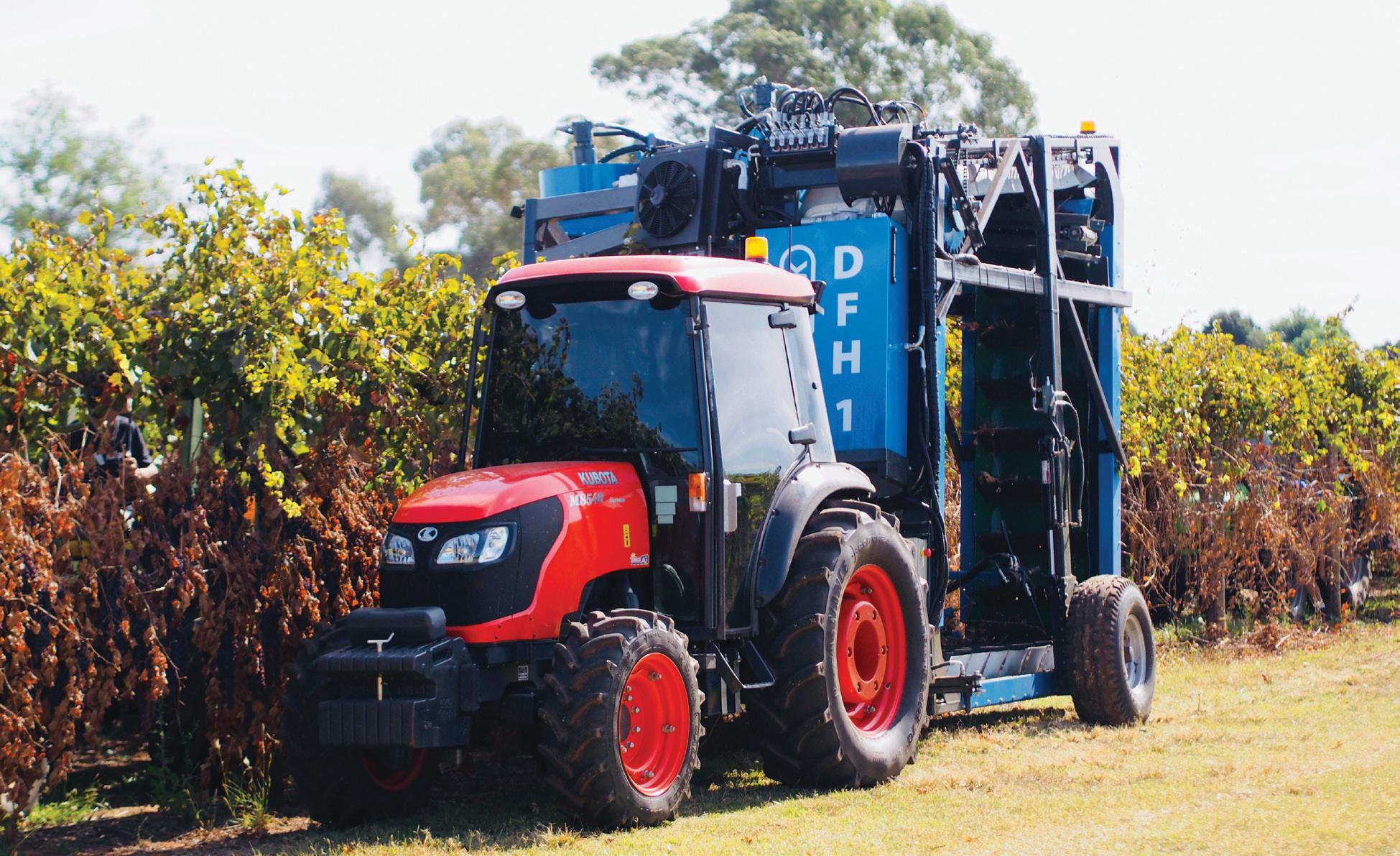
5 minute read
Project yields investment
New Harvesters Shake Up Industry
What does the dried grape industry do when faced with a challenge? Rises to it.
