
10 minute read
RALEIGHITES
Andy Danser in his Durham guitar workshop
by SAMANTHA GRATTON photographs by BEN MCKEOWN
Advertisement
FINE-TUNED
Hearing from guitar makers in the Triangle
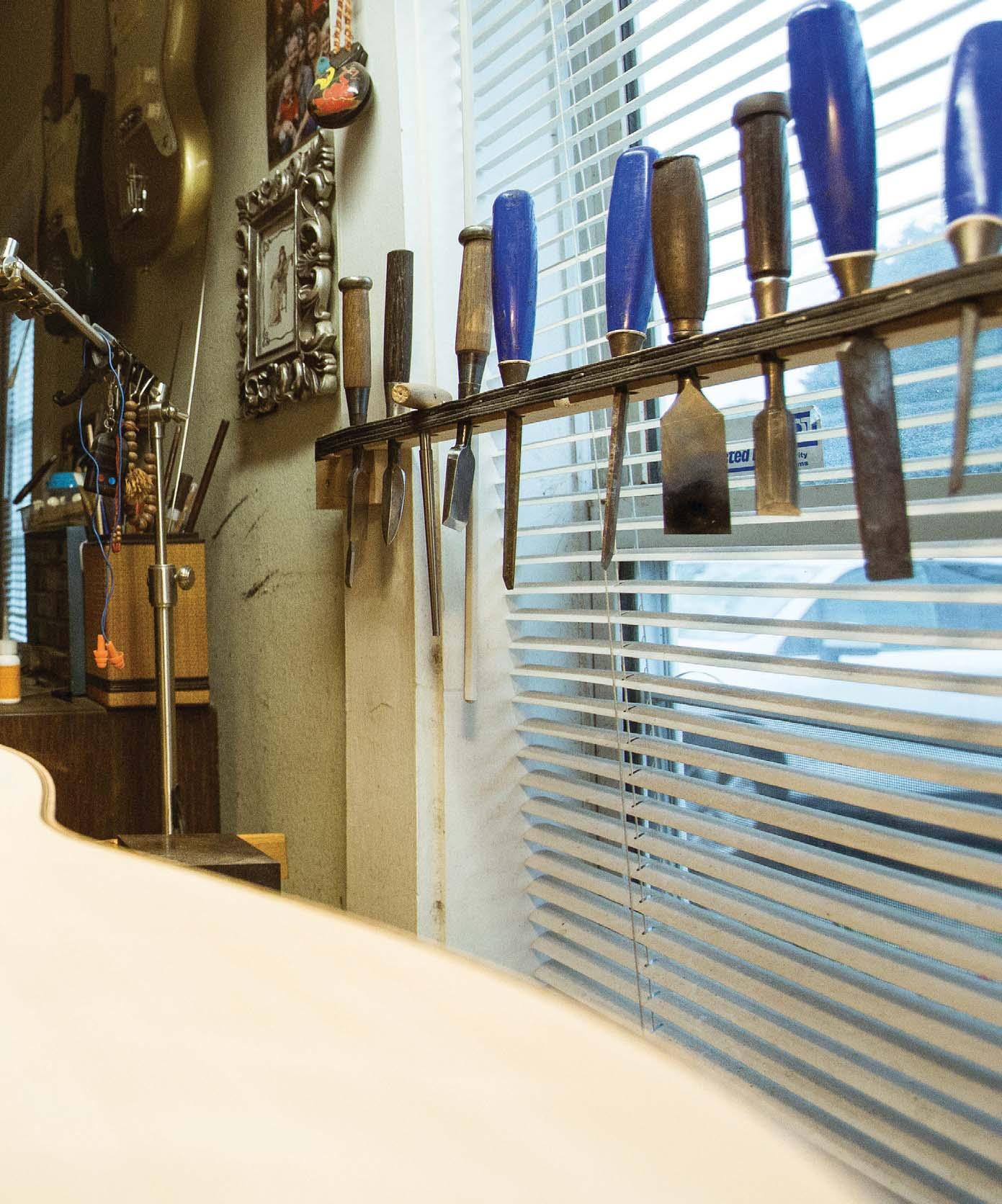
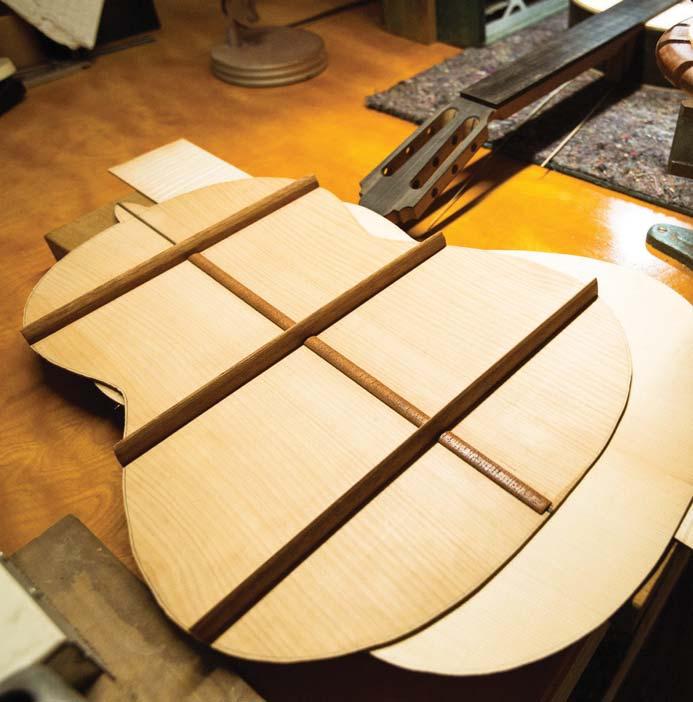
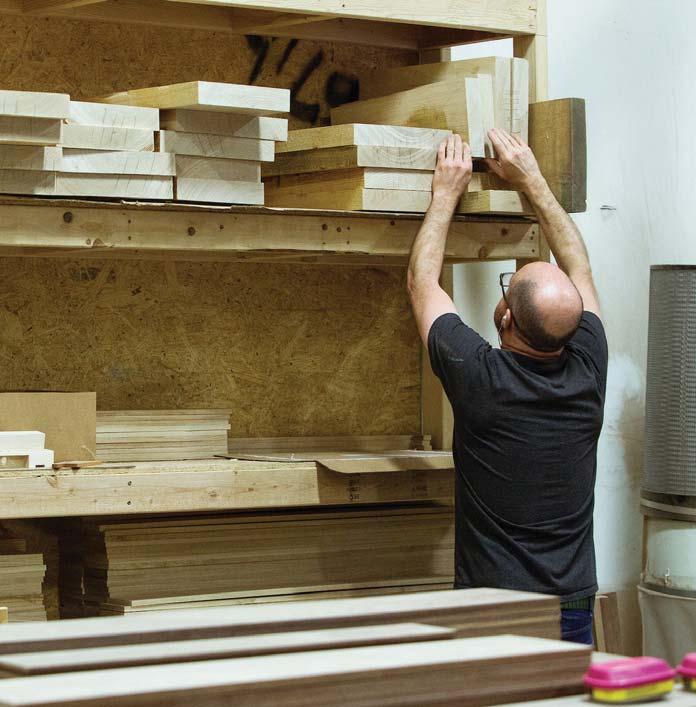
From left to right: Behind the scenes at Pre-War Guitars Co. in Hillsborough; Andy Danser’s workshop in Durham; Tim Benware in his home workshop in Creedmoor; Tim Benware holds an instrument in the making Every guitar has its own distinguishing feature, be it the sound, color, or brand name on the headstock. Every guitarist chooses a varying tune and playing style, but the instrument itself can impact the sound almost as much as the musician. Of those making guitars in the Triangle, each luthier is as different as the guitar he or she makes—different backgrounds, different goals, and different perspectives. Each is bringing something new to the industry, from completely custom guitars based on the whims of their customers to a style of guitar that has not been commonly found in decades. Here, meet a few of them.
