
17 minute read
NURTURING THE FUTURE OF SHIPBUILDING
NURTURING THE FUTURE OF SHIPBUILDING
Inside Incat’s Masterful Fusion of Innovation, Education and Dedication
Incat is a leader in the shipbuilding industry with their fuelefficient, eco-conscious, lightweight ferry solutions. What truly sets Incat apart is their dedication to the art of aluminum welding—a challenging feat that demands utmost precision and expertise. Incat prioritises training and education, running an innovative apprenticeship program, investing heavily in their welding workforce, and collaborating with local schools and TAFEs to raise awareness of career opportunities in manufacturing and engineering.
Firmly cemented as experts in cutting edge environmentally friendly vessels, Weld Australia member Incat provides lightweight ship solutions for ferry operators and special service providers. From fast, flexible and efficient vehicle-passenger ferries to crew ships and dynamic platforms, Incat sets the global benchmark in aluminium ship technology.
Continuing the emphasis on ecooperations and fuel efficiency Incat has developed lightweight, environmentally friendly fuel-efficient ships carrying heavier vehicle loads than ever before and at the lowest operational costs. With the focus now firmly on all-electric, zero-emission ferries, Incat is building the world’s largest electric vehicle and passenger ferry. It will have capacity for 2,100 passengers and crew, 225 cars and a massive Duty Free Shop of over 2,000m2 on one level. The battery installation will be four times greater than any other marine vessel in the world.
Incat’s shipyard is on Prince of Wales Bay at Derwent Park near Hobart, Tasmania, Australia. Their 70,000m2 facility incorporates four building halls, extensive wharf facilities, a slipway and two dry-dock areas. Incat boasts innovative production facilities to construct, launch and deliver small craft through to larger ships of 150m length and of panamax beam.
Incat takes ownership of the customer’s specific needs ensuring on-time delivery of the right ship for the right job. A reputation for quality and excellence in production is supported by an experienced and dedicated workforce.
High Quality, Intricate Aluminium Welding
With Incat specialising in the manufacture of aluminium vessels, their team are experts in welding this lightweight, yet incredibly strong and durable, material. This is no mean feat—learning how to weld aluminium is challenging, requiring care, precision and specialised equipment.
For instance, aluminum has a low melting point, making it more likely to warp, crack, and break during welding. In addition, when welding aluminum, magnesium oxides can collect at the weld on the base of the material, leading to discoloration.
According to Incat’s CEO, Tim Burnell, “Incat’s welding process are not hugely automated. We have some machines that perform double-sided automated welding, which we actually developed in-house. Our welding and fabrication processes are very labour intensive and this is unlikely to change—the quality and the intricacy of our welding necessitates a very hands-on process,” said Burnell.
“Aluminium welding requires a different skill set compared to carbon steel welding. It requires specialised training, particularly in the maritime industry.”
Like any thriving business, a core of dedicated and loyal staff can be found at the centre of Incat’s success. Many team members’ experience stretches back over two decades across a range of trades.