Season 2022 was no-doubt a difficult one. Wet conditions meant limited windows to remove fruit, leaving many growers producing poorer quality fruit that cost more to dry and offered lower returns.
At the heart of the issue – with one of the industry’s key harvest contractors taking a step back – was a lack of available harvest machinery.
The industry and its growers wasted no time in coming up with a solution to this bottleneck.
Innovation Committee’s first task
Chaired by Ashley Johnstone, the Dried Fruits Australia Innovation Committee – then an informal group of growers chatting about the needs of the industry – met after last year’s harvest.
“We wanted to look at a few mechanical ideas, improvements, not anything extravagant – just a few little gadgets to get the ball rolling. That was the initial intention of the group,” Ashley said.
“After the 2022 season, it was clear there simply wasn’t enough harvesting equipment to pick swingarm trellis.” There was discussion around resurrecting and upgrading old machines, but Ashley said his view was that the industry needed new equipment for safety, and to maximise efficiency and productivity.
“We had to look at what was the best dried fruit harvester around, and around the year 2000, about eight radial head Shaw harvesters were built. They were built by Mildura Irrigation Repairs Mick Stanbrook using Ivan Shaw’s design,” he said.
“In about 2009 – Tim – my brother built the harvester that I have now, which is a copy of those harvesters, with a few modifications. That harvester of mine was the one to be copied going forward (with this project).”
With funds from the Dried Grape Trust, the Innovation Committee employed a draftsman to get the ball rolling.
Ashley said fellow grower and Innovation Committee member Rod Trigg played a pivotal role in seeking out the draftsman, and also putting the team in contact with Mildura-based manufacturer Interlink Sprayers.
From design to reality
Two growers, Rob Kennedy and Ash Chabrel, were the first to make a commitment to order a machine and Interlink got to work.
“You need to have the best equipment and that equipment needs to be working hard to pay for itself. If you’ve got old and unreliable equipment, then don’t expect good performance,” Ashley said.
“These are the solutions that we needed for our industry, rather than patching up old dinosaurs. “They’re ancient and they’re not the future of the industry – the future is new equipment.
Interlink Sprayers managing director and head of design Matt McWilliams said the first two machines were built as a research and development project for Interlink – with little profit margin – to get some runs on the board.
“We made it more automated and easier to adjust speeds – that can all be done from the cab,” he said.
“We’ve gone to an LED screen that shows the harvester operating and shows (the driver) which part of the harvester they’re adjusting.
“It’s similar to a new car, I suppose – there’s some really flash technology on it.”
Manufactured in the heart of the growing region
For the Innovation Committee, with
Mildura the centre of Australia’s dried grape production region, to have the equipment made locally made sense.
Matt worked closely with growers and said it was important to develop the machine for the specialised task of harvesting dried grapes on the Shaw swingarm trellis.
