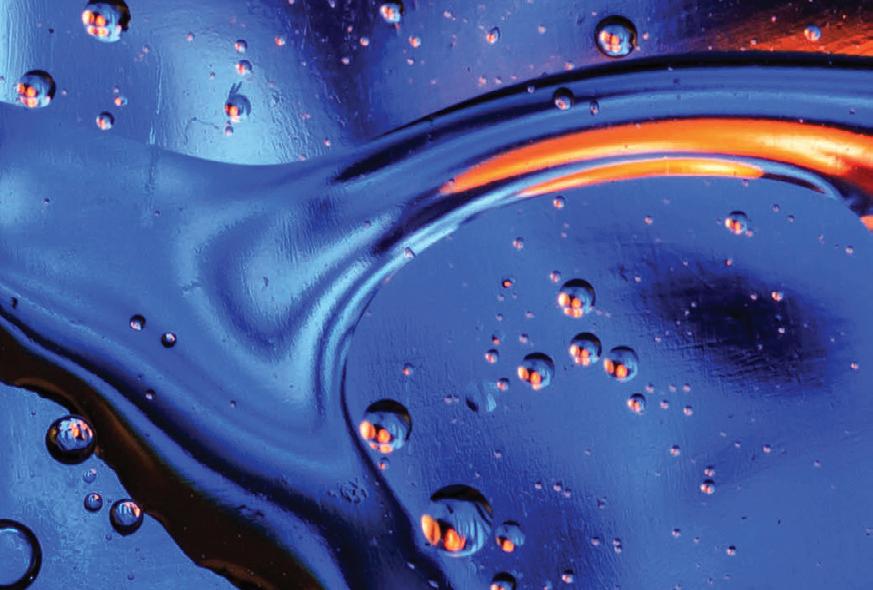
5 minute read
Mixing incompatible fluids
©stock.adobe.com/au/Shcherbyna Mixing incompatible fluids
Researchers from Flinders University have developed a technique that allows liquids that are usually immiscible to be successfully combined without the use of harsh chemicals. The technique has been built on 10 years of research and has been led by Professor Colin Raston, who was recognised as one of South Australia’s scientists of the year in 2020.
The technique relies on the Flinders vortex fluidic device (VFD), which is able to mix incompatible fluids together using a system of currents, microfluidics, high shear flow chemistry, high heat and mass transfer, along with a simple solvent. Through its use, emulsions are avoided, meaning that the liquids are perfectly blended. The technique can also be used to de-mix certain liquids.
The research, published in the Chemical Science journal, outlines the exact technique with a dizzying array of highly technical chemistry. The scientists have been working on increasing the size of their vortex fluid device so that it can breach the field of pure science and be used in industrial fields. By utilising the method it is predicted that a range of industries, including food processing and drug development, could reduce the chemical impact of mixing liquids as they would not need to rely on harsh surfactants for the mixing process. The VFD has already been used elsewhere in food production to produce better fish oil, manipulate a useful milk protein and was even able to unboil egg protein, a discover that netted the researchers an Ig Nobel prize.
These chemicals can often leave undesirable waste products behind so reducing their use is a step towards a greener and cleaner form of chemistry, the researchers say, and would thus reduce pollution into waterways.
“Mixing immiscible liquids is fundamentally important in process engineering and usually involves a lot of energy input and waste products,” said Professor Raston, who was the senior author of the paper.
“We now demonstrate how this process, using a common solvent and water, can avoid the use of other substances for controlling reactions across immiscible liquids, making it cleaner and greener.”
