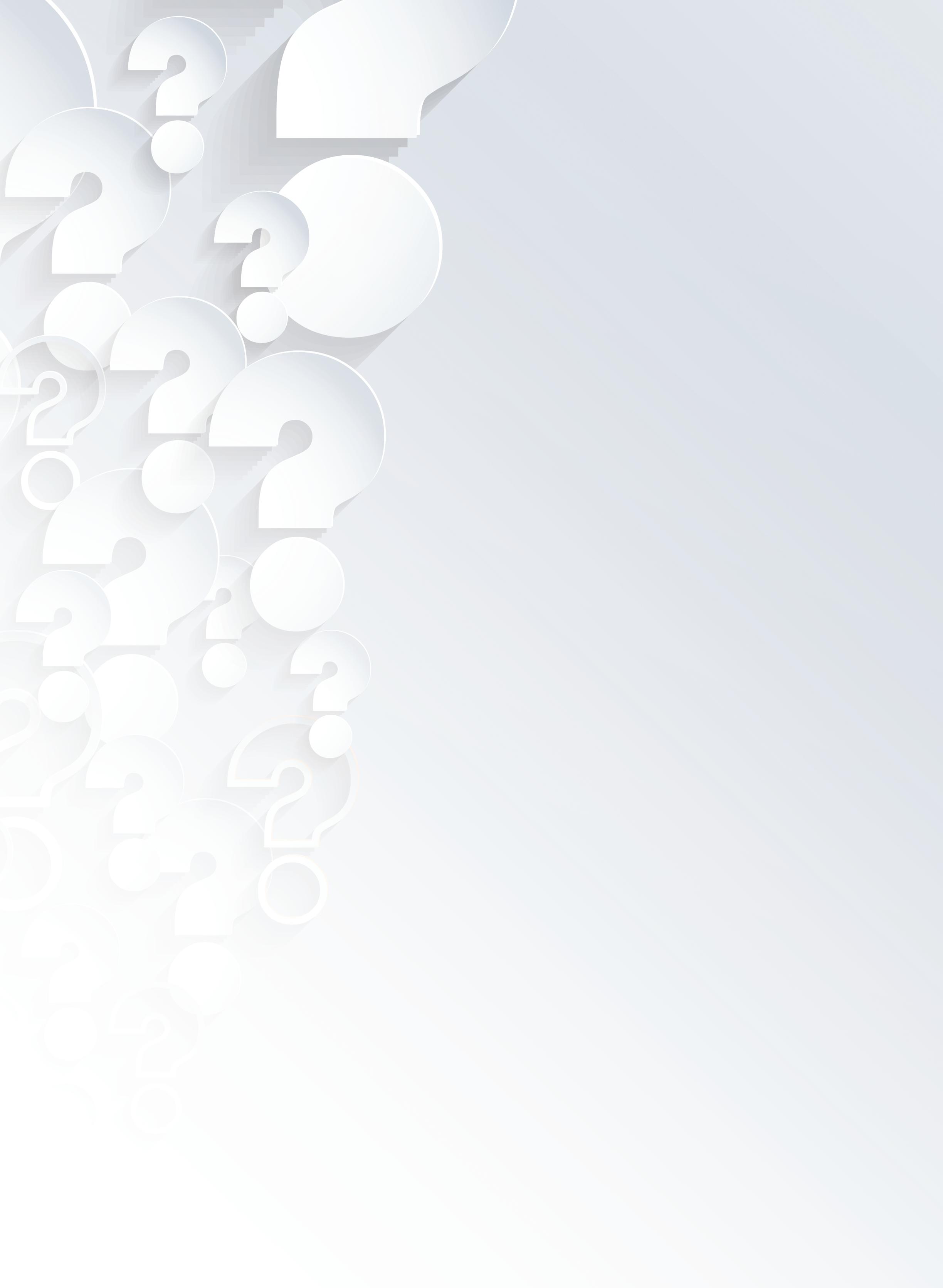
9 minute read
EXECUTIVE Q&A
KILIAN RENSCHLER, CEO OF KOENIG & BAUER US/CA
By Ralf Schlözer
Kilian Renschler has been named the tools quickly to keep our customers busy. new CEO and president of Koenig We were also happy to grow our market share. & Bauer US/CA at the start of 2021. One of the reasons was that we have a very strong Previously, he was executive vice presi- portfolio for packaging customers, not only our dent of sales of Koenig & Bauer US/CA. Rapida presses, but die cutters and folder-glu-
Kilian Renschler has been named the ers. We are seen as experts in this new CEO and president of Koenig & Bauer market and when times get diffi-
US/CA at the start of 2021. Previously, he cult customers go to the company was executive vice president of sales of where they feel they get the best
Koenig & Bauer US/CA. service and the best consulting. We
WhatTheyThink: Having a discussion in saw customers investing in devices early 2021, there is no way not to touch upon with higher productivity, customthe developments in 2020, the COVID pan- ers investing especially in large logisdemic and the impact it had on everybody. tics systems around their equipment,
How would you describe the impact it had on Koenig & Bauer, and how much of the impact Kilian Renschler, CEO since logistics is a big cost driver in folding carton. Customers, when do you still feel? upgrading presses, they were also looking into ways
Kilian Renschler: A big difference we saw was to increase the overall efficiency on the shop floor. the use of virtual tools. The importance of virtual We have seen more sales of sophisticated service and support tools was key in this time. It machines, long presses, more embellishment, also brought up the importance of the digitization double or triple coaters to offer new products and of Koenig & Bauer, that we already have tools in innovations for the market place for preventive maintenance, to monitor press WTT: I assume commercial press sales were down performance and consult customers based on that. considerably during the pandemic. Has that market
Communication was very important, how to recovered? train service technicians in a pandemic when travel KR: We have customers in the commercial market is not possible. Here the factory came up with inno- who are very successful, they have succeeded even vative ways to train technicians and continue to in difficult times depending on the market they serve the market. serve. Overall, it is fair to say that commercial print-
What we clearly saw is that the packaging ers have not grown in comparison to the packaging market remained very active. The changed con- market. However, we do see the commercial market sumer behaviors to buy more packaged food in rebounding once we get past COVID. grocery stores resulted in a high demand of food WTT: Last year you had the Koenig & Bauer Print packaging. Also, on the pharmaceutical side we saw Live event where you launched new machines. Maybe that customers were busy and we needed to guar- you can give a quick intro to these and whether they are antee uptime. We have a strong service team that available already? proved to be very flexible and adopted the new KR: Last year we had a virtual event, which was
