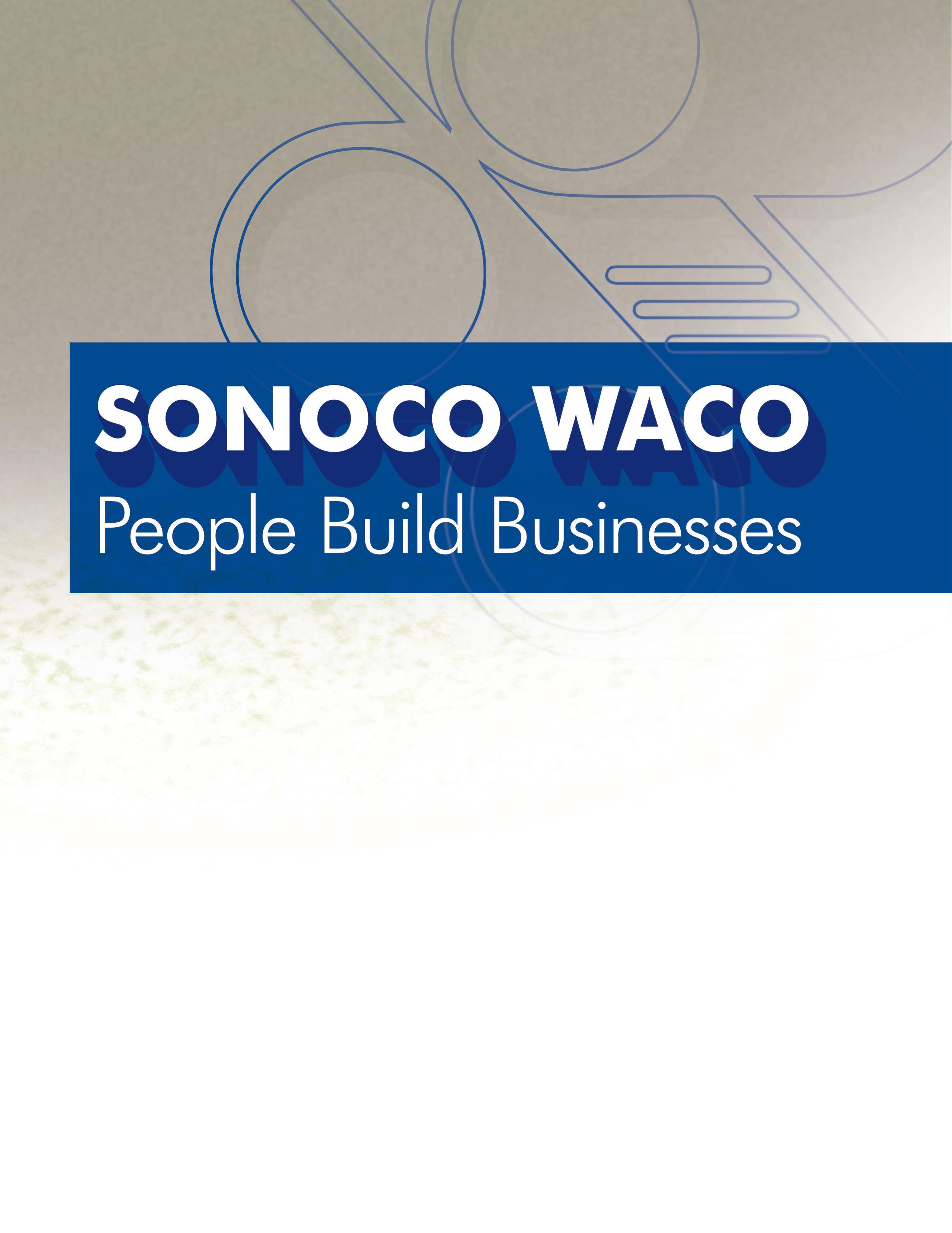
7 minute read
Sonoco-Waco People Build Businesses
by Jeremy Mitchell, Technical Manager, Sonoco Flexibles Division and Sara Schlesinger, PhD, Process Engineer, Sonoco Flexibles Division
Since Sonoco expanded to Waco in 2006, the company has not stopped growing. Upon landing in Waco in 2006, after the acquisition of Seville-FlexPack, Sonoco-Waco sales were just over $6 million. Since then, sales have increased more than ten-fold. SonocoWaco has more than tripled its workforce, with teammates increasing from 23 to more than 80 today. Sonoco has invested well over $25 million in this facility with capital going to new primary equipment and secondary equipment, storage racks, lighting upgrades and machinery improvements. Whether it’s through opening capacity by working on DMAIC (define, measure, analyze, improve, control) and lean projects or adding capacity through investment, our goal is to reach over $100 million in sales.