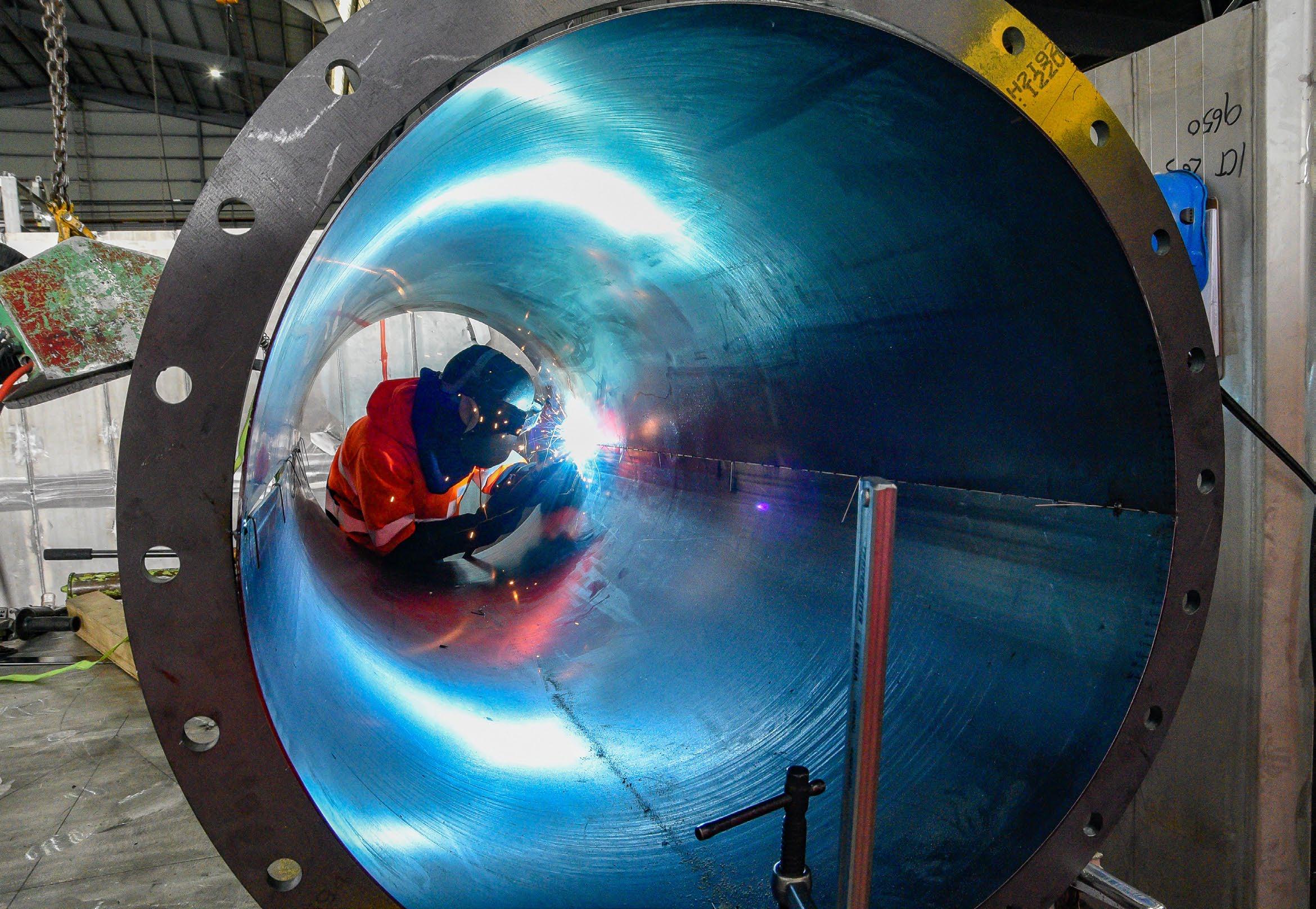
“We still have people working for us who were apprentices with us 25 years ago—they have honed their welding skills over time and, today, deliver superior quality workmanship on each and every Incat vessel.”
“The expert skills of our team members enable us to deliver a quality product that customers appreciate—it is the reason why so much of our work is repeat business. One of our customers has been with us for over 25 years, and has ordered nine vessels,” said Burnell.
Although Incat builds ships in Tasmania, they operate globally maintaining and delivering vessels, which provides an opportunity for experienced tradespeople to work overseas. Incat welders, fabricators and electronics staff recently travelled to Trinidad and Tobago, Spain and South Korea, working and expanding their skills in a variety of unique environments. The company understands the strength of working overseas in new environments.
Workforce Training Excellence
Incat took out Weld Australia’s 2022 Welding Excellence Award for Training
and Education—Organisation. Incat heavily invests in the future of its welding workforce. Training is a core part of Incat’s success. The company has a small, yet highly effective training team whose core focus is providing accredited training.
