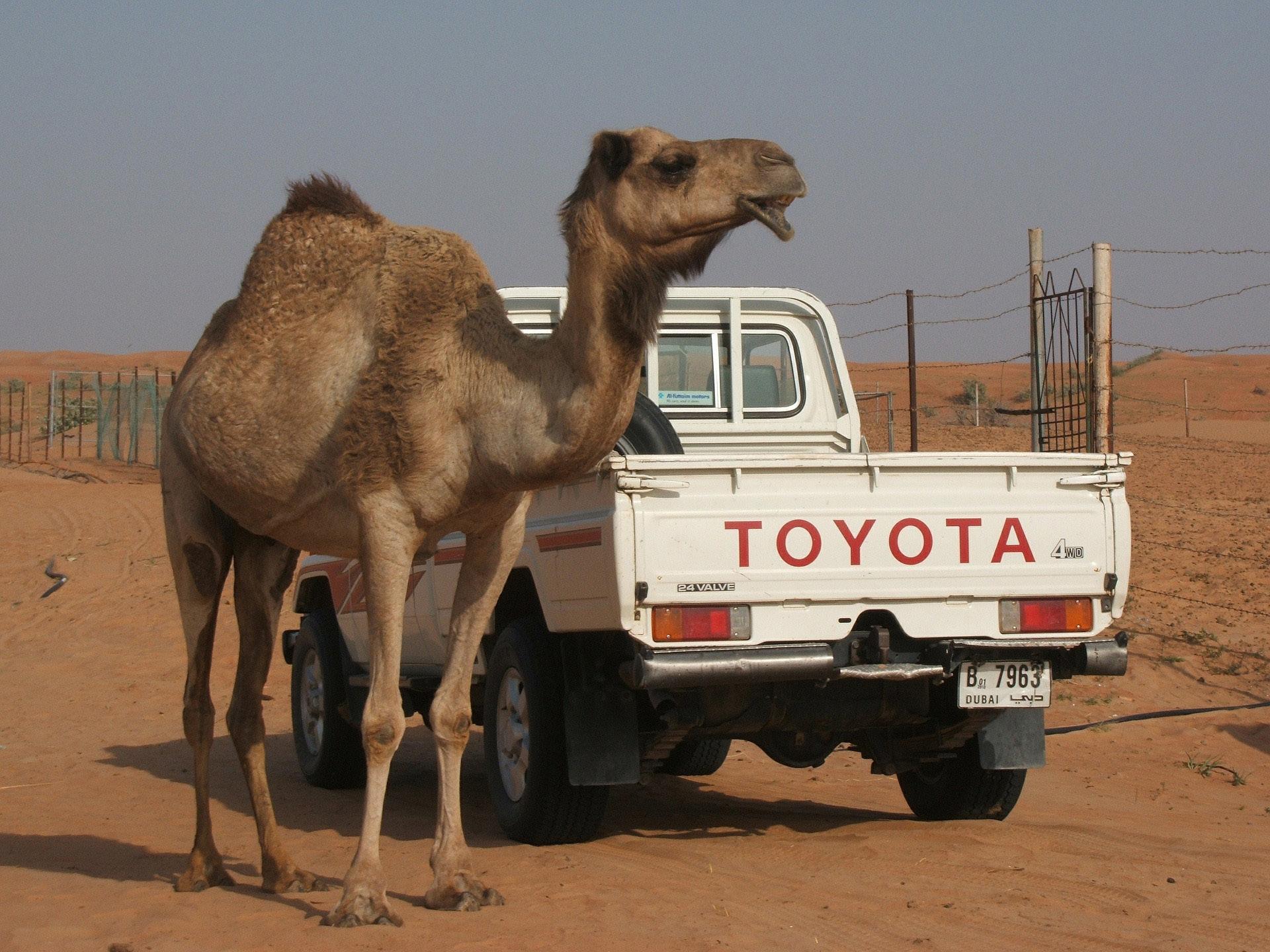
2 minute read
Toyota
from BYZMAG podzim 2020
by BYZMAG
Toyota
Na počátku všeho byla 2. světová válka, která doširoka rozevřela nůžky mezi americkým a japonským automobilovým průmyslem. Zatímco Henry Ford rozjížděl v USA vůbec první linkovou výrobu na světě a chrlil denně desítky aut, Toyota stála na pokraji bankrotu. I přesto zazněl z úst tehdejšího prezidenta společnosti Toyoty jasný rozkaz: „dohnat Ameriku do 3 let jinak japonský automobilový průmysl nepřežije.“ Tento výrok navždy změnil nejen Toyotu, ale veškerý světový průmysl.
