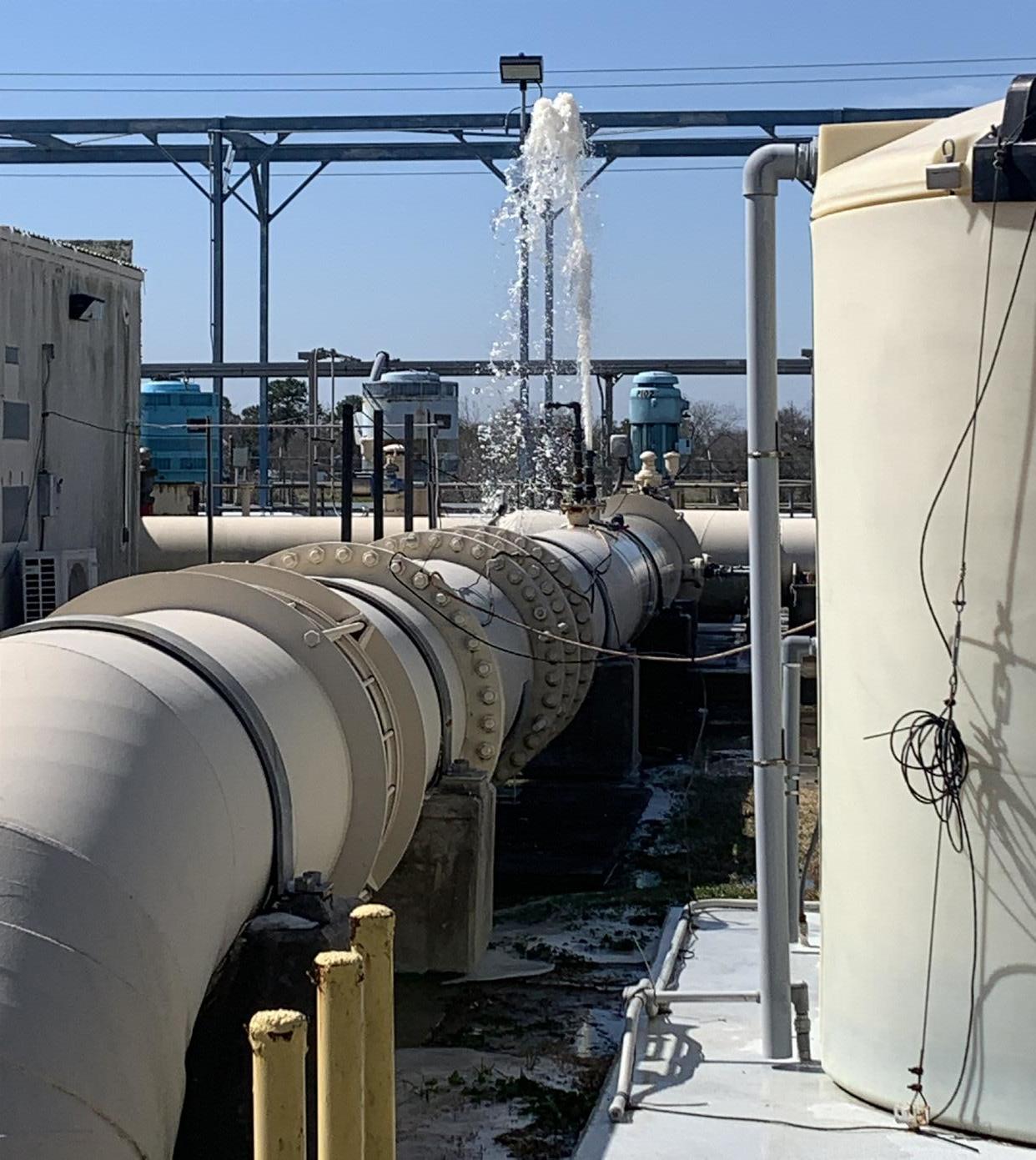
7 minute read
How the Gulf Coast Water Authority Performed Above 100 Percent Capacity During the February Storm
The Gulf Coast Water Authority (GCWA), headquartered in Texas City, Texas, provides wholesale water to Brazoria, Fort Bend, and Galveston Counties. During this February’s winter storm, the GCWA never lost power and operated at more than 100 percent of its rated capacity. In this interview, Jake Hollingsworth, the GCWA’s chief of staff, tells us about how the agency managed this impressive feat.
Municipal Water Leader: Please tell us about your background and how you came to be in your current position.
Advertisement
Jake Hollingsworth: I’m the chief of staff for the GCWA. I’m responsible for strategic planning and ensuring the organization stays on mission to reliably deliver water to our customers. Since coming to the GCWA in 2016, I have served as the strategy and performance manager and as the water plant manager. Prior to that, I was the assistant director of utilities for Bay County Utilities in Florida. There, I was responsible for a 60‐million-gallon-a-day (MGD) surface water plant as well as the distribution system and the wastewater system. I got into the water business after college and haven’t looked back. I really like the water industry—I feel like there’s always something new to learn.
Municipal Water Leader: Please tell us about the GCWA.
Jake Hollingsworth: The GCWA was established in 1965 by the Texas Legislature to deliver wholesale water to industrial, agricultural, and municipal users in Brazoria, Galveston, and Fort Bend counties. As a wholesaler, we do not provide directly to households. Our customers are the 13 municipalities we provide with drinking water. Through them, we serve about 200,000 people. Overall, we can deliver up to 200 MGD of water from the Brazos River to support agriculture, industries, and municipalities.
