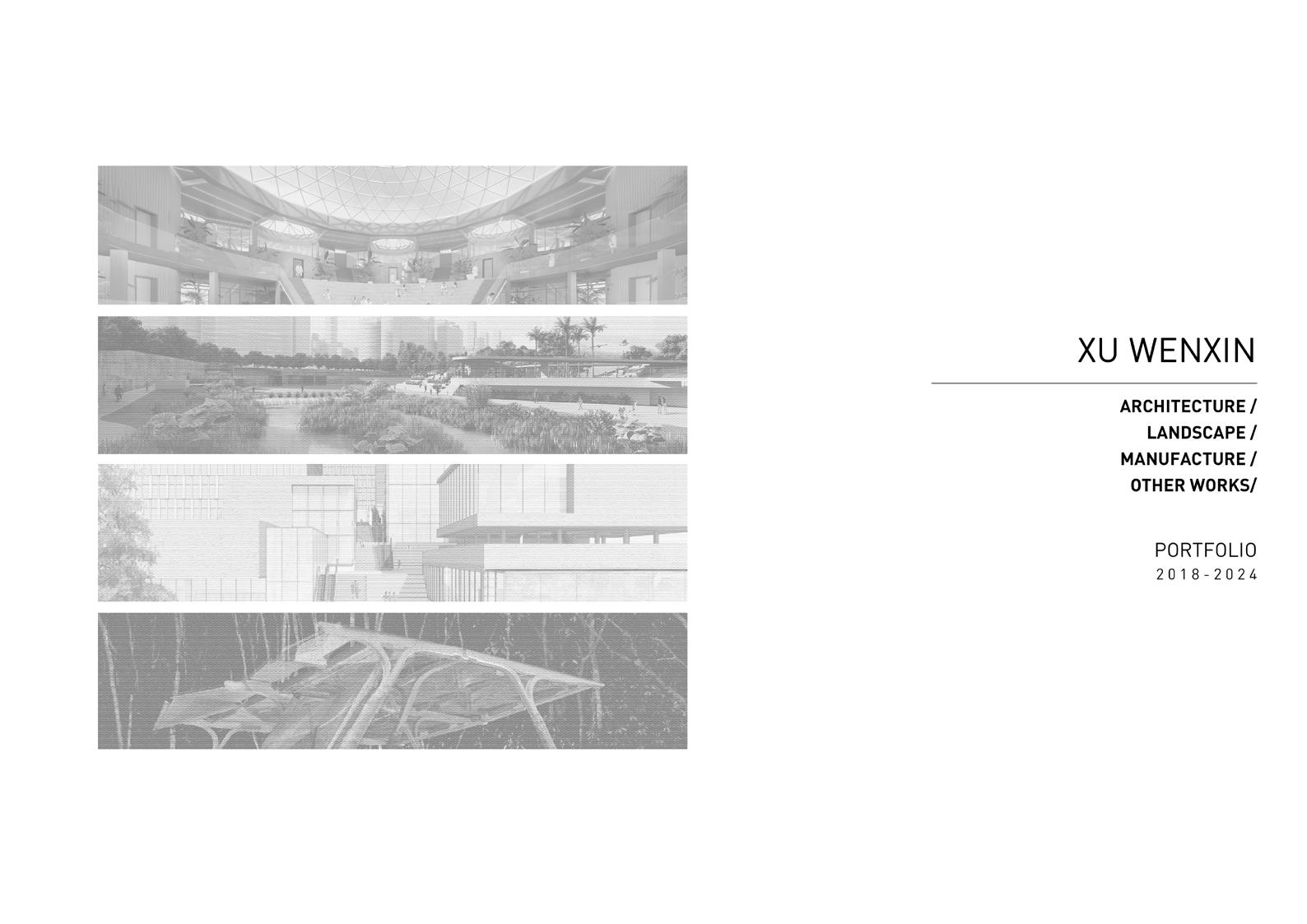
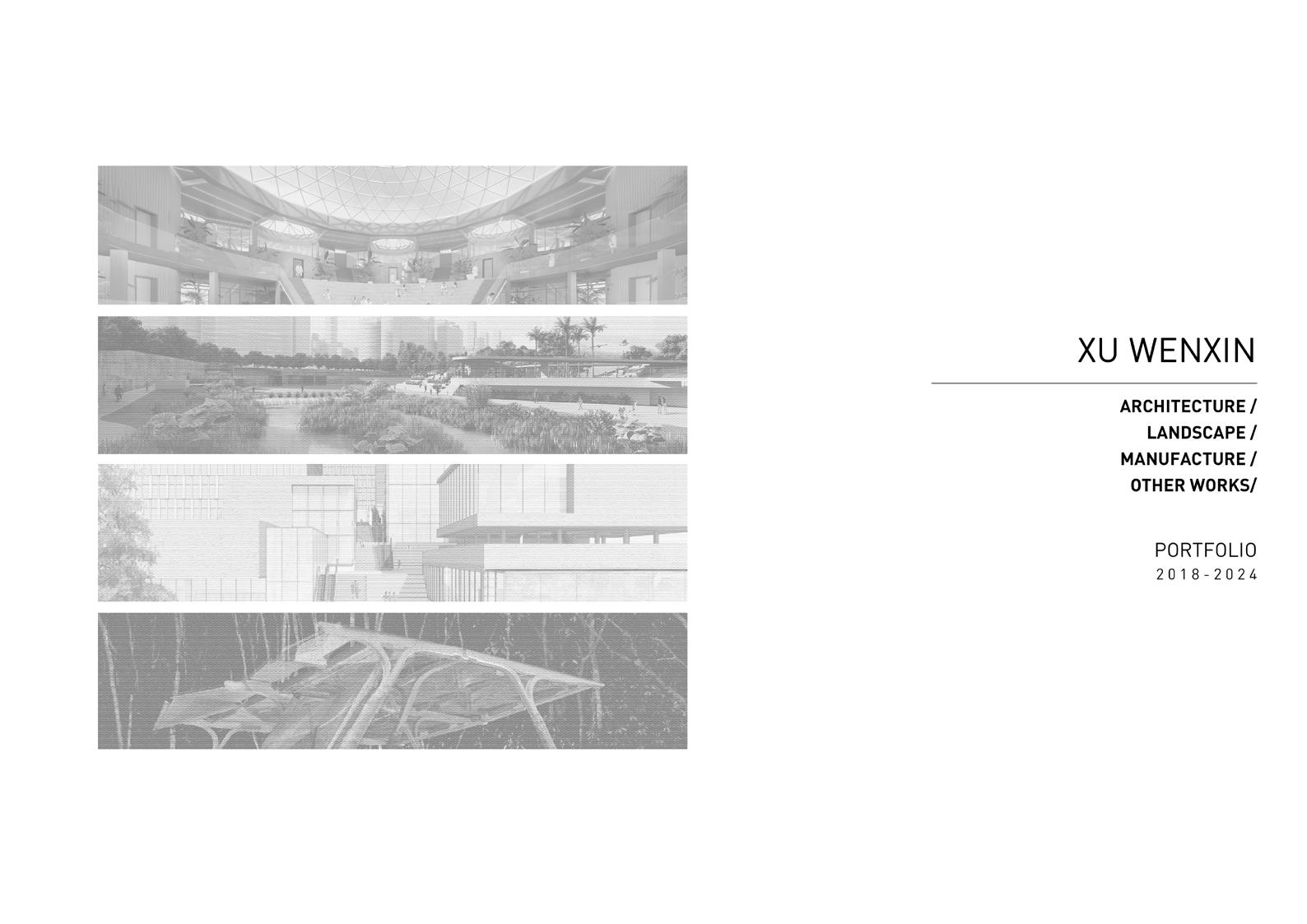
W E N X I N XU
EXPERIENCE
Mamou-Mani Architects Ltd.
Architectural Assistant Part2 equivalent
03/2023-Now
London, United Kingdom
TJAD Original Design Architect Studio
Architectural design Intern
05/2020-08/2020
Shanghai, China
EDUCATION
UCL | Bartlett School of Architecture
MArch Design for Manufacture (Merit)
09/2020-01/2022
London, United Kingdom
Nanjing Tech University Pujiang Institute
Architecture (87/100, Top 3%)
09/2014-07/2019
Nanjing, China
· Contributed to 15 projects within the last year, primarily focused on design tasks while also engaging in rendering, drawing, and manufacturing activities.
· Proficiently utilized Rhino and Grasshopper for parametric design, demonstrating effective collaboration skills during task handovers.
· Led small to medium-sized projects, collaborating with teams consisting of 3 to 5 members. Responsibilities included task allocation, design leadership, progress reporting, and client liaison.
· Completed project management training, acquiring skills in project planning, budgeting and cost management, schedule management, and client relations.
· Participated in the bidding process for the regeneration of the Guanlan River and won the bid.
· Investigated site information, analysed diagrams and proposed solutions.
· Modelled and simulated original state of the 14.6 km construction site, including existing buildings, bridges and city roads.
· Worked in a team of 3 to redesign the first main node of the project, and personally presented progress twice a week.
· Participated in the production of the bid report text, and was principally responsible for diagrams and rendering.
· Practiced practical CNC skills with timber and aluminium.
· Mastered with Manufacture progress of Aluminium Sand Casting.
· Worked in a team of 14 to design and construct a 1:1 physical wood seasoning shelter in Flimwell Park.
· Independently developed the design of an aluminium connector in the group project, and iterated 3 generations to adapt with other parts.
· Awarded 2nd place Scholarship for five years.
· Awarded 2nd Prize of The 4th Campus Town NJPJI Architectural Manufacture Competition.
· Honoured as ‘Outstanding Graduate’.
DIGITAL SOFTWARE:
Rhino, Grasshopper, Vary, Twinmotion, Revit, Prusa Slicer, Sketchup, Fusion 360, Lumion, PhotoShop, Adobe Illustrator, InDesign, AutoCAD, Microsoft Office.
MANUFACTURE PRACTICE:
Laser Cutting, 3D Printing, CNC Practice, Sand Casting(Aluminum), Steam Bending(Timber, Bamboo), Robotic Practice.
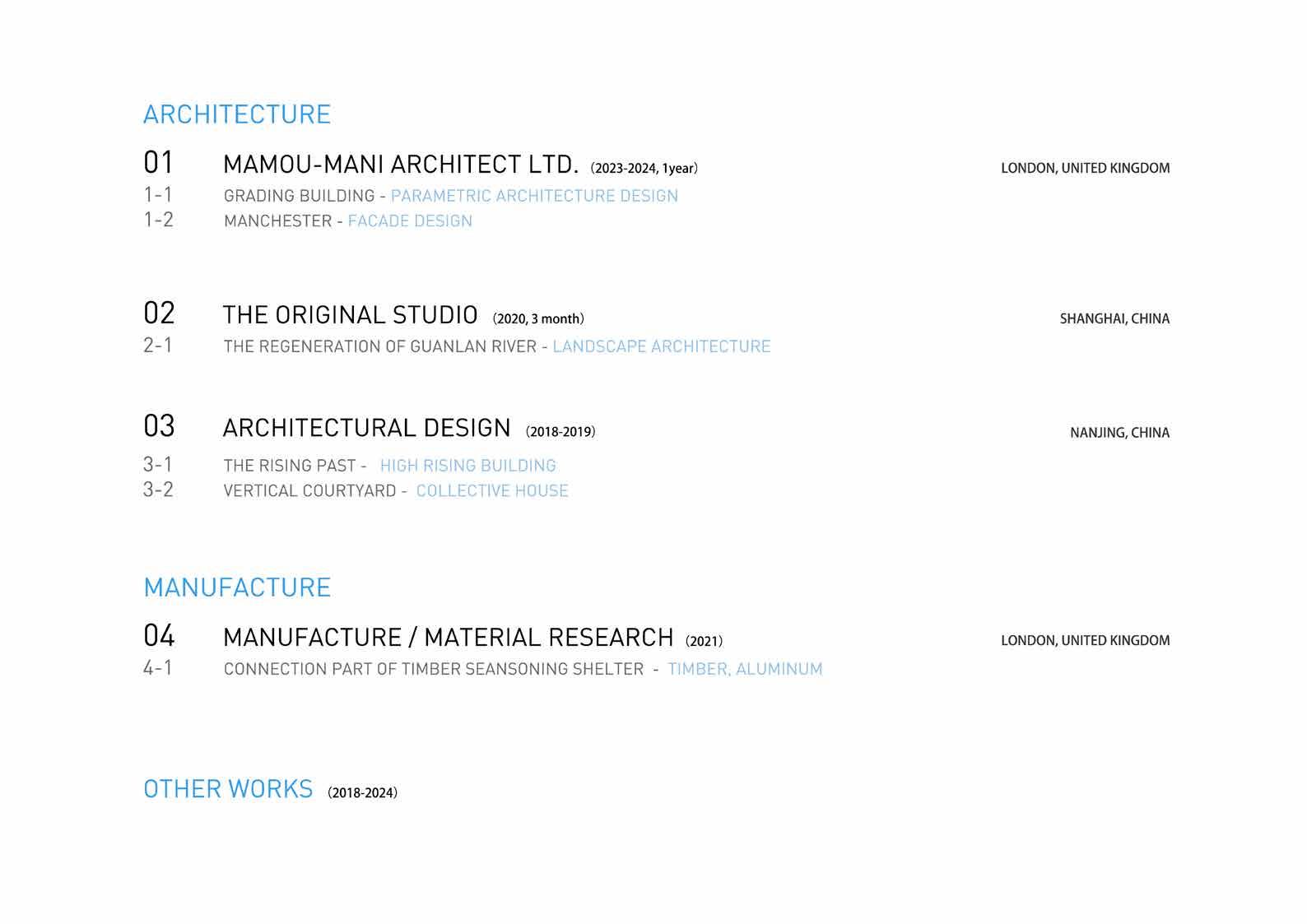
GRADING BUILDING
PARAMETRIC ARCHITECTURE DESIGN
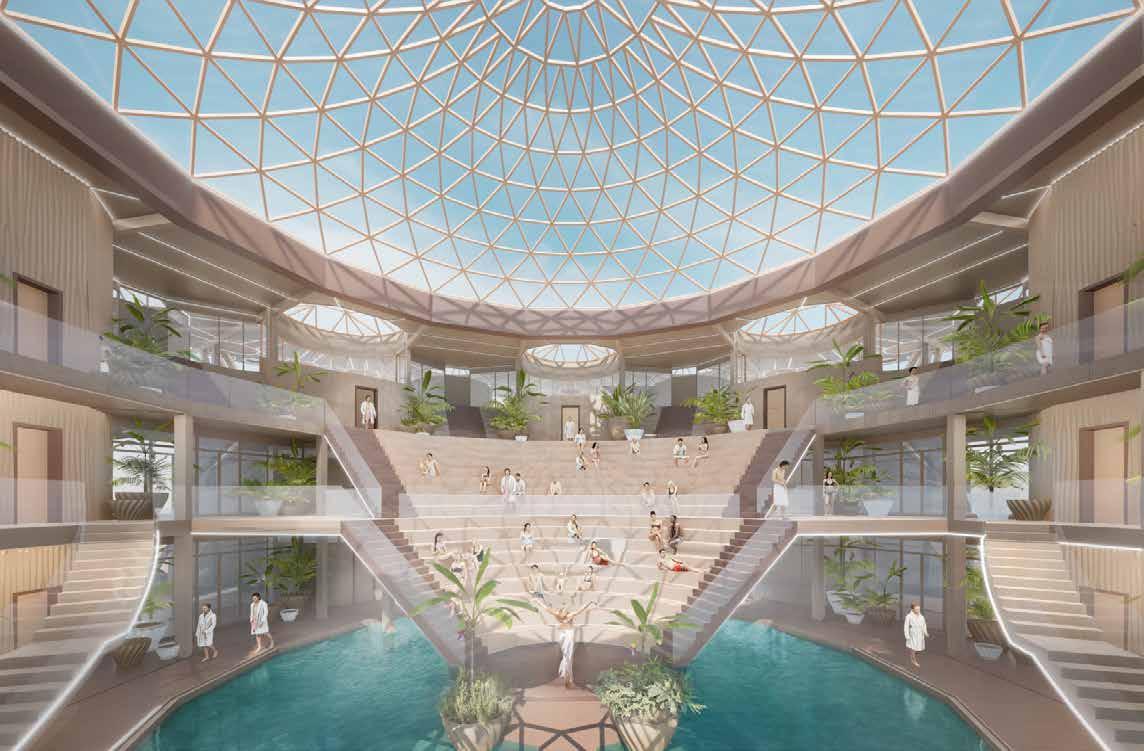
01 02 03 04 1-1 1-2
Date: 2023.10-2024.02
Location: Germany
Team: Nina Pestel, Eleonore d'Hauterives, Wenxin Xu, Hsiaoju Lee, Zeynep Aydinoglu, Minran Xue
Role:
· Architecture Design
· Paramatric Facade Design
· Render - Twinmotion
· Project Management
Design Explanation:
The envisioned project is a groundbreaking venture, blending functionality with entertainment in the form of a grading building. Located strategically, this structure is poised to revolutionize the urban landscape by not only providing recreational spaces but also integrating seamlessly with its environment to enhance air quality and overall ambiance. Embracing a holistic approach, the design seamlessly merges parametric principles from its floor plan to its facade, ensuring both efficiency and aesthetics.
Based on the design principle that is the incorporation of a salt wall, a natural element renowned for its air purifying properties. Positioned within the building's framework, this salt wall serves a dual purpose: enhancing the indoor air quality while also acting as a captivating architectural feature. By harnessing the natural benefits of salt, the building not only offers entertainment but also promotes a healthier environment for its occupants and surrounding areas.