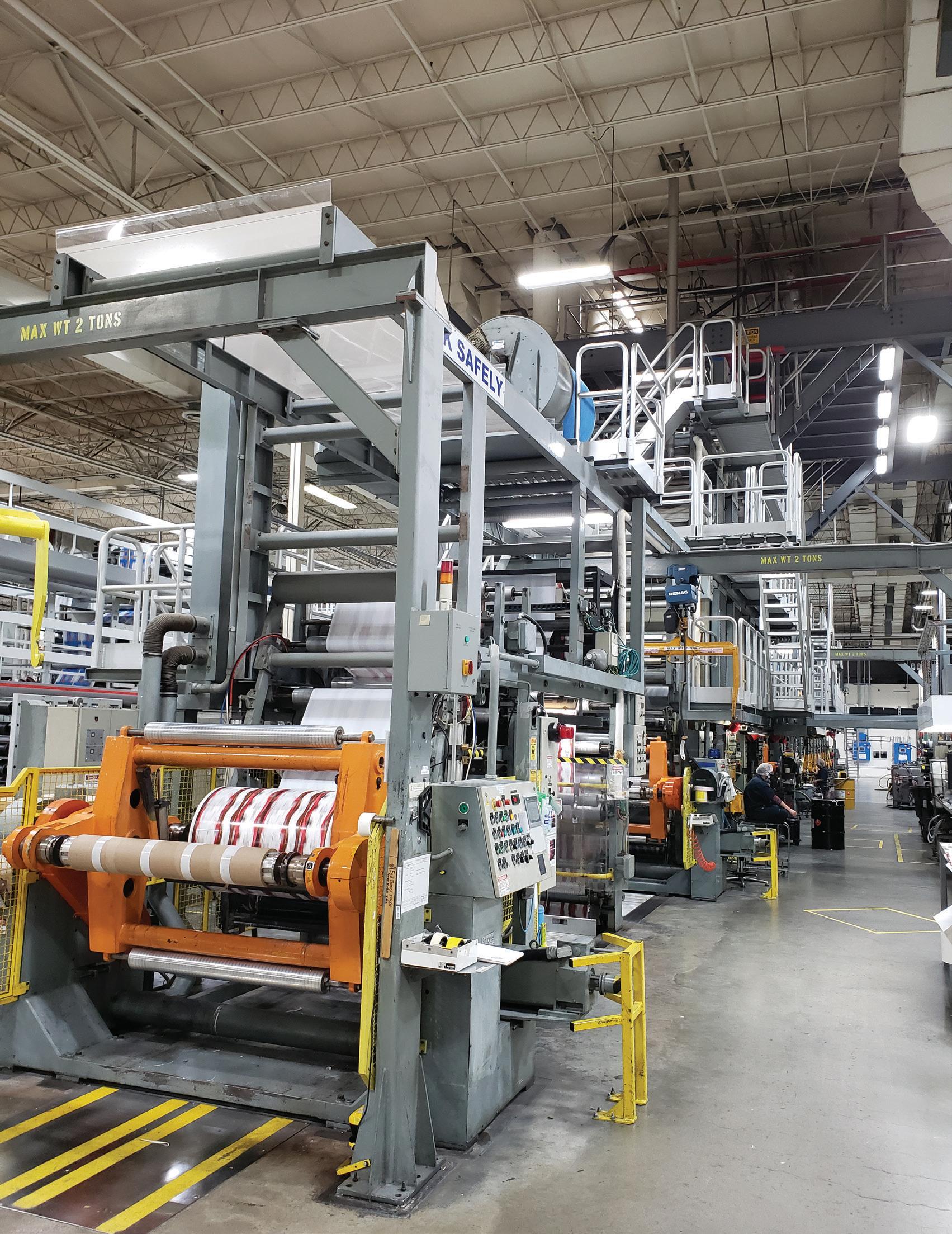
Schiavi II Printing Press
Located along Texas Central Parkway, Sonoco Flexible Packaging – Waco services the consumer packaging division of Sonoco Products Company, headquartered in Hartsville, S.C. Waco utilizes the rotogravure printing process with in-line lamination to manufacture 1, 2, 3 and even 4 ply flexible food-safe packaging. This packaging is used by customers to house confections, baked goods, coffee and other food products. SonocoWaco works with customers to understand their packaging needs like functionality, convenience, storage and visual appeal to produce high-quality, innovative, value-creating packaging solutions. Once an idea is conceptualized, teammates convert raw packaging substrates into printed material that includes the customer’s specific colors, logos, item numbers and UPC/QR codes. The printed and laminated material is then sent through the finishing department to complete customer requirements and is shipped. SonocoWaco’s customer mix extends as far north as Toronto, Canada, as close as Mars Wrigley in Waco, and as far south as Puebla, Mexico.
Sonoco is constantly looking toward the future and that includes the sustainability of products. There are projects in the works with several major customers on transitioning structures to monomaterial recycle ready films. With the specific technical requirements of many structures, this is a sizeable challenge. Sonoco is constantly looking for ways to eliminate its carbon footprint.
