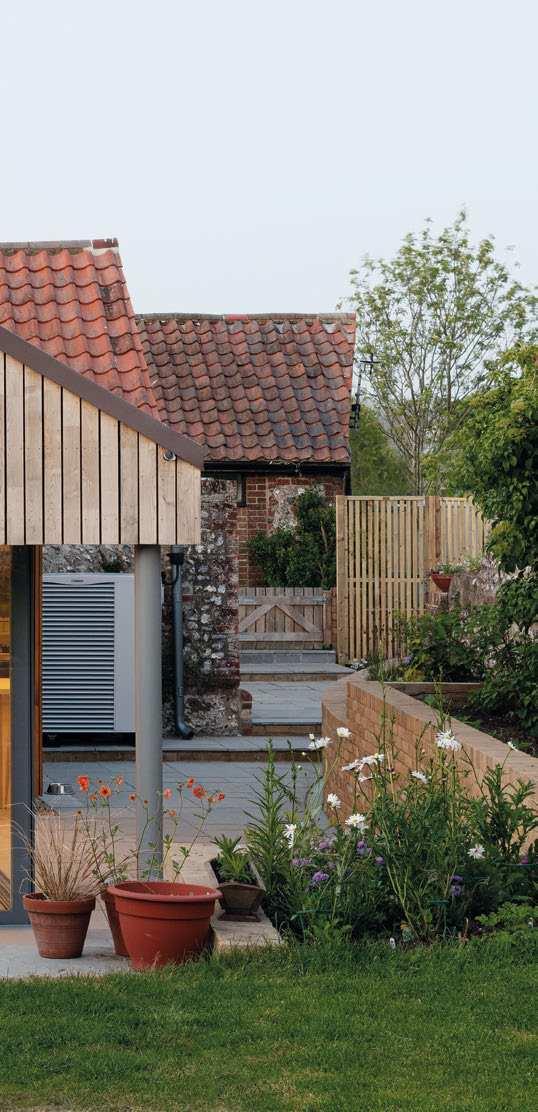
6 minute read
FOCUS ON TIMBER Exploring
from gcdfgf

Building with timber locks up tonnes of carbon in the structure for the lifetime of the home
Advertisement
A collaborative process
Firms specialising in building timber homes, such as Baufritz (baufritz.com) or Border Oak (borderoak.com), may be able to take care of both the design and construction of your home, as many have an in-house design team. Or you could commission an architect to devise the design – look for a practice with experience in timber buildings, and bring the architect and timber specialist together early on so the technical aspects of the design and the build system dovetail.
You can find reputable suppliers through trade associations such as the Structural Timber Association (structuraltimber.co.uk) and the Timber Research and Development Association (trada.co.uk). ABOVE AND BELOW A three-bedroom Victorian house in Barnet, north London, was extended by Amos Goldreich Architecture. A structural timber post-and-beam frame forms the roof of the extension. Built on site, it took four weeks to construct. Inside, limewashed timber joinery creates shelving and a room divider. A similar project would cost around £250,000. (agarchitecture.net)
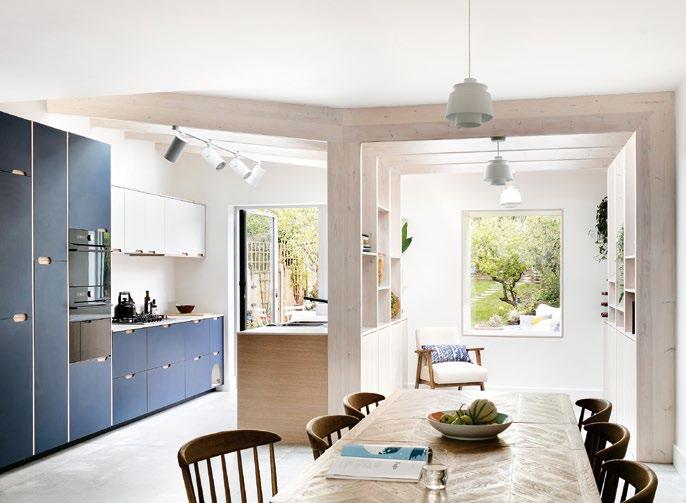
All above board
All the normal rules apply with regards to obtaining planning permission for your project. ‘The planning process considers a building’s design and impact on the area – it’s not as interested in the construction,’ says Adam Knibb, director at Adam Knibb Architects (adamknibbarchitects.com). A new-build home will need consent, as may an extension. Visit the Planning Portal for more information and consult with your local authority (planningportal.co.uk).
