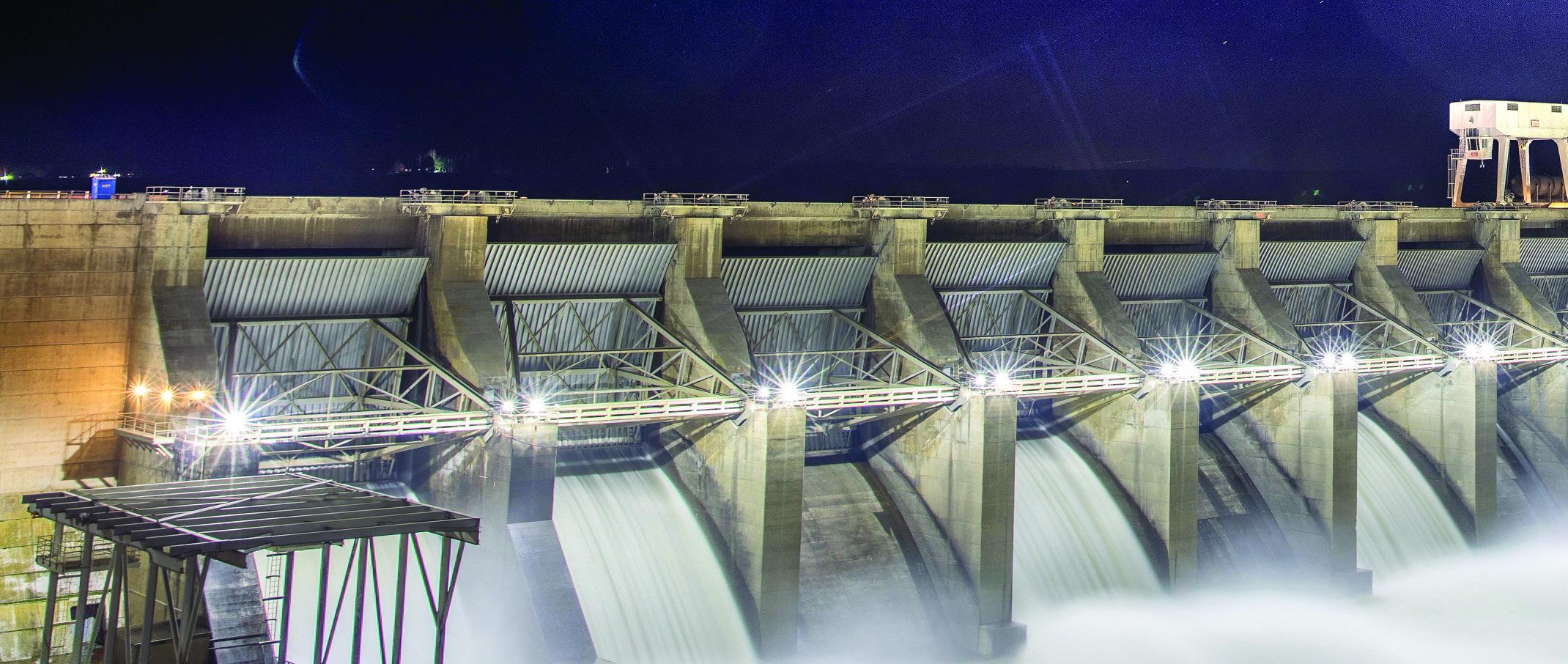
8 minute read
How Voith Hydro Designed Improved-Fish-Passage Turbines for Ice Harbor Dam
Ice Harbor Dam, located on the Snake River near Burbank, Washington.
How Voith Hydro Designed Improved-FishPassage Turbines for Ice Harbor Dam
Advertisement
Over the past few years, Voith Hydro has worked with the U.S. Army Corps of Engineers to design and install several turbines for improved fish passage at the Army Corps’ Ice Harbor Dam, located on the Snake River near Burbank, Washington. In this interview, we speak with Brian Van Baush and Jason Foust of Voith Hydro about what makes a turbine better for fish passage; what the Army Corps was looking for at Ice Harbor; and how Voith worked to design, test, and install the units at the dam.
Hydro Leader: Please tell us about your backgrounds and how you came to be in your current positions.
Brian Van Baush: I work in Voith Hydro’s business development group and have been with Voith for just over 5 years. I’ve been involved with power generation for roughly 25 years. I went to the Naval Academy, and when I left the navy, I went to work in the paper industry; then moved over to General Electric’s industrial group, which supported hydro; and now work at Voith.