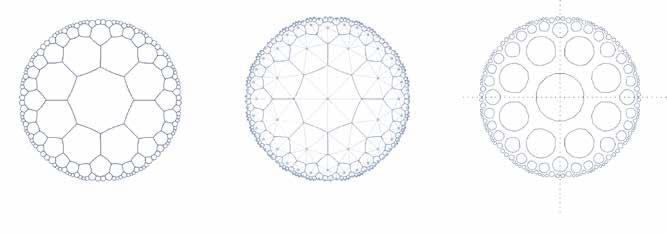
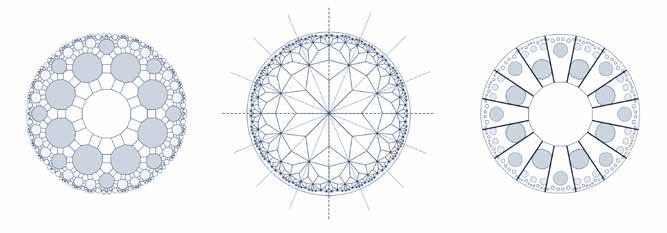
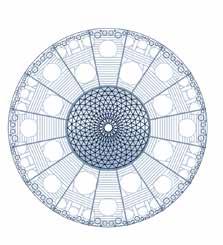
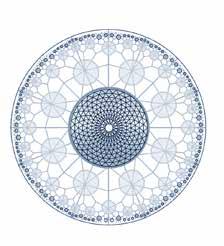
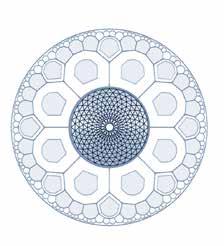
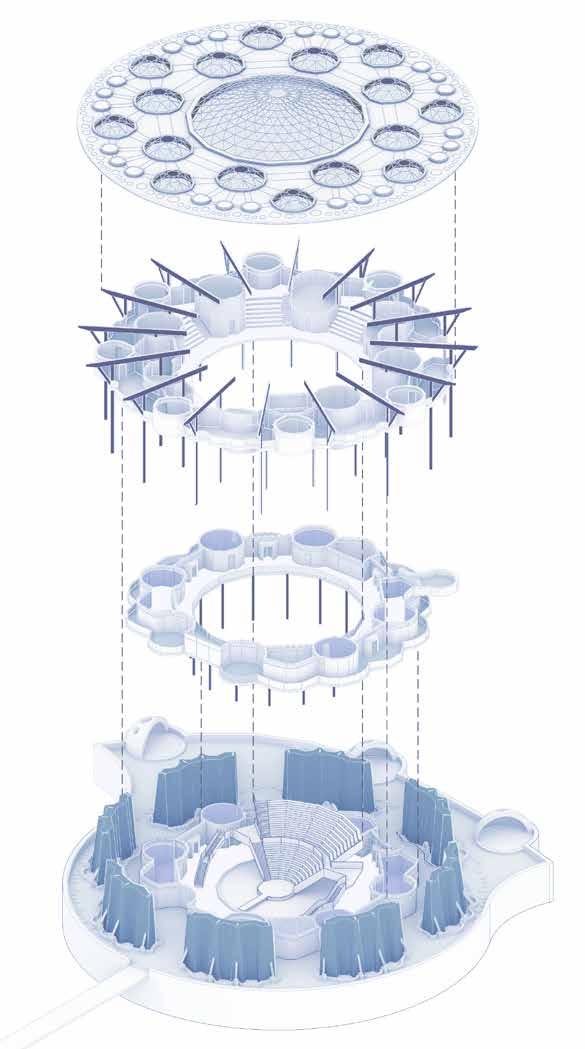
Sauna Room
Salt Wall
Swimming Pool
PARAMETRIC ROOF DEISGN
ROOF OPTIONS

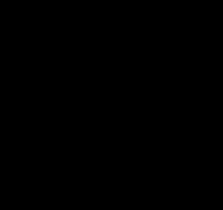
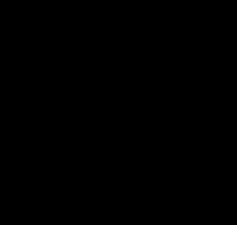
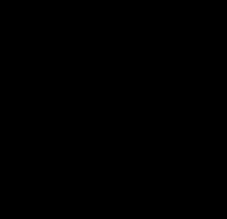
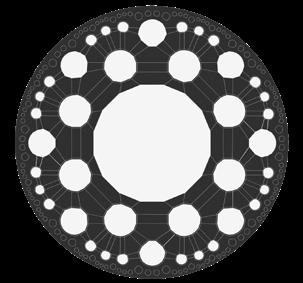
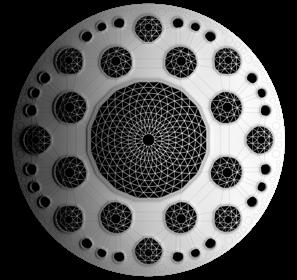
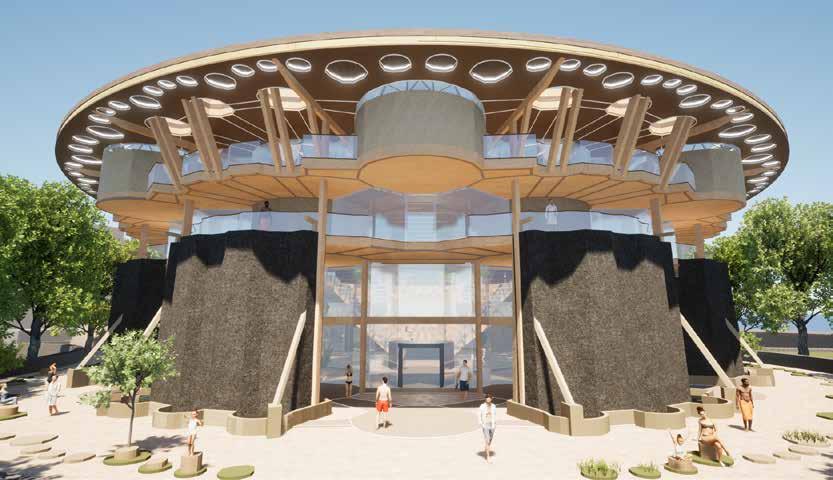
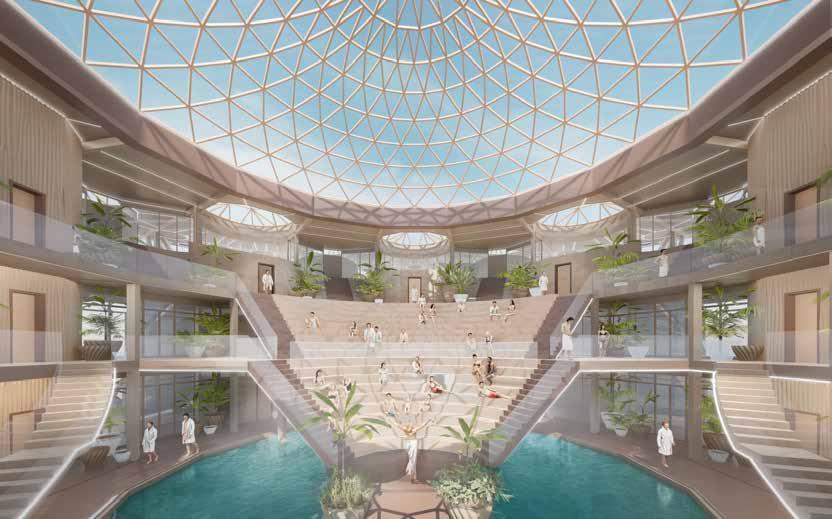
OPTION 1: DIAMOND
OPTION 2: STRAIGHT
OPTION 4: LAMELLA (CHOSEN)
OPTION 3: GALAXIA
INTERIOR 3D PRINTED WALL DESIGN
In order to break the conventional feeling of the interior, the customer favored parametric wall decoration with 3D printing. There are four parametric solutions and two materials - PLA and Wood.
A) Roe (Wood)
B) Wave (Wood)
C) Butterfly (PLA)
D) Altostrata (PLA)
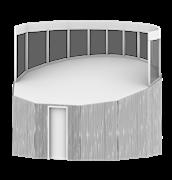
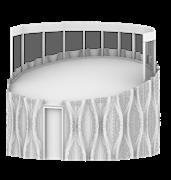
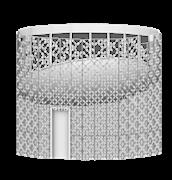
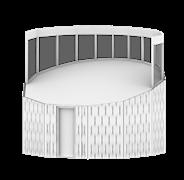
PROTOTYPE PROGRESS
The printing process is facilitated by a robotic, providing a clear visualization of the pathway. Depending on the size and shape specifications, prototypes are printed using different machines, such as the WASP 3MT or KUKA robotic, ensuring adaptability to diverse requirements.
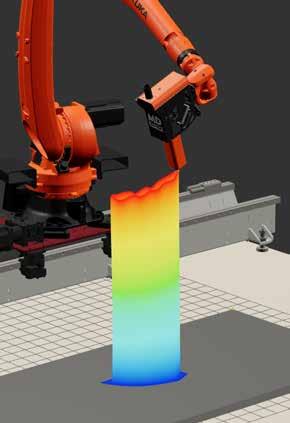
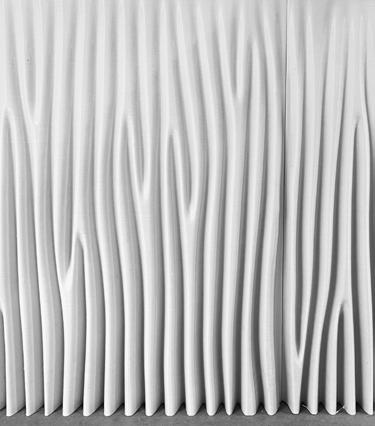
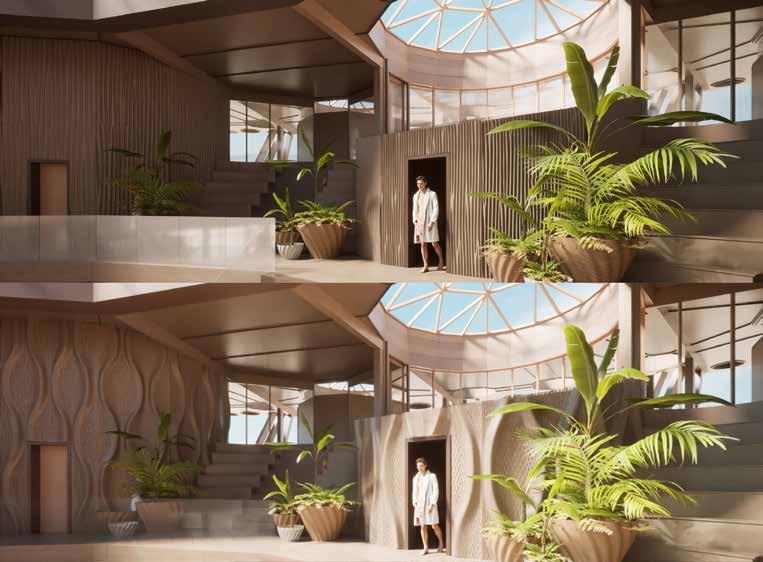
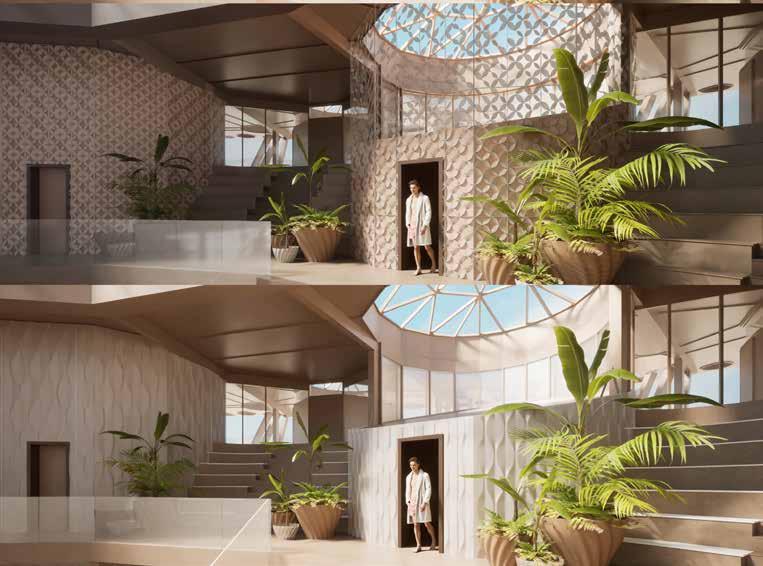
MANCHESTER THERME FACADE DESIGN
PARAMETRIC FACADE DESIGN
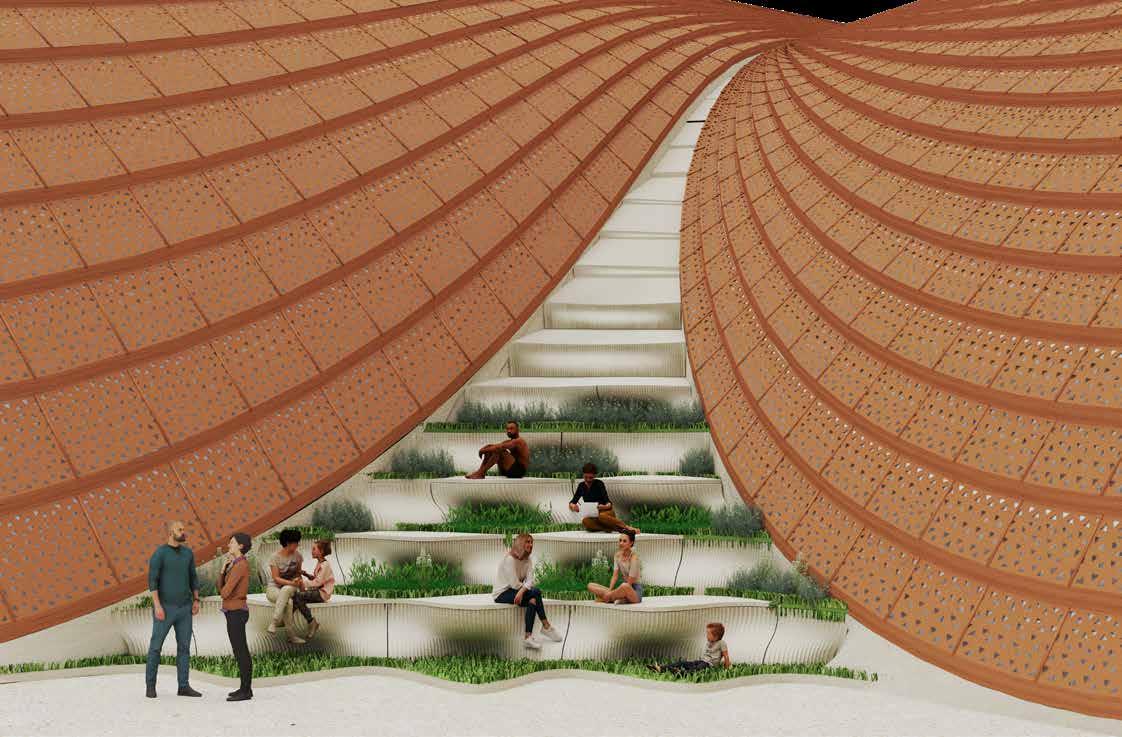
01 02 03 04 1-1 1-2
Date: 2023.10-2024.02
Location: Germany
Team: Nina Pestel, Wenxin Xu, Hsiaoju Lee, Aslan Adnan, Minran Xue
Role:
· Parametric Facade Design
· Structure Technical Design
· Render-Vray
Design Explanation:
The design concept for the building interface with the public space The wall stands as a beacon of innovation, bridging the industrial site with nature's embrace.
Its parametric façade, adorned with interlocking elements, seamlessly transitions into planters, blurring the line between architecture and landscape.
Through strategic perforations, the surface becomes porous and inviting, fostering a tangible connection between indoor and outdoor realms. Amidst verdant gardens contrasting the industrial backdrop, the wall emerges as a vibrant nucleus for community engagement. Here, amidst lush greenery, visitors find not only respite but also opportunities for social interaction and communal gatherings. This design ethos celebrates the harmonious coexistence of architecture, landscape, and urban vitality, redefining the cityscape with its innovative approach to placemaking.
OPTION1 VERTICAL WATERFALL
By integrating with traditional clay mold manufacturing methods, the 3D Printed Ceramic Cladding presents a revolutionary solution, requiring fewer molds and allowing for enhanced design flexibility. Crafted from natural earth and terracotta, this innovative approach not only minimizes environmental impact but also highlights the inherent beauty of organic materials. Explore the forefront of architectural design with endless possibilities and a commitment to sustainable craftsmanship.