Flinders University www.flinders.edu.au
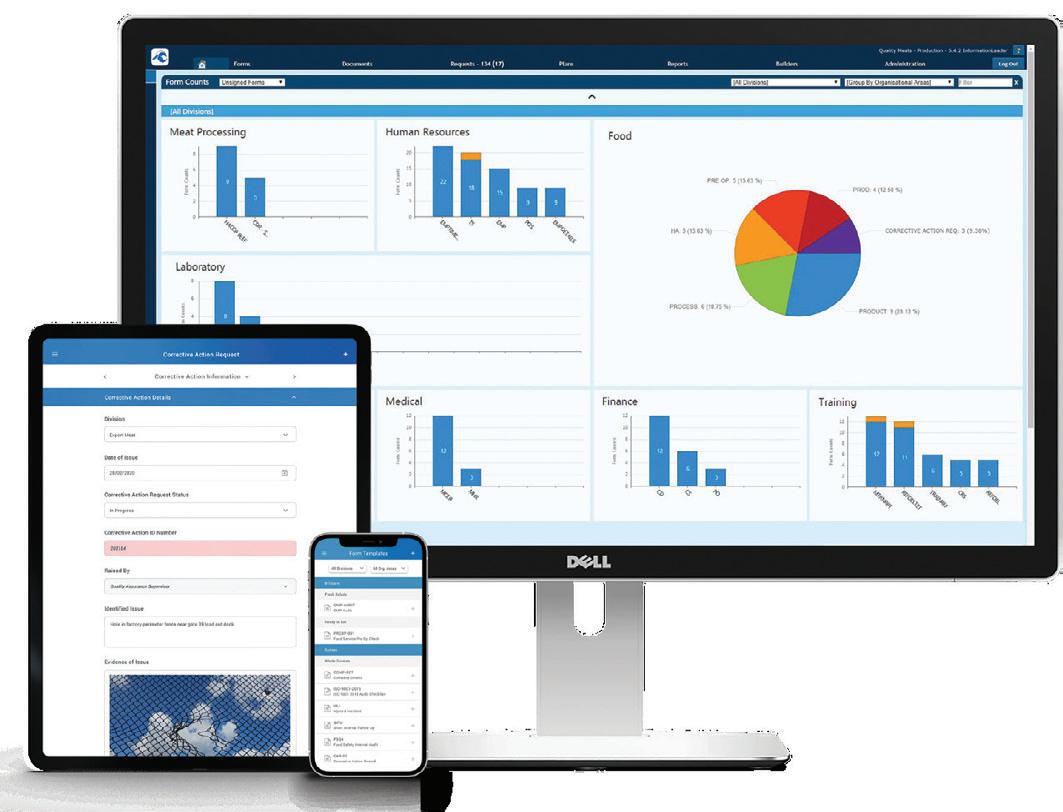
Laser sintering material for 3D printing
igus is expanding the scope of its 3D printing service: chemical-resistant, lubrication-free tribo-polymer components can be manufactured using selective laser sintering (SLS). This has been made possible by a new printing material for laser sintering printers called iglidur I10, which is resistant to acids, bases, alcohols as well as greases and therefore suitable for use in electroplating and food processing plants. The 3D filaments are also available to purchase directly from Treotham.
The laser sintering printing material iglidur I10 is resistant to acids, bases, alcohols, greases and oils. It is also characterised by low moisture absorption, high toughness and high ductility — which indicates the property of a material to deform permanently under shear load before breaking. It is therefore suitable for weightsaving industrial functional components with elastic properties.
The printing material is FDA-compliant, making it suitable for applications in the packaging and food industries. It also complies with EU Regulation 10/2011, which certifies that the plastic is harmless in contact with food.
Treotham will also offer the new printing material via the igus 3D printing service.