A timber-built house or extension must meet the performance requirements laid out by Building Regulations. Part B covers fire-safety standards, an issue which may be of specific concern when building with wood. There are measures, including fire-resistant components, sprinkler systems and a floorplan providing easy escape routes, that can be taken to meet and exceed the requirements. ‘Fortunately, a new-build can be designed from the bottom up to include fire safety,’ says Oliver Rehm, CEO of Baufritz UK.
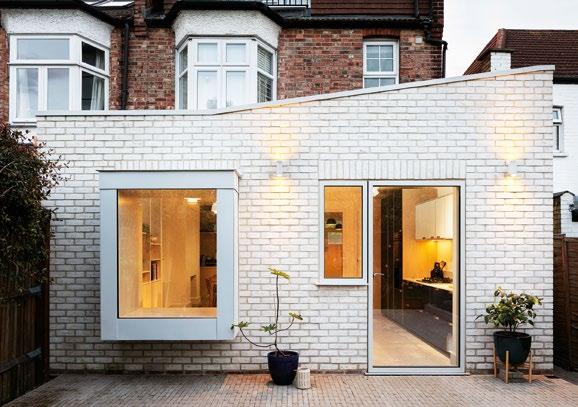

Funding issues
Lenders in the UK regard timber buildings as a nonstandard form of construction, therefore fewer are willing to provide funding. Start by taking advice from self-build mortgage brokers, such as BuildStore (buildstore.co.uk) or Mary Riley Solutions (maryrileysolutions.co.uk), which will have access to specialist products. ‘Most lenders require you to have a structural warranty in place before they lend,’ says Simon Orrells, managing director at Frame Technologies (frametechnologies.co.uk). ‘This insurance policy covers the cost of rectifying defects in a self-build. It’s not compulsory, but if you want to sell your home within ten years, you might have problems without one.’
Open-panel timber frame
These are softwood frames covered with wood-composite panels, usually plywood or oriented strand board (OSB), with a waterproof membrane on the outer surface. On site, the insides of the panels remain open until the structure is built and made weathertight. After this, the insulation and services are fitted, as well as windows and doors, before the panels are sealed with plasterboard. A weathertight structure can be in place in a week or two.
Accuracy is required so the walls slot into place, and there’s no room for error when laying the foundations. As the frames are manufactured off site, it’s tricky to make design modifications once they’re made. Although they offer good thermal performance, it’s not to the same level as closed panels, where insulation is installed under factory-controlled conditions. A one or two-bedroom house with a simple design could be completed for upwards of £80,000, with a lifespan of up to 100 years. ABOVE AND BELOW A timber frame was chosen for this two-storey extension to a 500-yearold Grade II listed cottage in Winchester, Hampshire, by Paul Cashin Architects. The frame components were easier than other build options to deliver to the hard-to-access site. Mineral wool insulation was installed on site between the vertical posts, with 50mm of PIR boards fitted over the frame. Clay tiles clad the exterior. A similar project would cost around £3,250 per sqm. (paulcashinarchitects.co.uk)

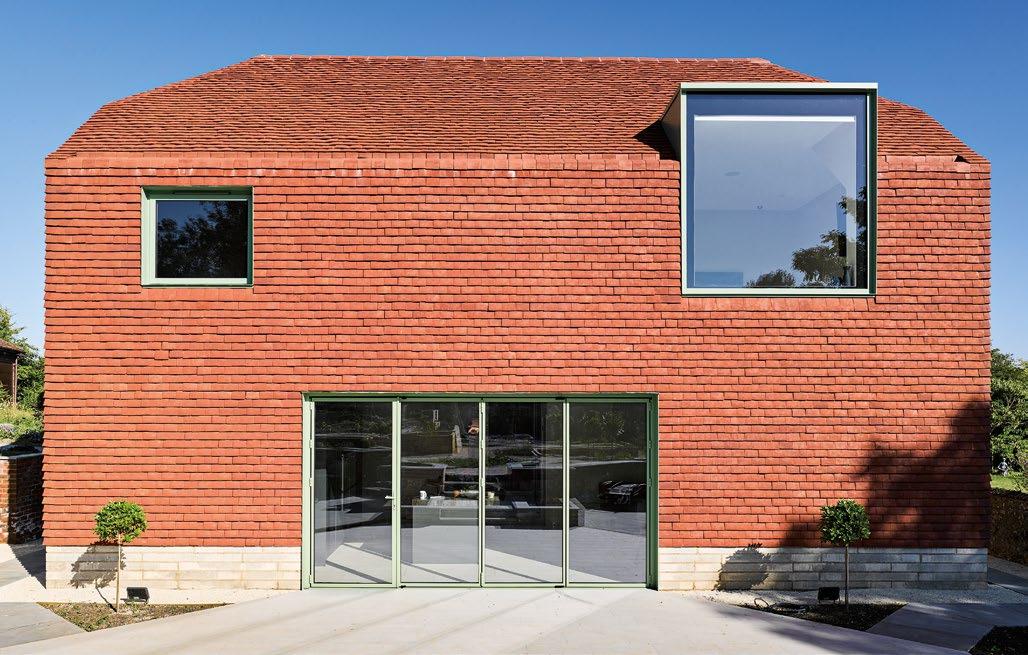

Structural insulated panels (SIPs)
SIPs typically consist of a layer of rigid, plastic-based insulation sandwiched between two wood-composite sheets. Engineered in a factory, once on site they can be slotted into place to form floors, walls and the roof in as little as two weeks.