At Sonoco, we believe “People build business by doing the right thing.” As a corporation, we have celebrated the contributions of the people who have built our business for more than 120 years. Today, we remain devoted to our team by providing a caring, safe and fulfilling work environment. Employees are involved in every level of our safety program. They conduct monthly plant safety audits, lead and participate in eight different safety teams and take part in robust near-miss reporting systems which require employees to document any potentially unsafe condition or behaviors they observe and report these events to drive improvement. Each teammate is also involved in the Sonoco Performance System, a process that drives sustainable continuous improvement in safety, quality and production.
Over the past two years, Sonoco has reduced its turnover rate in Waco by 62%. This is, in part, due to yearly wage analyses that have resulted in hourly pay increases. It can also be attributed to the continuous skills development team, which has worked to reduce the time from onboarding to fully qualified (at which point an employee begins to receive certified-position level pay) from an average of 16 weeks to just six weeks.
Even as Sonoco grows in Waco, teammates still consider the facility a small family. During the freeze in February, Sonoco was fortunate to have electricity. The company opened its doors to employees day and night so they could have hot showers, light and warmth.
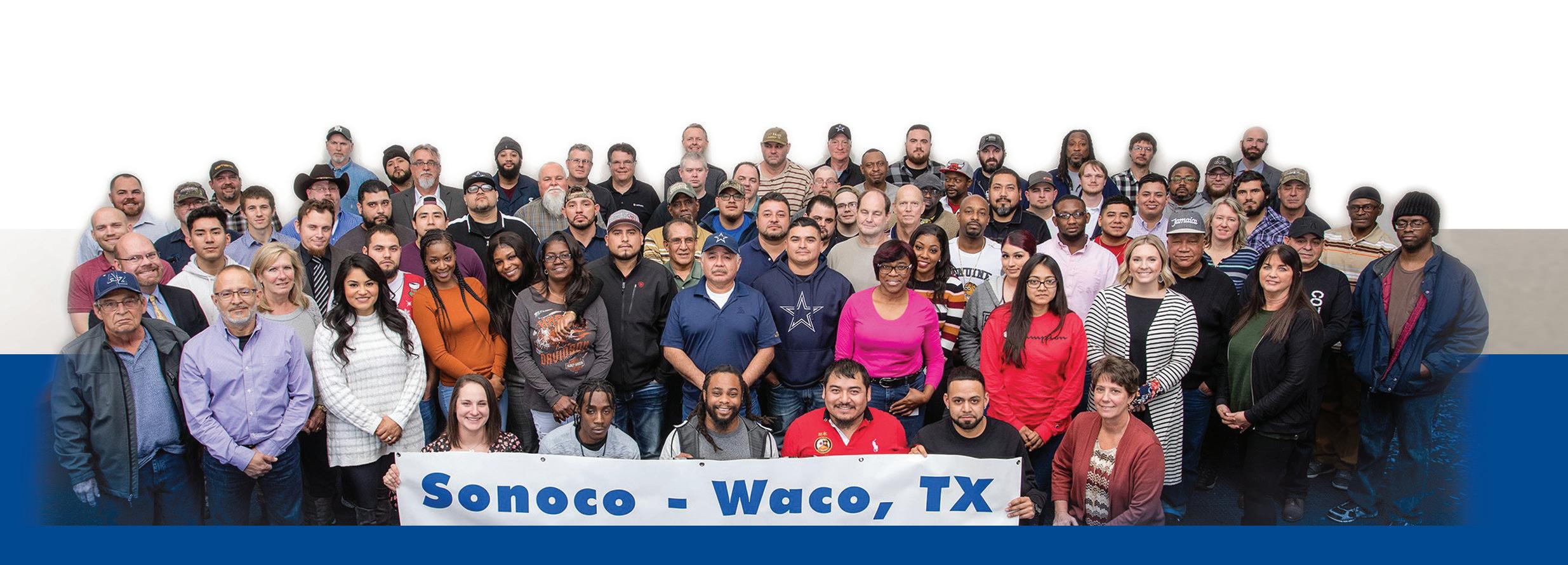
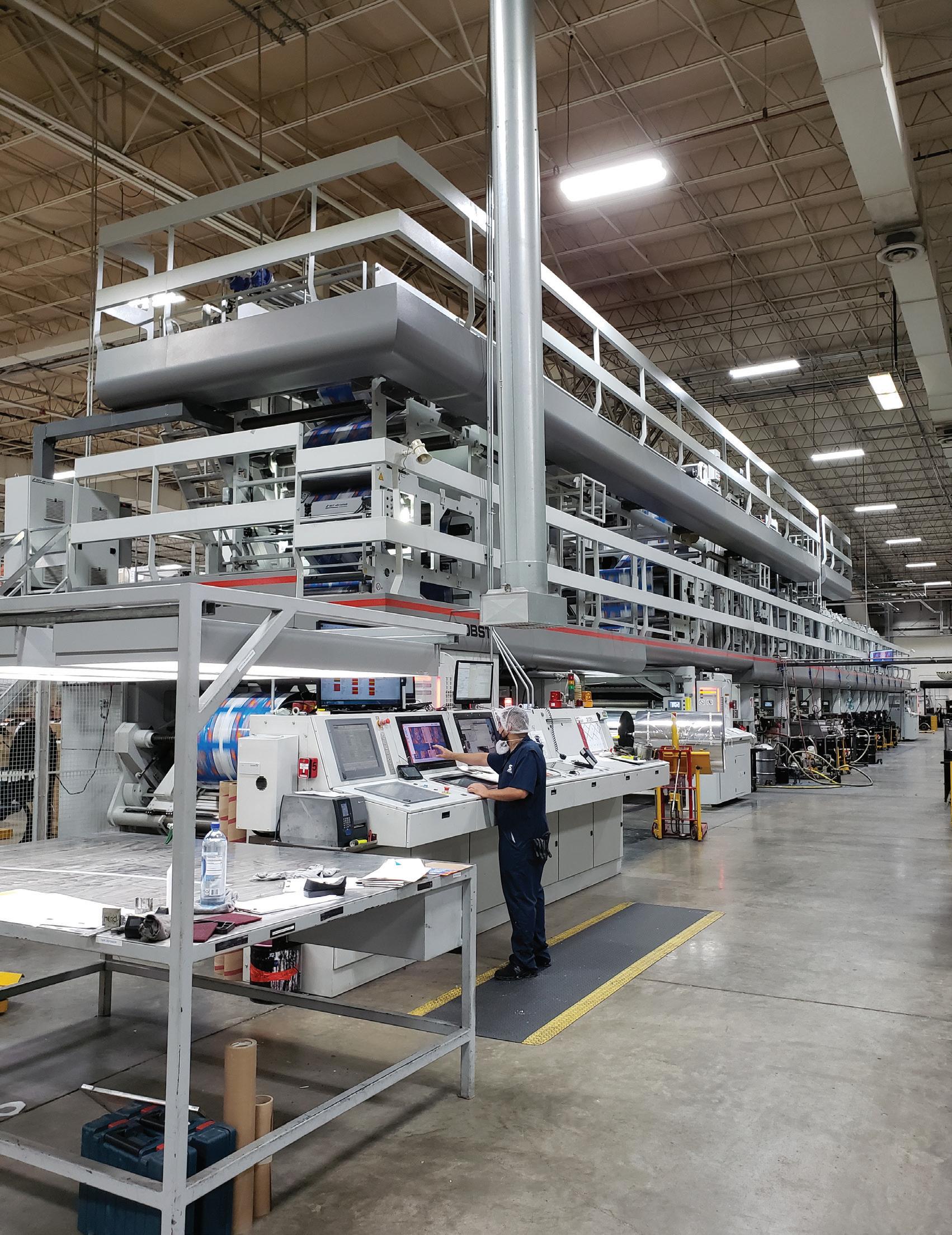
Rotomec Printing Press
