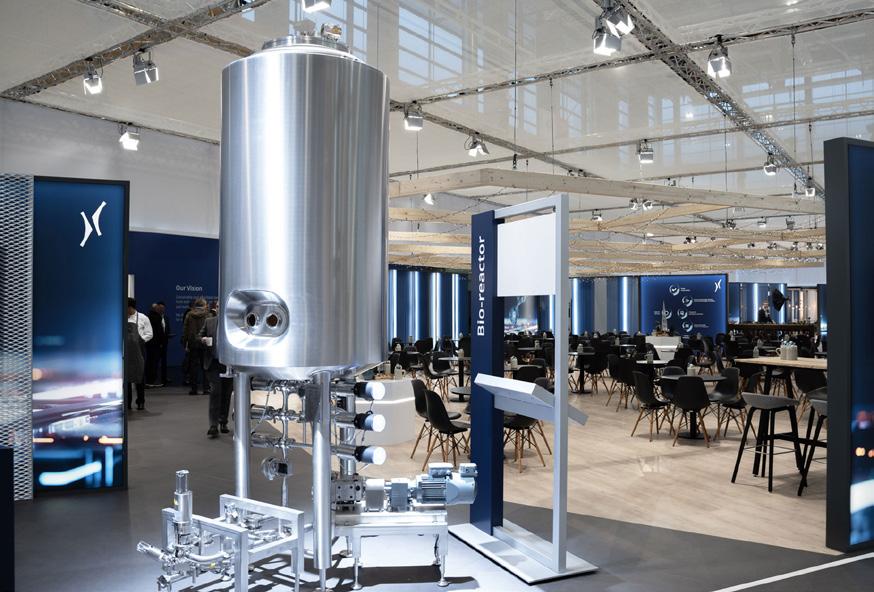
6 minute read
Krones Process & Filling Technology Krones at Anuga FoodTec 2024
What are the challenges faced by beverage and food producers worldwide? One is certainly ensuring security across the entire production process – because, of course, only products of impeccable quality should ever roll off the line and make their way to consumers.
What are the challenges faced by beverage and food producers worldwide? One is certainly ensuring security across the entire production process – because, of course, only products of impeccable quality should ever roll off the line and make their way to consumers. Another is sustainability, a factor that applies along the entire value chain. As we approach the end of certain finite resources, society has an obligation to do everything in its power to protect the natural environment and our planet as a whole. Of course, it goes without saying that these topics also play a central role in the vision and mission of the Krones Group, whether for new and continuing developments or for its many overarching concepts and services. At Anuga FoodTec 2024, Krones, together with its subsidiaries Steinecker, Milkron, Evoguard and HST, will be presenting plant and engineering solutions for beverage and food production. One main focus will be on showcasing customised, holistic sustainability concepts, especially those designed to save water and energy in the production process.
Integrated modular sustainability concepts
Krones plant engineering looks at a customer’s entire value chain and offers advice for recovering and recy-cling energy and water across the production operation. Steinecker and Milkron also offer a variety of ap-proaches to optimise sustainability in the production of milk and dairy products and plant-based alternatives, juices and soft drinks. Specific applications include HydroCircle, a complete concept for wastewater recycling, and specially designed heat exchanger systems or heat pumps for sustainable energy recovery.
Bioreactors for the “new food” sector visit: www.krones.com
When it comes to leveraging synergies, Krones doesn’t limit itself to simply choosing solutions for customers. Instead, the company seeks to use them to develop new systems and technologies, drawing on decades of in-house expertise in process technology and plant engineering and applying it to new and different product categories. The latest example of this comes from Steinecker, whose knowledge of and technology for fermenting beer, combined with Krones’ aseptic expertise, can be adapted to accomplish the cell-based manufacturing of new food products. Steinecker’s bioreactor is suitable for both precision fermentation and cell cultivation, mak-ing it possible to manufacture new food products like alternative proteins for meat substitutes and whey and egg proteins. Krones recently launched a partnership with the Swiss startup Food Brewer, and now the two companies are testing various applications and sharing the results with other companies to develop their own recipes and trials.
Equipment for the production and preservation of beverages and foods
For further process technology, Krones also offers a diverse range of solutions, from the plant planning and engineering expertise of Milkron to HST’s HLI90 high-pressure homogeniser and the VarioAsept D direct-heating system from Krones right through to the broad portfolio of pumps and valves from Evoguard and Ampco, for both standard and aseptic applications. Krones is also driving security and sustainability in other filling and packaging processes. For instance, by offering filling valves specially designed for the respective final product, we are
Food and Drink Network, Sustainability, 133 x 186 mm, CC-en 02/24 ensuring the highest quality when filling milk and dairy products and plant-based alterna-tives, juices and sauces. Meanwhile, LitePac Top is one of the most sustainable packaging concepts available today for PET containers and cans. Integrated concepts and solutions are among the greatest strengths of Krones process technology and of the entire group.
Shaping the future together
It’s important to look beyond the short term, which is why Krones is working on “Solutions beyond tomorrow”. Beverage filling lines, digital services and plastics recycling: Krones’ innovative solutions combine superior performance with sustainability.