Jason Foust: I started at Voith 15 years ago. I work in hydraulic engineering in the contract execution phase for projects. Once a contract is awarded, I’m responsible for the definition of the hydraulic shapes for the runner and the various hydraulic components that are being modified or replaced. That involves a lot of computational fluid dynamics (CFD) modeling and model testing. In addition to those normal hydraulic engineering tasks, I’m also heavily involved with environmental technologies for aeration and fish passage. Hydro Leader: Please introduce Voith Hydro and the range of turbines it manufactures.
Brian Van Baush: Voith Hydro has been in the power generation hydro business for 155 years, and through our acquired companies, Voith has been in North America for 145 years. We have grown over that time period through internal development and the acquisition of other hydropower equipment manufacturers, such as S. Morgan Smith and Allis Chalmers. We design and manufacture Kaplan, Francis, Pelton, and pump turbines. We are also deeply involved in small hydro projects, ranging from 1 to 15 megawatts. We have even developed the Streamdiver, which is a completely encased unit with a capacity of less than 1 megawatt that you can put into a canal.
Hydro Leader: Would you introduce the concept of improved fish passage with reference to turbines? What are the factors that make a turbine better or worse for fish passage? Does this conversation primarily concern the passage through the turbine itself, or are we talking about other factors, such as dissolved oxygen?
Brian Van Baush: Our improved-fish-passage turbine project was developed with the Army Corps over several years. Specifically, we are trying to ensure that fish can pass through the turbine without damage.
Jason Foust: Fish passage is related to how a fish responds to a flow environment. This varies by species, so the main drivers are documented and studied by biologists, and we implement
design criteria for specific fish. For example, pressures within the turbine are important for both conventional turbines and those designed for improved fish passage. However, minimum pressure targets for fish generally differ from the design criterion we would use simply to ensure that the unit doesn’t cavitate. We don’t want the pressures to go so low that the gases in the fish’s body expand too much—kind of like what happens to a diver who comes up through the water too quickly and gets the bends. We also want to avoid rapid pressure changes. Another important design factor has to do with avoiding strikes against the physical structures. A blade striking a fish is another injury mechanism that can lead to mortality. Other factors include shear stress, overall flow quality, and providing uniform flow through the turbine so that the fish are not disoriented when they exit. If they are disoriented, they are easy prey for bigger fish and birds.
Hydro Leader: How do you ensure safe passage for fish through the turbine? Are you altering the speed of the turbine, adjusting its shape, or adding sensors to it?
Brian Van Baush: The main factor is the physical design of the turbine and its blades. Turbines turn at set speeds, so adjusting the speed is not a factor.
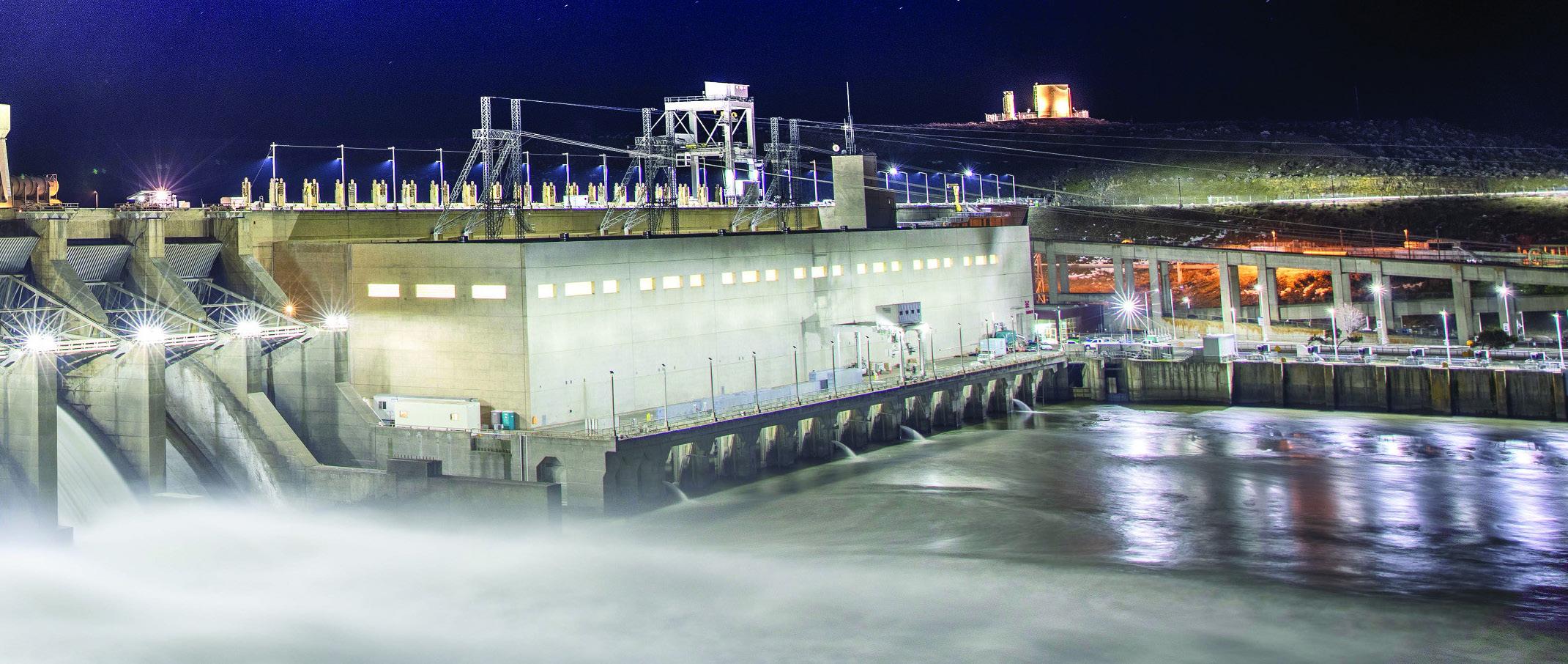
Hydro Leader: Would you explain how Voith came to be involved with the Ice Harbor project and tell us about the requirements that the Army Corps had for that project?