PROTOTYPE DESIGN
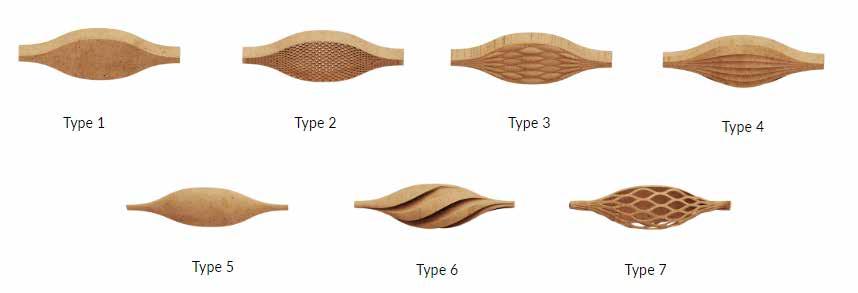
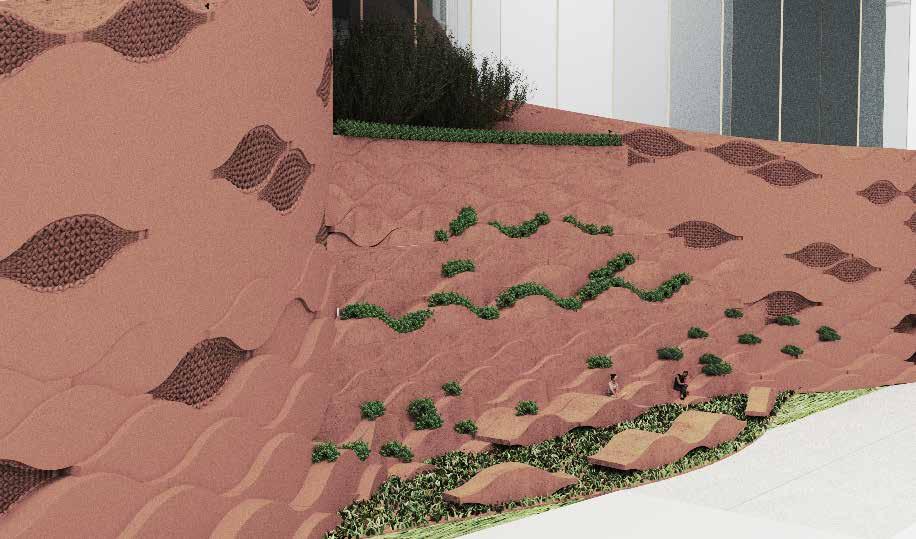
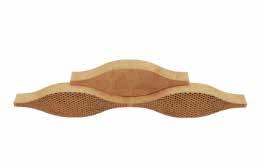
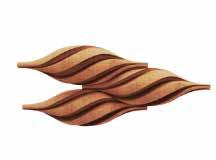
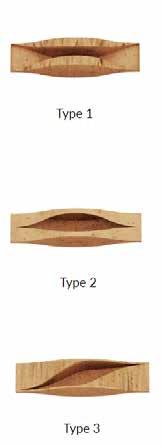
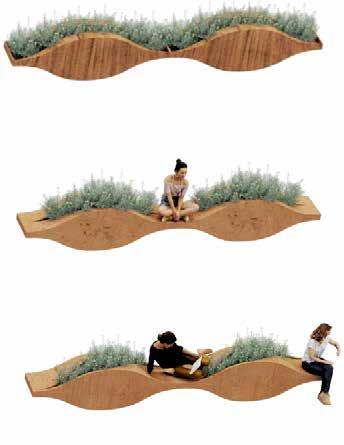
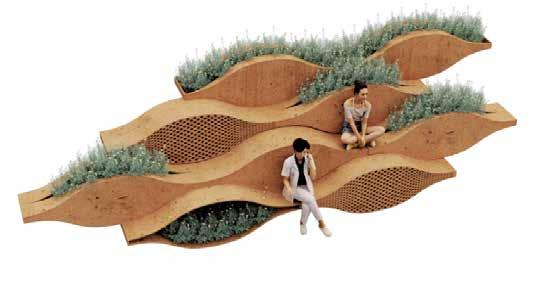
PROTOTYPE
OPEN-UP TYPES
OPTION2 CORNER WATERFALL
To enhance the abrupt transition at the corner, a waterfall form is employed to seamlessly connect the corners. The incorporation of landscaping and irrigation systems enhances the functionality of the corners, providing versatility.
This design intervention not only offers a comfortable resting spot for urban pedestrians but also seamlessly integrates nature into the urban environment. Additionally, the utilization of 3D printed seats combined with shingle or metal plates introduces a distinct juxtaposition, mitigating the sense of monotony caused by uniform materials across large areas.
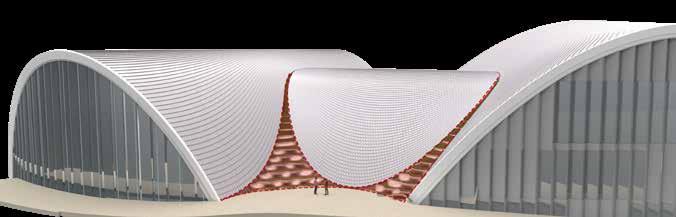
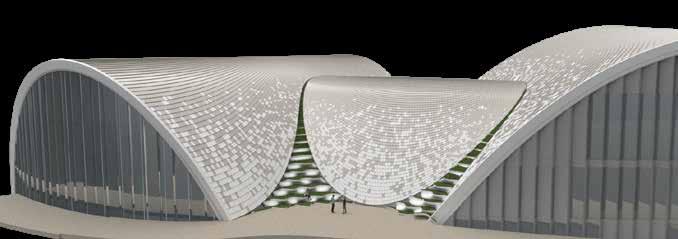
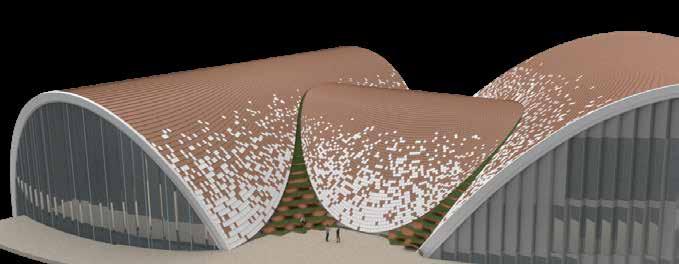
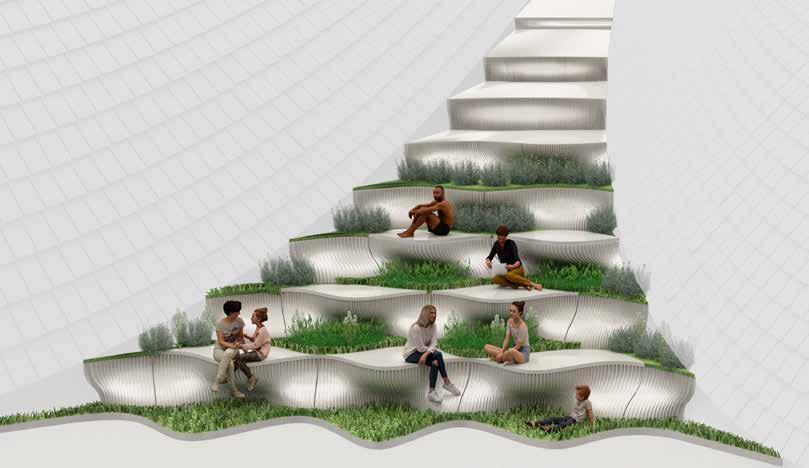
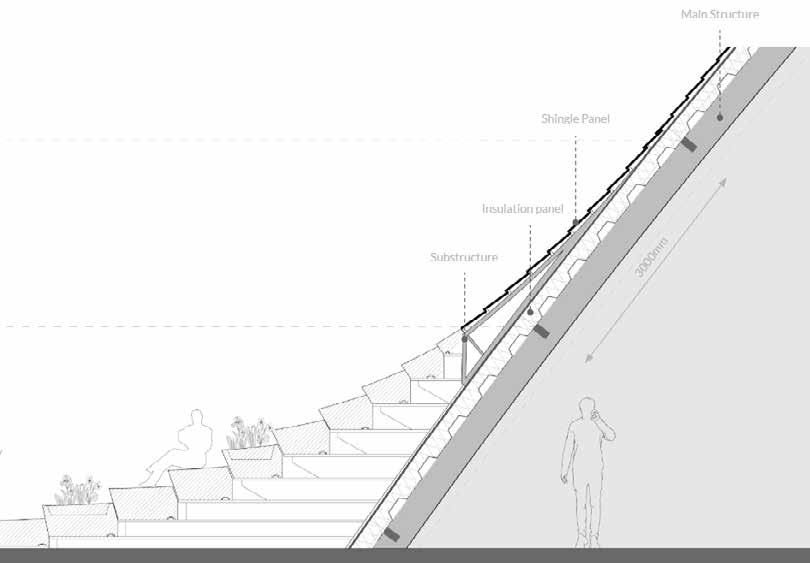
SHINGLE VERSION
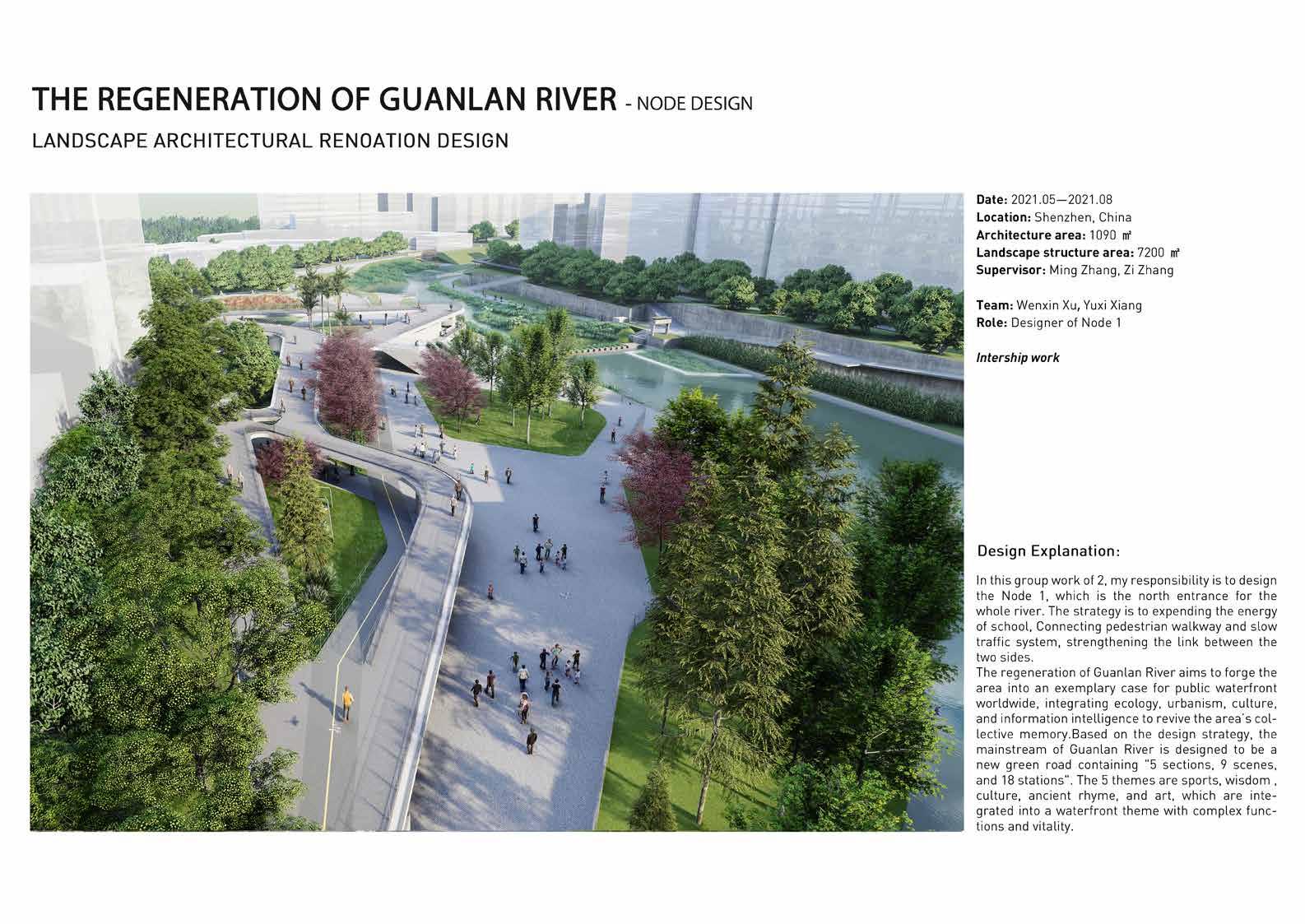
01 02 03 04 2-1
5.
6.
7.
8.
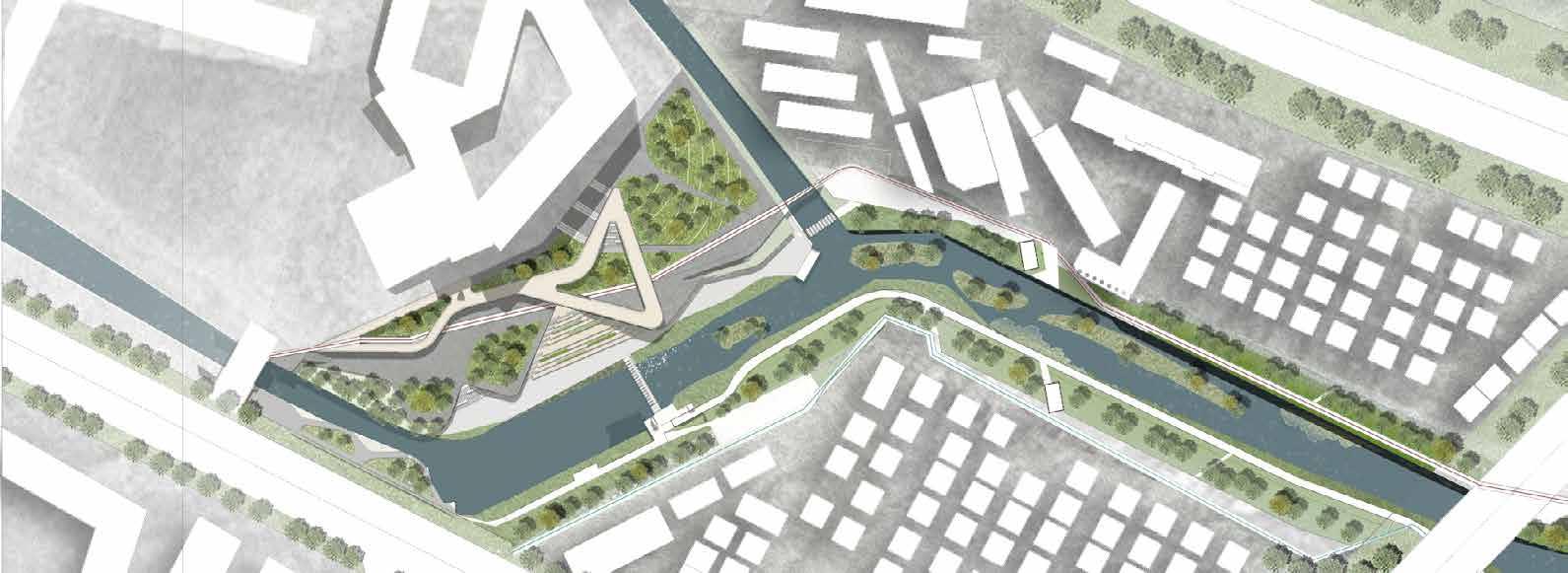
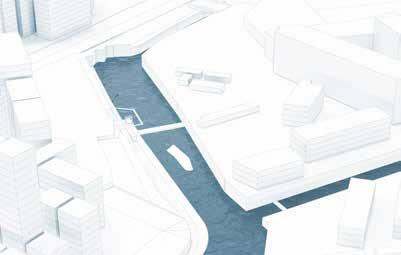
THE ORIGINAL SITUATION
There are some abandon buildings exsisting on the site. The vertical banks blocked up the people and river. The bank oppsite to the school is the entrance of the whole river.
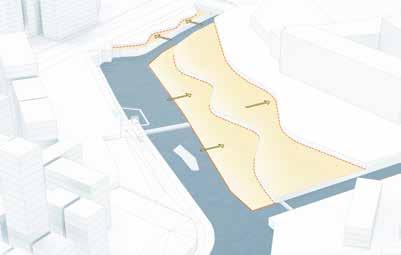
STEP1: TRANSFORM THE BANKS
The vertical banks are re-shaped into terraces, which forms the primary plantform, the secondary plantform and the thrid plantform beside the school.
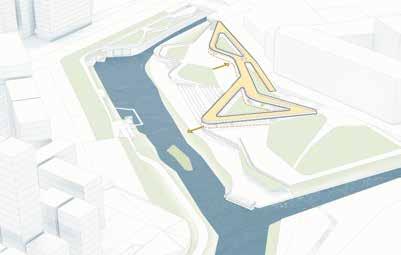
STEP2: GENERATE ACTIVITY AREAS
For expanding the school’s field of activity, the collage gallery is generated for students and their parents to take rest. It also aims to create a plantform for people to get closer with river.
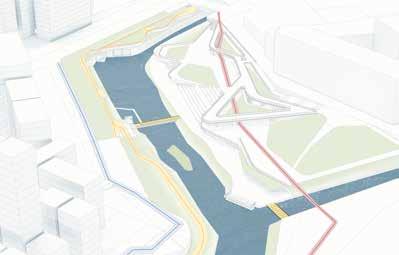
STEP3:
CONNECT SLOW TRAVEL SYSTEM
Along the banks, the pedestrain system and cycling system are introduced from city roads to river path. In order to strengthen the two shores connection, dean steps should be established.