Anuga FoodTec 2024, 19-22 March, Cologne, Hall 5.1/Stand A120-D129 krones.com freewheels, roller ramp clutches, combined sprag and bearing units and many more.
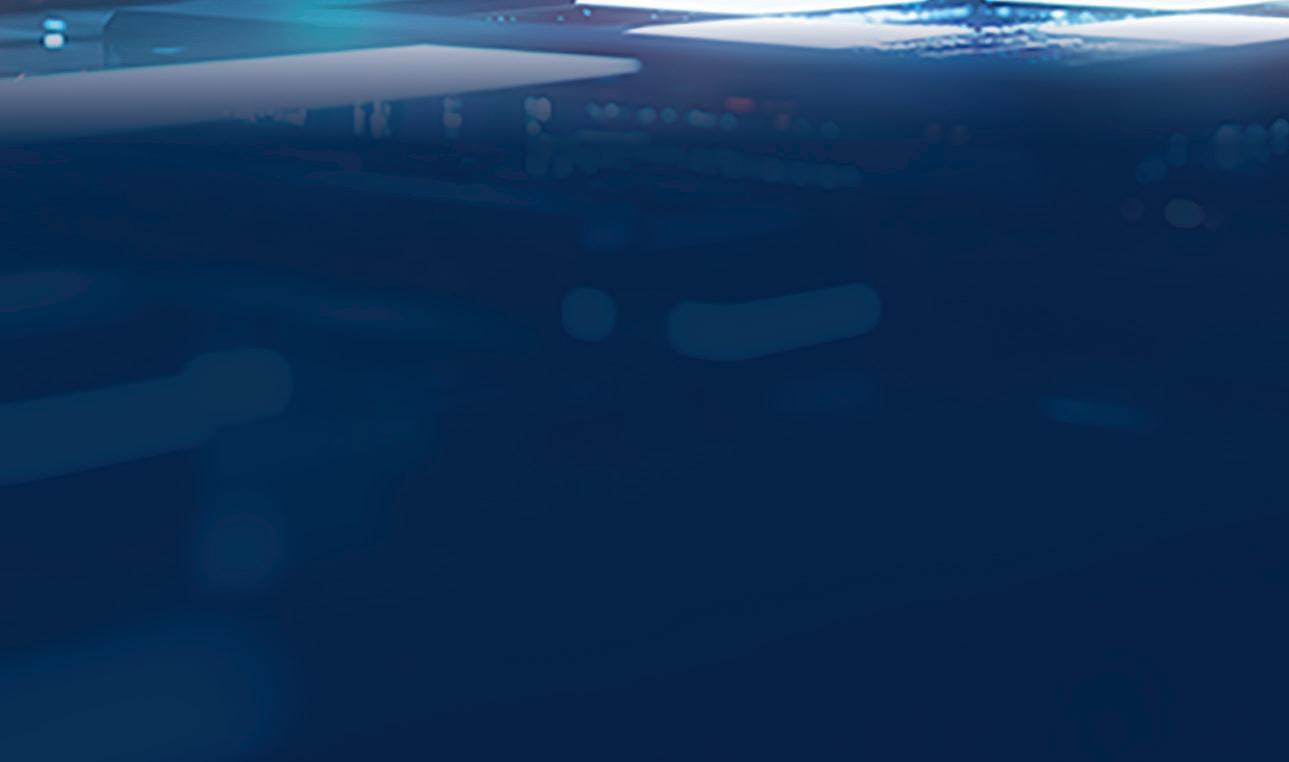
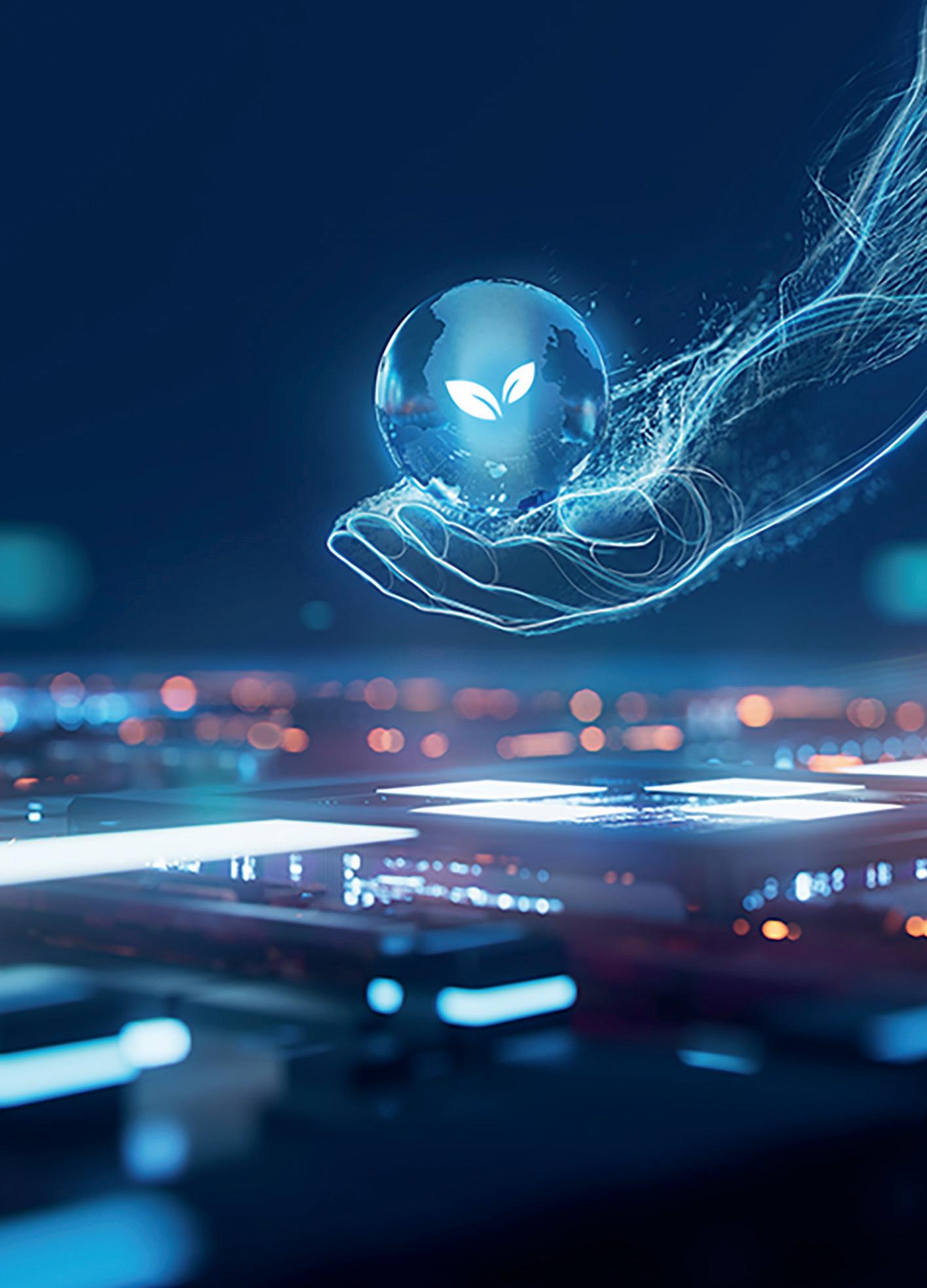
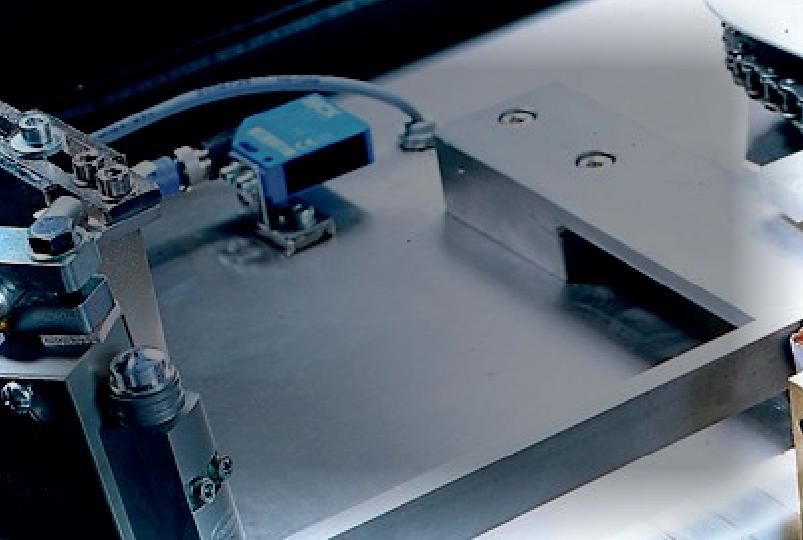

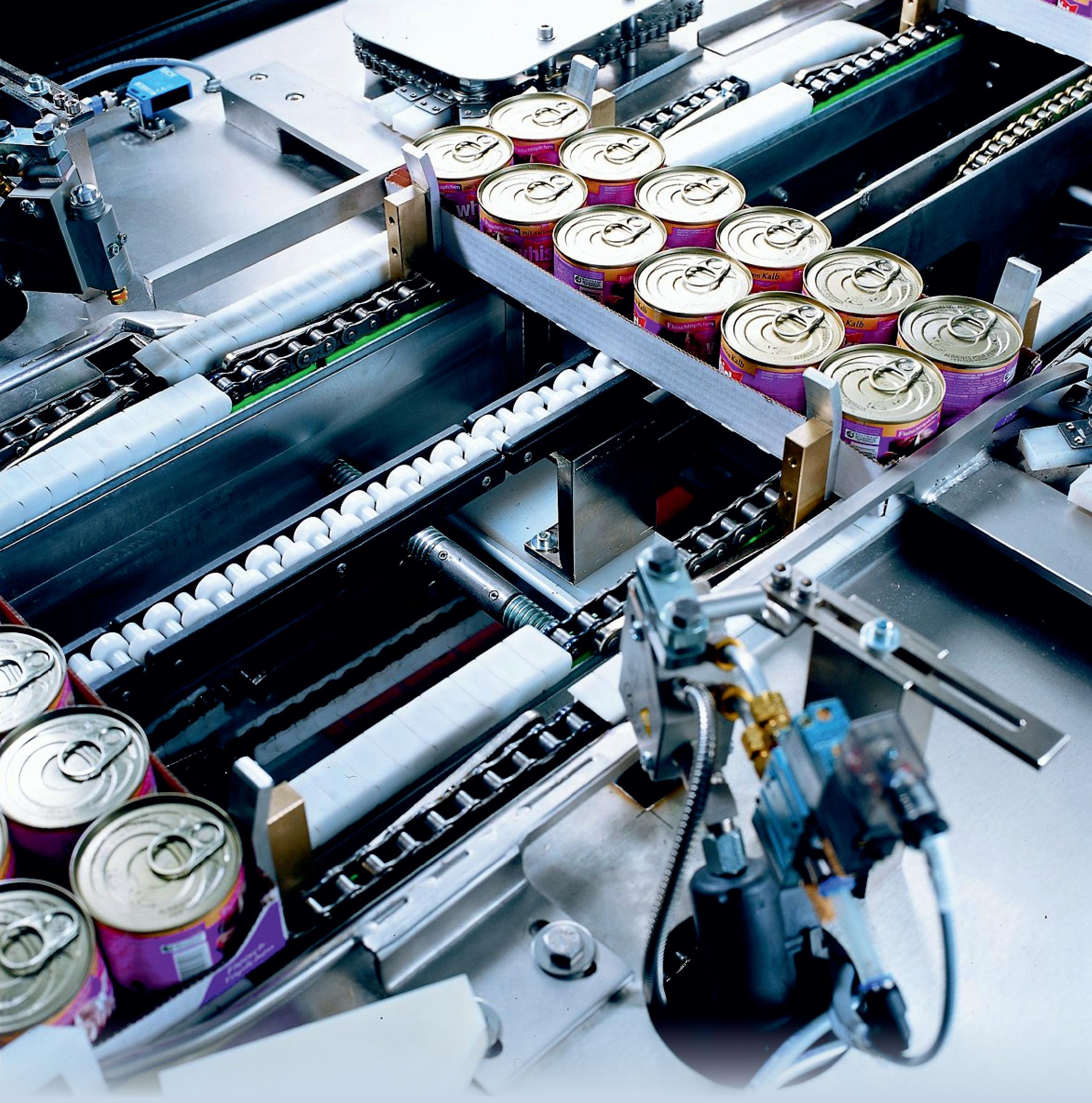
At Cross+Morse we aim to fulfil all industry demands, from the simplest to the highest level of precision required. Our objective is to offer a complete solution - not just products - to your power transmission challenges.
Cross+Morse are known in the industry as pioneers in quality standards, which is why we take our quality control processes very seriously. Quality assurance is central to our organisation with controls encompassing all aspects of design, manufacture, logistics and customer service. We are ISO 9001:2015 accredited and have been for over 20 years.
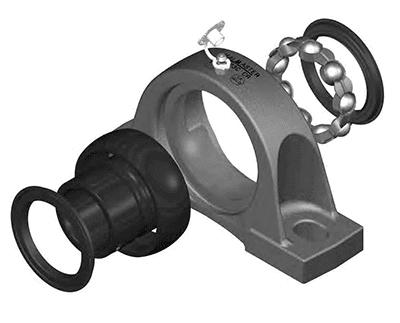