The company is also committed to employees furthering their education and skills. Always looking to grow its workforce, Sonoco-Waco has relationships with the career services department at McLennan Community College (MCC) and Baylor University’s Career Center to help place students into open positions. In February 2021, Sonoco attended the annual meeting of the MCC Engineering Advisory Council, which afforded the company the opportunity to be featured at one of the MCC Engineering & Physics Club’s Homework Nights where Sonoco-Waco discussed internship opportunities and career paths, as well as, how students might prepare themselves for interviews within the engineering industry. Sonoco-Waco also participates in a Skills Development Fund grant with MCC through the Texas Workforce Commission, which enables the company to bring both technical and non-technical training directly to employees through zoom training sessions and on-the-job training videos. Every employee at Sonoco-Waco has participated in these trainings in some way, and the training videos are an important tool to help bridge the gap between reading a standard operating procedure and performing production tasks.
Sonoco-Waco serves many instantly recognizable brands. Major customers include Mondelez International, Mars Wrigley, Perfetti Van Melle, Goetze, Mother Parkers and others. In Waco, the company offers many unique packaging innovations. One of these is Clearguard, a clear structure with an extremely high barrier that can be used for snack bars. One of the biggest packaging innovations in Waco is the snack and seal structure (SNS) for Mondelez International, a resealable package that houses Oreos, Chips Ahoy, Fig Newtons and other cookies. More than half of all SNS packages are made right here in Waco. The company is also working to increase market share in smart lidding, a resealable flexible lid that covers plastic containers holding fruits and other food items. It is just one of many new business opportunities for Sonoco.
Continuous improvement is a huge part of Sonoco and that holds true for the Waco plant. For the past several years, Sonoco has implemented a program called Sonoco Performance System (SPS). This is an overall continuous improvement program that works on creating value-driven DMAIC projects. DMAIC stands for define, measure, analyze, improve, control and is a controlled method for setting the scope of a project and ensuring decisions about the project are made with supporting data. SPS is a program that not only encourages employee participation but also demands it. There are several pillars that focus on different aspects of the plant including safety, quality, production, cleanliness/organization (5S), maintenance, etc. Waco was lucky enough to be chosen as the SPS pilot plant for the flexibles division in 2012. By reducing returned sales, internal waste, downtime, and other important metrics, we worked our way through bronze, silver, and finally gold status, which we reached in 2015. When a plant reaches gold, they must be recertified every other year. Waco was the first gold plant in the entire company to be recertified without contingency and has since been recertified twice. Because SPS is about continuous improvement, Sonoco is continuously working to find, reduce and eliminate waste, whether that be time, material, talent, or other wastes. Some examples of projects completed in just the last year at the Waco Plant are changeover time/waste reduction and a project we call Sonocoly.
