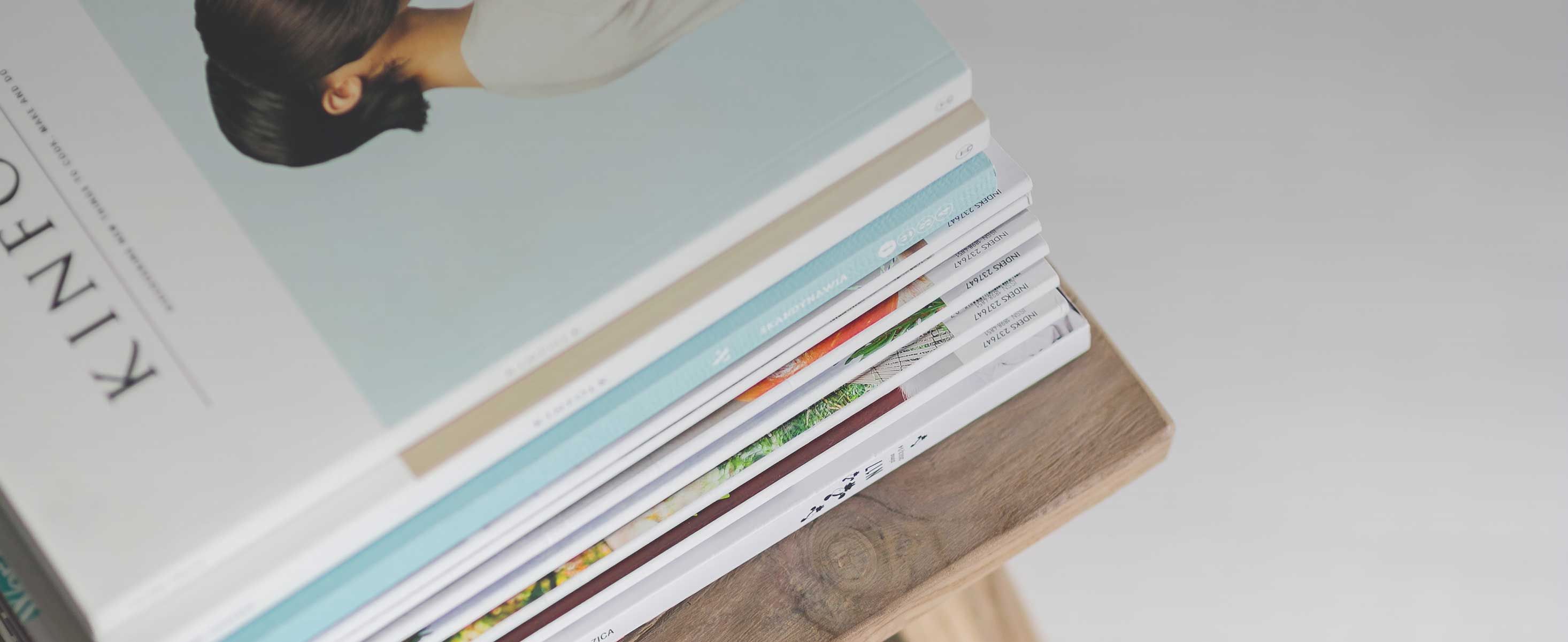
1 minute read
IO-LINK SENSORS: WHERE IT ALL WENT RIGHT
Ken Collishaw, Product Manager, Turck Australia
Sensors
IO-Link has enabled more comprehensive sensor communication, enabling sensor condition monitoring, while making set-up and maintenance easier.
In various and evolving forms, sensors have long been an integral component of industrial automation. They perform what initially appear to be very simple tasks, and for the most part they just let the control system know when something is present, absent, correct, incorrect or at a specific position or measuring point.
Of course, it isn’t really that simple. To address the huge variety of automation applications there also needs to be a huge variety of sensors, and choosing the correct sensor for an application is not always straightforward. There are different devices available to detect or measure different materials and there are sensors for speed, temperature, pressure, colour, vibration, humidity, angle, flow, vibration and much more.
There is also a dauntingly wide range of sensing principles in use including, but not limited to, inductive, photoelectric, capacitive, magnetic, ultrasonic, radar, guided microwave, magnetostrictive, mechanical, MEMS, gyroscope, infrared, vortex and calorimetric.
After the introduction of non-contact sensors (usually threewire devices) the basic operation of sensors stayed the same for a very long time. The sensor was powered up and, when specific set parameters were met (or not met), a signal was sent to the control system. Prior to Industry 4.0, and with a few rare exceptions such as a remote teach wire, the flow of information from sensors was all one way from the sensor to the control system and the information passed on was limited to basic digital or simple analog signals.
Industry 4.0 and more specifically IO-Link has now given us the ability to get much more from our sensors and also made using the sensors much easier. There are several ways in which this applies.
Connectivity
Using IO-Link sensors can save on connectivity costs. Most of us by now are familiar with the major benefits of remote I/O when compared to ‘traditional’ hard wiring. These include reduced physical wiring, the reliability of pre-made connectivity and the easy identification of faults. IO-Link technology adds a further level of cost savings when sensors with analog outputs are used. Shielded cables are no longer required and, when a full IO-Link system is used, there is no longer the need for any costly individual analog input cards. Connectivity from the IO-Link master to the control system is via fieldbus but the IO-Link sensor connections are point-to-point from each device to the IO-Link master using standard and reasonably priced industrial connectors, which are usually pre-moulded, double-ended M12 cordsets.