Treotham Automation Pty Ltd
www.treotham.com.au
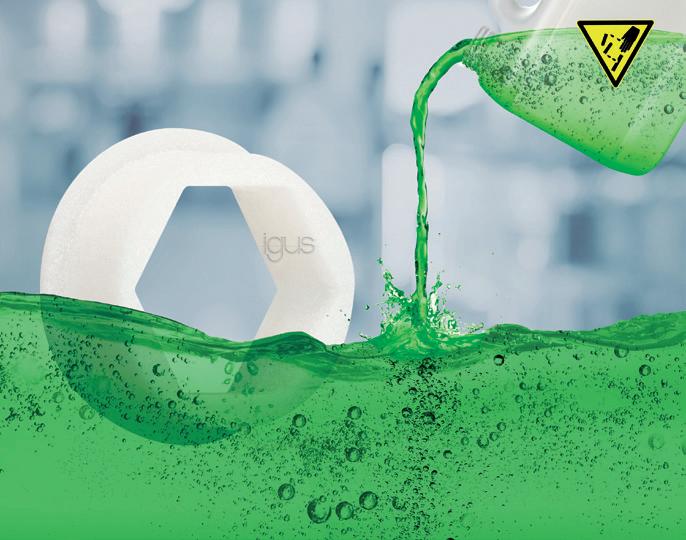
Auger feeders
Sterling Systems & Controls auger-type screw feeders are used within ingredient batching systems for food processing, feed milling and many other industrial applications.
Each end of the feeder incorporates industrial-grade bearings to support the auger, thereby preventing contact with its housing.
Seals are located between the product zone and auger bearings. An air gap between the bearing and seal plates creates a buffer zone to ensure the material doesn’t enter the bearings and lubricant doesn’t enter the material.
Keeping the auger in suspension using shaft clamps is key to ensuring that the thrust load is not transferred to the drive assembly, which therefore increases drive life. Shock-absorbing couplings are used to help reduce the start/stop shock on the motor/drive.
Sterling Systems and Controls Inc
www.sterlingcontrols.com
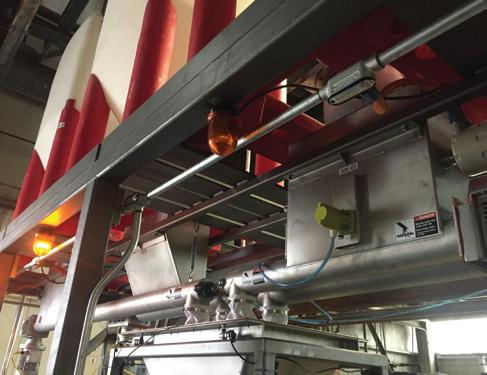
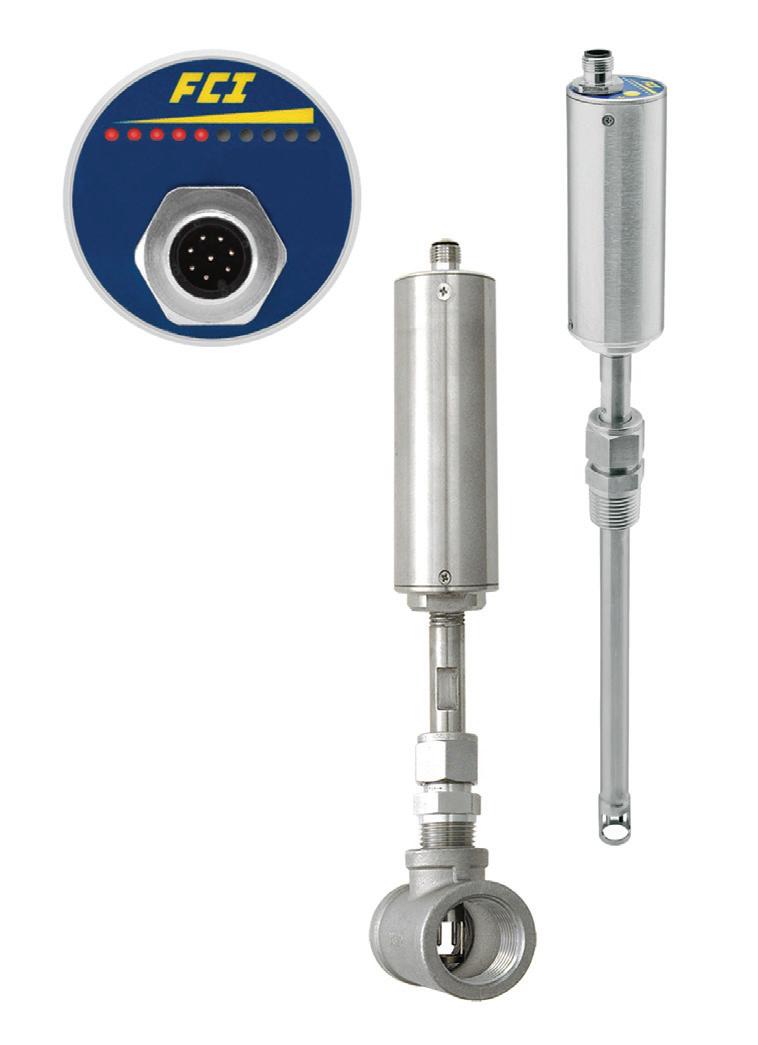
Compressed air thermal flow meter
Process and manufacturing engineers responsible for compressed air systems used in a wide range of industrial applications will find the FS10i Series compressed air flow meters from Fluid Components International (FCI) can help them improve productivity by measuring accurately and quickly detecting system leaks, which can improve overall process quality while reducing system energy costs.
