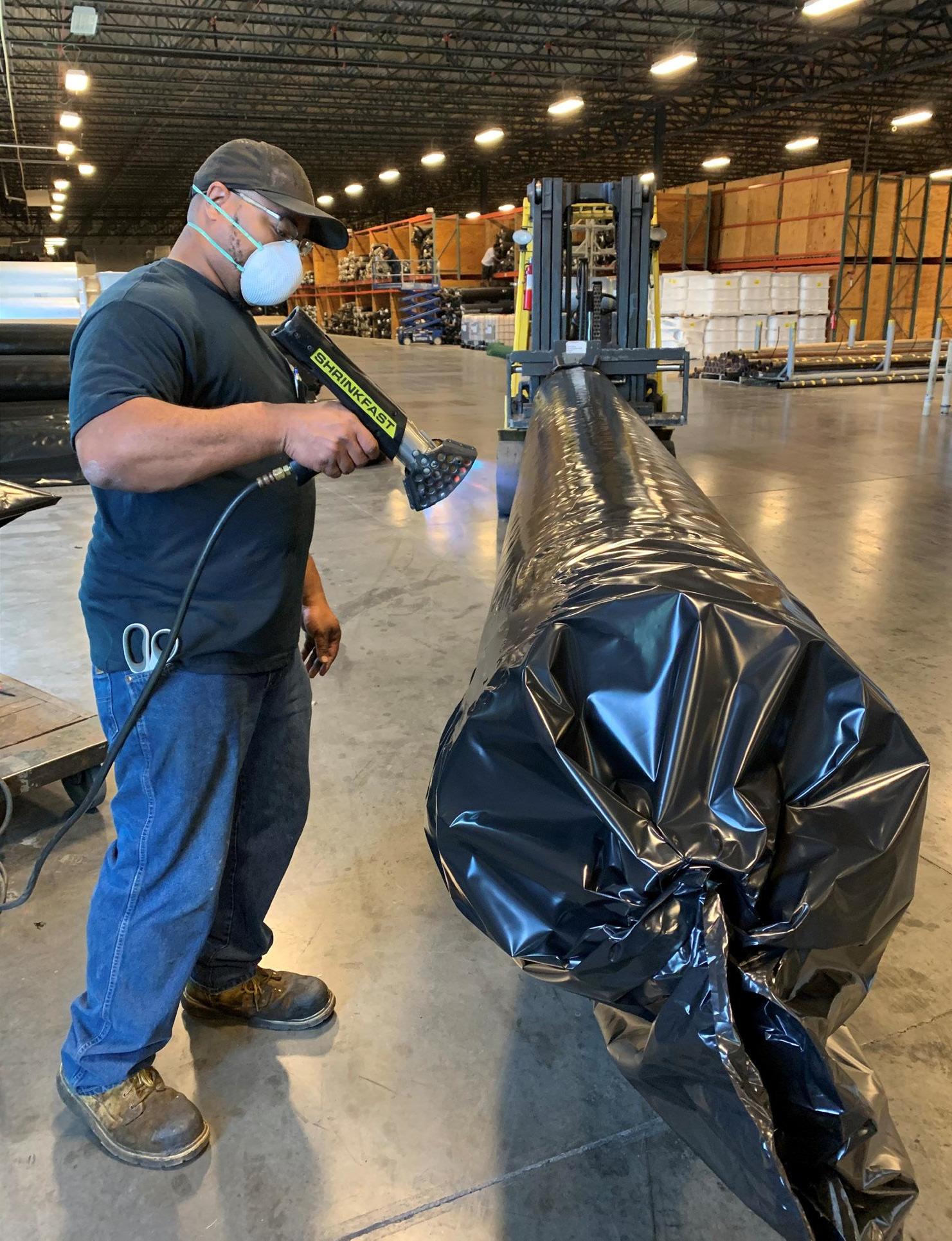
4 minute read
Roy McClinton, HUESKER, Inc.
Roy McClinton, HUESKER, Inc.

