
3 minute read
Jerry Gibbens
Director of Operations Northern Water
Berthoud, CO
Advertisement
Irrigation Leader: How many vehicles and pieces of equipment does your district own?
Jerry Gibbens: Northern Water’s fleet contains 19 sedans and SUVs, 46 light- and medium-duty pickups, 36 heavy-duty through tandem-axle dump trucks, 42 trailers and pieces of small equipment, and 24 pieces of heavy equipment. For reference, about 60 of Northern Water’s approximately 165 staff are directly involved in the day-to-day operation and maintenance of water infrastructure and facilities. We have developed a long-term fleet modernization plan based on historical, current, and future needs. With current economic conditions and with multiple emergencies in recent years that have affected availability and price in the rental market, we have decided to acquire several pieces of equipment that we previously rented, including a new semitractor and lowboy, two new excavators, and several other smaller pieces of equipment.
Irrigation Leader: What kind of maintenance is required for your vehicles and equipment?
Jerry Gibbens: We have a 10,000-square-foot fleet maintenance shop at our Berthoud headquarters campus staffed by one mechanic and one fabricator who provide full services on vehicles every 3,000–5,000 miles and on equipment every 100 hours or per manufacturer’s recommendations. We also have a newly constructed shop of approximately the same size at our new Willow Creek Campus, which is located near Granby, on the west slope of the Continental Divide. Our staff can perform routine maintenance, conduct most repairs (those that aren’t under warranty), replace tires and consumables as required, perform minor interior and exterior body repairs and specialized fabrications, perform new vehicle make-ready setups, and perform Department of Transportation inspections. Each of our campuses also contains newly constructed fuel islands and wash bays.
Irrigation Leader: What kinds of records do you keep of that maintenance?
Jerry Gibbens: All maintenance requests and records are entered, tracked, and stored in our Maintenance Connection enterprise asset management system. Staff track vehicle mileage and equipment hours by activity for each unit to ensure that the appropriate funding source pays for those uses according to a standard rate schedule. Based our experience in seeking Federal Emergency Management Agency disaster recovery grant funding (particularly our experiences in the 2013 Colorado Front Range floods), we consider it extremely important to ensure that staff time, expenses, and vehicle usage are consistently and accurately tracked.
Number of employees: 165 Size of service area in acres: 1.6 million; about 600,000 irrigated
Amount of water diverted per year for irrigation in
acre-feet: 220,000 diverted on average with about 50 percent used for irrigation Main crops irrigated: Alfalfa, corn Predominant irrigation methods: Flood, pivot
Irrigation Leader: How do you buy or bid for equipment?
Jerry Gibbens: Equipment replacements and additions are incorporated into our annual fleet capital budget. Once that budget is approved, our facilities and equipment department creates a specification for each unit. We first seek to use our eligibility in the Colorado Multiple Assembly of Procurement Officials, which is a statewide cooperative purchasing program. If vehicles or equipment are not available through that program (which is more common for equipment, especially specialized heavy equipment), we investigate availability through other intergovernmental purchasing agreements, including through the U.S. General Services Administration, or we issue a request for quote. More recently, because of the nationwide shortage in vehicle availability in all programs, we have made a few off-the-lot purchases of vehicles and smaller equipment.
Irrigation Leader: How long do you use your vehicles and pieces of equipment before replacing them?
Jerry Gibbens: Consistent with our long-term fleet modernization plan, sedans are typically replaced after 80,000 miles; SUVs after 95,000 miles; and pickups between 95,000 and 140,000 miles, depending on age and condition. Through financial analyses developed during our fleet modernization plan, we identified a 7- to 10-year replacement schedule for all large trucks and equipment. We found this was the ideal replacement schedule to leverage buying power through the various purchasing programs and resale value. IL
Jerry Gibbens is the director of operations at Northern Water. He can be contacted at jgibbens@northernwater.org.