The compact easy-to-install units can measure the flow rate of compressed air, air and natural gas. They are accurate to ± 1.5% of reading and ±0.5% of full scale, with repeatability of ± 0.5% of reading and a response time of 4 seconds (1 time constant). They are SIL-2 rated for safety instrumented system (SIS) critical processes.
Using thermal dispersion flow sensing technology, the flow meters provide a fluid-matched, calibrated and linearised 4–20 mA output of flow rate, and a user programmable high or low flow alarm/ trip point with a 1 A SPDT relay output. For visual indication, the flow meters include a 10-segment LED array. This display illuminates proportionally to the flow rate and flashes if an alarm trip occurs.
Available in both in-line and insertion style configurations to support installation in line sizes from DN25 to DN500, they operate over a 100:1 turndown from 1,6 to 122 NCMH depending on the fluid media and line size.
Each meter is precision calibrated on FCl’s air and gas flow stands, which are outfitted with NIST and ISO/IEC 17025 traceable equipment to ensure their accuracy and measurement repeatability.
AMS Instrumentation & Calibration Pty Ltd
www.ams-ic.com.au
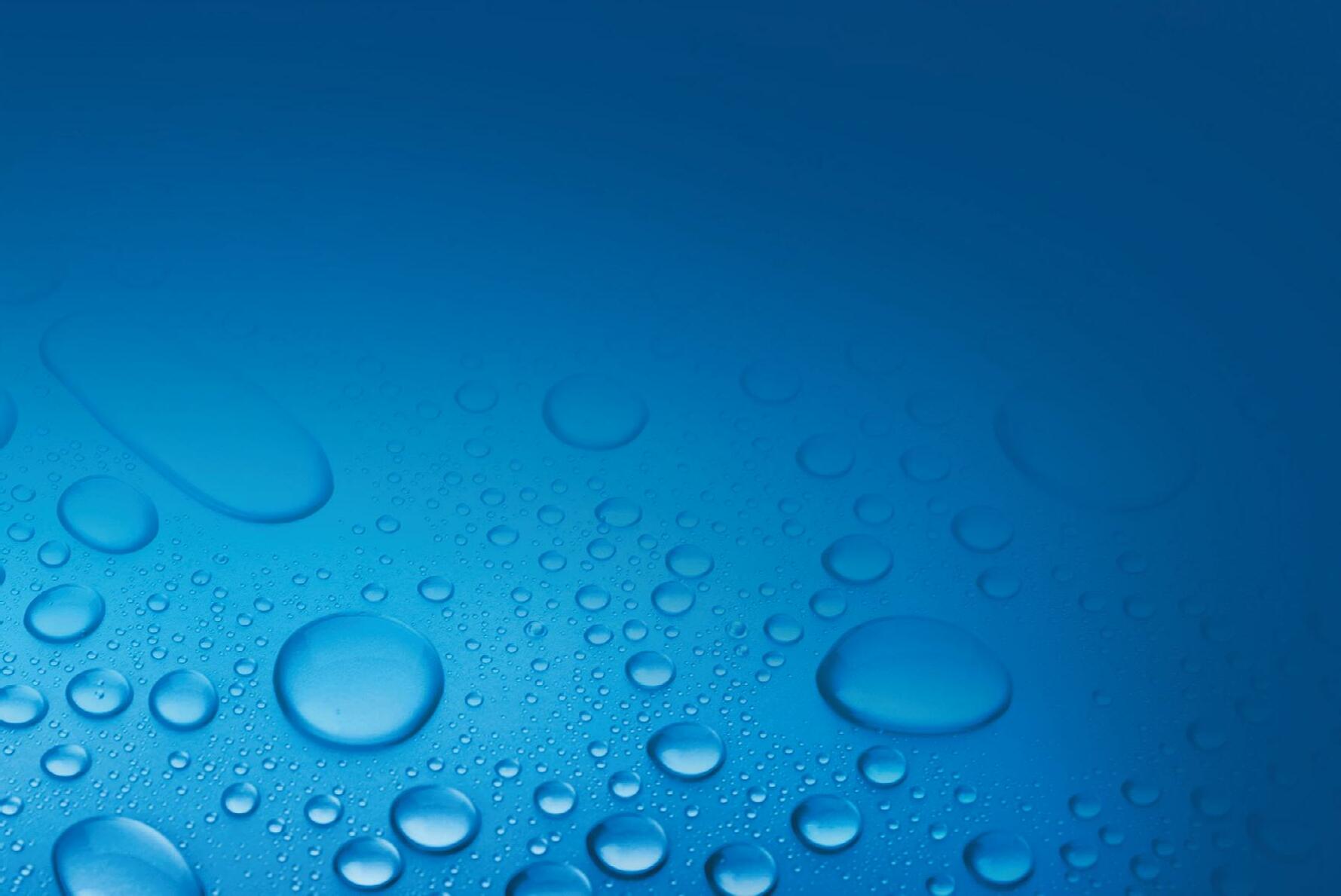
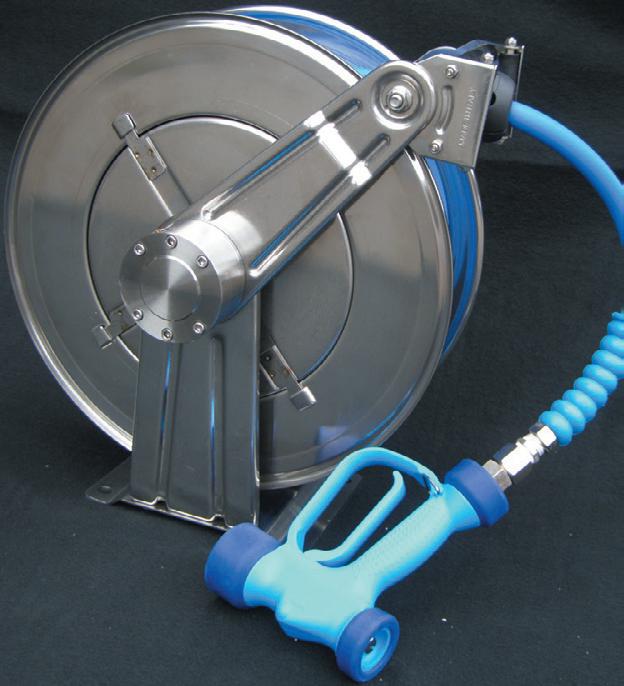
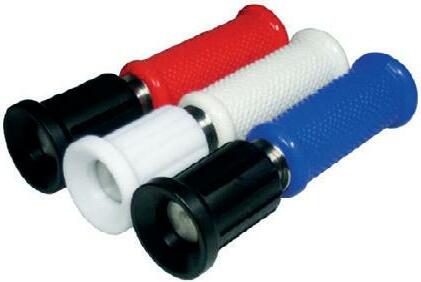