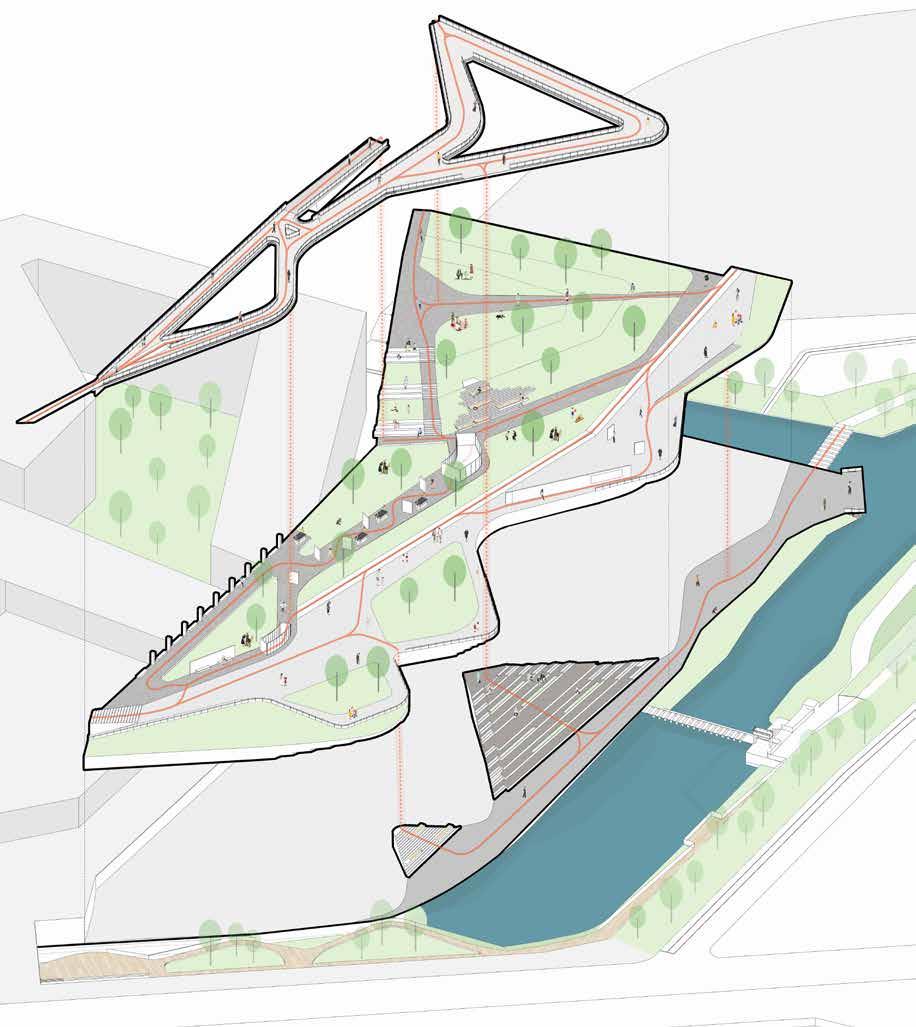
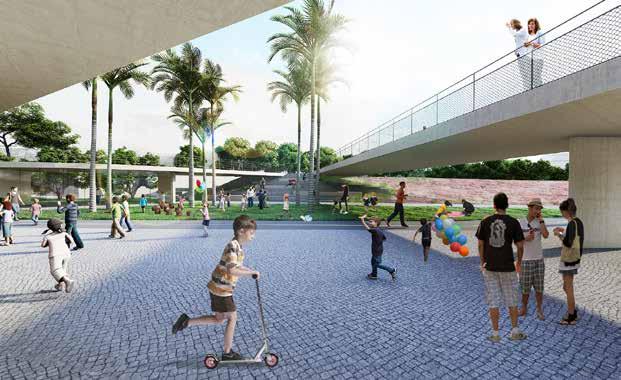
SCENE PERSPECTIVE 1: Bridge Gallery
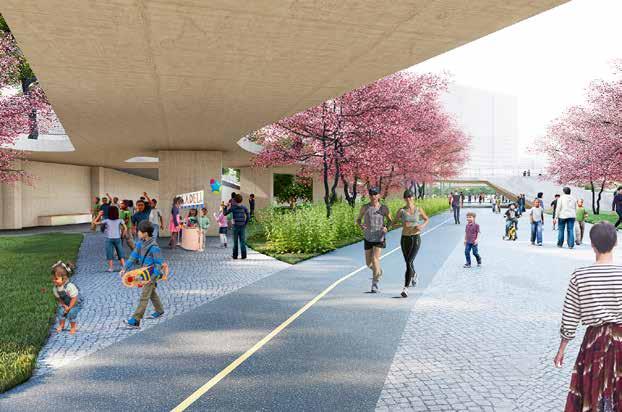
SCENE PERSPECTIVE 2: Central Playground
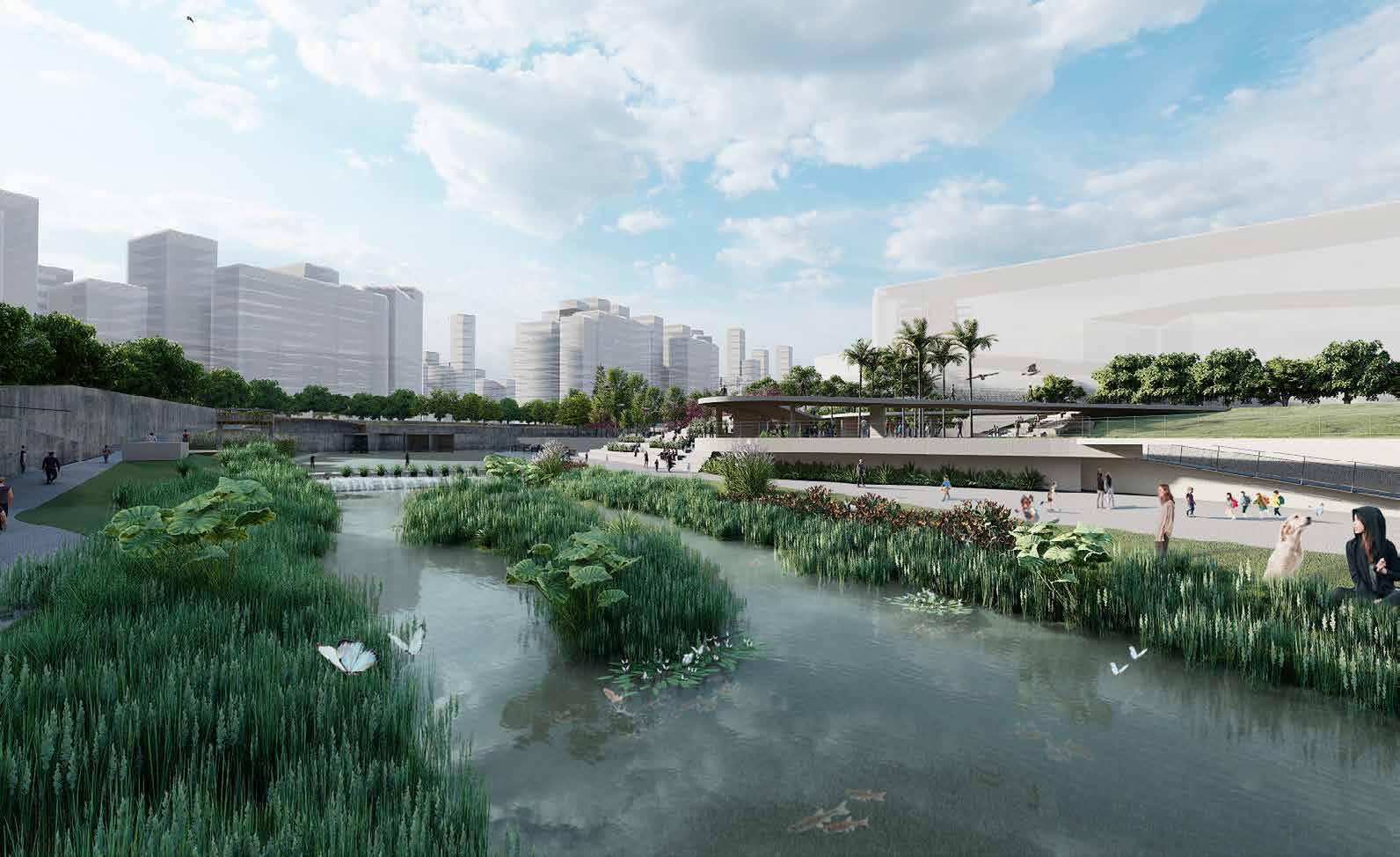
CONTRAST RENDERING AFTER RENOVATION WITH THEORIGINAL SITE
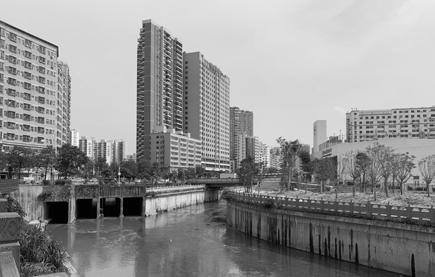
