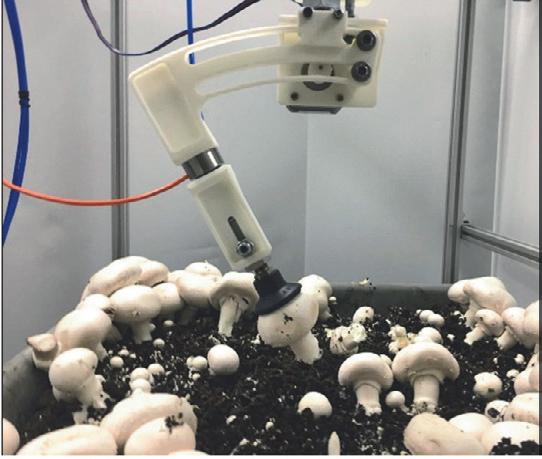
4 minute read
Mushroom robot
The prototype, which is designed to be integrated with a machine vision system, showed that it is capable of both picking mushrooms with a pneumatic system (above) and trimming them.

The button mushroom — Agaricus bisporus — is an important agricultural commodity. Approximately 404 million kg of button mushrooms valued at $1.13 billion were consumed in the US within one year (2017–18).
Because 91% of the mushrooms consumed come from the fresh market, labour costs for harvesting mushrooms account for around 15% to 30% of the production value. Therefore, mechanical or robotic picking could help to alleviate the associated labour shortage issues and costs, so researchers looked for a solution.
Researchers at Penn State’s College of Agricultural Sciences have now developed a robotic mechanism for automated harvesting of button mushrooms. The prototype uses a pneumatic system that has been designed to be integrated with a machine vision system. It has been shown to be capable of both picking and trimming mushrooms growing in a shelf system.
Developing a device to effectively harvest mushrooms was a complex endeavour, explained the lead author of this study, Long He, assistant professor of agricultural and biological engineering. In hand-picking, a picker first locates a mature mushroom and detaches it with one hand, typically using three fingers. A knife, in the picker’s other hand, is then used to remove the stipe end. Sometimes the picker waits until there are two or three mushrooms in hand and cuts them one by one. Finally, the mushroom is placed in a collection box. A robotic mechanism had to achieve an equivalent picking process.
The researchers designed a robotic mushroom-picking mechanism that included a picking ‘end-effector’ based on a bending motion, a ‘4-degree-of-freedom positioning’ endeffector for moving the picking end-effector, a mushroom stipe-trimming end-effector and an electro-pneumatic control system. They fabricated a laboratory-scale prototype to validate the performance of the mechanism.
The research team used a suction cup mechanism to latch onto mushrooms and conducted bruise tests on the mushroom caps to analyse the influence of air pressure and acting time of the suction cup.
The test results, recently published in Transactions of the American Society of Agricultural and Biological Engineers, showed that the picking end-effector was successfully positioned to the target locations and its success rate was 90% at first pick, increasing to 94.2% after second pick.
The trimming end-effector achieved a success rate of 97% overall. The bruise tests indicated that the air pressure was the main factor affecting the bruise level, compared to the suction-cup acting time, and an optimised suction cup may help to alleviate the bruise damage, the researchers noted.
The laboratory test results indicated that the developed picking mechanism has potential to be implemented in automatic mushroom harvesting.
Mobile bulk bag discharger with screw conveyor
The Flexicon Mobile Bulk Bag Discharger with Mobile Flexible Screw Conveyor allows dust-free discharging of bulk solid materials and conveying to downstream process equipment or storage vessels throughout the plant.
Mounted on locking castors, the BULK-OUT BFF Series discharger has four adjustable extension posts to accommodate bulk bags 915 to 2135 mm tall. The removable bag-lifting frame with Z-CLIP strap holders allows bulk bags to be attached at ground level, then forklifted into receiving cups on the discharger frame.
A SPOUT-LOCK clamp ring atop a pneumatically actuated TELE-TUBE telescoping tube secures the clean side of bag spout to the clean side of the equipment, and exerts continuous downward tension on the bag as it empties and elongates, promoting flow and evacuation. A vent port with filter sock contains dust.
Additional flow is afforded by FLOW-FLEXER bag activators that raise and lower opposite bottom sides of the bag at timed intervals into a steep ‘V’ shape, and top-mounted POP-TOP extension devices that elongate the entire bag, promoting total discharge with no manual intervention.
The discharge housing of the mobile flexible screw conveyor is supported by a mast affixed to the mobile discharger frame, allowing the transfer of free- and non-free-flowing bulk materials to multiple destinations.