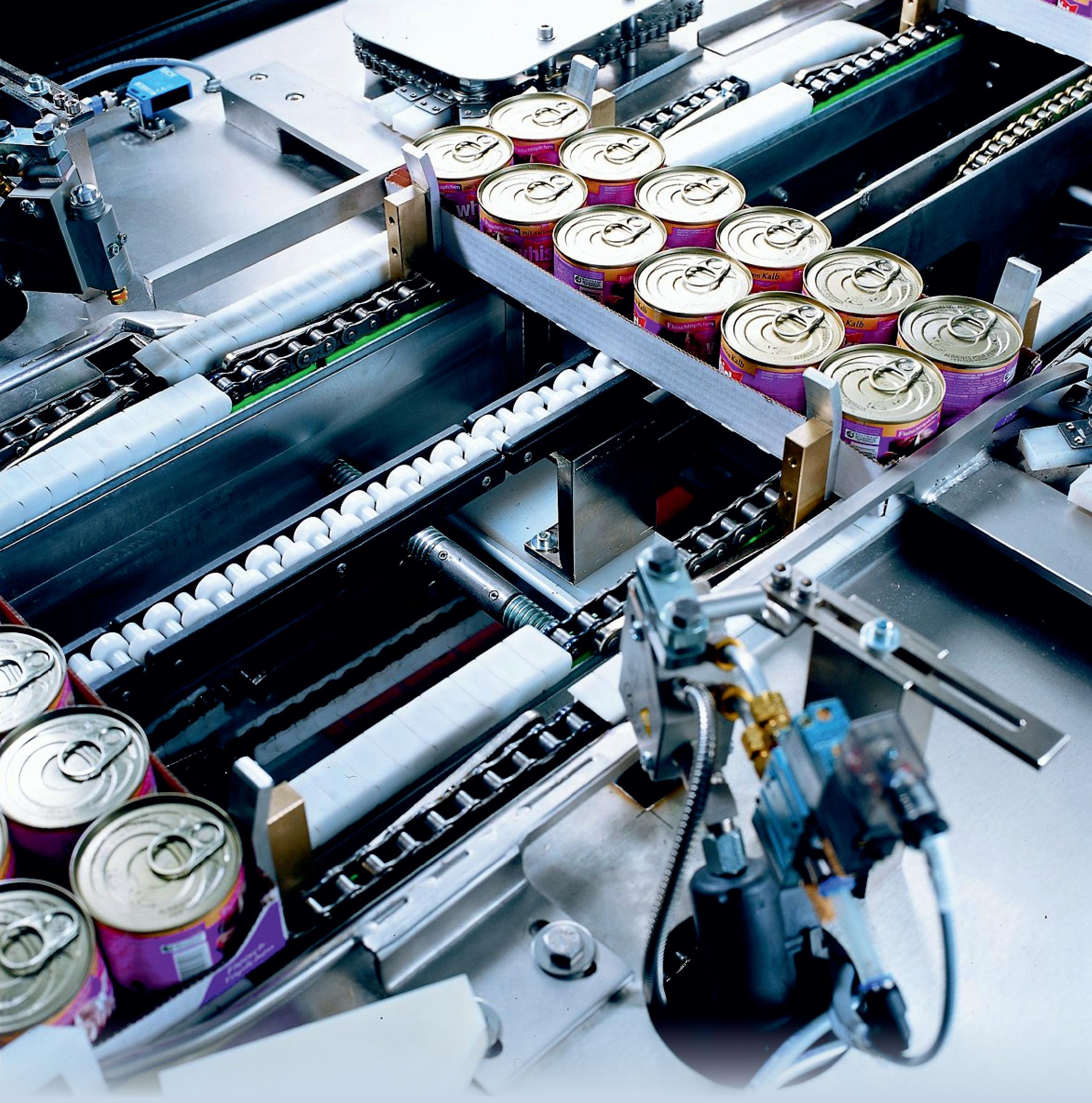
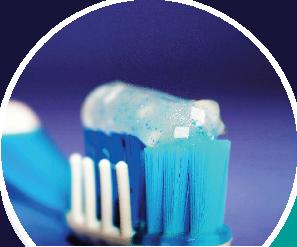
At Cross+Morse we have continuously invested in top of the range measuring equipment: Co-ordinate Measuring Machine (CMM), digital tri-bore gauges and micrometres which are constantly calibrated to comply with ISO standards. Our stringent inspection process guarantees that when manufacturing each operation is thoroughly inspected by either a highly trained shop-floor staff supervisor or an inspector, ensuring that manufacturing is only allowed to continue when each phase has been approved. Our hardening treatment is checked using Rockwell or a Vickers testing machine.
We review our quality procedures continuously to provide up-to-date mechanisms for ensuring conformity to the quality system; different audits are carried out on all activities in the company throughout each year.