The key areas of Incat’s training include:
• Apprentice onboarding
• Supporting apprentice on job and off job training
• Developing and delivering post trade training for qualified personnel
• Providing training to enable external certifications
• Ongoing work health and safety
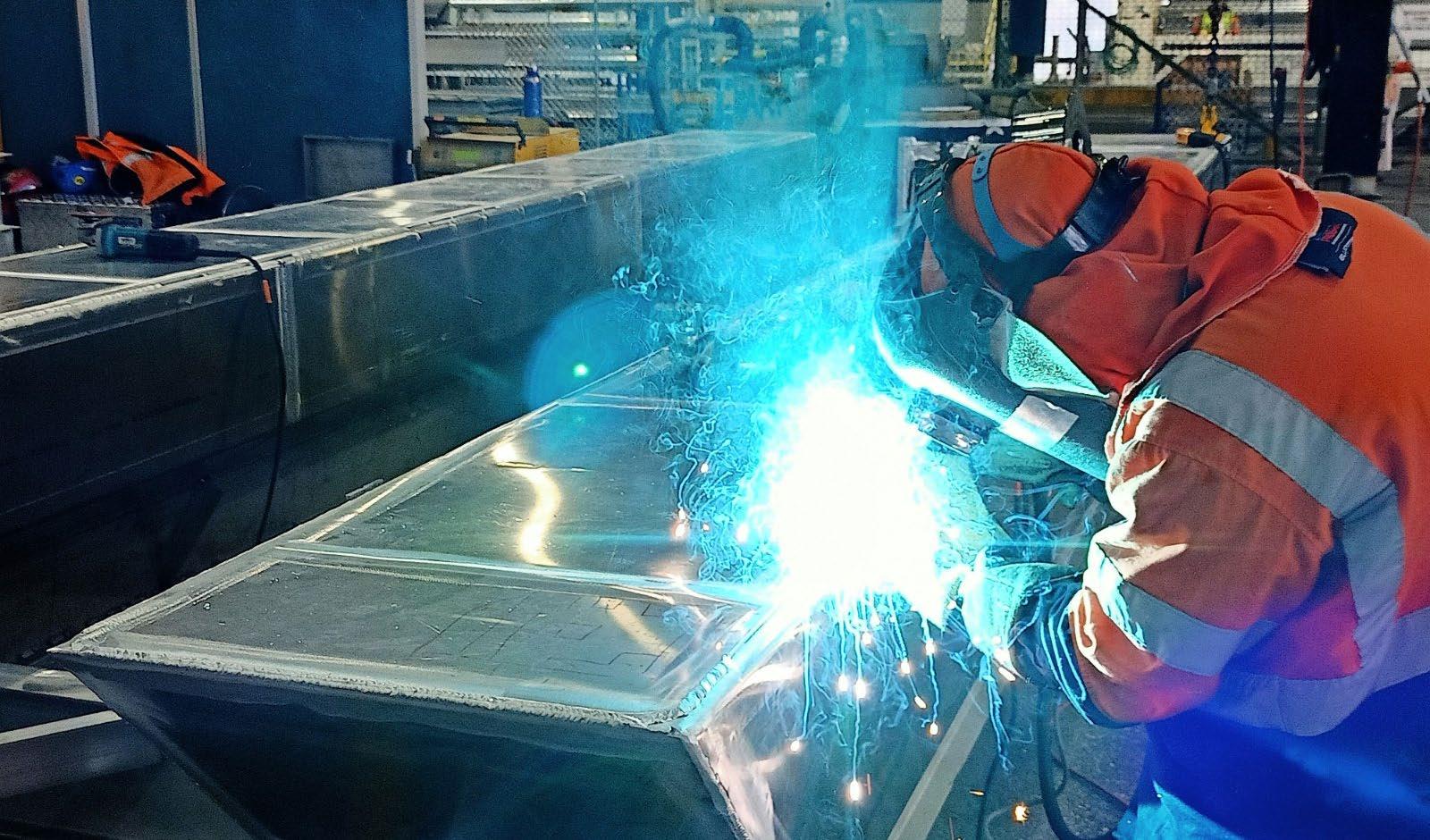
In the 2021-2022 financial year, Incat 900 hours of training per month. A significant percentage of this training was delivered by the Incat’s in-house training team. Their partnerships with training providers and regulators also ensure that the company can provide effective localised, targeted training and assessment in specialist areas with minimal impact to the business.
An Innovative Apprenticeship Program
Incat’s apprentice program has two intakes of 15 apprentices per annum, with upwards of 70 apprentices in training across four separate trades at any one time. Incat encourages everyone to apply for their apprenticeship program; the current apprentice mix includes two mature apprentices aged over 45 years, two Indigenous and two female apprentices.