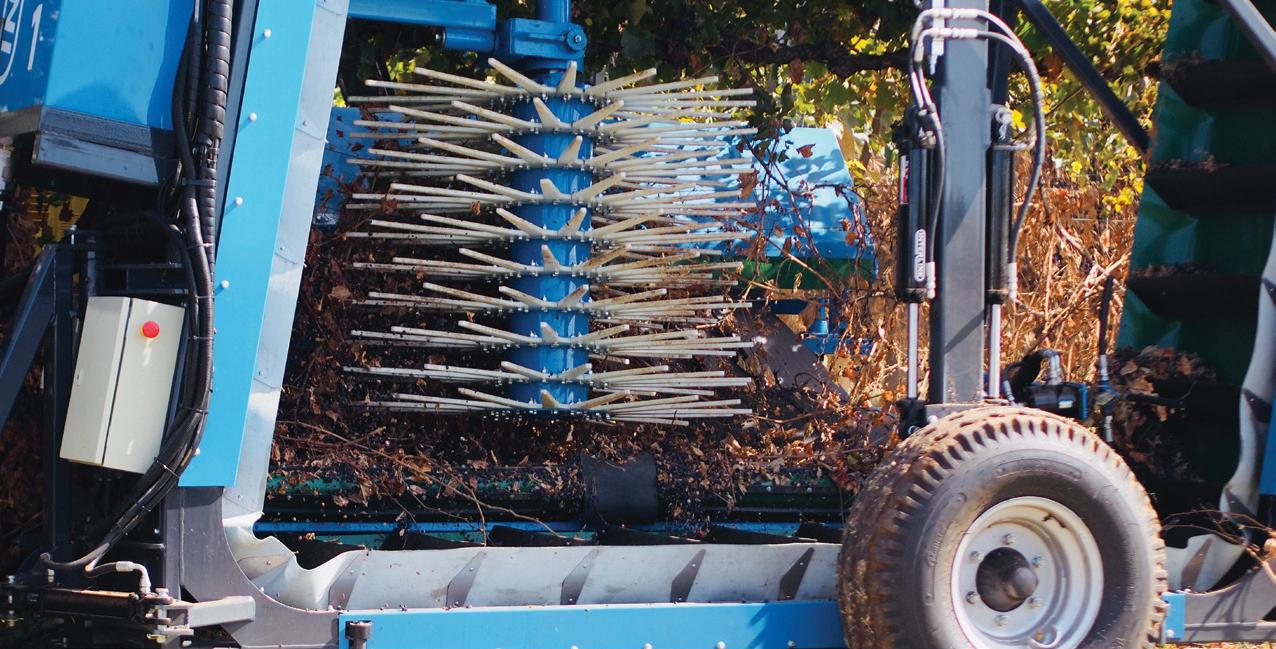
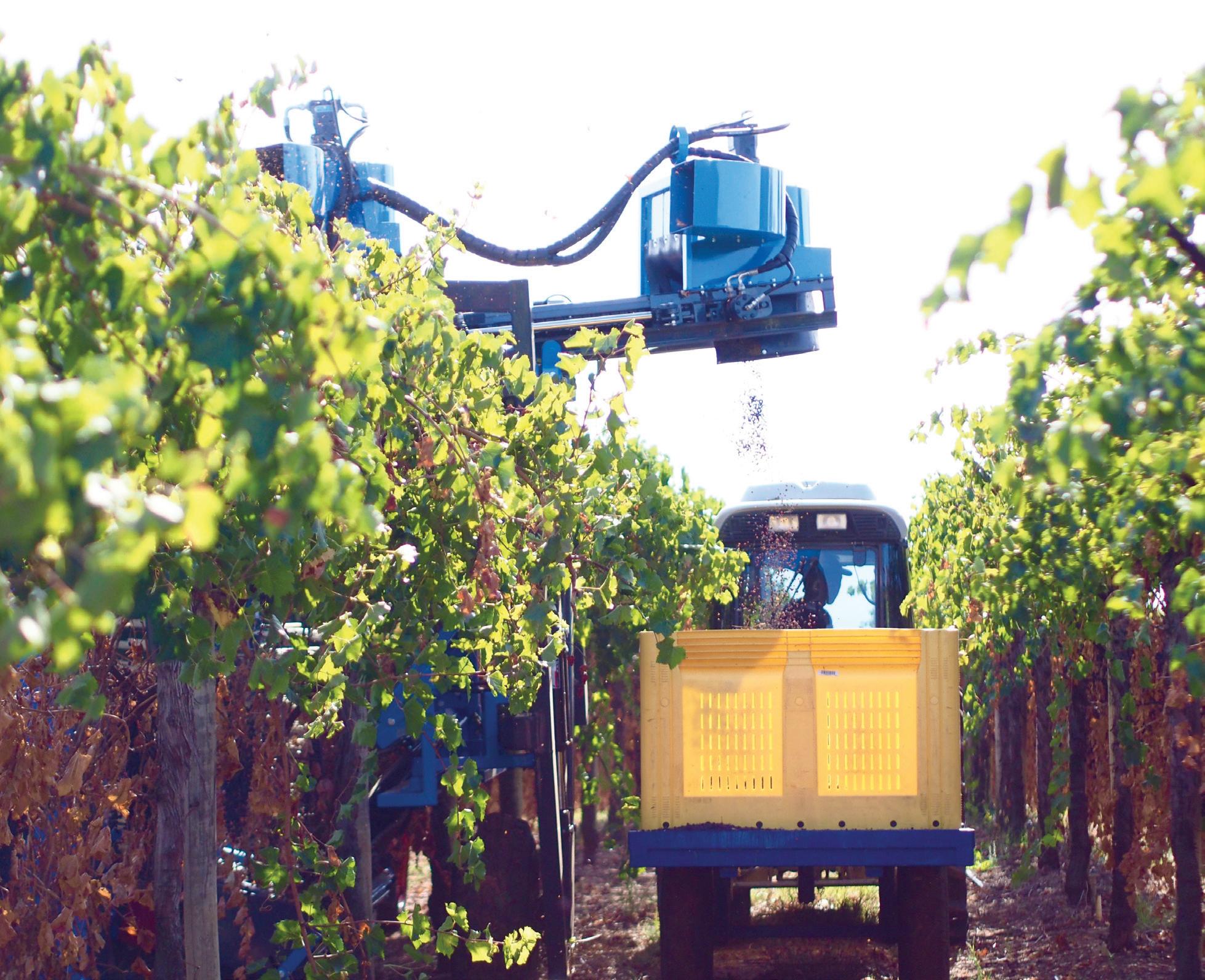
“It’s one of those things that anyone out of the industry probably doesn’t appreciate – it really is quite specialised,” he said.
“It was a massive feat.”
All of the manufacture was done in-house, from engineering to spray painting.
While the first two harvesters are already hard at work, Matt anticipates another eight will be in the field by harvest next year.
“I’m grateful we took it on,” he said.
“It’s one of the few machines where we start it up in the factory and we’ve got 20 people standing around and watching this thing go, mighty proud of themselves, saying ‘we did it’.”
Control back in growers’ hands
Rob Kennedy’s new harvester was delivered just before harvest began and has already been put to the test on 30 acres of Sunmuscats, currants and Sunglo.
While he said he was fortunate to have harvested all his fruit last season, this year – without a contractor to do the job – he was left few options other than to buy his own machine.
“There was no one to contract pick, so that left us wondering what we were going to do and the solution was to buy our own machine,” he said.
Investing in the new harvester put some of the control back in his hands.
“With rain coming, without access to a machine, you’d be in a line (for a contract harvester) and you might not get your fruit off,” he said.
“Generally the contractor was pretty good, they’d try to get to you if they could, but as soon as there’s rain coming everyone wants him.
“That’s the best thing about it. We can pick when we need to pick, and not wait until a machine is available.”
Strengthening the industry
Ashley said the investment growers were making in their own businesses would help the wider industry persist.
“We needed more of these machines floating around the industry if it’s going to persist,” he said.
“If you don’t have harvesting capacity for this trellis system, then growers will either get out of dried fruit all together or they might alter their trellising system so that more narrow harvesters can harvest their crop, and then you lose all the other advantages of swingarm.”