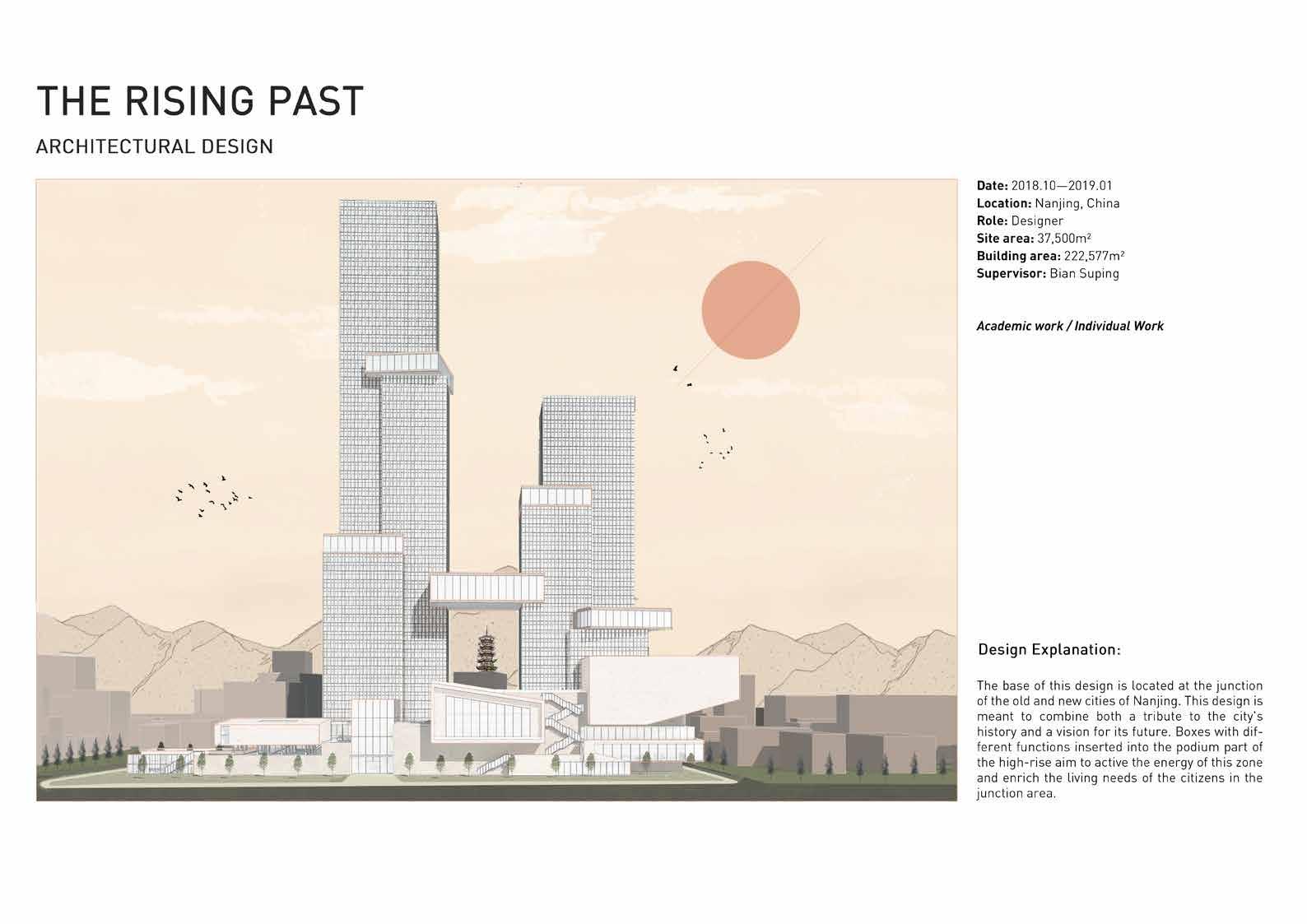
01 02 03 04
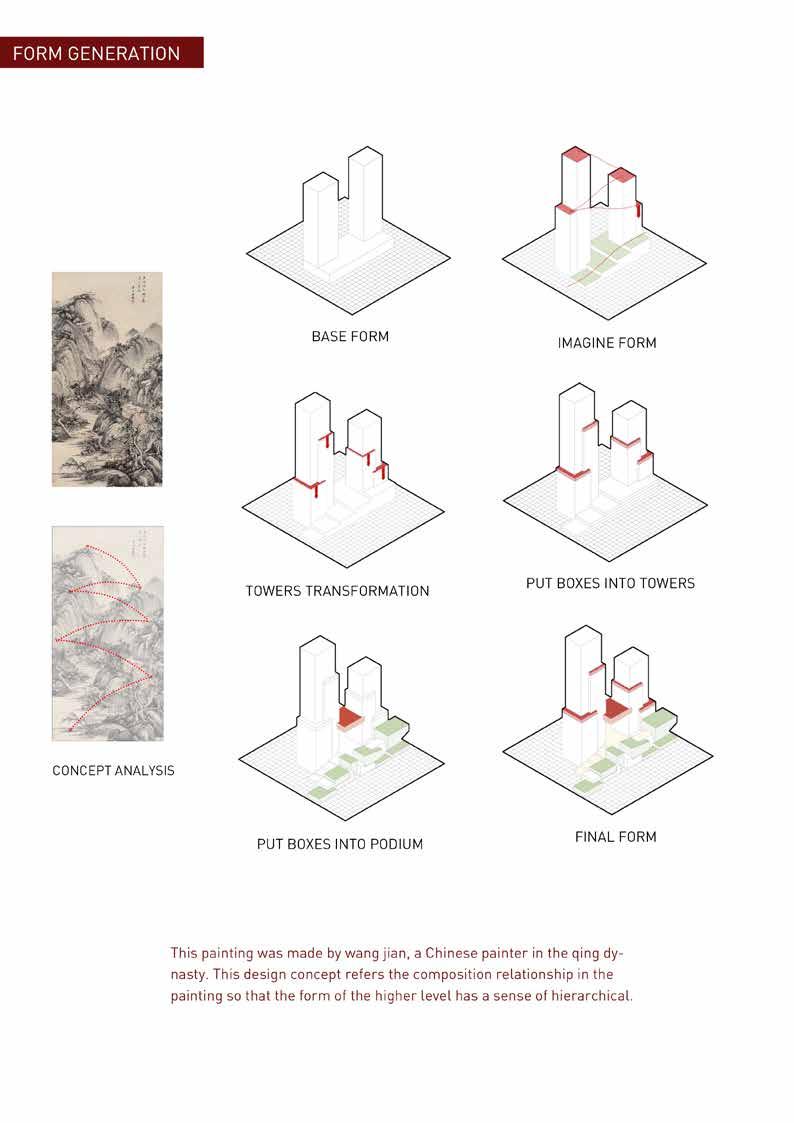
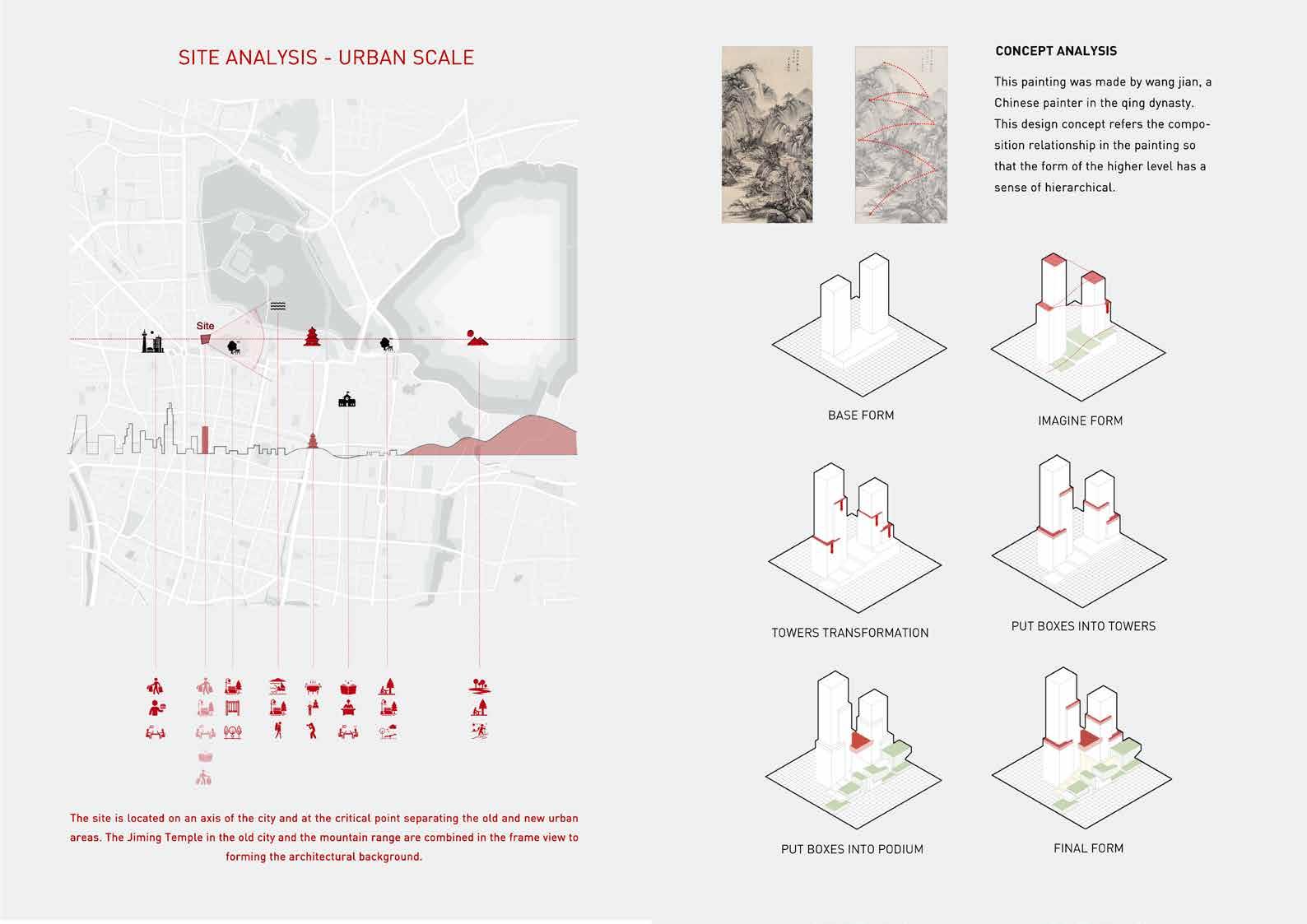
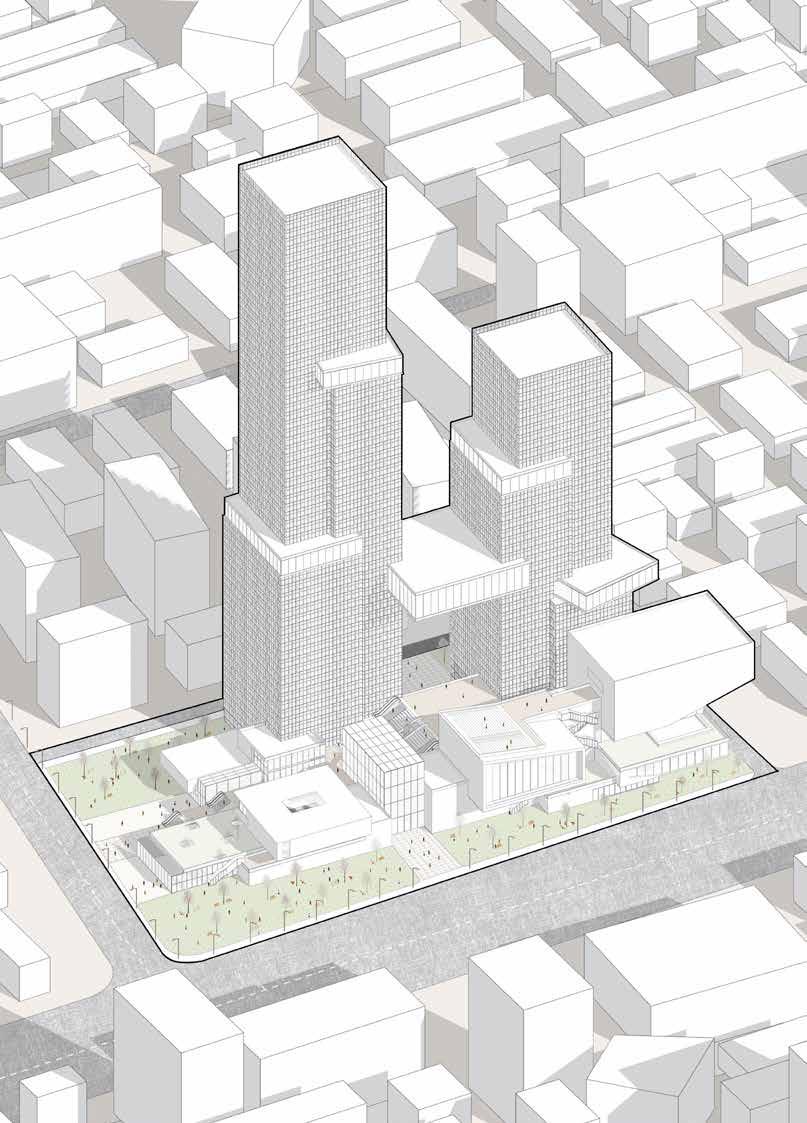
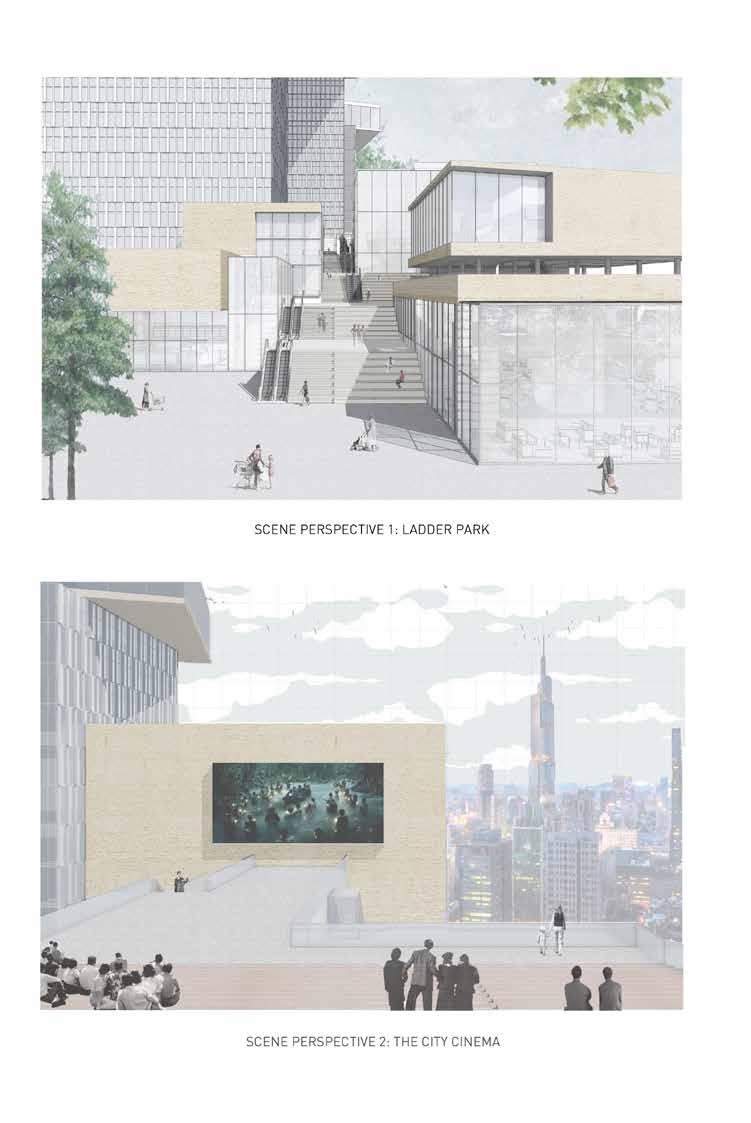
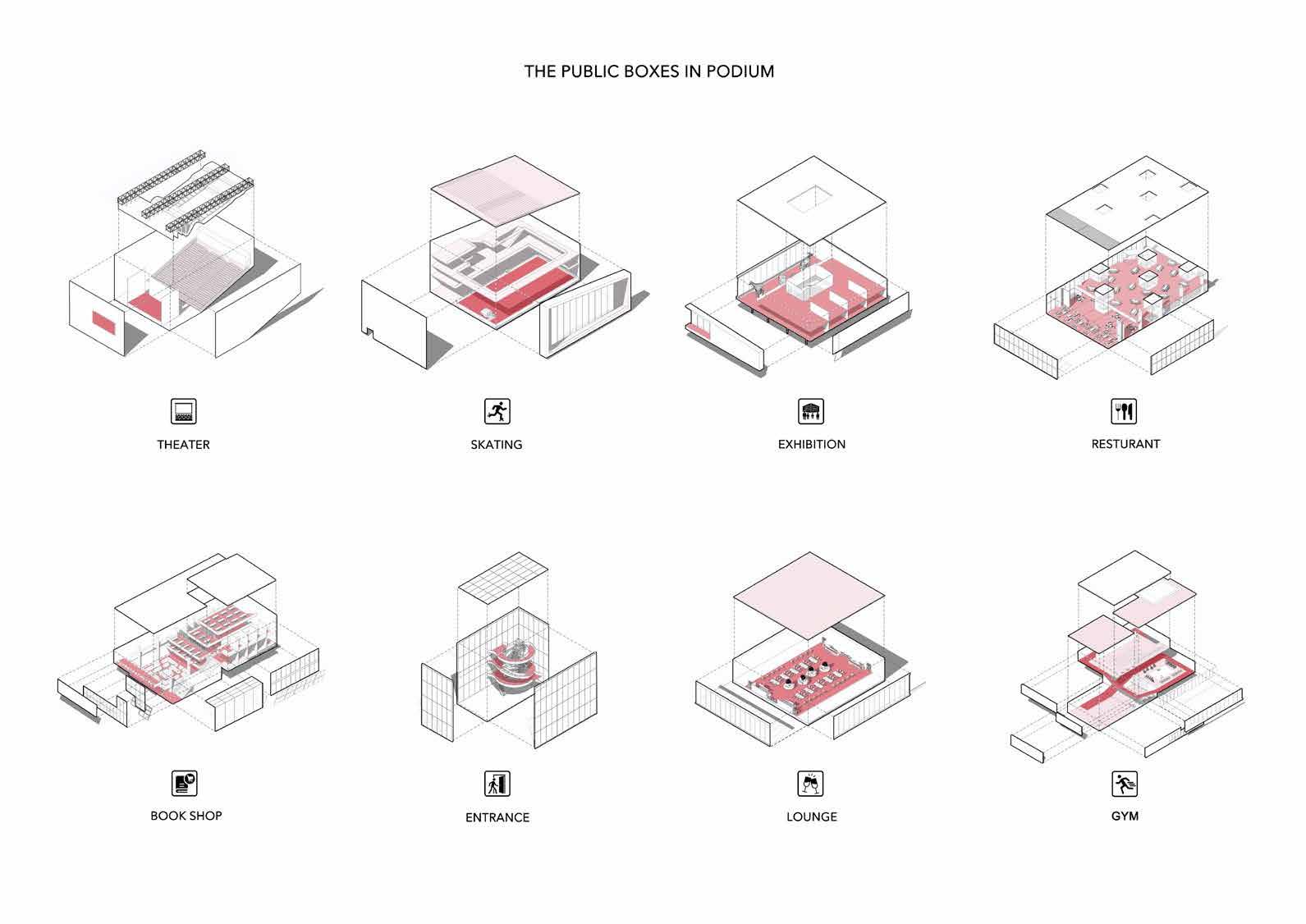
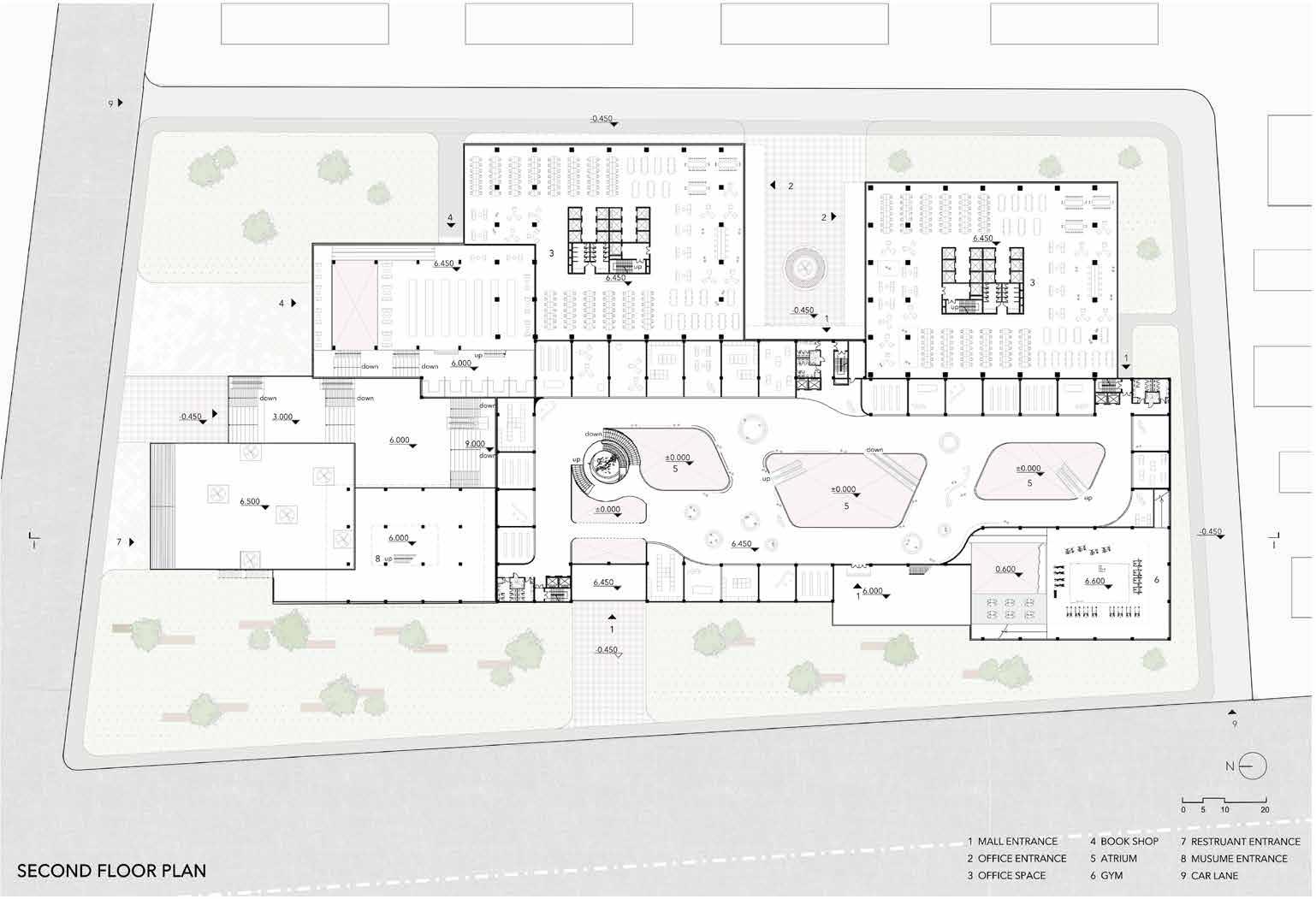
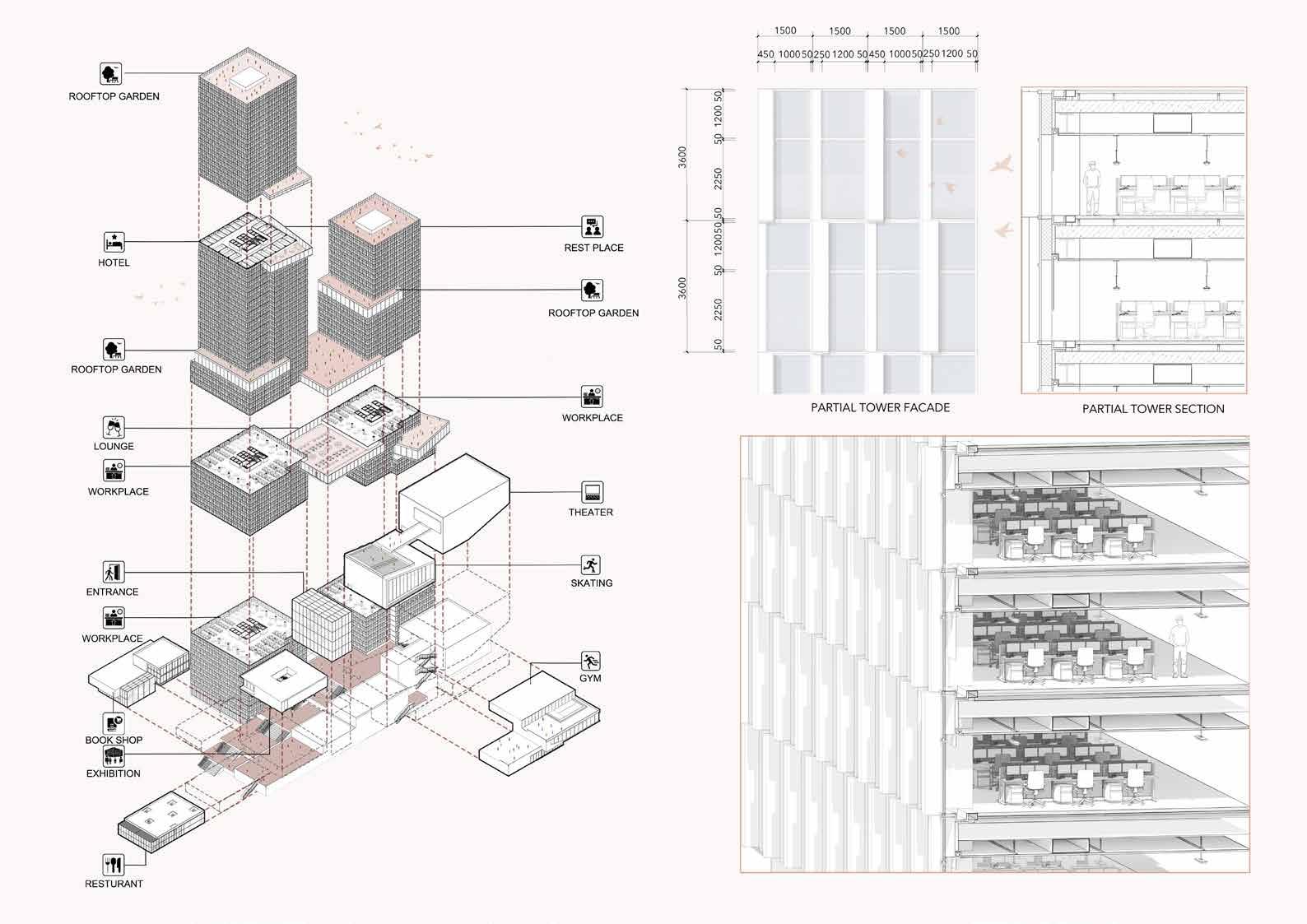
