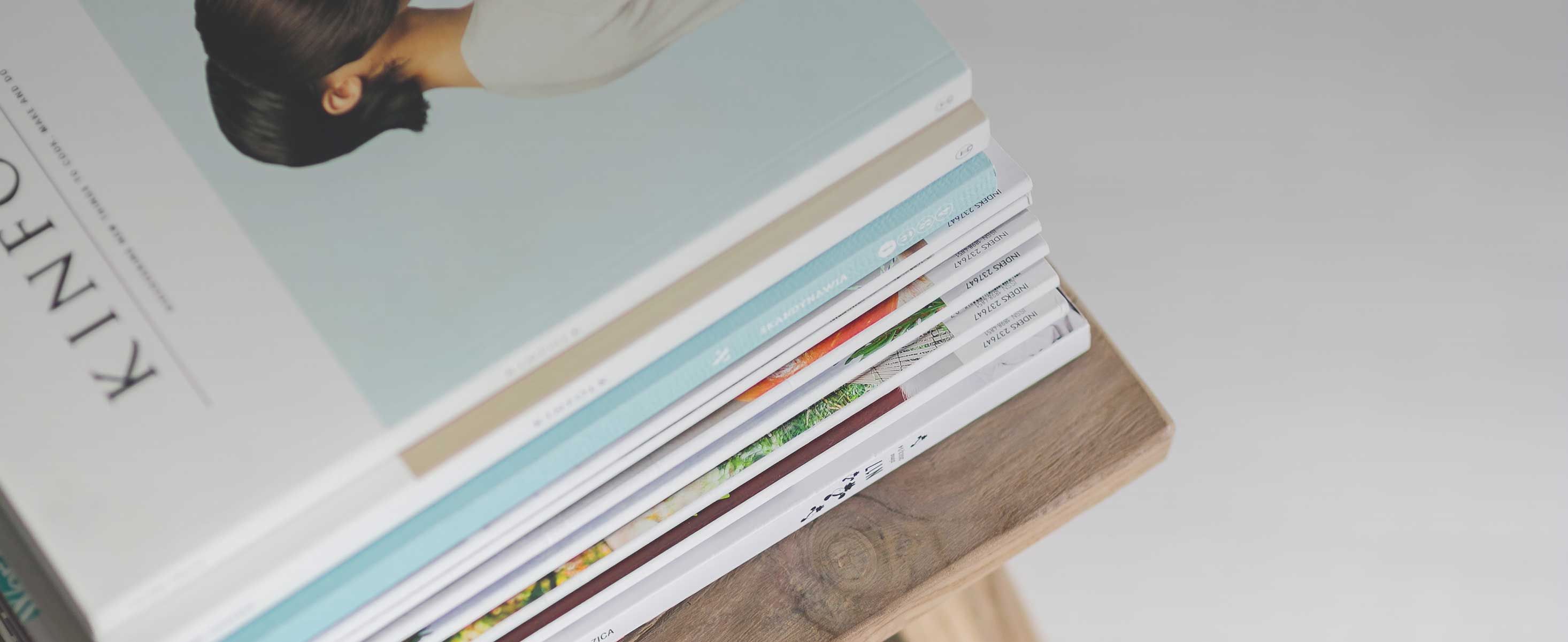
9 minute read
Make, Think, Imagine Lord Browne of Madingley Engineering The Future of Civilization
Several years ago, a friend took me to an auction of old watches in Switzerland. He told me he was keen to buy one made by Breguet; I had no idea what he was talking about, but I went with him to the pre-sale exhibition, and what I saw opened my eyes to a branch of bespoke manufacturing that I had never seen before.
Here were masterpieces of ingenuity –small worlds of gears, springs, wheels and ratchets, all in the service of telling the time. Some were so elaborate that they were called ‘grande complications’. I fell in love with the idea that such effort had gone into achieving a simple objective of measurement, which can now be achieved by an inexpensive digital watch.
Advertisement
The watchmaker Abraham-Louis Breguet was a master of the handmade and introduced a series of innovations that revolutionised the reliability and accuracy of the pocket watch during the late eighteenth century.
Napoleon bought three of Breguet’s watches and used them to coordinate his army’s actions on the battlefeld. Throughout his long career, Breguet’s quest was to perfect the pocket watch and, as a result, every one of his timepieces was unique. His most famous watch, commissioned by French queen Marie Antoinette in 1783, was so complex that it took forty-four years to c omplete and left Breguet’s workshop only after both queen and watchmaker were dead. When it was fnally fnished, the Breguet No.