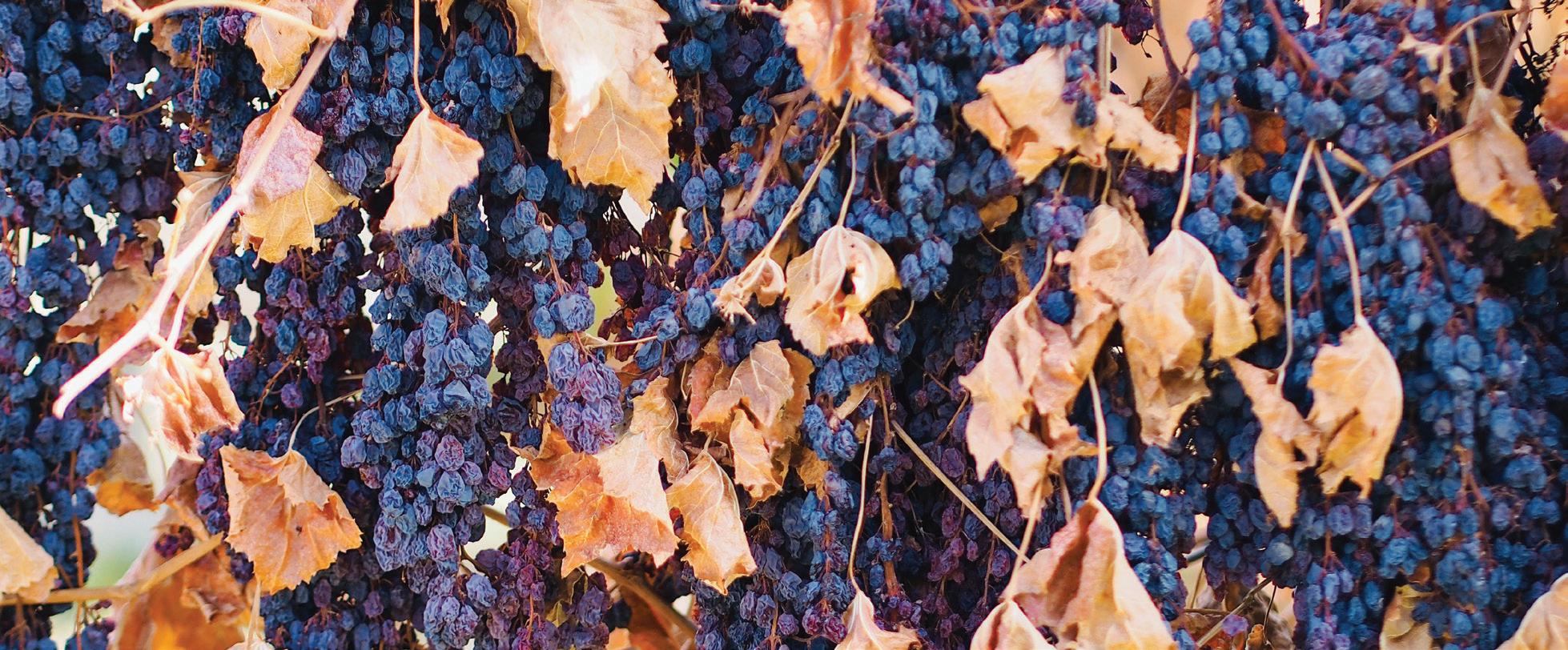
Ashley said the Shaw swingarm trellis was industry best practice, and was one that allowed the production system to be continually refined and mechanised.
“We don’t want to lose that because we don’t have enough harvesters for that system,” he said.
It was a sentiment shared by Dried Fruits Australia’s field officer Stephen Kelly.
“These harvesters have been ordered by not only smaller growers who have a long history in the industry, but also by newer corporate producers,” he said.
“This means, particularly in tough seasons like last season, fruit can be taken off at the optimal time. This will mean higher grades of fruit will be delivered, increasing grower returns.”
DFA CEO Thomas Cheung said small but extremely successful projects led by the Innovation Committee show the decision to wind up old branches and streamline resources into industry initiatives was a wise move.
“There will be more projects to come from the committee, so stay tuned," he said.
Next step for Innovation Committee
Once the dust settles on season 2023, Ashley said the Innovation Committee would meet again to decide on its next priority.
The next stage of mechanised winter pruning, new varieties and sustainability are among the issues the committee is keen to focus on.
“There are so many other things in the pipeline that this committee’s looking at,” he said.