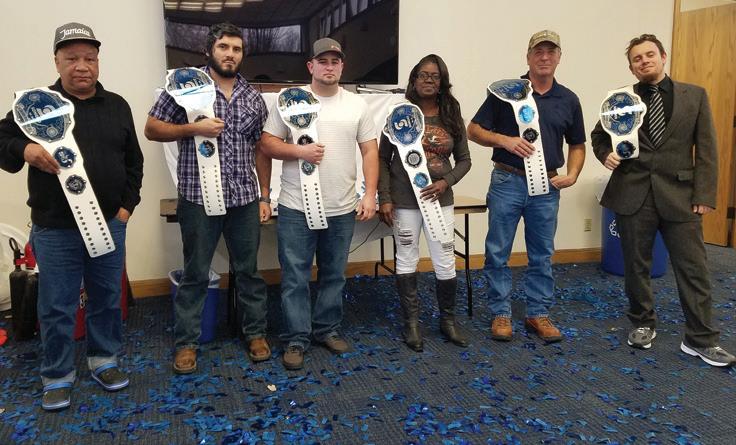
2020 SPS Department Champions
One of the biggest wastes in flexible packaging, both in time and material, is a process referred to as ‘changeover’. This is the time period starting from the end of running item A to the beginning of running good material for item B. During that time, there are several individuals involved in making the many changes necessary to begin running item B. Inks need to be swapped out, printing cylinders need to be removed, printing cylinders need to be added, doctor blades (used to wipe away excess ink) need to be swapped out, raw materials may need to be changed, web path may alter, among other changes. When Sonoco first acquired the plant in Waco, a changeover would take multiple shifts (each more than 8 hours). Over the years, the team has implemented many projects that gradually reduced this time to allow for multiple changeovers in a single shift. The Waco plant recently completed a DMAIC project focused on the newest press. This project analyzed the current process and decided to rebuild and replace the existing process. This has been one of the most successful projects yet, reducing the internal waste during changeover and the time required to complete the changeover by nearly 50% from previous levels.
Sonocoly is a program directed at employee engagement in helping to control gains made by other projects. Sonocoly is based off the wellknown Hasbro game Monopoly; in Sonocoly players move around the board by rolling dice, buying properties within the plant using ‘money’ earned based on their teams performance metrics; however, instead of paying each other rent, the plant manager is also rolling dice around the board and is the only one who pays rent. Just like in Monopoly, players can trade properties with each other and buy buildings to increase the rent on their owned properties. At the end of a quarter each team can spend their total earnings on various prizes including food deliveries, “mymarket” cards and a trip to Saltgrass. This project has been a tremendous success and was entirely devised and led by an employee. It is currently being leveraged to plants not only throughout the division, but throughout the company.
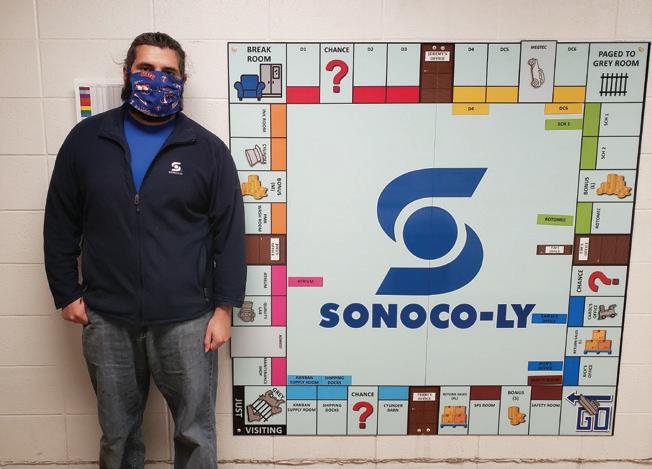
The Game of Sonocoly along with Creator Michael Canales