Nostalgic for another era
When it comes to building guitars, Wes Lambe and Ben Maschal have a very specific style and sound in mind. Instead of building custom guitars, the two joined together to create Pre-War Guitars Co., named after the guitars commonly found in the late ’30s, prior to World War II. Customers choose between the different ’30s-era models of acoustic guitars, and then choose the level of distress they want, ranging from mint condition to heavy wear. Their guitars have been popular with bluegrass musicians, and their customers include Tommy Emmanuel, Molly Tuttle, David Grisman, Trey Hensley, and Andrew Marlin. These well-made guitars expertly appear well-worn, giving each guitar the look and feel of something that has experience. It’s a difference that appeals to musicians more than collectors. Lambe says Pre-War Guitars are “more of a players instrument—not art, but a tool for musicians to make their art.” To create the well-worn appearance, Lambe and Maschal intentionally add wear and tear to each freshly crafted instrument. When they first distressed a guitar after months of working on it, Maschal admits he felt like he “ruined it.” Luckily, the partners’ friendship continually encourages them to have fun and take
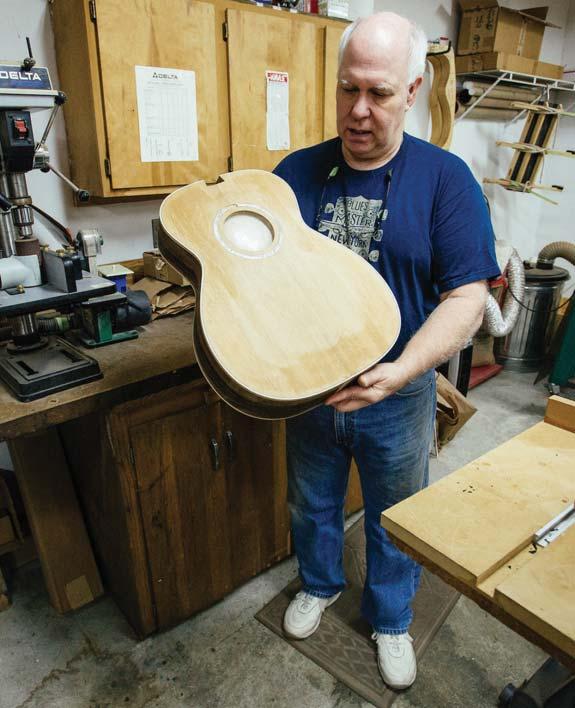
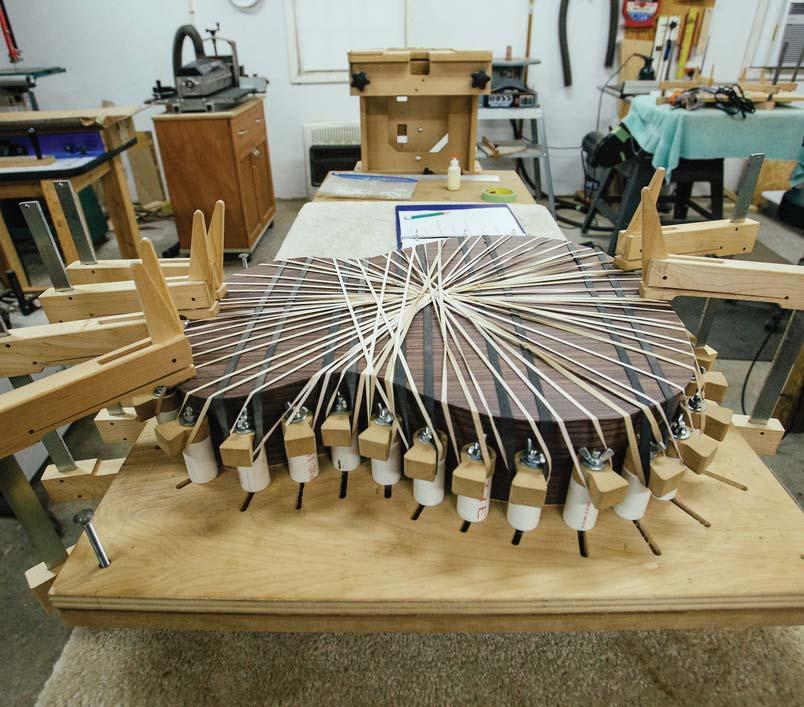
risks for the sake of their craft. And these two know their craft. Prior to Pre-War Guitars, both luthiers had been making guitars on their own; Maschal estimates he had made around 50 guitars and Lambe had made almost 200. Along the way, they also extensively repaired guitars actually from the 1930s era, which today leaves them with a thorough understanding of how to accurately replicate the vintage guitars. North Carolina natives, Maschal was born in Charlotte and Lambe in Durham. After high school, both went to different schools for guitar-building and lutherie before returning to their home state to work on guitars. As