Cross+Morse is the largest authorised distributor and stockist for American transmission products manufactured by RegalBeloit (formerly EPT) in the United Kingdom. The range includes Sealmaster®, Browning®, Jaure®, Kop-Flex®, McGill® and Morse®.
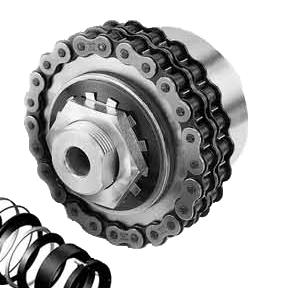
Inverted tooth chain: including the standard SC type from 3/16” to 2” pitch and HV type from 3/8” to 2” pitch; as well as conveyor chains up to 12” width in centre or outside guide construction. We manufacture standard and special sprockets in-house for a complete drive solution.
We pride ourselves in offering a complete range of overload protection devices ranging from the simplest to the most accurate and precise overload clutch: Sheargard range of overload clutches, wedge pin type, available as a chain coupling and the option of low inertia rubber elastic couplings for higher speed drives. The Crossgard range, ball detent type, comes in 3 versions and also available with roller chain and low inertia rubber coupling option. The Safegard CS series, ball/roller detent type, comes in 2 two basic types (standard or mini) and also available as shaft couplings. Series CZ and CN zero backlash Safegard clutches for responsive overload protection, available in both basic and shaft coupling types.
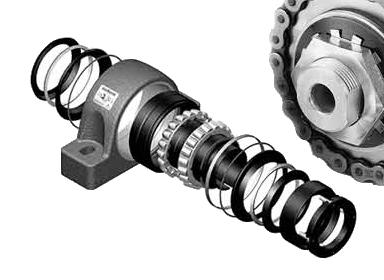
We offer a wide stock range of flexible shaft couplings to accommodate different types of misalignment: Jaw couplings, elastomeric couplings, roller and Delrin® chain couplings, gear couplings GFA & GFAS, polymer gear couplings, Morflex elastomeric disc couplings and Crossflex disc couplings.
Our Crossbore® rework service includes reboring, keywaying and setscrewing of standard sprockets, pulleys and gears in a dedicated production area with specialised CNC machines for a rapid response. Induction hardening of teeth is also offered in-house.