Brian Van Baush: We became involved with the Army Corps primarily because of our base here in North America and the engineering, design, and lab resources we have in York, Pennsylvania. We are the only supplier with a hydraulic turbine development lab in North America.
Jason Foust: The process kicked off in 2010 and was quite long. We were looking at two types of machines for Ice Harbor. There are existing Kaplan turbines at the site whose blades can be adjusted depending on the inlet site conditions and operation goals. As part of the contract with Voith, the Army Corps replaced three of those existing Kaplans, one of which it replaced with a fixed-blade turbine. That being the case, development took place from 2010 to 2015 for two different hydraulic designs. There were quite a few iterations;
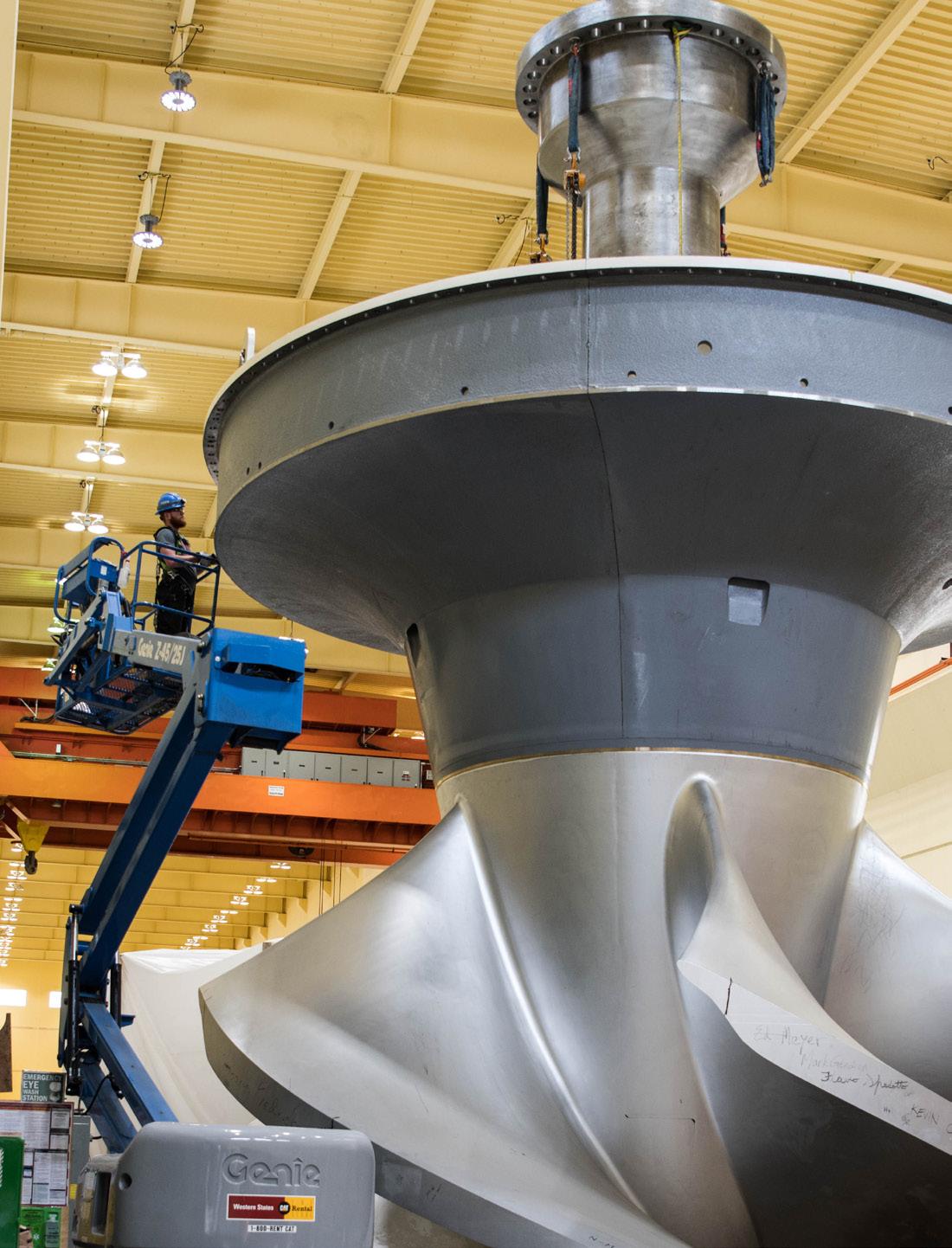
Ice Harbor Dam personnel work to install Voith’s improved-fishpassage turbine runner.