The high level of prefabrication allows for a predetermined level of airtightness and thermal performance. Design-wise, the slim profile of SIPs provides a proportionally bigger floor area inside the building and their strength negates the need for roof trusses, which allows for lofty vaulted ceilings and double-height spaces.
SIPs tend to be more expensive than other timber-frame systems, costing as much as £500 per sqm, depending on the complexity of your design and the supplier. Although, as they are lightweight, they require simpler and less costly foundations. RIGHT Glosford SIPs (glosfordsips.co.uk) worked with Warren Benbow Architects (warrenbenbow.com) to design this four-bedroom house on the border of Herefordshire and Worcestershire, before the components were made in the company’s factory. The project cost £950,000
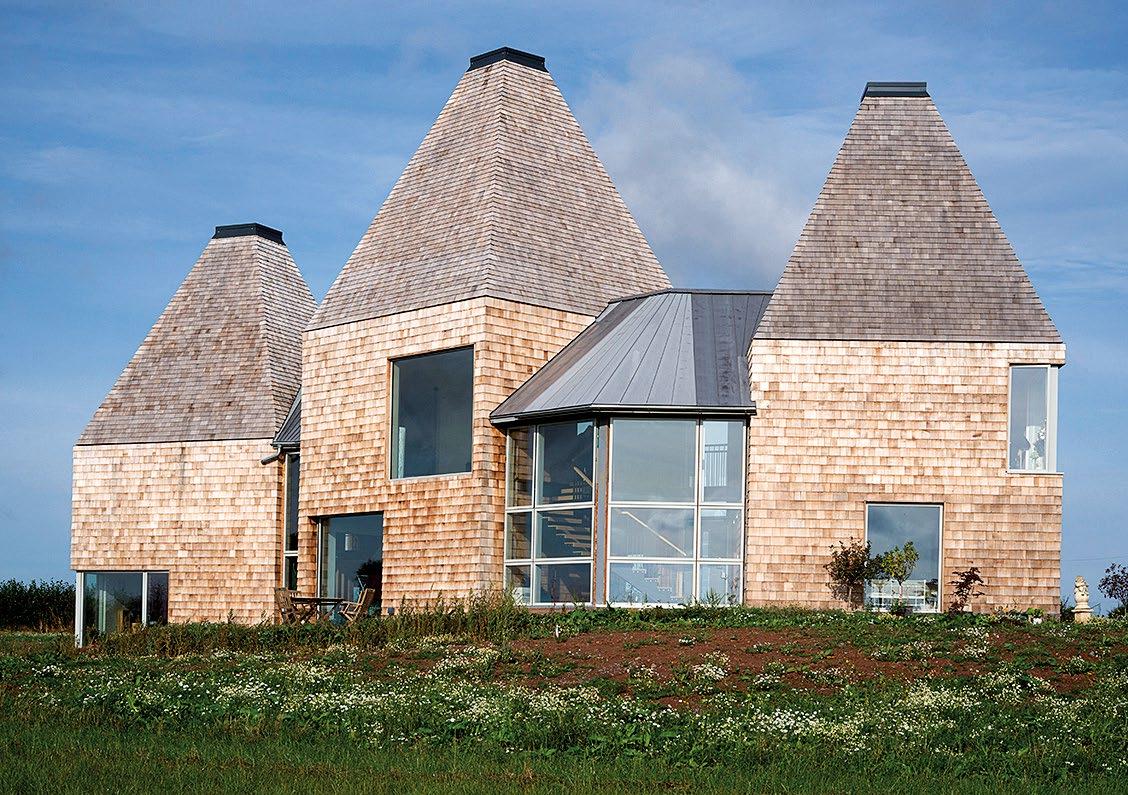
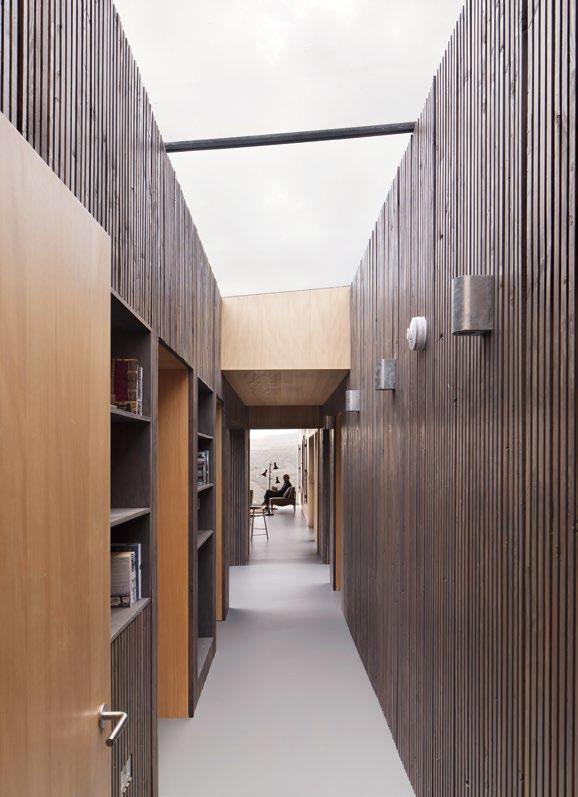
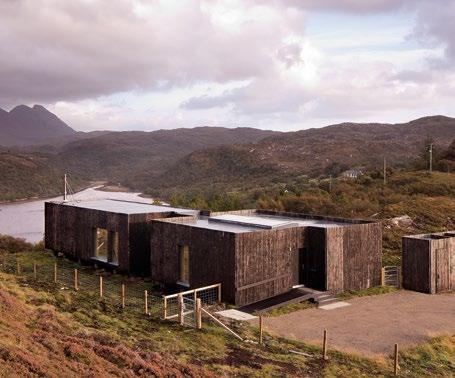
ABOVE AND LEFT Overlooking Loch Nedd, Scotland, this two-bedroom home was built with CLT. Carbon Dynamic (carbondynamic.com), which specialises in off-site modular construction, provided the structural elements. Designed by Mary Arnold Foster (maryarnold-forster.co.uk), it cost around £325,000 Cross-laminated timber (CLT)
Made by gluing several sheets of timber together in perpendicular layers, CLT is compressed so that it’s dimensionally stable. Perhaps because the suppliers are based in Europe, CLT is not a mainstream option in the UK and the carbon cost of transporting the material will impact the project’s carbon footprint. Its price is on a par with SIPs, but this can be offset by leaving the interior walls exposed. ‘CLT may look expensive on paper, but once the speed of construction and the reduction of trades is factored in, it becomes less so,’ says architect Adam Knibb. ‘Depending on the size of the project, homes built with CLT can be erected in one to three weeks.’