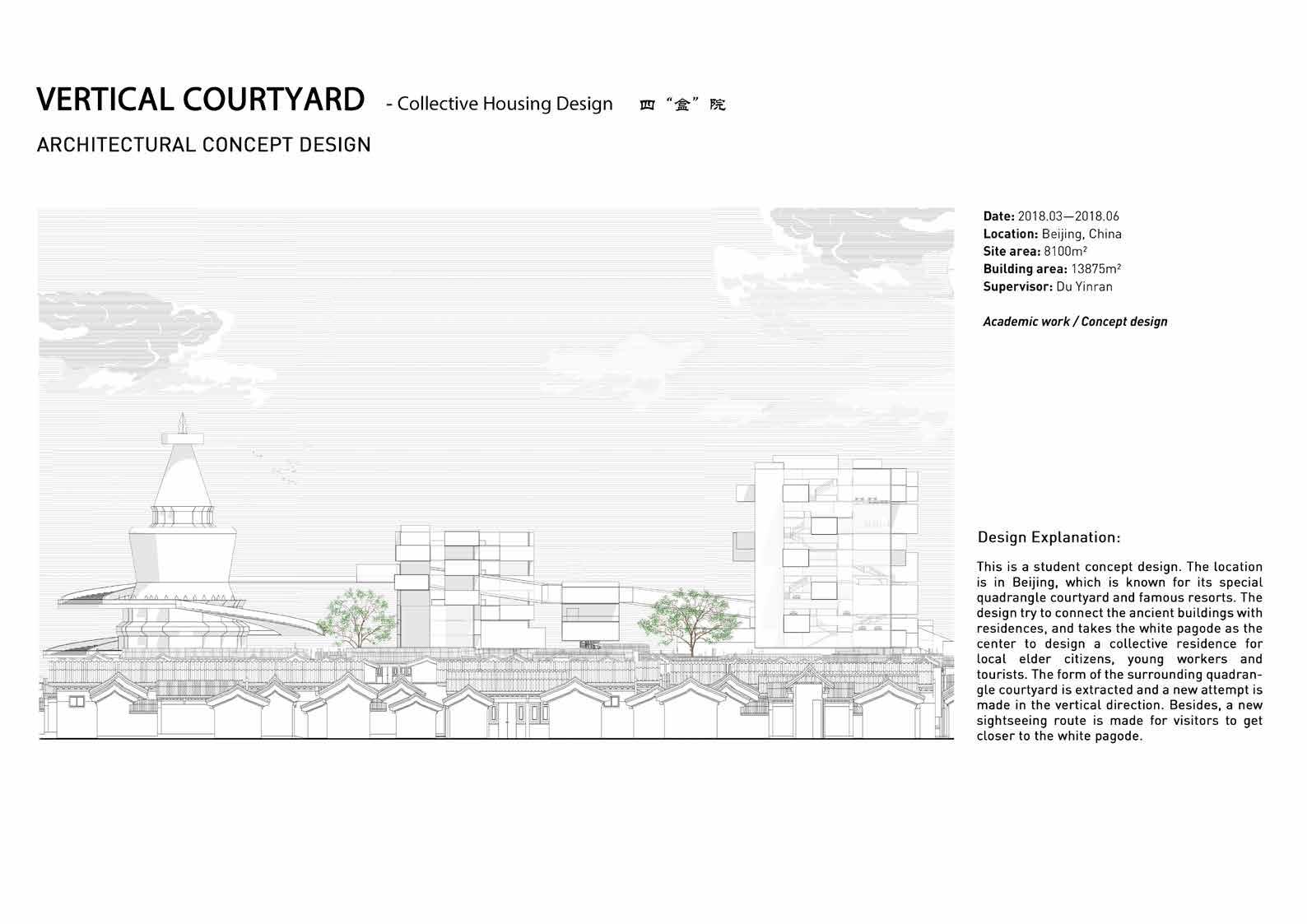
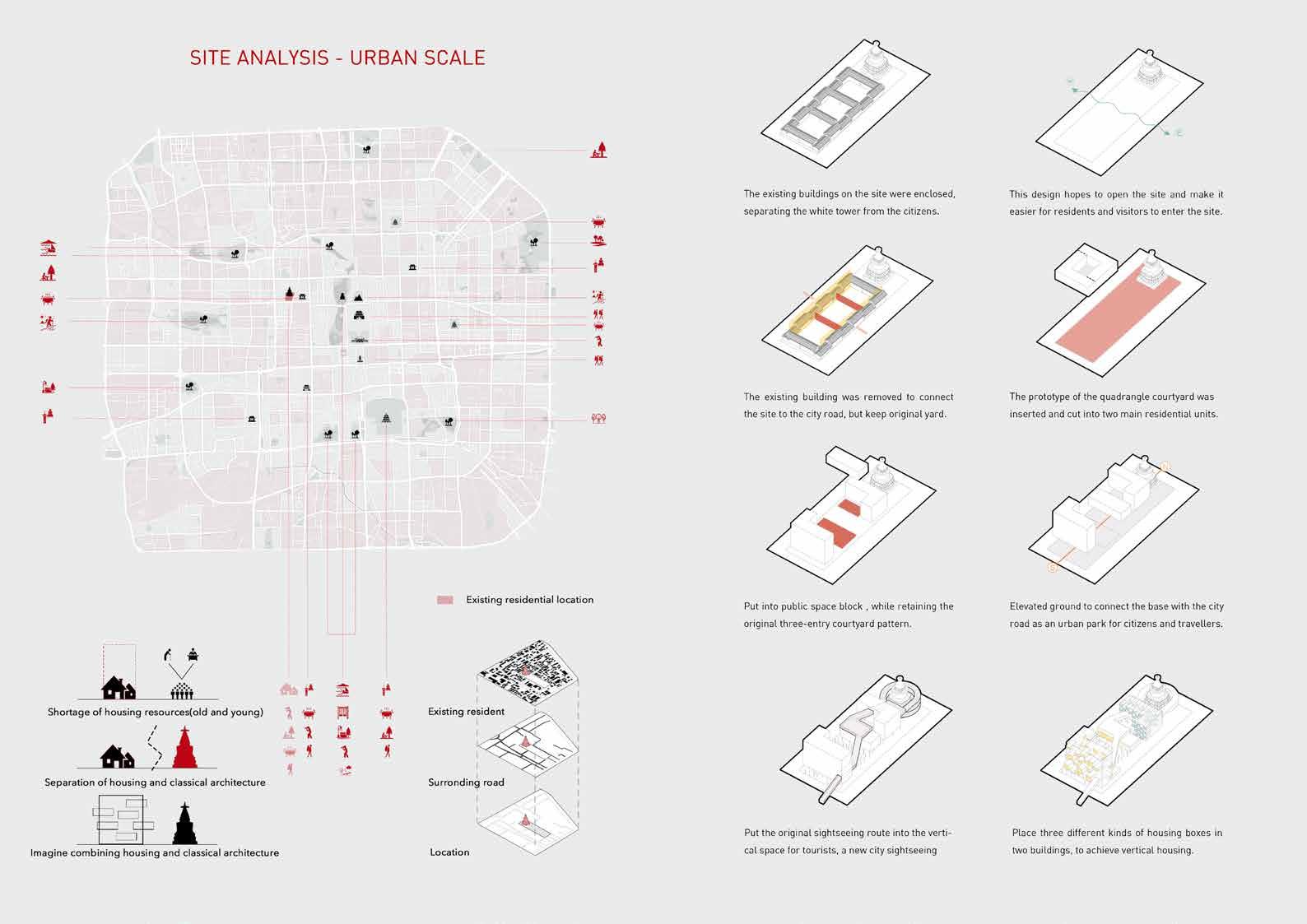
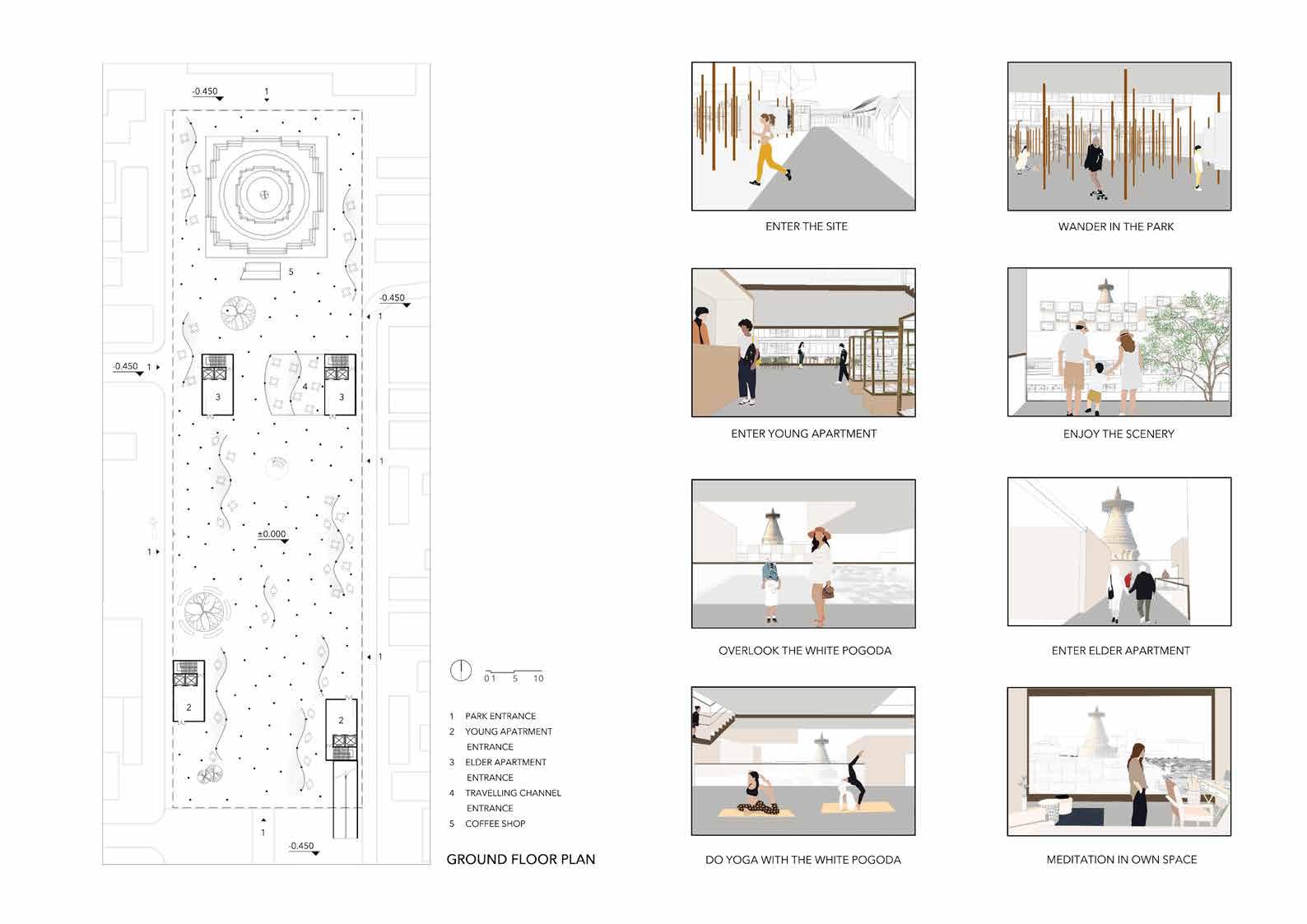
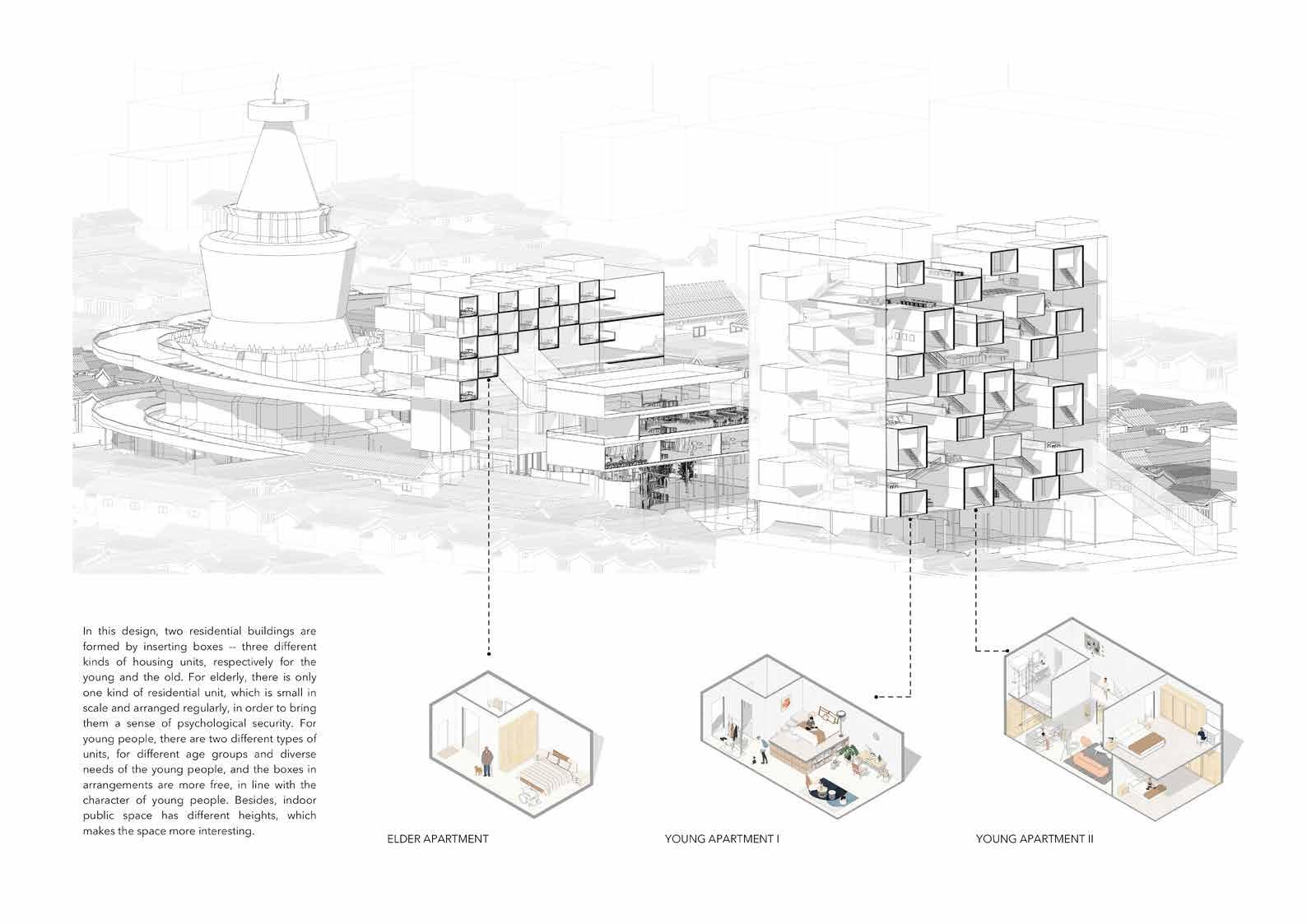
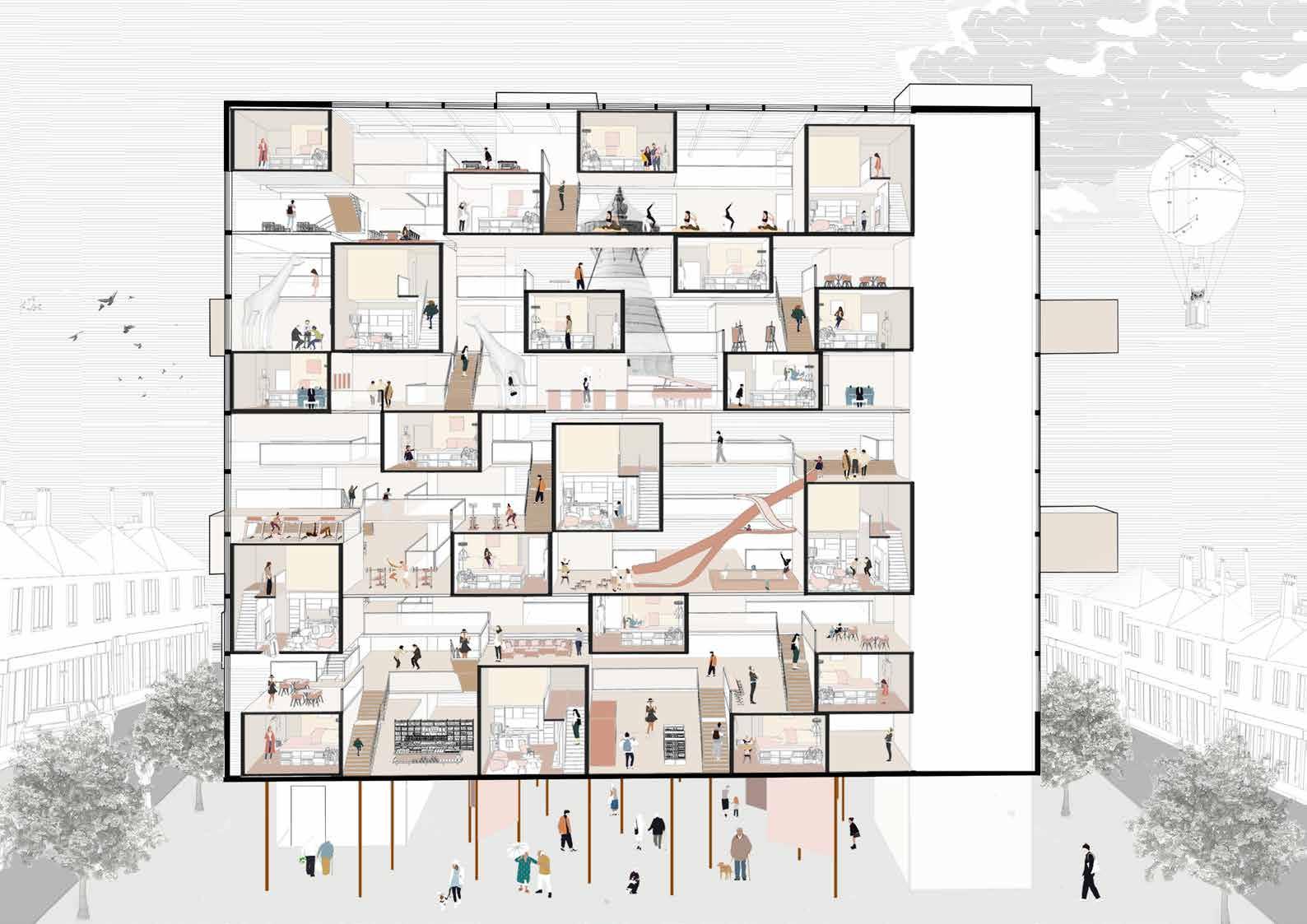
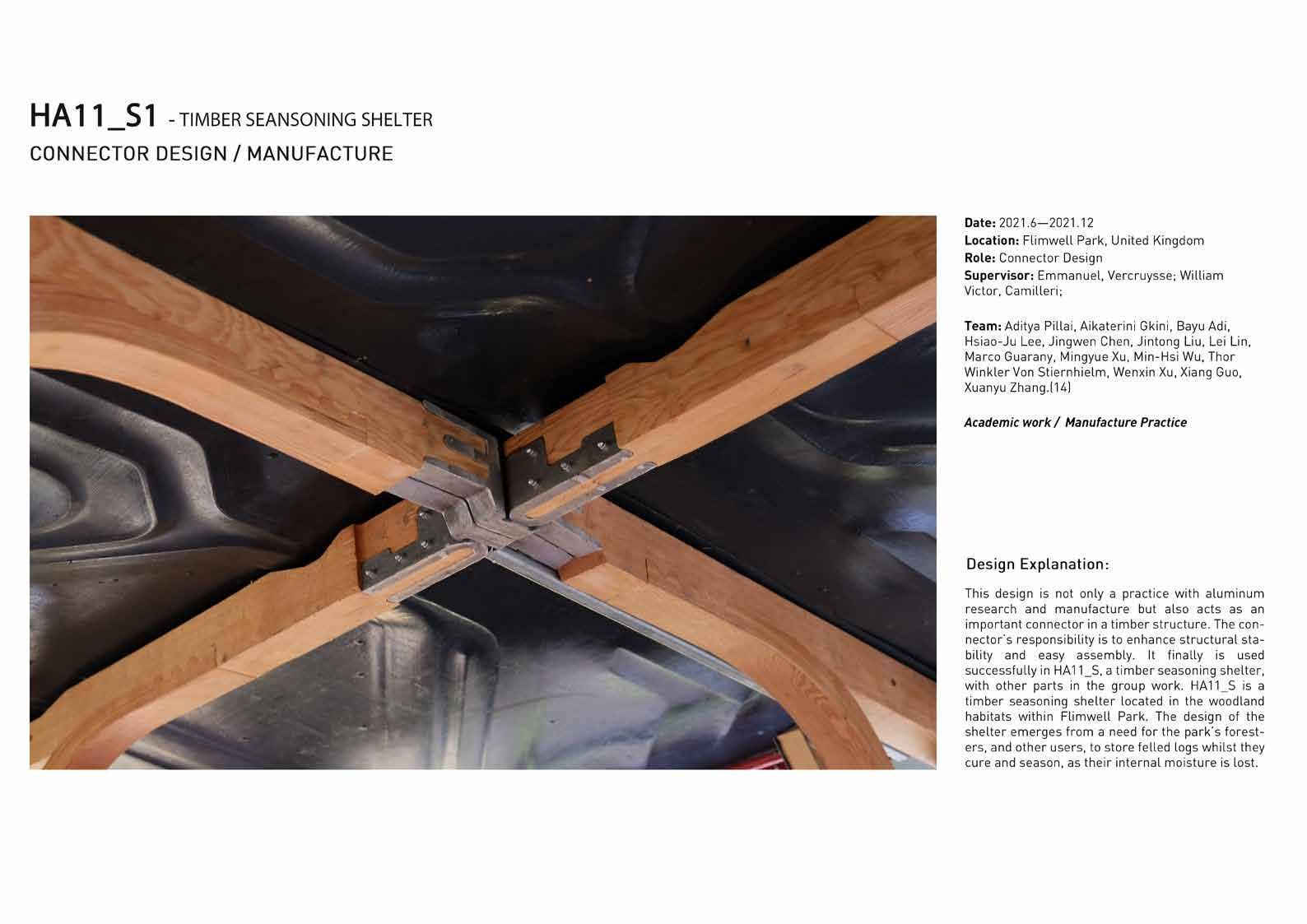
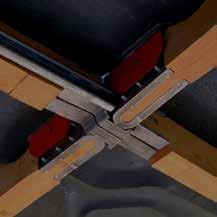
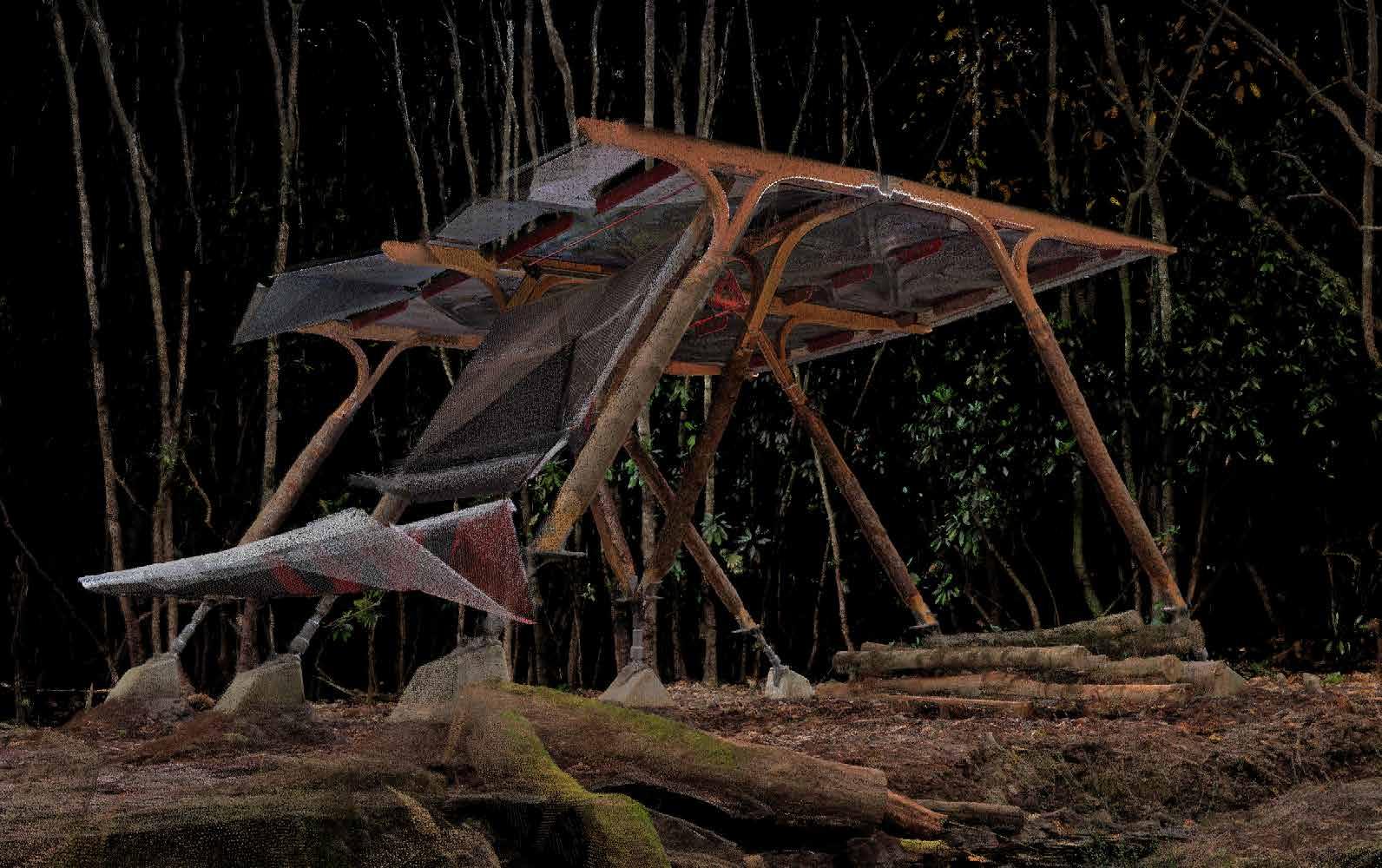