For further information contact:
Shaft clamping elements for precision transmission of torque with no backlash: a complete range from stock.
Our range of Freewheel clutches for overrunning, indexing and backstopping applications; including sprag clutches, industrial ratchet
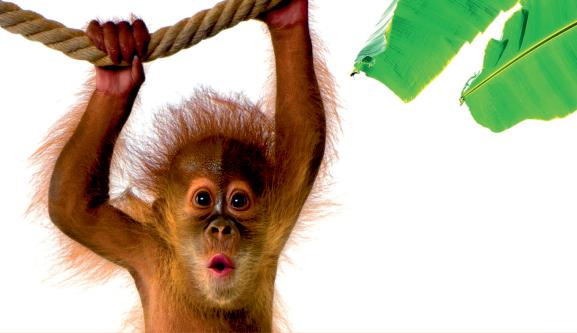
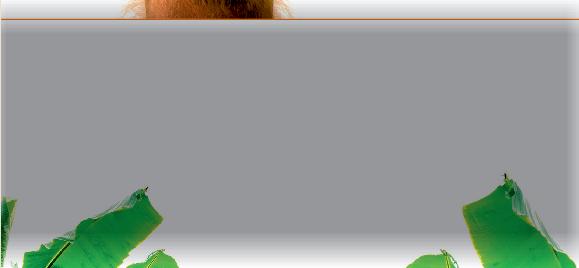
Telephone: +44 (0) 121 360 0155