A HUESKER employee uses a heat gun to shrink wrap a product.
PHOTOS COURTESY OF HUESKER.
Advertisement
The HUESKER Group is one of the world’s leading manufacturers of geosynthetics and agricultural and industrial textiles. Its products and services provide solutions for projects in earthworks and foundations, roads and pavements, environmental engineering, hydraulic engineering, industry, and agriculture. In this interview, Roy McClinton, the technical sales director of HUESKER, tells Irrigation Leader about the changes that have been implemented in the company’s operations to ensure that it can continue to provide its vital services.
Irrigation Leader: Please tell us about yourself and about HUESKER.
Roy McClinton: I am the technical sales director of HUESKER in North America. I’ve been with HUESKER for 22 years. I started my career with HUESKER handling subbase reinforcement and HaTelit, our asphalt paving products. In 2004, I moved to our geocomposite division, and in 2019, I was promoted to my current position. HUESKER is a family-owned company that has been in business since 1861 and has been based in Charlotte, North Carolina, since 1991. We are active in the United States, Canada, Mexico, and Central America.
Irrigation Leader: How has the COVID‐19 pandemic affected your operations?
Roy McClinton: COVID‐19 has affected many industries, and manufacturing is not immune. Infrastructure, construction, and agriculture are driving forces behind economic growth and provide essential services to the nation. This means that our production is more important now than ever. Fortunately, HUESKER has always had a policy of putting the safety and health of our employees first, so we were well equipped to effectively respond to the situation.
Irrigation Leader: What are some things that you’ve done to keep your customers and employees safe?
Roy McClinton: We are actively monitoring the temperature of all employees before their shifts begin. Anyone with a fever is not allowed to clock in and is required to remain home until they recover. Each week, the company is providing all employees with promotional-size bottles of hand sanitizer that we had on hand for use at trade shows. In addition, all employees are provided with face masks to use both on and off the job. Extra pay and sick time are being provided for all employees to ensure that they can care for their children or family members without suffering financially.
We are keeping departments separated from one another as much as possible. Within departments, employees are required to keep 6 feet of distance from each other unless absolutely necessary. Shifts are staggered to ensure that if any employee is infected, exposure is limited to their shift only. Weekly meetings between management are now being held out in the open and in a much more relaxed and distant setting.
Weekly plant socials and gatherings are now held outdoors, weather permitting, or in our large warehouse area. The company believes it is important that we maintain our sense of community and family by continuing to hold these plant socials each week, but we want to ensure that it is done safely and according to guidelines. Whereas buffet-style foods normally would be served, meals are now prepackaged to avoid any contamination.
Finally, we are also being more conscientious about how our products are handled. There is no reason for five people to touch one roll to get it from production to the customer. We are relying heavily on our forklift operators to move material so that employees do not have to do so with their hands.

A HUESKER employee checks a fellow employee’s temperature before he enters company premises.
Irrigation Leader: What is the most innovative thing you have done to maintain workflow and safety?
Roy McClinton: I would have to say it is the process we initiated to begin heating the plastic that we wrap our product with. Before, rolls of material would be loosely bound within a plastic cover wrap. Now, however, we are in effect shrink wrapping our products using heat guns, yielding a more tightly sealed package that is more compact and easier to handle. This allows less contamination to penetrate the product, and the process kills any active virus on the outside of the material.
Irrigation Leader: Do you expect any of the changes you have made to be retained after the pandemic is over?
Roy McClinton: A lot of the measures do not affect our ability to efficiently produce quality products. The separation of departments has allowed us to streamline certain processes and remove distractions. I think keeping the departments separated has had a positive effect on our facility. This is especially true for management meetings, in which we would previously spend too much time discussing small issues. Going forward, keeping these meetings straightforward and to the point will make our communications more efficient. Working in manufacturing is not always a clean job, but we would also like to maintain our focus on the importance of hygiene and health.
Irrigation Leader: What is your advice for other businesses?
Roy McClinton: My advice for other businesses and agencies is always to put your employees’ security, health, and safety first. It is important to let employees know that their jobs and paychecks are secure. This reduces the risk that a sick employee will come to work and infect others. Sales and production can always recover, but employees are a company’s most valuable asset. If all your precautions work as they should, it will seem like they were unnecessary.

Roy McClinton is the technical sales director of HUESKER in Charlotte, North Carolina. He can be contacted at rmcclinton@huesker.com or (704) 927‐7908.