POSITION OF THE COMPONENTS IN THE WHOLE STRUCTURE
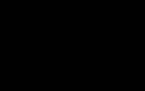
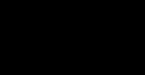
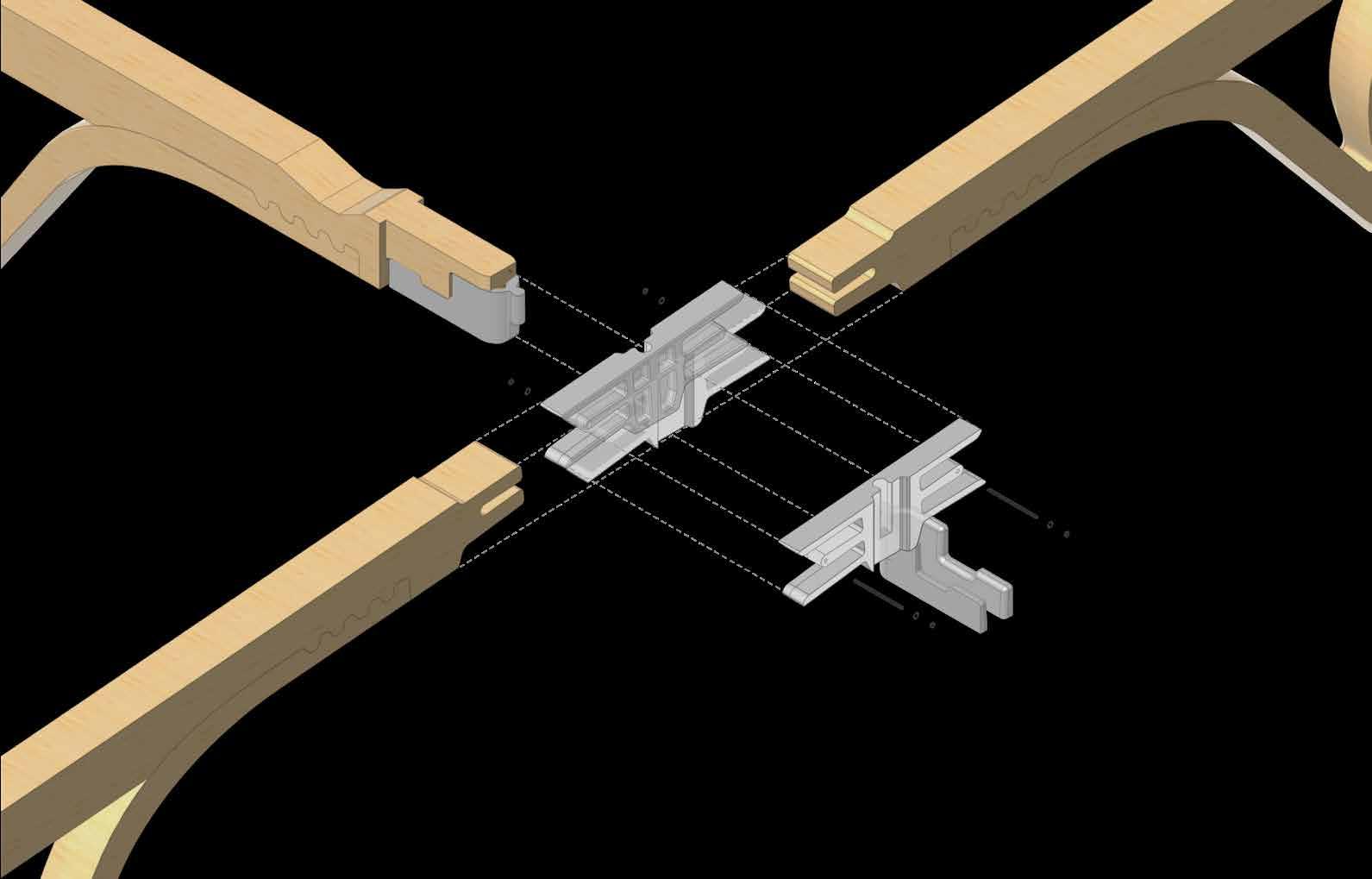

The diagrams shows how the component connect with the timber parts. Its draft angle which made during sand casting would be used as a method to grab the timber tightly.