Municipal Water Leader: Please tell us about the GCWA’s experience with the February winter storm and the effects it had on your infrastructure and services.
Jake Hollingsworth: We did not have any critical failures due to freezing in our plant system. There was nothing that affected our ability to produce safe drinking water. None of the pipes inside our buildings burst, just a few water supply lines to chemical tanks that are used for flushing. That’s a credit to our operations staff, who are the best in the business. We were 100 percent operational the entire time. Sometimes, we were more than 100 percent operational, meaning that we were actually pumping more water than we were contracted for. Our plant is rated at 57 MGD, but our peak flow during the storm was at least 62 MGD at moments.

A low lift leak on an ancillary raw water line.
Winter is when we do a lot of plant maintenance, and one of the biggest challenges was that at the beginning of the event, one of our clarifiers was out of service for painting, coating, and the kind of maintenance we do every 4–5 years. That one clarifier accounts for 30 percent of our plant capacity by itself. We called our operations personnel and the contractors we had working on that job at 2:30 a.m., and within 45 minutes, they were there pulling all their equipment out. That job normally takes days to do correctly, but we put that clarifier back in operation within 10 hours of that phone call. Our personnel and contractors did an immense amount of work in some really bad weather conditions. Our canal division personnel came and helped the water plant operators, maintenance crew, and contractors get it all done. Getting the clarifier running in 10 hours was a big deal. It speaks volumes about the teamwork mentality that we have in our organization.
Municipal Water Leader: Did you lose your normal power supply?
Jake Hollingsworth: We never lost power, thanks to a public-private partnership with a company called Enchanted Rock. It owns a bank of generators on our site, and we contract with it to provide power to us. It had those generators running the entire time. Not only was it supplying us with power, but it had the ability to produce excess generating capacity that fed back into the state grid. After Hurricane Ike in 2008, the biggest problem we had was loss of power and getting the plant back up. That event is what inspired us to establish that partnership and put in those generators.
Municipal Water Leader: During the storm, did you see unusual changes in water demand?
Jake Hollingsworth: Water demand was at the highest level the plant has ever seen. Our customers were pulling more than their contract quantities pretty much across the board. It took a lot of effort and communication to make sure that we were sending water where it was most needed.
Municipal Water Leader: What interaction did you have with other agencies during the storm event?
Jake Hollingsworth: Our operations personnel were in constant communication with our 13 municipal customers, telling them the status of the plant and sending water to parts of the system with the most need. We were also providing some updates to the public via Facebook and communicating with local newspapers to make sure that the right information was getting out. Thanks to this work, the public knew that our water plant was still operating at 100 percent capacity.
Municipal Water Leader: Would you tell us about your emergency preparedness work and how it helped you in this situation?
Jake Hollingsworth: A crisis like the one we had in February puts a big strain on the system. The entire state of Texas freezing is something extremely unusual. Fortunately, we do massive amounts of preparation and planning. The operational staff at our water treatment plant and elsewhere in our organization do a phenomenal job of training, making sure they’re ready for every circumstance. We train to be able to run our plant manually, without our computer system. We do extensive emergency response planning, including tabletop exercises and lots of what-if scenarios at the water plant.
We learned a lot from the freezes we experienced from 2018 to 2020. We have heat tanks and heat lamps on our critical infrastructure. At the start of each winter season, the staff carry out a freeze protection check, a practice we established from experience to protect our assets. We make sure all the heat tracing and taping protections are plugged in and functional. We put in pipe insulation and wrap exposed pipe, heat components, valves, and anything else that needs to be protected from freezing. That prior planning is why we kept ourselves operational when a lot of people did not.
Municipal Water Leader: What changes might you make to your emergency preparedness measures to prepare for similar events in the future?
Jake Hollingsworth: Historically, we have not spent a lot of time considering how to treat a freeze event. We have a massive hurricane preparedness plan that we’ve gone over again and over again. We are now thinking we need to do the same thing for freeze events. We need to start using a National Incident Management System approach and making sure that 3 days out from the event, we’re starting to call and prepare our rideout crew—the group that stays at the plant until the event has subsided. We did not do that in this case because we had never dealt with a freeze that lasted as long as this one. We’ve learned that we have to staff our plant the same way during a freeze that we do during a hurricane event. We don’t want to have to worry about people going back and forth from home to work. We want to make sure that they’re safe. We also want to make sure that we’re not overworking people. We don’t want people working 16‐hour shifts.
Municipal Water Leader: Are there any infrastructure changes that you may want to make in response to this event?
Jake Hollingsworth: We are looking into whether we need microgrids with electrical generation elsewhere. We don’t have anything specific in the plans at the moment. We didn’t lose power at all, so we don’t foresee the need to make huge changes. We just need to focus on what we’re doing well.
Municipal Water Leader: Is there anything you would like to add?
Jake Hollingsworth: Our employees did a wonderful job. Like a lot of people in the area, they weren’t just dealing with problems at work. They were dealing with issues in their homes, such as bursting pipes. I can’t give them enough credit for dealing with all that and doing the wonderful job they did.

Jake Hollingsworth is the chief of staff at the Gulf Coast Water Authority. He can be contacted at jhollingsworth@gcwater.org.