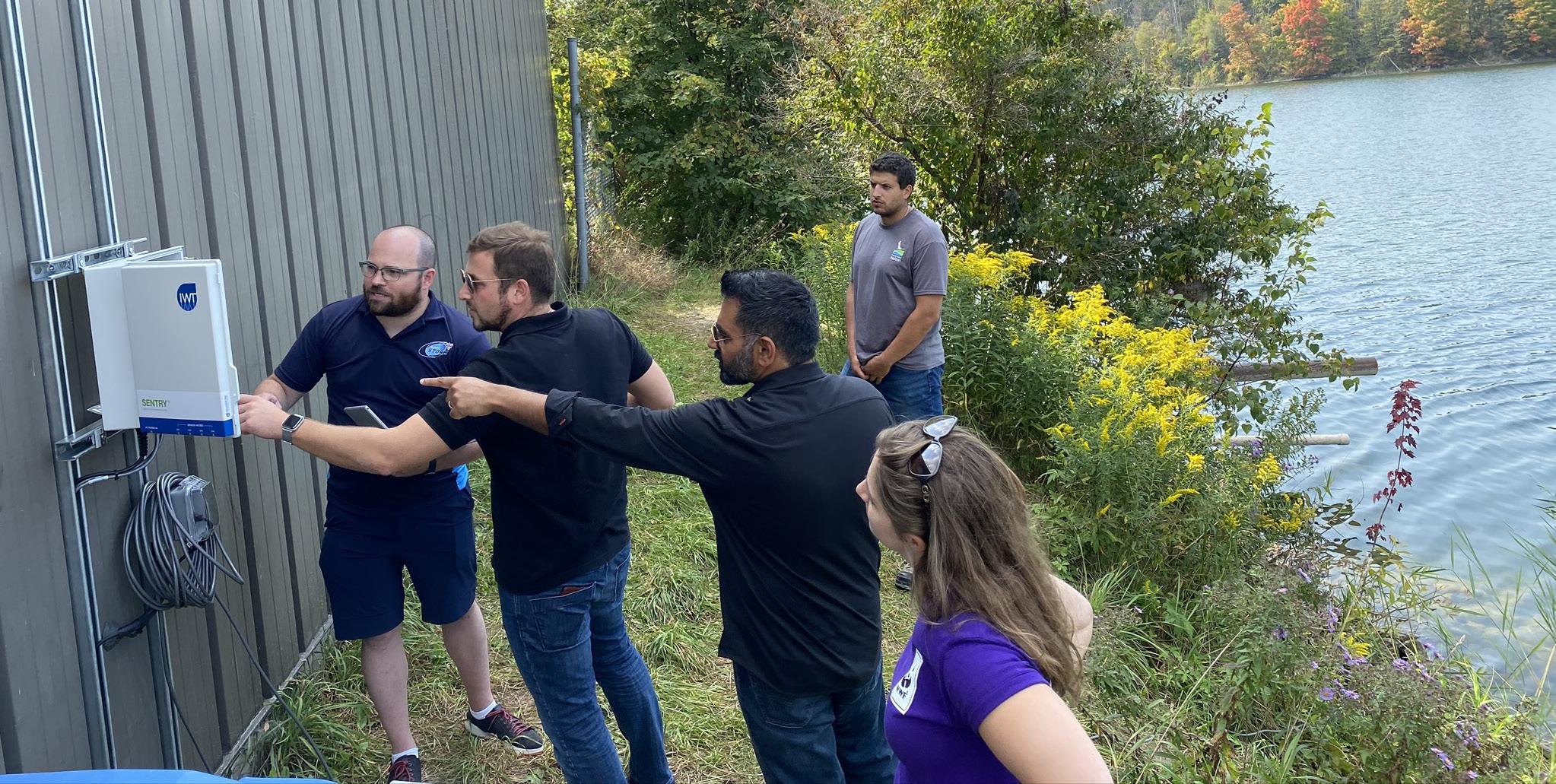
9 minute read
Jonathan Grant: Striking a Better Balance for Wastewater at SENTRY

A SENTRY system is installed at Kelso Lake.
Having accurate and consistent data is vital for overcoming the challenges faced by wastewater treatment plants, but most monitoring techniques are either vulnerable to fouling or slow. SENTRY’s new bioelectrode sensor avoids both problems. The product improves the monitoring of microbial balance, toxic shock events, and other factors that impede effective wastewater management. In this interview, Jonathan Grant, SENTRY’s chief commercial officer, tells Municipal Water Leader how the product was developed, the benefits it provides customers, and the effect the technology is having on wastewater management around the world.
Advertisement