CONNECT SLOT (67MM)
HEADLESS SCREW M4 75MM
Φ4.5 MM HOLES
MANUFACTURE METHODS:
- 3D PRINT MODEL (20H / PER)
- SAND MODEL MAKING (3H /PER)
- CASTING & FILLET (3H / PER)
- FACING (0.5H / PER)
- CNC SLOT (0.5H / PER)
- DRILL HOLES (0.5 H / PER)
- ASSEMBLY TWO PART (0.5H / PER)
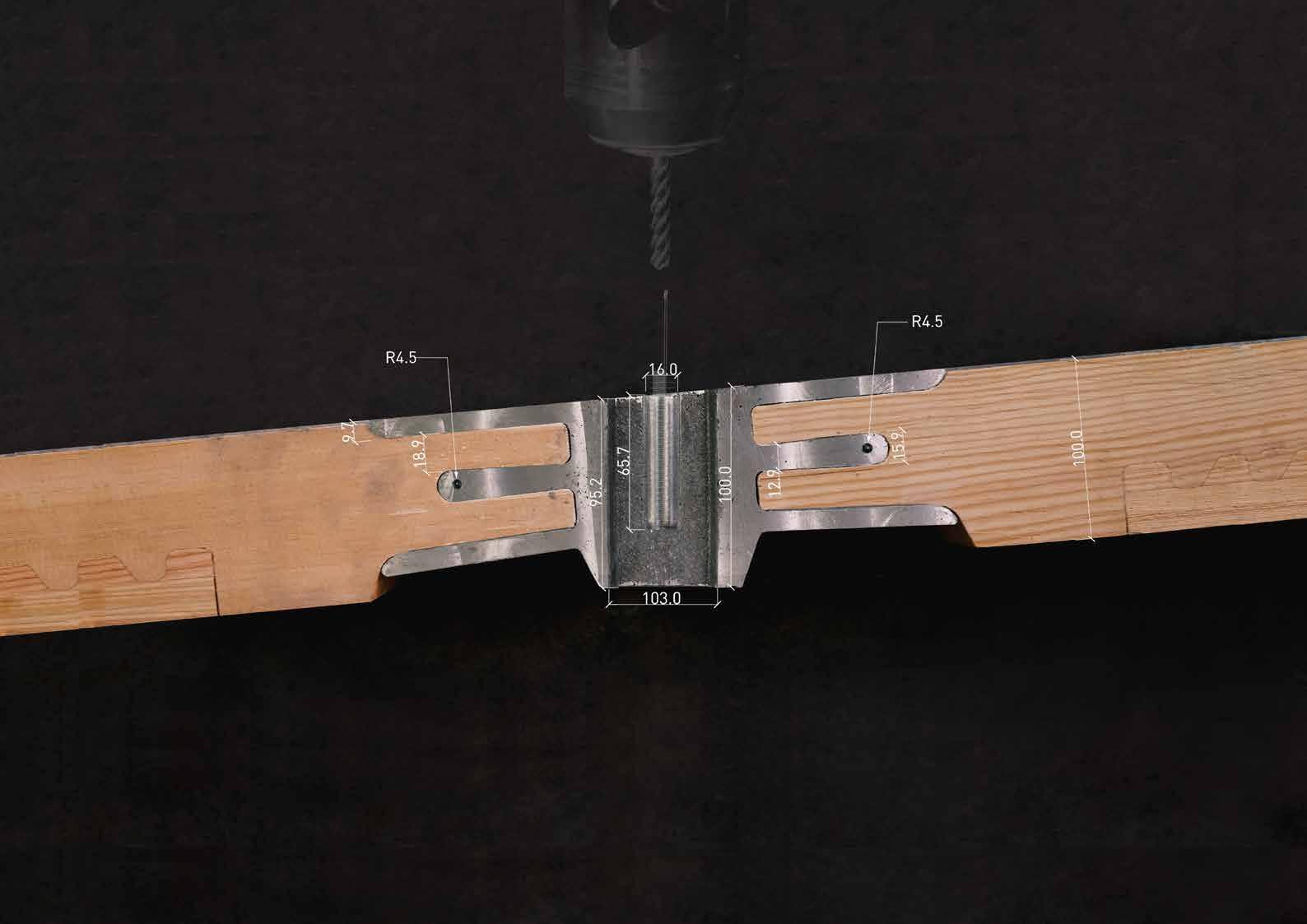
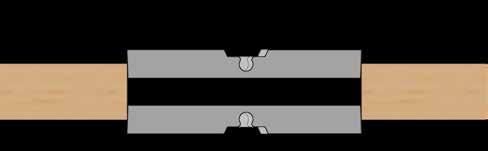
STEP1: 3D PRINT
MAKING TIME: 20.0 h / per NUMBER: 2
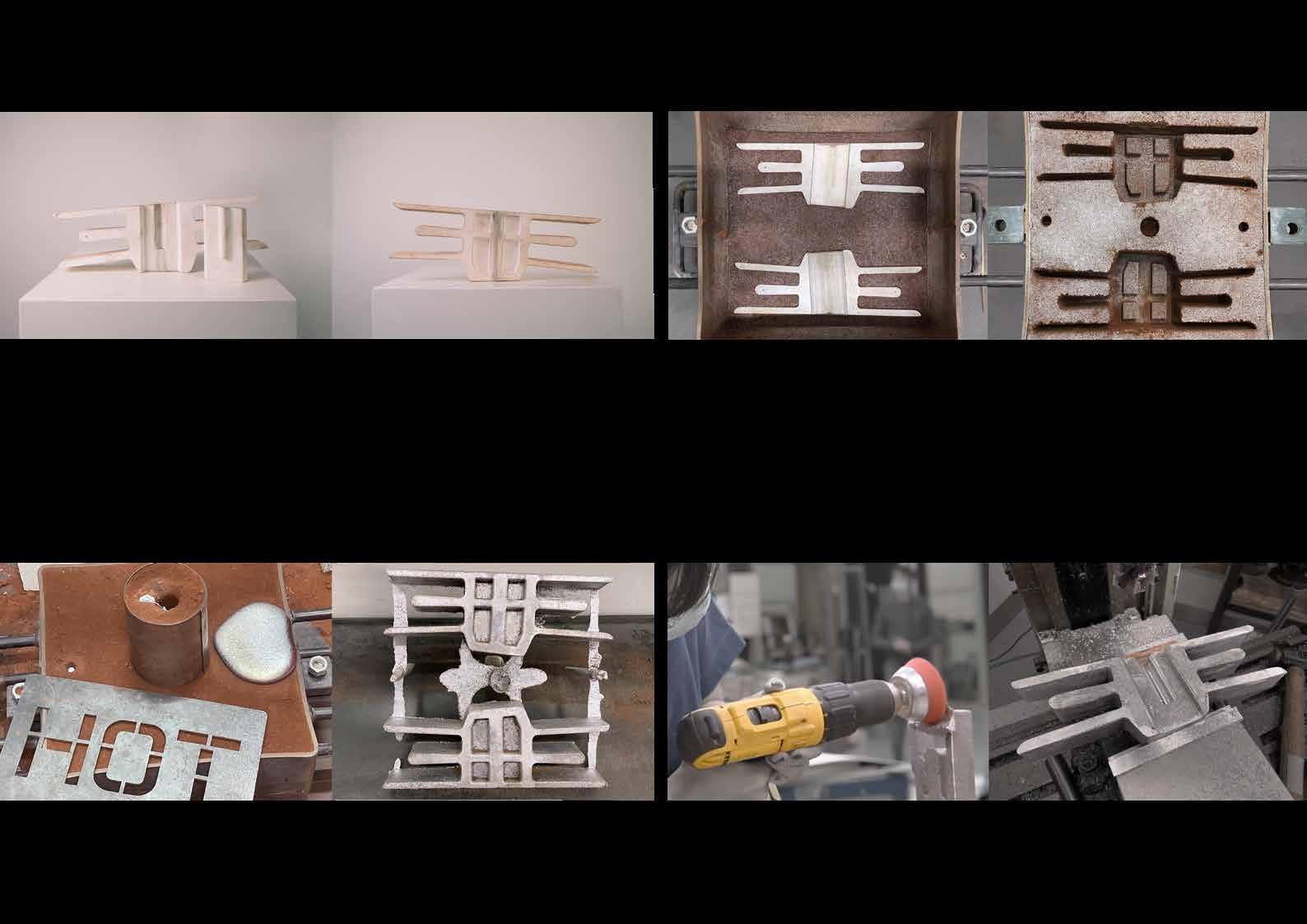
STEP3: SAND CASTING
MAKING TIME: 2.0 h / per NUMBER: 3
STEP2: SAND MODEL MAKING
MAKING TIME: 4.0 h / per NUMBER: 3
STEP4: MANULLY POLISH + FACE SURFACE
MAKING TIME: 2.0 h / per NUMBER: 6
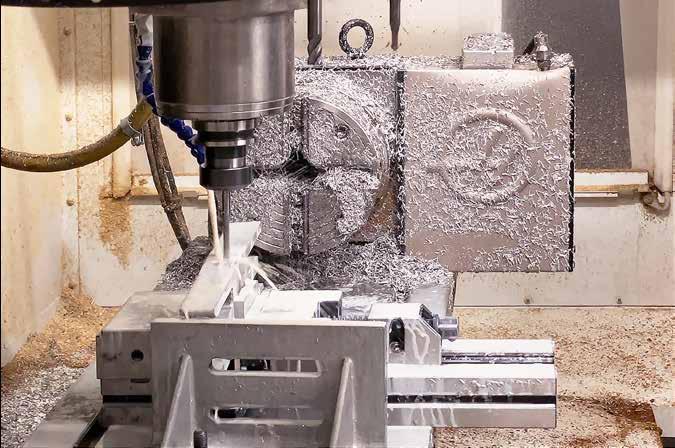
MAKING TIME: 0.5 h / per NUMBER: 6 M8 75MM
STEP5: CNC DRILL ( FOR CONNECTION SLOT)
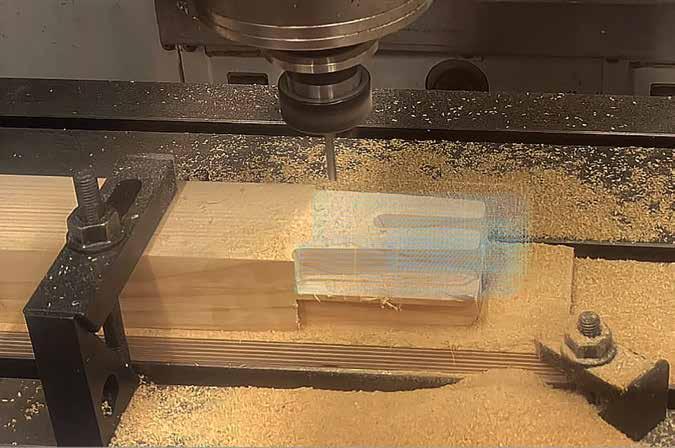
STEP6: CNC MILLING ( FOR CONNECT TESTING)
MAKING TIME: 0.5 h / per NUMBER: 2
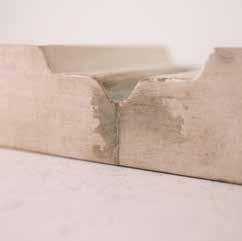
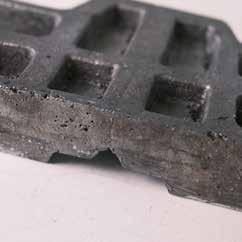
Remain the gap when glue two parts together for CNC location after casting.
Take this point as ‘Original point’ when use CNC drilling the connection slots. Original point (0,0,0)
3 ° Draft angle
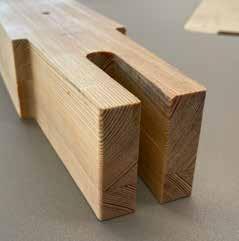
Milling the timber to match the connector front and back, keep 3° Draft Angle.
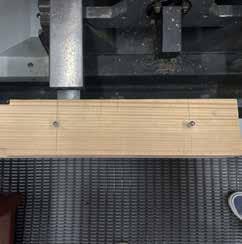
The Location pins are for making sure it stays in the same position after flipping.
Location pins
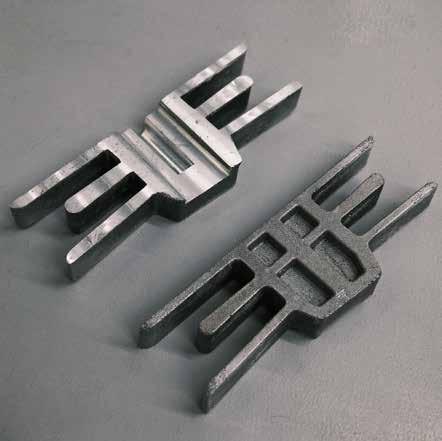
FINAL WORK - TWO PART THE SLOT DETAIL
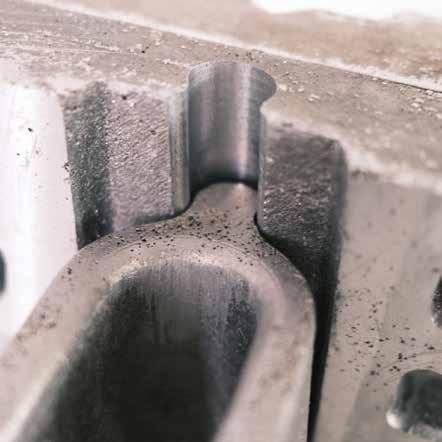
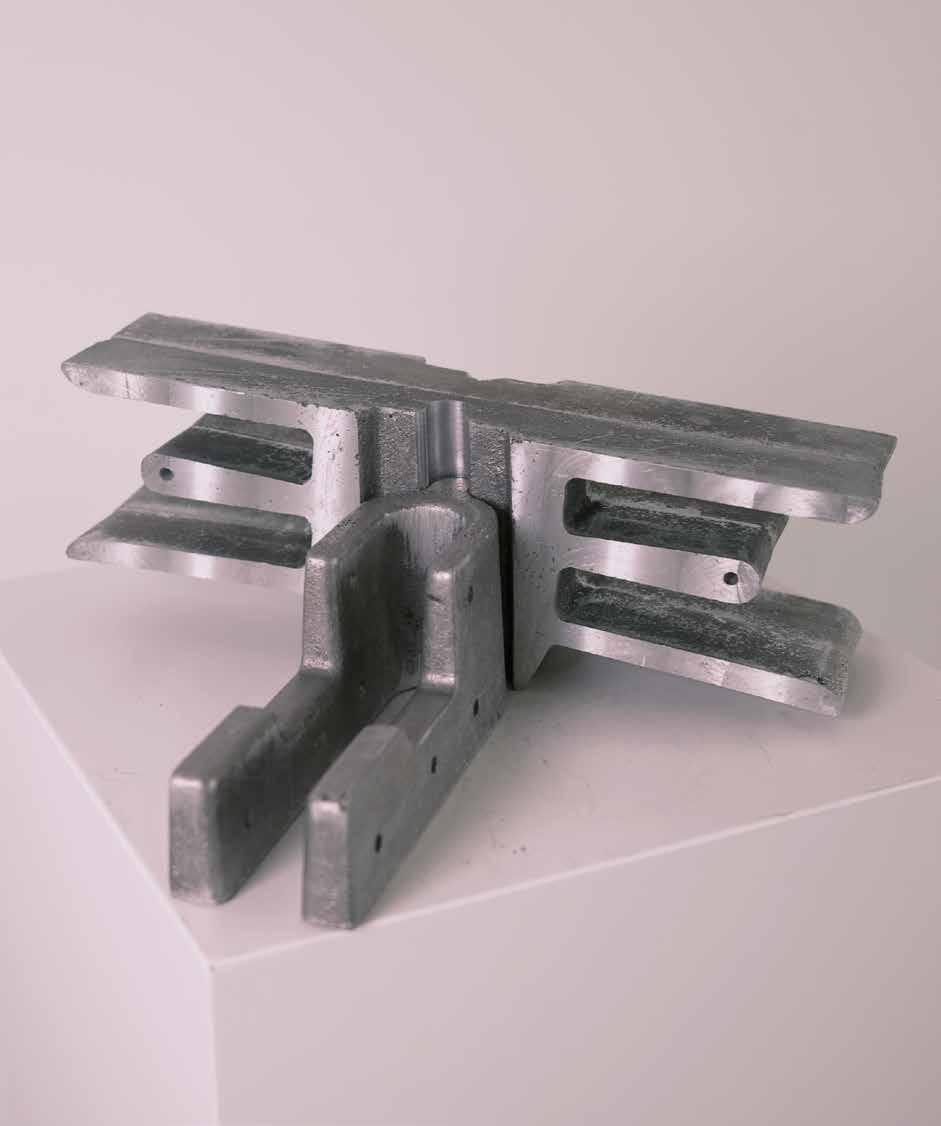
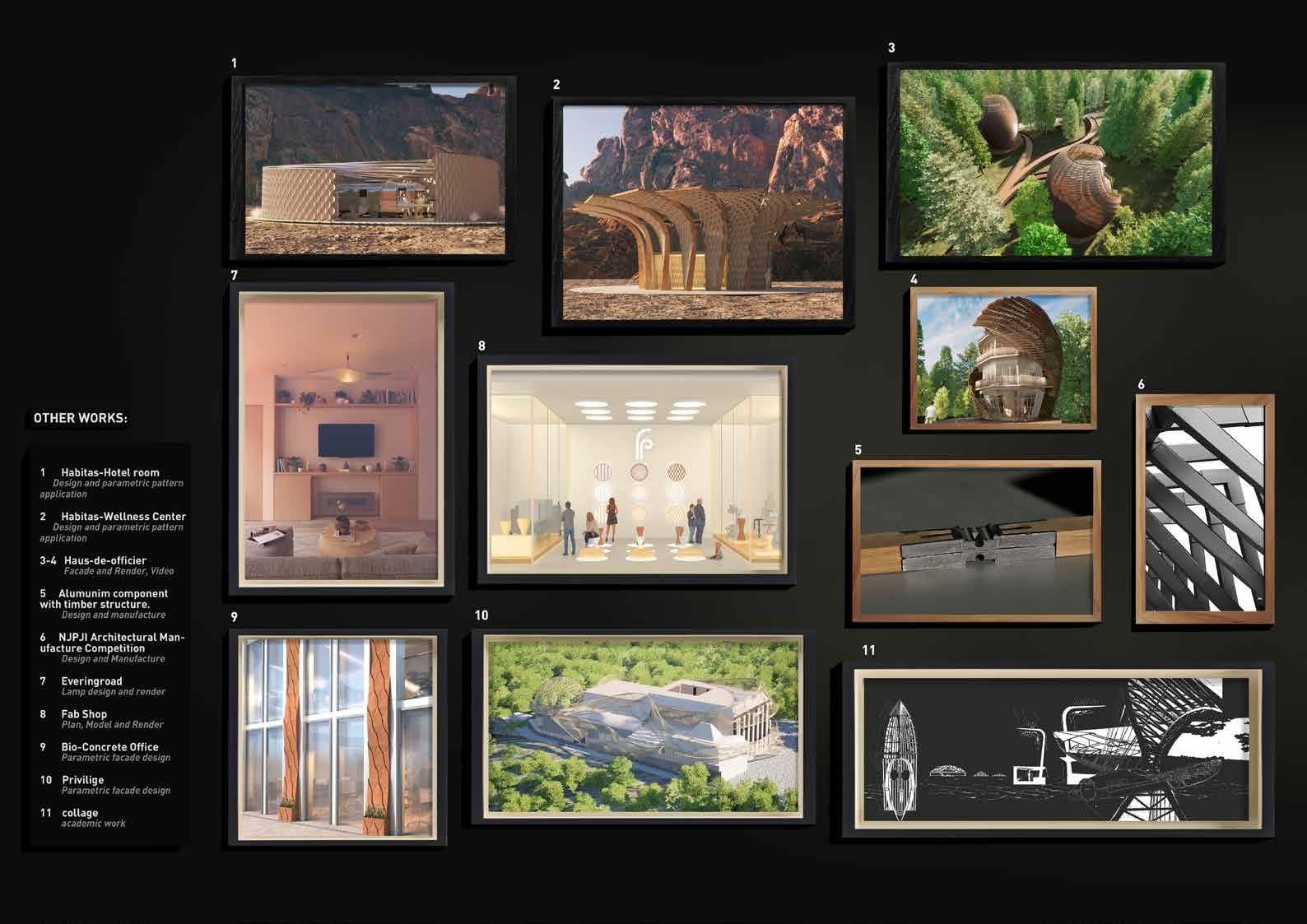