Apprentice rotation is managed by a dedicated apprentice supervisor to ensure apprentices receive a broad cross-section of skills. The responsibility for this role entails tracking profiling progression, and linking on the job training requirements to align with off the job training. Incat has mapped sections of the ship building process to specific competencies of each apprenticeship or traineeship.
This forms the baseline for charting each apprentice or trainee’s individual journey through their training, ensuring no element of on-the-job training is missed. Competency is not signed off until the team leader agrees the apprentice has met the required level of competency in the workplace.
Across the company, Incat apprentices collectively spend around 1,000 hours per month attending off the job training opportunities, where they develop important skills relevant to their line of work.
Incat has a strong relationship with TasTAFE. There is a purpose-built TAFE campus adjacent to the shipyard, which offers a unique training advantage for apprentices. It means Australia’s future workforce gets a rare insight into the world’s best practice aluminium shipbuilding operation.
TasTAFE teachers also gain access to a range of industry opportunities to further their development. The two-way communication focus means trainers learn about modifications or changes in welding techniques and technology implemented during the construction phase of Incat vessels in a steadfast manner. Together, this ensures apprentices gain valuable experience and knowledge of various aspects of shipbuilding.
Finally, Incat apprentices graduate into employment, with ongoing training, throughout the shipyard. Importantly, there is an ongoing safety and skills on-the-job training across the workforce, which is crucial for new and longer-term employees to ensure workplace standards are met across the range of skill sets.
Strengthening the School to Employment Transition
Incat is working with schools and colleges in their local region to raise awareness of the career opportunities which can result from undertaking a manufacturing or engineering apprenticeship. The company regularly engages with vocational students and teachers, hosting information sessions and answering any questions.
Incat has worked with the Jordan River Learning Federation, hosting a ‘try a trade’ program for students interested in an engineering career. The program commenced with a tour of the Incat Shipyard and then two classes where Incat’s training team worked with the students in the school facility. Incat has developed a series of exercises that include an introduction to MIG welding in which the students made a set of drink coasters from aluminium.
Incat has also developed a first year apprentice support network where a fourth year apprentice acts as a big brother or sister. Fourth year apprentices must complete the competency requirements for ‘Assist in the Provision of on-the-Job Training’, which develops their leadership capabilities. Placing new apprentices with more experienced apprentices has resulted in the older apprentices enthusiastically taking ownership and showing the new apprentices the ropes.
Incat has observed that apprentices are settling into the workplace more quickly and are more comfortable raising concerns or issues when they have the support of an older apprentice.
The Welder Non-Trades Program
In 2018, Incat identified job applicants who demonstrated high level vocational skills, or came with overseas welding qualifications, but were missing opportunities to undertake apprenticeships in welding and fabrication. So that they could provide employment and training opportunities to those within this demographic, Incat developed their Welder Non-Trades (NT) Program.
The Welder NT program is comprised of 21 Enterprise Units of Competence which are internally delivered over a five-month period. The program is delivered to small groups of four to six trainees. This ensures that Incat can provide adequate attention and support to each of the trainees. Successful completion of the course results in a DNV certification process.
To date 29, trainees have completed this program. Three of those have transitioned into an apprenticeship and completed MEM30305 Certificate III Engineering –Fabrication Trade.