The SENTRY probe.
Municipal Water Leader: Please tell us about your background and how you came to be in your current position.
Jonathan Grant: I wound up with SENTRY because I’ve been consulting with and working with startups for the past decade. I’ve been with SENTRY for about a year and a half. My real strength is in helping companies take an interesting technical idea and turning it into a value-driven message that a layman can understand. I consulted for a number of innovative earlystage companies. Before that, I was with a startup artificial intelligence company that was acquired, and prior to that I was at a water technology accelerator called WaterTAP.
Municipal Water Leader: Of your previous ventures, how many were water related?
Jonathan Grant: All have been water related. At WaterTAP, it was my job to understand who was doing what in the Ontario water sector, and then help them grow globally. I spent 4–5 years traveling the world, going to every conference, and helping those companies out. That’s how I met Patrick Kiely about 8–9 years ago.
Municipal Water Leader: Please tell us about SENTRY.
Jonathan Grant: SENTRY started off about 8 years ago as part of Patrick Kiely’s company Island Water Technologies, which he developed to create innovative water technologies. It’s based on his postdoctoral research into microbial fuel cells. The company has about 12 employees and is growing. We have about 80 clients. At this time last year, we had about 25, so it’s been quite a rapid growth. About half are municipalities; the other half are industrial users in the pulp/ paper, food and beverage, and petrochemical industries. In terms of municipalities, we’ve been installed everywhere from a town of 3,000 in Prince Edward Island called Montague all the way up to Chicago’s Metropolitan Water Reclamation District. We’re now on every continent. We’re installed at the Basic Sanitation Company of the State of São Paulo in Brazil; the Singapore Public Utilities Board; the San Francisco Public Utilities Commission; and a number of utilities in the UK, including United Utilities and Wessex Water.
Municipal Water Leader: Please tell us about your product.