with many guitar makers, guitar repair work supplemented much of their income, but they also had to work other jobs—Lambe in restaurant kitchens, Maschal building cabinetry. “It’s really hard to just make guitars,” Lambe says. Finding a partner makes it easier. After each working separately on both guitars and their side jobs, in 2014 Maschal started doing subcontracting work for Lambe. By the fall of 2015 they formed The Luthiers Workshop in Hillsborough and then Pre-War Guitars in 2016. “I feel very lucky to be doing what I do,” says Lambe. Mashcal adds, “I feel lucky to be making a living at it.” They build about 12 to 15 Pre-War Guitars a month, and have been conscious to remain diverse in their work. Lambe and Maschal are also part owners of Hybrid Guitars Co., a company that makes a combination instrument of a bass and guitar. Lambe continues his Wes Lambe Guitars instrument-making business. Each year, the duo also builds thousands of wood side panels in analog synthesizers for Moog Music in Asheville.
Building relationships
Tim Benware, a luthier from Creedmoor, knows one thing is certain when it comes to making guitars: “It has to be a combination of look good and sound good.” After a full career in law enforcement, Benware retired as a police chief in 2012. About 10 years ago, he started asking himself what he wanted to do in retirement. His experience with guitars up until then consisted of minor repairs to his own guitars, bolstered by his perspective as a musician. Since the early ’70s, he’s played acoustic and folk music in a band and at church, and his band has cut two albums and a Christmas record. To prepare for his retirement, Benware decided to study with Dave Nichols at Custom Pearl Inlay in New York in 2010, taking classes in guitar-building and advanced repairs. When he retired, he put his classes to work to take on guitar repairs, and started building custom acoustic guitars out of his garage in