Advertisement
Válkou sužované Japonsko nemělo po druhé světové válce příliš sil ani peněz pro podporu soukromého sektoru. I přesto se však v Toyotě nechtěli vzdát snu o velké prosperující firmě. Když se v den, kdy skončila druhá světová válka, postavil před zaměstnance prezident Toyoty, Toyoda Kiichiro, s výzvou „dohnat Ameriku za 3 roky“, jen málokdo věřil, že lze společnost Toyota zachránit, natož konkurovat americké velkovýrobě. Ve stejnou chvíli se však k podniku připojil Taiichi Ohno, mladý a velmi dravý strojní inženýr. Zachránit firmu bez možnosti investic do lepších technologií, to byla skutečná výzva.
Produktivita? Jedině bez plýtvání
Na rozdíl od Fordu vyráběla poválečná Toyota rozmanité portfolio automobilů s různou úrovní výbavy. Firma kvůli tomu bojovala se špatnou pružností výrobních linek, nízkou produktivitou, vysokými zásobami různých dílů a velkým množstvím chyb. Taiichi Ohno si uvědomoval, že z tohoto kruhu jej vyvede jen jedna cesta – identifikovat a eliminovat veškeré plýtvání, což umožní soustředit se na činnosti, které produktu přidávají hodnotu. Sestavil si seznam 7 druhů plýtvání, který byl základem nově vznikajícího TPS (Toyota Production System).
Kdo chyby nedělá, nic nezkazí
Revoluční byl také přístup k chybám ve výrobě. Namísto zlepšování kontrolních procesů se pracovníci Toyoty začali zaměřovat na prevenci vzniku chyb. Důvod byl snadný – chyby a jejich následné odhalování zkrátka stojí peníze. Pokud ale úplně zamezíte jejich vzniku, ušetříte materiál, čas, výrobní kapacity i náklady na kontrolu. Ani zde ale nebyl prostor pro drahá technická řešení. Předcházení chyb proto spočívalo v jednoduchých opatřeních, které většinou mechanicky bránily vzniku chyby (tzv. poka yoke) a vyrovnané pracovní zátěži pracovníků i strojů. Důležitost vyrovnané pracovní zátěži výroby vysvětloval Taiichi Ohno na příkladu zajíce a želvy: „Pomalejší, ale vytrvalá želva způsobí méně ztrát, než zajíc, který rychle běží vpřed, sem tam se zastaví nebo si zdřímne.“
Už během prvních několika let došlo k poklesu chybovosti ve výrobě o neuvěřitelných 50 % a firma dál pokračovala ve zlepšování kvality, tentokrát už si mohla dovolit i malé investice. Jedním z nejznámějších opatření bylo zavedení andon systému, kdy měl každý zaměstnanec možnost stiskem červeného tlačítka okamžitě zastavit celou výrobu, pokud zpozoroval chybu nebo odchylku od standardu. Drahé, ale funkční řešení vyšvihlo Toyotu mezi automobilovou elitu a svůj vysoký standard v kvalitě si stále drží – je dodnes považována za automobilku s nejvyšší kvalitou vozů.
Ford kopíruje Toyotu?
Díky novému pohledu na výrobu se firma postavila na nohy – zbavila se zbytečných procesů a zásob, které brzdily firmě kapitál, zvýšila produktivitu, flexibilitu a snížila chybovost ve výrobě. Postupně přidávala do svého TPS další a další nástroje, které dříve či později okopírovaly všechny další automobilové společnosti. Toyota se díky svému procesnímu systému proslavila po celém světě a zaslouženě se jí připisuje vznik celé metodiky, kterou dnes nazýváme lean.
Text: Kristýna Váchová
Foto: Oliver Fischer z Pixabay