The installation of a SENTRY probe.
Jonathan Grant: Rather than trying to generate energy from biology, Patrick flipped the concept on its head. What we do is apply a small voltage to a flat surface on which biofilm grows, and as carbon is consumed by the biology growing on the sensor, it respires electrons. We essentially measure that respiration. If there are a lot of organics, as in a brewery discharge, there’s more carbon to be consumed, and the biofilm respires more. If there’s a toxic shock from chemicals or something like inflow and infiltration, it reduces the available carbon and there will be less respiration. Our device is kind of like a heart rate monitor for your biology’s ability to treat incoming wastewater.
The probe is built to live in wastewater, so it can be placed anywhere. We can help at every point in the process, but right now our standard practice is to start at the primary clarifier and then move on to optimize a specific process. The primary clarifier is where 85 percent of our clients start. Clients love to identify and understand what’s coming into their plants while they still have time to act on that information. Our typical deployment is a 6‐month pilot with clear success criteria, so that the end user isn’t putting time and effort into something that won’t lead to value. Upon success, there are two options for expansion: either we can go out into the collection system, find industrial discharges, and put probes there, or we can go into the plant and optimize a process like anaerobic digestion, aeration optimization, or supplemental carbon dosing.
Municipal Water Leader: Do you have two types of probe, one that can be installed in a pipe and one that is inserted directly into a body of water?
Jonathan Grant: It’s the same probe; where it is placed depends on the location and configuration of the plant. It’s easy to screw into a pipe with 1½‐inch threading or to attach to an aeration basin or a primary clarifier. It installs pretty much like a diffused oxygen probe or a pH probe.
Municipal Water Leader: Where precisely in a plant should the probe be positioned?
Jonathan Grant: The ideal place for our probe is at the front end of a plant, right after a screen, so that it doesn’t get debris on it. The ideal setup is to put one at the front and one at the back of the primary clarifier. That way, users can actually see the shock that hits the system and how much it is going to affect things further down the line with sufficient lead time. It can pretty much be put anywhere, other than a hydraulic dead zone where it’s not going to get any flow over it or directly downstream of ferric dosing, because the chemicals used in that process are metallic and stick to the plates.
Municipal Water Leader: You mentioned that your approach flips conventional approaches on their head. Would you expand on what you meant by that?
Jonathan Grant: There are two basic ways to get information about wastewater biological conditions. One is with a light-based sensor, which essentially shines a light through a glass plate. Those are effective, but they require a lot of maintenance, because with biofilm growth, they literally get covered in waste. The other approach is just taking samples of the water and getting a lab analysis, which is fine for regulations and for getting specific chemical or species validation but can take up to 5 days.
Our sensors are built to work in nasty conditions. The reason they can be placed in so many different parts of the plants is that they’re built to live in places that grow biofilm. Biofouling disrupts every other sensor, but it is actually what makes our sensor work.
Municipal Water Leader: What kind of maintenance does your probe require?
Jonathan Grant: We ask that people look at the probe once a quarter. If there’s anything on it, such as fats, oils, grease, or rags, it can usually be cleaned by swirling it around in a bucket for a minute and then put right back in. For most folks, the probe requires 4 hours of maintenance a year.
Municipal Water Leader: How often does the probe take a reading?
Jonathan Grant: Once a minute. The whole system uses less power than a light bulb, so it can run at all times. That gives a good baseline to see any issues that occur. Once a client understands the metric and how to use it, the next question is how to optimize their processes and make better decisions.
Municipal Water Leader: Can end users install these probes themselves?
Jonathan Grant: We’ve shipped around the world during the COVID‐19 pandemic. Especially in places where we have manufacturer’s reps, we do offer to do the installation, but it wouldn’t be difficult for a municipal operator to install the probe. It usually takes 2–3 hours to install.
Municipal Water Leader: Is your primary customer base local, regional, or international?
Jonathan Grant: It is truly international. Our best clients are those who have had a local brewery open up or are pulling their hair out because every time it rains they experience effluent issues. We can also serve leading operators anywhere who want to understand and improve their plant. Eventually, we want to become a standard operating tool.
Municipal Water Leader: How did you develop this technology?
Jonathan Grant: Initially, our technology was built to help monitor a package treatment plant that our sister company REGEN had developed. Remote monitoring for that project was important because it was getting shipped out to an extremely remote place, and when I say remote, I mean off grid solar powered. We realized that this was actually a winning device on its own. We tried a couple of things. The first was to ask treatment plant operators where they thought it would be useful. That’s why we have so many different problem statements—we tried it out in lots of places. The funny thing we always joke about is that we first thought that everyone would want to use our probe to monitor their effluent. No one wants that. They want to know what they can do to act on something beforehand instead of finding out that they have an issue at the end. If we had waited for regulation, we’d still be waiting. Anaerobic digestion is a key market for us as well, especially with codigestion becoming a more popular way for municipalities to generate energy.
Municipal Water Leader: What is your top goal as a company?
Jonathan Grant: We’re trying to change the metric that has been used for monitoring for as long as anyone can remember: biological oxygen demand (BOD) or BOD surrogates. We think we have a better metric for real-time process control and reliability, and it is complementary to the existing processes and tools out there. The superiority of our process is like that of e-mail over waiting for something to come in the mail. The difference in terms of real-time understanding between our biological sensor and a lab test for BOD really is that stark. Our biggest challenge is to break through the status quo and ensure that operators understand how to use this information.
Municipal Water Leader: How do you plan to make that breakthrough?

A SENTRY technician installs a probe.
Jonathan Grant: We’re doing a lot of work with academics, research and development departments at large utilities, and innovation groups. We had a lot of early success and continue to have success with groups like that. We’re still breaking through that wall every day; 80 units is a lot for us, but it’s not a lot in terms of numbers of treatment plants. A number of issues hold true potential for the water community to provide better wastewater treatment, and we’re a small part of that.
Municipal Water Leader: What is your vision for the future?
Jonathan Grant: Our big, hairy, audacious goal is for SENTRY to be installed in every advanced water and wastewater process in the world by 2040. More immediately, we want to have 400 installations by the end of 2024. We are dreaming big but being practical. Our real vision is to make biological processes intuitive, simple, and controllable.
I would suggest reading the book Start With Why by Simon Sinek. Our why as a company is that we care about the environment and making the world better through smarter decisions in treating water and wastewater. I think that’s likely true of almost everyone in the water and wastewater sector: We get up every day and know that we’re making the world a better place.

Jonathan Grant is the chief commercial officer for SENTRY. He can be reached at jgrant@islandwatertech.com.