Creedmoor. He started with a few ads on Craigslist and business quickly grew by word-of-mouth. Today, about half of Benware’s time is spent repairing or restoring guitars and the other half is spent building. He makes acoustic guitars primarily, but he has also built ukuleles and electric guitars. He has since moved his work into its own workshop, and most
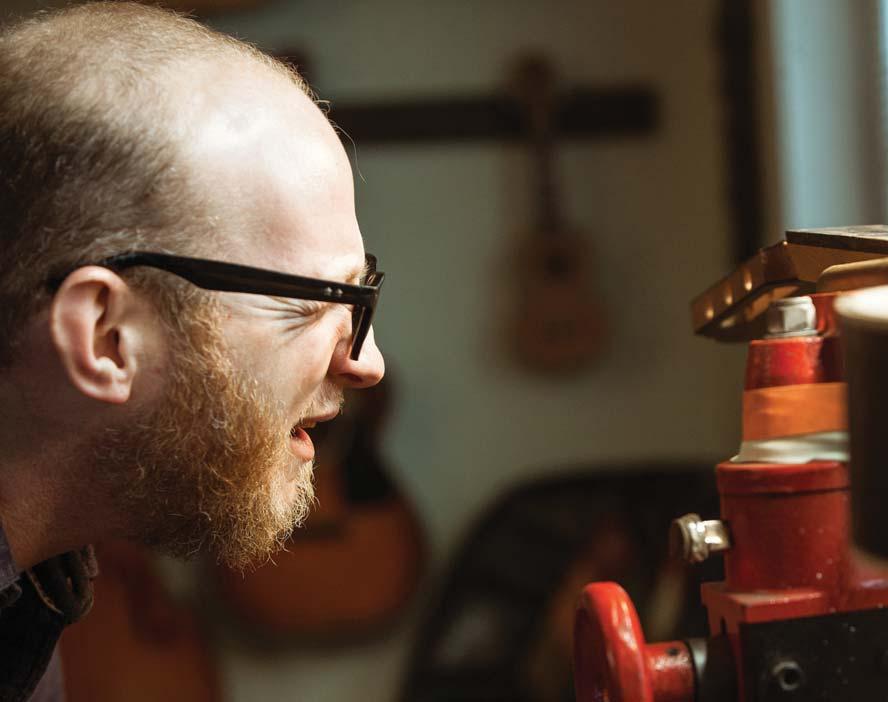
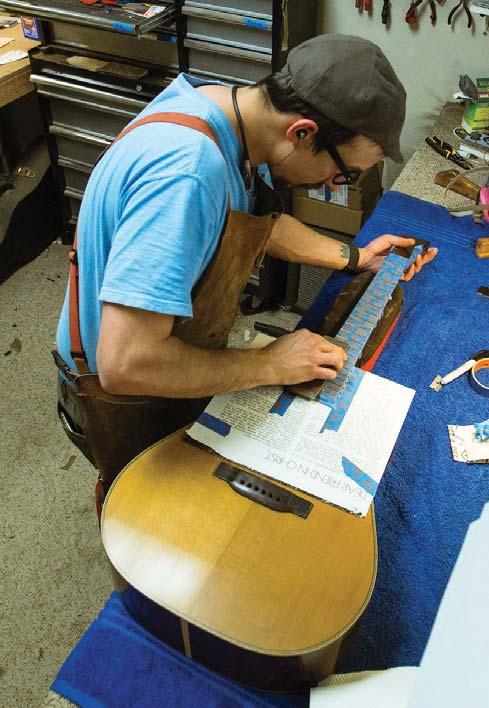
of his business is from repeat customers. Benware estimates that he has built about 100 guitars now, each time matching the guitar to the musician who will later play it. He is willing to try just about anything when it comes to customer specifications and takes pictures throughout the process to show the guitar’s progression. He likes the flexibility he has in adding proprietary designs and tones that differ from those found in standard manufactured guitars, but admits it is more time-consuming. “I think there’s a proven difference,” says Benware. “I know my customers well enough, and they compare the sound and they can hear the difference—it’s clear.” Over time as his work as become more known in the area, he’s had to scale back to balance the high demand for his work. “Making money wasn’t my main motivator for doing this. I like having the people come in my shop and talking with them,” says Benware. “A lot of my customers have become good friends. They enjoy it, I enjoy it.”
Musician + maker
Classically trained in both playing guitars and making them, Andy Danser specializes in classical and flamenco guitars. Different than a standard acoustic guitar, this type has nylon strings and is lightly built with finer woods that do not vibrate or resonate quite as much. Classical guitars, which originated in the 19th century in Spain, are also known for the rosette around the sound hole, an intricate design that provides reinforcement and beauty to the guitar. “To me, one of the most beautiful parts of a