160 was a masterpiece of mechanical complexity. It kept track of the date (including the ability to accommodate leap years), chimed the hour, had a power reserve indicator, a stopwatch and even incorporated a thermometer.
Breguet’s approach to making was the antithesis of his contemporary, the French engineer Honoré Blanc. In November 1790, Blanc put on a dramatic demonstration for a group of politicians and generals. By selecting components, apparently at random, from bins arranged in front of him, he quickly assembled several working muskets. .
France was in the throes of bloody revolution; it had an urgent need for affordable and reliable weapons. So the crux of Blanc’s sales pitch was clear; it did not take a highly skilled craftsman to build a musket – if the gun parts were designed by an engineer and machined to meet pre-specifed criteria, they could be assembled by almost anyone.
Blanc’s approach delivered guns that were not only cheaper than the competition, but also far more reliable. By the time he died in 1801, his factory at Roanne in central France was turning out more than ten thousand identical muskets a year for Napoleon’s armies. This was a new way to manufacture that demonstrated the effciency gained by using interchangeable parts to make exact copies.
Blanc’s mass production of guns and Breguet’s bespoke crafting of pocket watches were very different ways of making things, but both would change our world profoundly. Breguet’s watches paved the way to the accurate timekeeping that rely on to run our lives and our economies, and Blanc’s gun-assembly technique pointed the way to modern mass production, which has been the engine of global economic progress for the last two centuries. In both developed and developing countries, manufacturing contributes disproportionately to exports, investment in innovation and productivity growth.
Mass Customisation: Effcient, Personalised and On-Demand
In the eighteenth century Blanc, the mass-producer, and Breguet, the master craftsman occupied opposite ends of the manufacturing spectrum. Had they been alive today, their work would have been much more closely aligned.
To make his bespoke watches, Breguet had to make many of the components by hand. Today, makers have access to huge catalogues of standardised parts, an idea pioneered by the industrial manufacturer Blanc.
I saw the power of this approach when I visited Surrey Satellite Technology. Its CEO, Martin Sweeting, explains that ‘the frst four decades of the space era were dominated by a few superpowers who alone possessed the knowledge and budgets to undertake the enormous technical and programmatic challenges posed.’ That has changed dramatically during this century. Sweeting shows me a range of micro-satellites under construction.
These have altered the economics of space profoundly; the key to reducing costs has been the enormous advances in the manufacture of microelectronics.
Most of these small satellites are made from off-the-shelf components that are also used in consumer electronic devices. Some of them use a smartphone to navigate and take images of Earth. ‘Space is now within the reach of small companies, universities and even high schools,’ says Sweeting. The falling cost and improving capabilities of constellations of small satellites will stimulate new applications in communications, Earth observation and more.
The makers of small satellites solved the challenge of integrating and adapting existing technologies to create new and powerful capabilities, bridging the difference between the bespoke and the mass-produced.
Nanotechnology and synthetic biology promise to bridge this same gap by, for example, creating materials and cells that can self-heal and adapt themselves to changing environments. These technologies are moving forward in parallel with great advances in 3D printing, robotics, artifcial intelligence and other forms of automation. Together, these different of engineering herald a revolution in the way we make and consume.
The team of young makers in a London start-up called Unmade provide a glimpse of the possibilities created by the new world of mass-customisation. In a studio beneath London’s Somerset House, Ben AlunJones points to one of the grey automatic knitting machines that is controlled by his company’s software. It is the length of a small automobile, with spools of brightly coloured yarn lined up along the top. ‘That one probably has 30,000 moving parts. It’s far more complex than any 3D printer,’ says Alun-Jones. He describes how the machine is entirely computer-controlled, although the proprietary software that comes with it is frustratingly infexible.
Alun-Jones and his co-founders have set about adjusting the machine’s code to develop new capabilities. Some of the results are displayed on a nearby rack that holds an eclectic mix of colourful knitted sweaters.
One bears a four-colour portrait of Ernest Hemingway, while another disturbs the neat blue stripes of a classic Breton sweater with a chaotic series of swirls and vortices.
Unmade’s new code gives customers a role in the design of their clothes and, at almost no cost to effciency, every garment made by the machines that are controlled by the company’s software is unique. ‘You could do what we’re doing by manually programming each one. We do it on an automatic industrial scale now,’ says Alun-Jones, who hopes that this new approach will soon expand to tailoring. ‘Fit is much harder than what we’re doing at the minute… But it’s on our road map. When we solve that, it will be a big deal.’
Alun-Jones is also committed to helping to reduce the extraordinary waste created by today’s fashion industry. ‘It’s a $2.4 trillion industry and there is $250 billion a year in wasted stock,’ he explains incredulously.