For further information about Incat and their capabilities, simply visit: incat.com.au
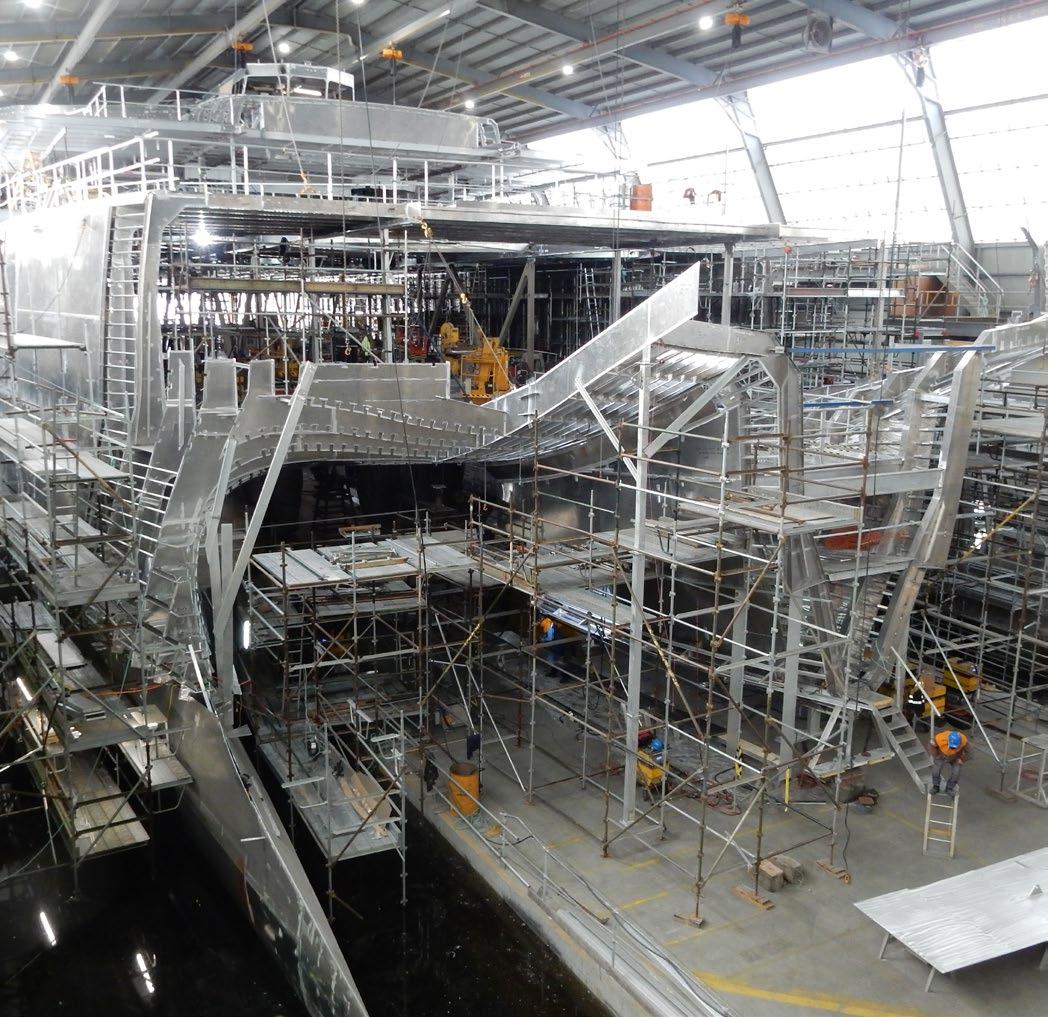
King of the Pack Wins Training and Education Award
Simon King (Technical Training Officer at Incat) took out the 2022 Weld Australia Training And Education—Teacher (Tasmania) Award.
With 26 years in aluminium and steel welding, King holds a Certificate III in Engineering Production, is an International Welding Inspector and a Det Norske Veritas (DNV) Certified Welder, which he has maintained since 2010. King’s DNV certifications make him the perfect candidate to prepare Incat’s qualified welders for their own DNV certification assessments.
King brings a wide variety of experience to his technical training, having worked in a diverse range of settings and roles, including:
• Fly-in fly-out on the BHP Billiton Olympic Dam project as a Shutdown Supervisor and as a welder
• Fly-in fly-out worker at the Newcrest Mining Cadia Gold Mine
• Caterpillar Elphinstone
• Impact Fertilser
• One Steel Reinforcing
• Richardson Devine Marine and North West Bay Ships involving aluminium and steel welding
According to King, “I absolutely love training and teaching and passing on my knowledge to first year apprentices and trainees and work colleagues.”
King is responsible for teaching Incat’s first year apprentices about the fundamentals of welding aluminium. Initially, he demonstrates the skill being taught and then breaks it down into smaller bite sized learning packages.
Once his apprentices have been assessed for their initial weld, and improvement opportunities have been identified, King provides targeted training.
Incat’s strong emphasis on training and professional growth means the candidate’s knowledge and skills quickly reach the required standard.
Since taking on the role of Technical Training Officer in February 2022, 97% of Incat’s DNV certification candidates have successfully complete their certification on their first attempt. This is testament to King’s skill and ability as a specialist trainer.