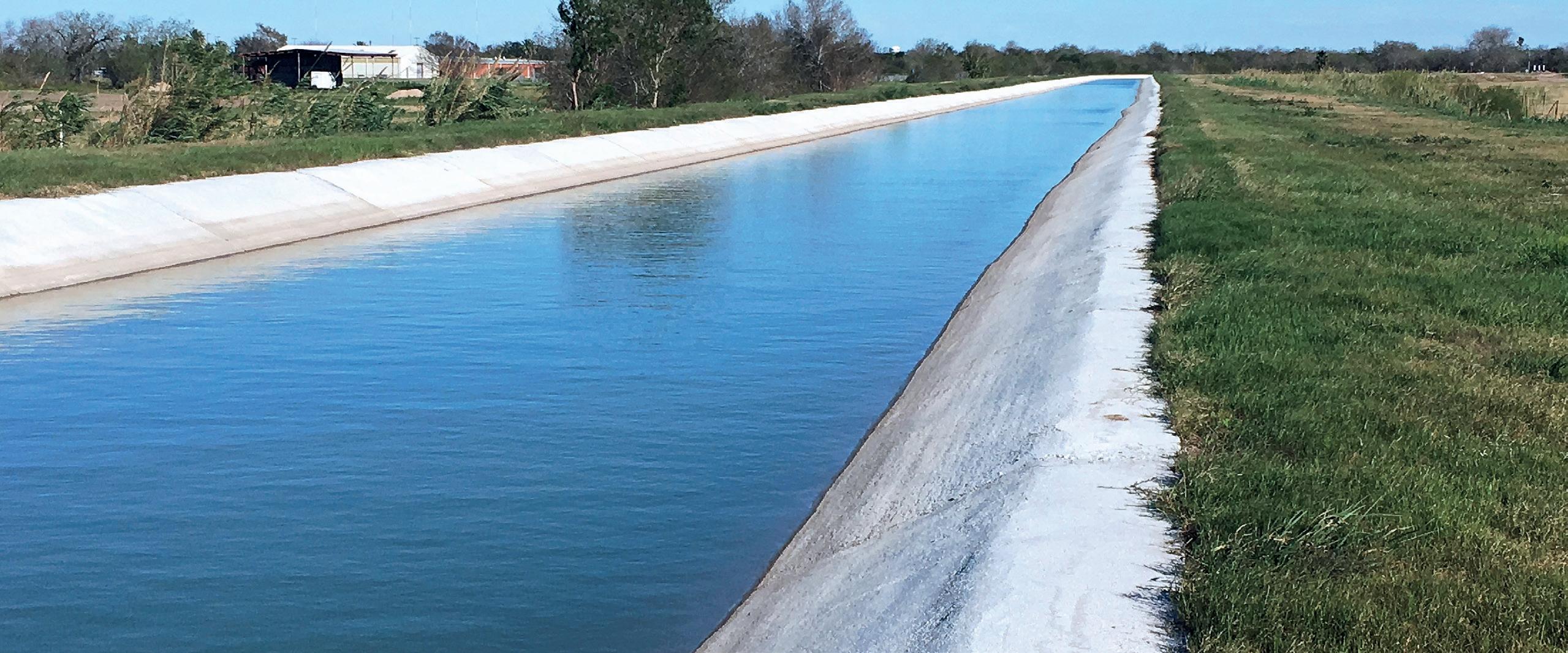
EVERY DROP COUNTS
HUESKER Canal3

Canal3 provides durable sealing, and excellent erosion protection with superior puncture resistance for various site conditions. Irrigation districts and contractors agree that this Made in America product saves you time and money thanks to faster installation with less seams due to wide width rolls.
MADE IN USA FASTER INSTALLATION HIGH DURABILITY TIME & COST SAVINGS
Get in touch: 1-(704) 588 5500 3701 Acro Corporate Dr. Charlotte, NC, USA www.HUESKER.us marketing.us@HUESKER.com