“We’re really trying to absolutely nail the production system and get it to be super efficient, and having good quality equipment is critical to having an efficient production system.”v Growers who want access to the drawings for the dried grape harvester can contact the Dried Fruits Australia office by emailing Stephen at projects@driedfruitsaustralia.org.au
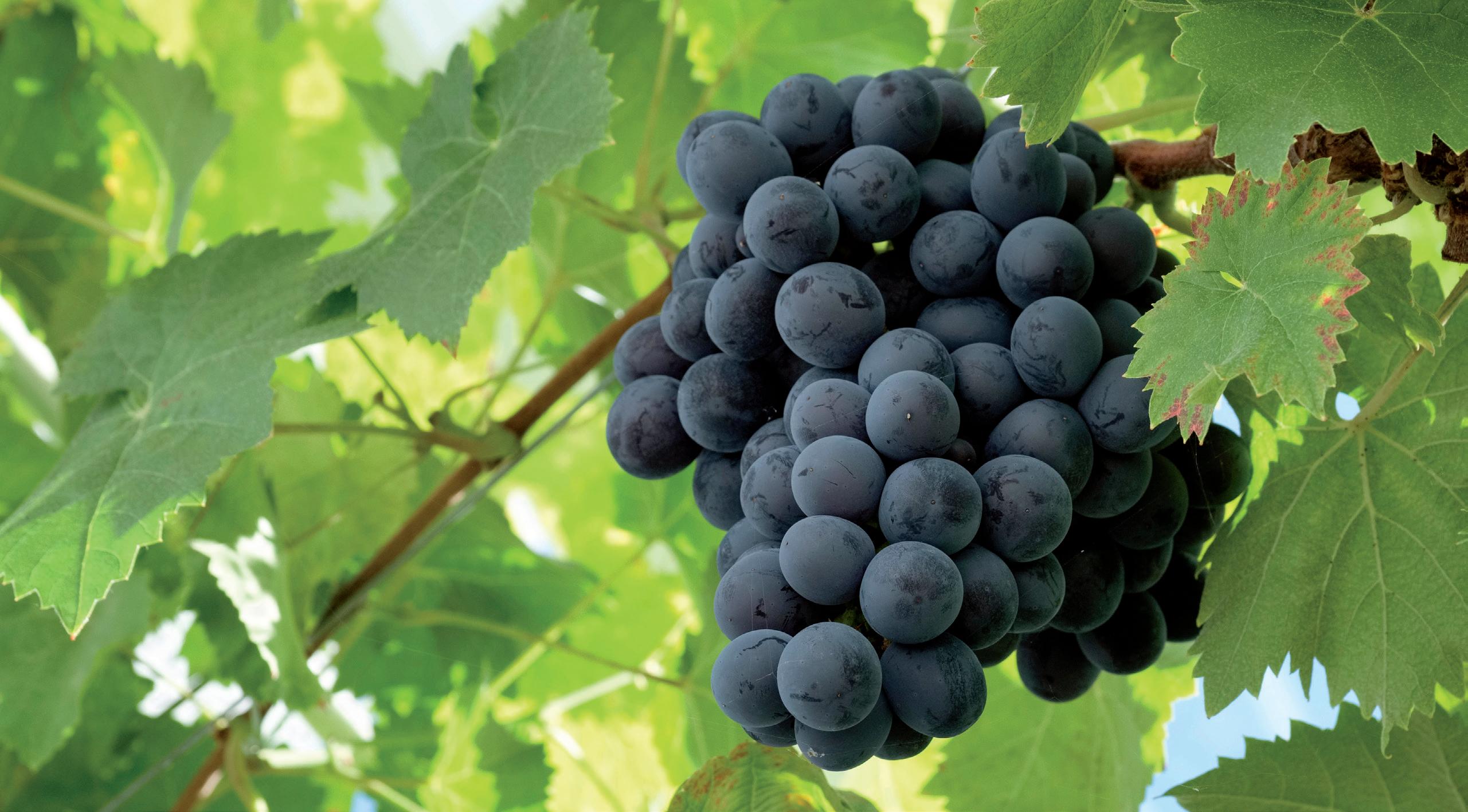