guitar, aesthetically, is a rosette. I do traditional intarsia which is the Spanish method of making rosettes,” says Danser. Created over several hours through a complicated woodworking process and then cut in a way that produces a pattern, the pieces are put together similar to a mosaic to form the rosette. Danser grew up in Durham alongside his twin brother, who also makes guitars in Austin, Texas. His father was a woodworker and stained glass artist, so he grew up watching him in the shop. Between earning his bachelor’s degree from UNC-Chapel Hill and later attending graduate school, Danser took a month-long course to learn how to build guitars. His plan was to complete
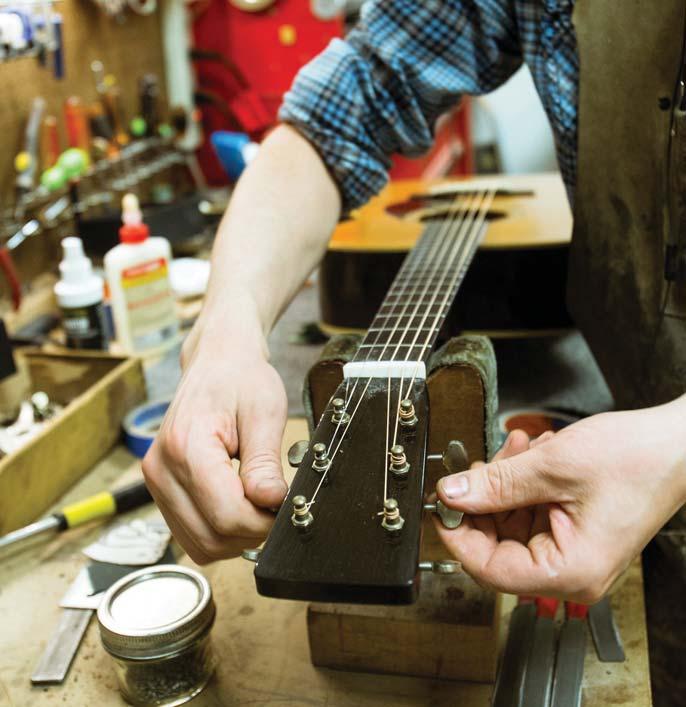
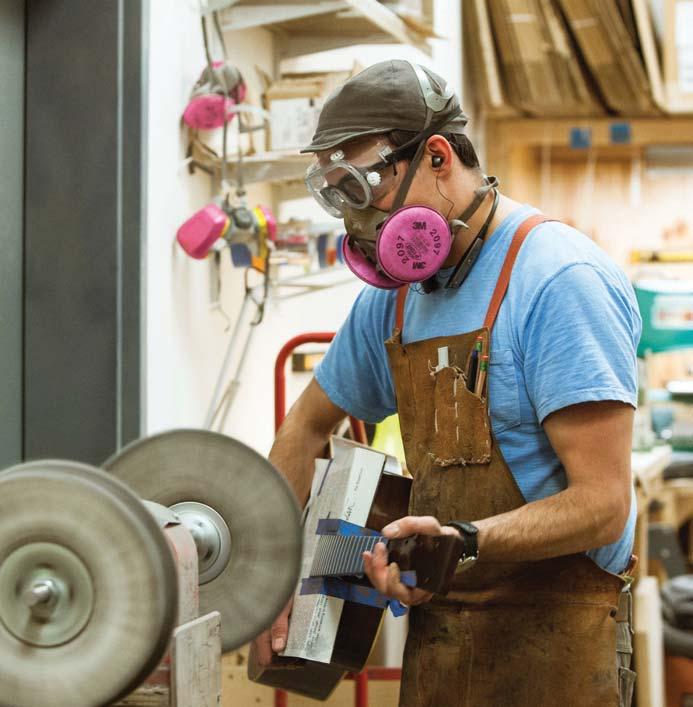
his master’s degree in international education, but guitar-making intrigued him most. “I was building guitars in my apartment, in the living room,” says Danser. “And it was all I could think about.” It wasn’t long before he left the master’s program to move to England and pursue classical guitar-building through a two-year program. Afterward, he did a year-long apprenticeship with esteemed guitar repairman Robert Jones in New York. In that time, Danser learned more about guitar repairs on a variety of expensive and vintage guitars. “Building guitars and repairing are two completely different disciplines,” says Danser, who felt he benefited from training in both. His has built over 25 guitars, but most of his clients first come to him for repairs. In 2006 he returned to his hometown of Durham, to be closer to his family and the great music scene in the area. He was active in a band and constantly found friends and fellow musicians who needed guitar repairs. Since then he has continued to be busy with guitar repairs, but tries to balance it out with building guitars and also spending time with his wife and kids. Danser is sure to prioritize: “my passion is building classical guitars.”