The mass-customisation processes pioneered by organisations such as Unmade parallel those recently established by car manufacturers like Mercedes-Benz, which now allow customers to specify one of up to a million combinations of customisable options.
These advances show us that manufacturing will increasingly shift to an ‘on-demand’ process, which can supply products that are tailored to individual requirements and made only when they are required, in a way that minimises waste and maximises effciency.
Speaking to many engineers and business leaders who are pioneering these developments, they were all at pains to emphasise that total automation of manufacturing processes is not a desirable or a realistic ambition. Rather, they emphasised the immense potential of human makers working in collaboration with the very best tools from robotics, artifcial intelligence and other branches of automation. Clearly, we are not on the verge of massive technological unemployment, a fact refected by today’s high employment rates in Britain, the US.
Physical Things in a Digital World
In 2011 the web pioneer Marc Andreessen announced that ‘software is eating the world’. His argument was that every part of our lives and every corner of our economies is being reduced to bits and bytes, which are then manipulated by computer algorithms.
The implication was that the physical world, populated by the tangible objects that we make, build and exchange, will gradually recede in importance. While it is true that inventions such as the smartphone collapse multiple functions into a single form (nobody need carry a separate camera, diary, typewriter, pocket radio and book with them these days), these positive trends towards ‘dematerialisation’ and ‘digitisation’ can only go so far.
As John Hennessy, Turing Prize winner and Chairman of Alphabet, puts it, ‘If we’re really going to invent a better world … there’s got to be more than just digitisation.’ We cannot eat software and nor will it heal us, clothe us or provide us with shelter. Just as we will rely on the ingenuity and fexibility of a human workforce, we will still need such basic things as steel pipes and optical fbres, as well as the more complex technological devices that support all our digital tools.
Tony Fadell, one of the principal inventors of the iPod and the iPhone is adamant that innovation in hardware still represents the way forward. ‘Software can only eat the world after a hardware disruption has been created. If the hardware wasn’t there, none of the software would have been created.’ And in his view, getting the devices right so they can unshackle new potential is critically important, and often much more challenging than software engineering.
‘It takes a radical way of thinking about the entire system to create the explosion of new opportunities, new businesses, new industries and new verticals that can be created [after a transformative new device or platform is invented].’ The successful launch of constellations of GPS satellites is a clear illustration of this point – only after the physical satellites were in orbit and fully operational could the crucial applications upon which we all now depend be born. The European Space Agency’s Paul Verhoef echoed Fadell’s central message when he said that, as hardware innovators, ‘we need to look ahead, often a lot further ahead than where the IT folks are looking’.
Many of the biggest challenges facing humankind can only be tackled by making physical objects and systems. The crucial goal of reducing carbon dioxide emissions in order to tackle climate change demands that we innovate and deploy new energy sources and distribution networks. Relieving energy poverty and securing supplies of water, food, sanitation and other basic necessities in the developing world requires physical engineering. As health care improves and populations get older, we will need better and more affordable medical devices that we can deploy ubiquitously. And, as cities grow, we must make physical infrastructure and transport systems that maintain cities as functional and pleasant places to live. Digital tools can certainly help us make solutions in more inventive and effcient ways, but they cannot confront these problems alone.
The engineering of physical objects at higher and higher effciencies is, however, the primary means through which the fruits of progress can be shared most widely. 3D printing and related fabrication techniques will take this to a new level, allowing for more on-demand, localised and customised manufacturing, with less wastage of material and energy.
Despite repeated claims that software will ‘eat the world’, it is of no value without hardware to run on. The relatively slow pace of hardware development will always limit the rate of change in manufacturing and technological advance more generally; often this is a good thing, since it gives us time to adapt, to design effective regulation and to re-train and re-educate workers so they can get best out of new tools. In the years to come, manufacturing will increasingly be changed by robotics, data analytics, connected sensors, synthetic biology and nanotechnology, but society will use these new tools to continue the decades-long trend of reducing average working hours.
If our basic needs can be met with less effort, we will be able to invest more energy in improving the world around us.
The human urge to make is at the heart of all progress; it is implicit in every new work of art, every attempt at DIY and every patch that is coded for a piece of open-source software. It is a universal activity and the products of engineering allow us all to tinker, refne and choose how we want to make our lives better and more enjoyable.
At the most fundamental level, making things is at the root of all of progress.
As the late Calestous Juma, Professor of the Practice of International Development at Harvard University, put it to me so clearly, ‘Society advances because we make things. It’s just so obvious.’
This is a modifed extract from John Browne’s new book Make, Think, Imagine: Engineering the Future of Civilisation, published by Bloomsbury, £25 hardback.