Email: sales@crossmorse.com or visit www.crossmorse.com
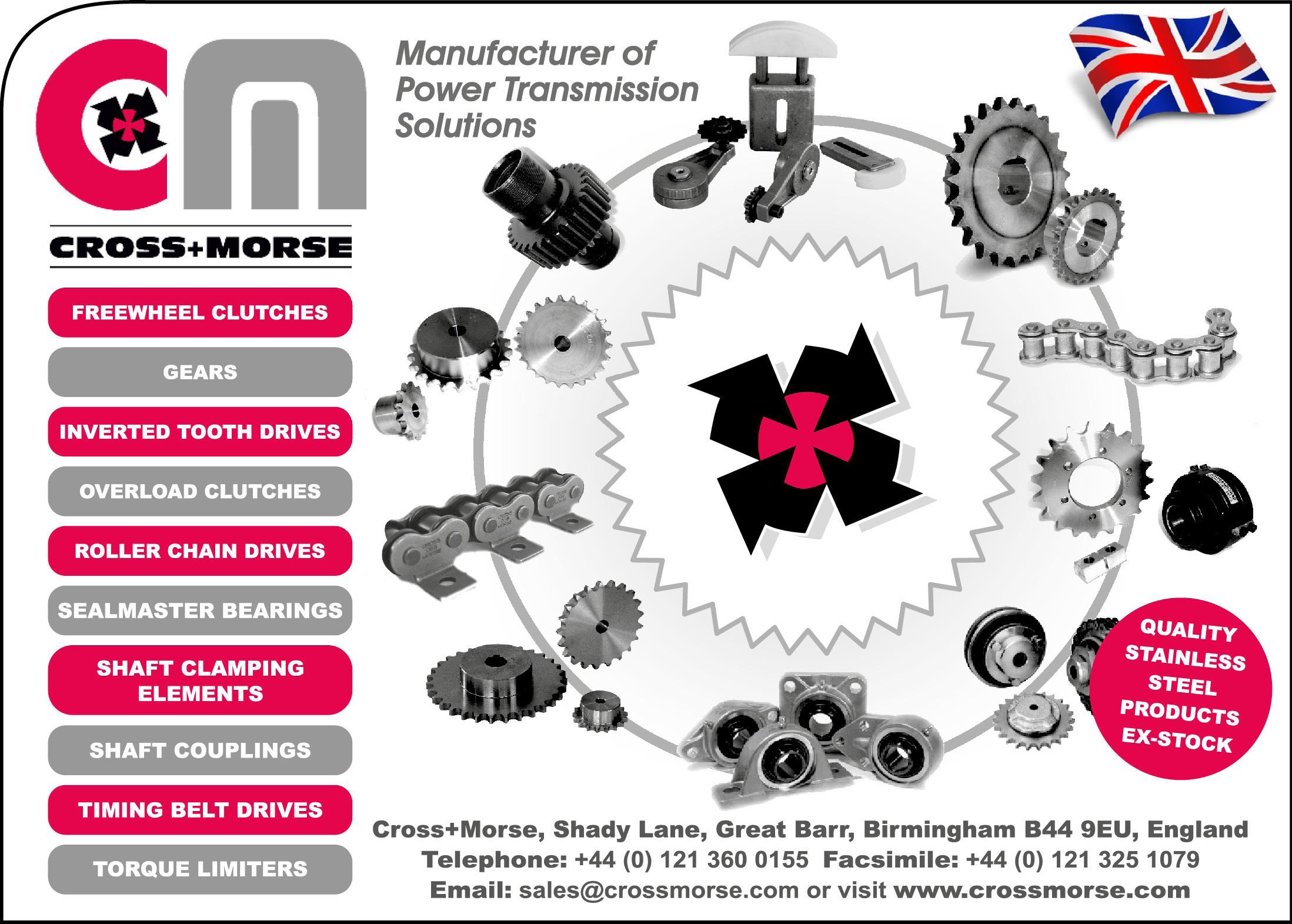

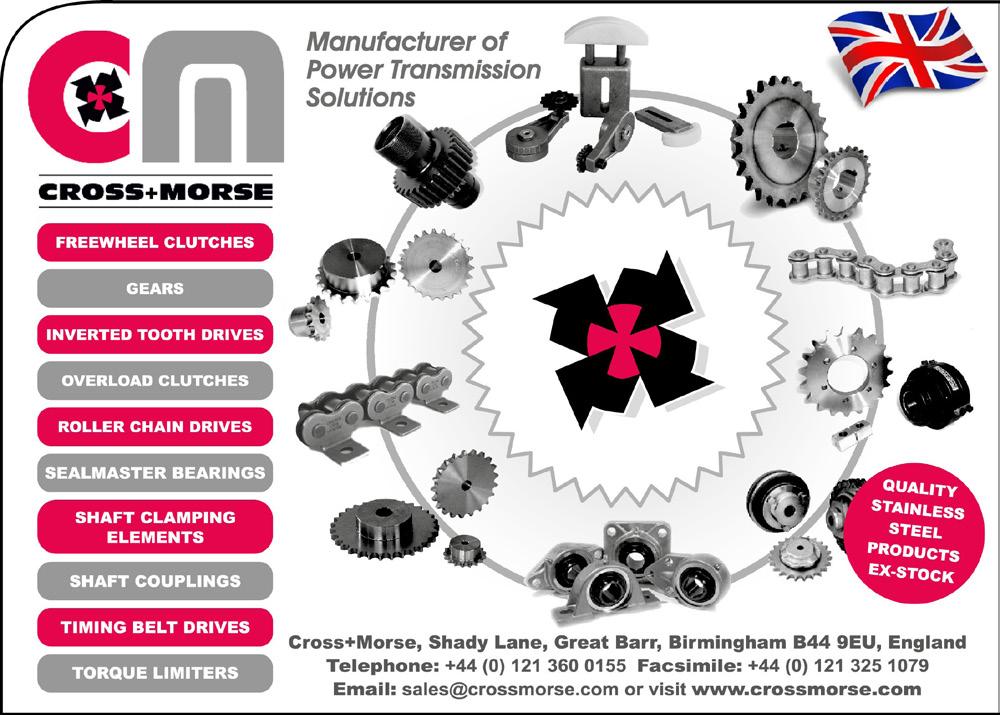
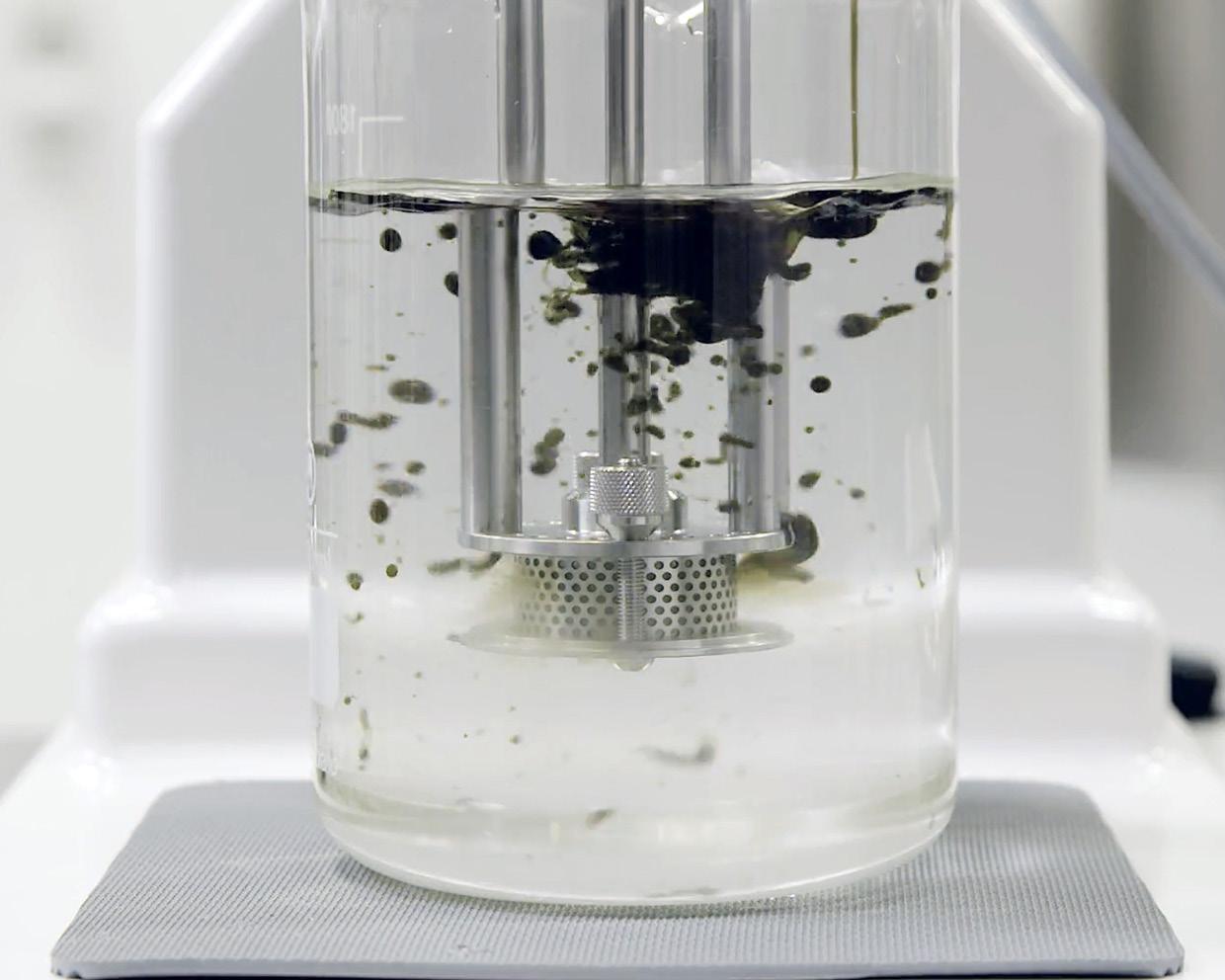
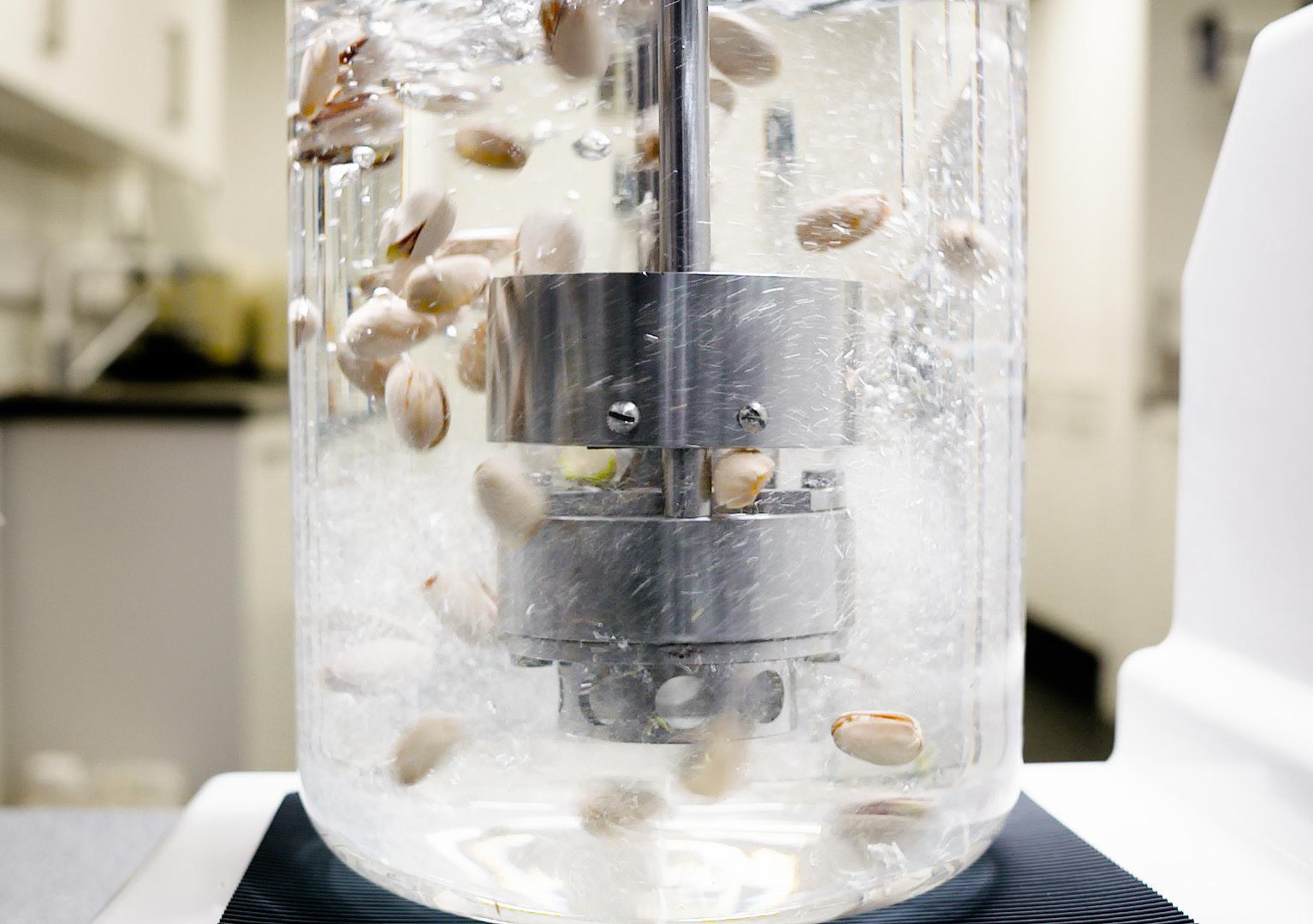