Fair bit of art, fair bit of science
After a long career in pharmaceutical manufacturing, Dale Brown jokes that he went “from drugs to rock ’n’ roll” when he began making guitars and bought Zion Guitars. Wanting to own his own business, Brown contacted Zion Guitars to learn more about their process, and ended up acquiring it in 2000. At the time, it was located in Greensboro, but he moved the business to Raleigh in 2001 where it continues to specialize in custom electric guitars. Brown had always had a guitar of his own and occasionally played in bars or at church, but he first tried building one in 1997. He is primarily self-taught and has made about 1,000 guitars since 2000. While a few of those have been acoustic
From left to right: Ben Maschal at Pre-War Guitars Co., which he co-founded with Wes Lambe; Andy Danser getting his details right; Maschal in process; Pre-War Guitars Co. co-founder Wes Lambe strings a vintage-style guitar
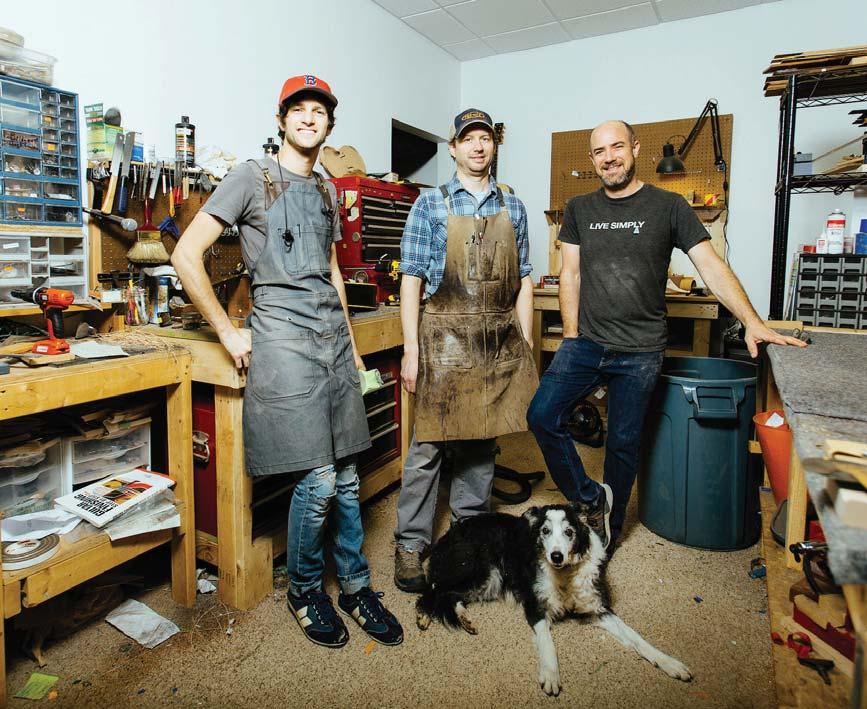
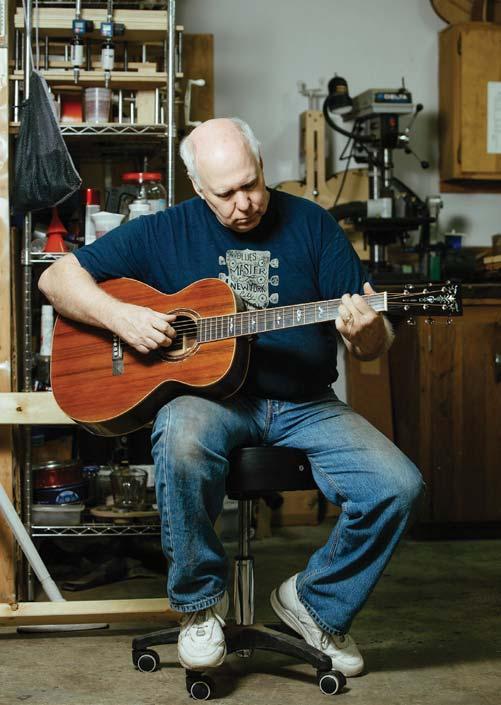
From left to right: Tim Benware also plays guitar, which informs his lutherie; Pre-War Guitars Co. craftsman Ross Guret, co-founder Wes Lambe, and craftsman Clay Conner
guitars, the majority have been electric. In regards to the manufacturing process of each guitar, Brown says, “There’s a fair bit of art, and there’s a fair bit of science.” It starts with selecting the guitar body shape, choosing the wood type, and then picking the hardware to go inside. The guitar neck, bridge, inlay, pickguard, and final color and finish are all customizable, too. “If you can think it, you can have it,” says Brown. He prefers to meet his customers and see them play in person so he can design a guitar that best suits their playing style. People have come from all over the world to begin the process, and when they are done, Zion Guitars have been shipped to far away places like Hong Kong, Hawaii, Indonesia, and Italy. While he spends most of his days building or sometimes repairing guitars, he most enjoys working with the people. “It’s a very interesting business, it absolutely is, and you get to meet some really nice people. … Any time you get together with somebody, you learn,” says Brown. “That’s something I like to do.”