THIS PICTURE AND BELOW The damaged timber structure of this four-bedroom barn conversion in Herefordshire was dismantled and taken to the Border Oak workshop, where replica sections of oak were spliced into the original frame. A similar new-build would cost around £2,500 per sqm. (borderoak.com)
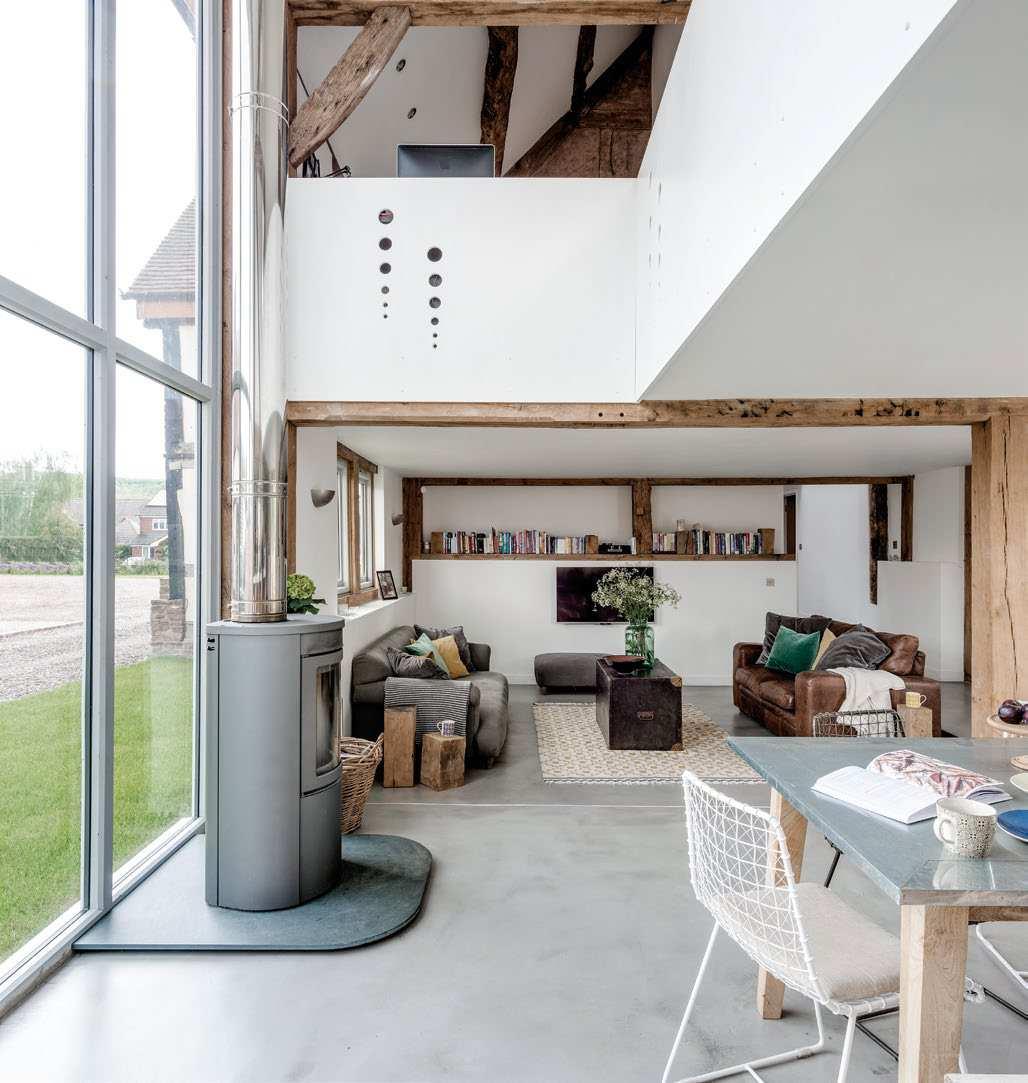
Oak frame
Oak is a tried-and-tested building material, having been used to construct homes in the UK for centuries. Most oak-framed buildings are of post-and-beam construction, comprising substantial vertical posts supporting horizontal beams. The spaces between them are filled with a system such as SIPs, which includes the insulating material, to create an airtight shell.
The structure is built in around a week or two, depending on the complexity of the design, and the material has good eco credentials. ‘Oak frame has low embodied energy, with minimal processing and no additives, and stores more carbon than other timbers,’ says Merry Albright, creative director at Border Oak (borderoak.com). ‘An oak frame looks good, so you don’t need to add lots of decorative finishes, and has unrivalled longevity of up to 1,000 years.’
Oak is a premium material, so total build costs are likely to be between £1,750 and £2,000 per sqm. A complex design that requires curved timbers, or one with lots of exposed oak, will drive costs up.
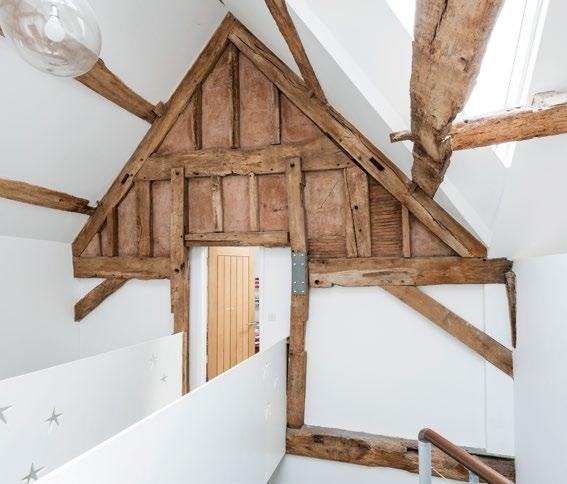