we were very thorough. Design decisions were made together within a small team that included members of the Army Corps, the Bonneville Power Authority, and the National Oceanic and Atmospheric Administration. These decisions were based on what worked best for fish passage. We learned a lot from that process, and I think another similar project in the future could be done faster based on what we learned.
Hydro Leader: Did the Army Corps reach out to Voith specifically, or did you bid on the project?
Jason Foust: There was a competitive bid. We were selected based on our technical solution and on normal factors such as schedule, costs, and experience. We’d had experience with previous fish passage technologies, such as the minimum gap runner and fish passage studies.
Hydro Leader: What was the Army Corps looking for in particular for this project?
Jason Foust: What made Ice Harbor special was that we weren’t just focusing on the flow environment within the runner. We looked at the entire flow passage, starting from the inlet. Analysis of the distributor showed that stay-vane modifications help to align these structures better with the wicket gates across the flow range, resulting in a more streamlined flow path for the fish. We also made changes to improve flow quality downstream of the runner. A lot happens within the runner, but for this project, we were considering the complete flow environment.
Hydro Leader: Would you tell us about the process of research, design, and manufacture that Voith went through?
Jason Foust: It was very detailed. We went through our CFD process, then did a physical model test in our laboratory in York. We did the normal tests for performance, cavitation, runaway speed, and pressure fluctuations and documented the hydraulic characteristics. After that, we took a step we don’t do for every project. The runner and modified hydraulic components were shipped down to Vicksburg, Mississippi, where the Army Corps has its Engineer Research and Development Center. The staff there used the same scale model we used in York, installed our components, and then did fish passage testing. For each iteration, they did bead-strike analysis, velocity mapping, and other visual analyses of the flow characteristics within the turbine. It was important feedback that we incorporated into the next design iteration.
What I think made this project a success was our collaboration with the entire design team. Everyone was involved through the entire design process, reviewing the CFD results, the performance results, and the fish passage visuals. Having this level of engagement from such a diverse team, especially the biologists, helped set the design criteria for the engineers. Brian Van Baush: Testing took place over several years. Part of it was done in the research facilities in York and Vicksburg, where we looked at the design and did model testing. Then we installed the unit into Ice Harbor and tracked fish as they went through and compared survival rates before and after the turbine went into place.
Hydro Leader: What results has the Army Corps seen from the new turbine? What are the differences in fish survival numbers, and have there been any changes in power generation?
Jason Foust: We saw an increase in efficiency that increased power generation by 3–4 percent. Live fish testing was conducted for the fixed-blade unit across the operating range with juvenile Chinook salmon. Direct survival through the operating turbine was documented to be 98.25 percent. The Pacific Northwest National Laboratory also passed sensor fish devices, which measure pressure, acceleration, and other quantities within the flow field, through the turbine during operation. The sensor fish validated the fixed-blade design analysis that indicated that near-zero barotrauma mortality is expected for passage through the fixed-blade runner. The adjustable blade runner should be field tested for fish passage later in 2022, following the installation of the turbine.
Hydro Leader: To what degree does this turbine provide a model for future improved-fish-passage installations?
Brian Van Baush: All turbines are site specific, but the design of the turbine and the blades can play a role in the design of the next unit for other powerhouses in other areas.
Jason Foust: I think what Ice Harbor demonstrated is that there is a process that allows you to provide the best of both worlds: good power and efficiency and excellent fish survival. There’s always been an interest in fish passage as an environmental concern. I think that is gaining momentum, and I hope that Ice Harbor is a case study that we can point back to. H
Jason Foust is a principal hydraulic engineer at Voith Hydro. He can be contacted at jason.foust@voith.com.
Brian Van Baush is a business development manager at Voith Hydro. He can be contacted at brian.vanbaush@voith.com.