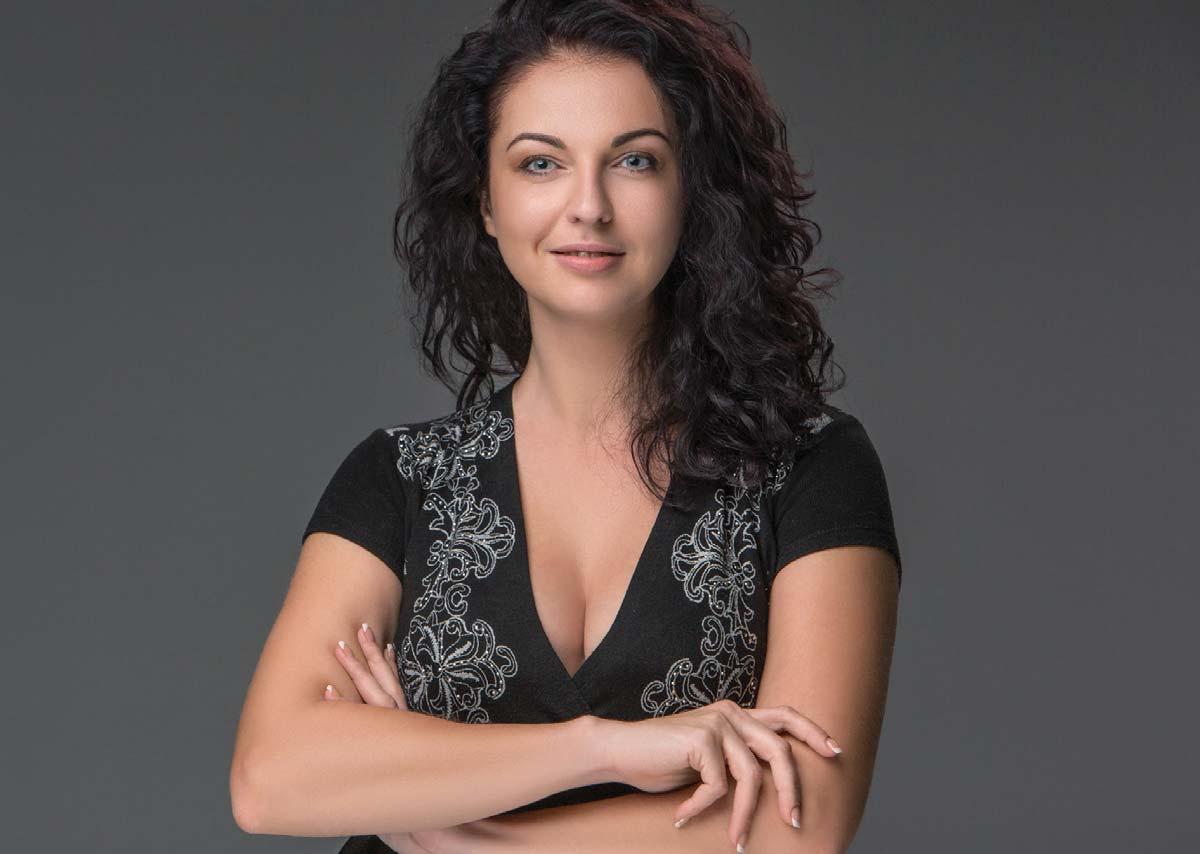
Artful.Natural.Zenn. . .N
BoardCertifiedplasticsurgeon, Dr.MichaelZenn,isoneof thecountry’sforemostexpertsincosmeticsurgery.Forthe past23yearshehassharedhisartistry,surgicalskillsand compassionatecarewithpatientsatUNCandDuke.