The flexible screw is the only moving part contacting material and is driven by an electric motor beyond the point at which material is discharged, preventing material contact with seals.
The entire unit can be rolled to a cleaning station. A lower clean-out cap on the conveyor tube can be removed to flush the smooth interior surfaces with steam, water or cleaning solutions, or to fully remove the flexible screw for cleaning and inspection.
The system is available in carbon steel with durable industrial coating and stainless steel material contact surfaces, or in all stainless steel finished to industrial, food, dairy or pharmaceutical standards.
Flexicon Corporation (Aust) Pty Ltd
www.flexicon.com.au

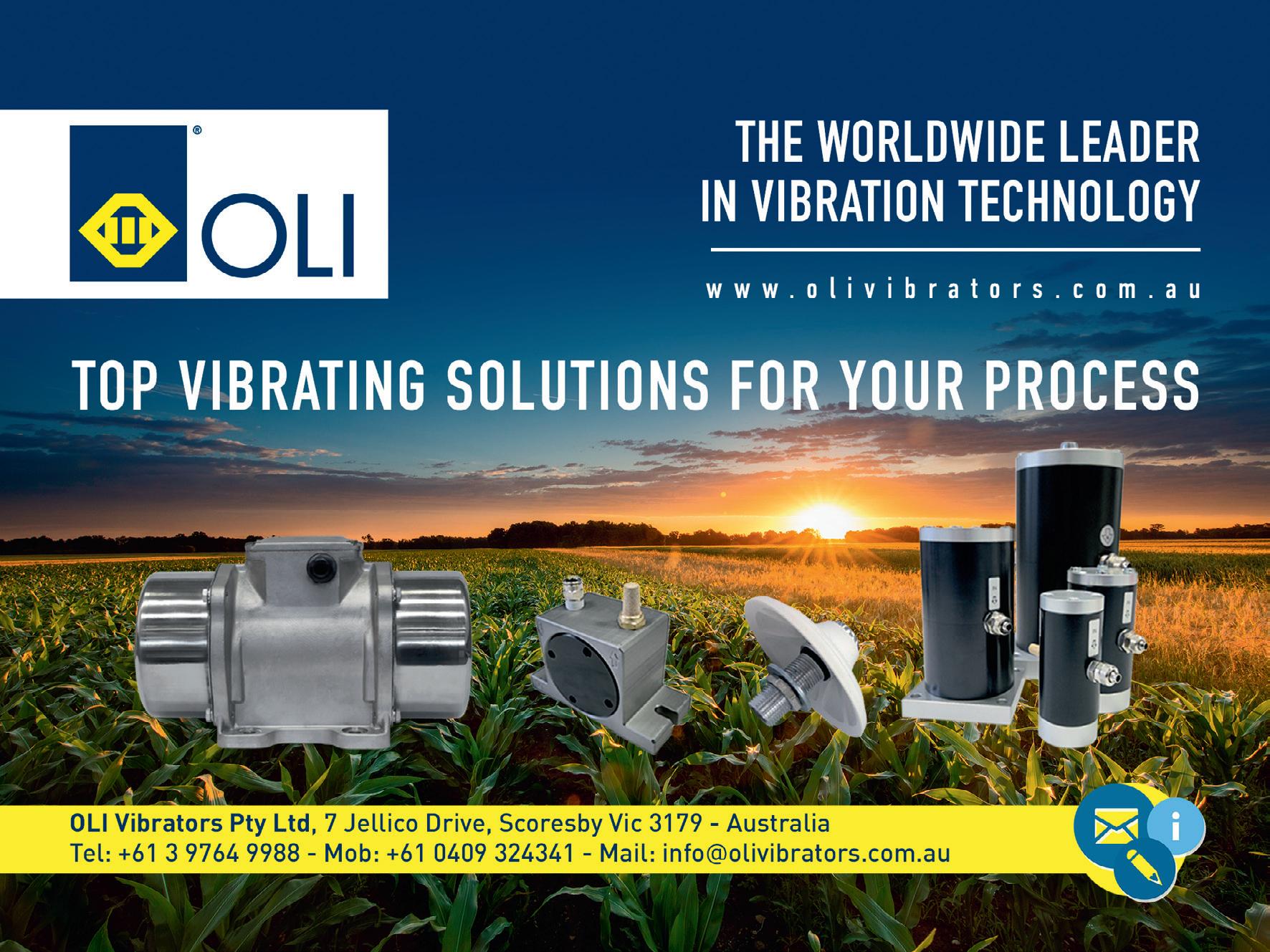