well accepted by the market. A big innovation we introduced was the CutPRO X – our new rotary diecutter. It is available and is being installed right now in the U.S. We also introduced a new generation of flatbed die cutter at the event, the CutPRO Q. It will become available in the U.S. later in the year – in Europe we are now installing the first machines.
A big innovation for us was the new Rapida 106 generation, especially the Rapido 106X. Koenig & Bauer has done a fantastic job of enhancing this platform to achieve a new standard. We showed the 20,000 sheets/hour in perfecting mode on the Rapida 106 X.
The new generation consists of Rapida 105, the 106 and the 106X. We tailor the presses to each customer’s exact need. This is a ground-up new generation of press technology with faster throughput, a focus on short runs, less maintenance, simpler operation and more integration with pre and postpress.
As we speak, we have the new generation being installed in the U.S.
WTT: One thing I found remarkable is the Qualitronic Color Control. You can measure every sheet on the device and detect faults.
KR: We measure every sheet and adjust based on every 10th sheet. Our system measures after the coating unit, which is a bit different from others. We have systems that can measure from basic density to spectral analysis to grey balance.
We can use the same hardware to offer sheet inspection control. We can offer different levels of inspection quality control, from basic to highly sophisticated, depending on the application.
Between color control, inspection and registration this is a leading technology. The aim is to have the system autonomous and self-managing.
WTT: On large format offset – Heidelberger left the market citing not being profitable there. How did the market develop for Koenig & Bauer?
KR: We have invested into our large format Rapida machines and the market has been very strong for us. The pandemic showed that the demand for food-driven applications grew substantially, and in North America this is mainly produced on large format presses. We also see growth in the litho laminate or top sheet printing segment with our large format presses. Overall, our success is quite diverse and comes from small, independent companies to large integrators.
We clearly believe large format will be a longterm integral part of Koenig & Bauer’s and our customers’ future.
WTT: The focus is more Read More… towards packaging than book Find article at print or commercial? PrintingNews.
KR: I believe that large com/21149482 format is of interest to all market segments including book and commercial. We also have online printers running ultra-short runs on large format presses in Europe.
Koenig & Bauer sees the importance of having presses and technology for commercial, book and web-to-print printers and has developed new products for their exact needs. This includes special features for them as their workflow is different. At Koenig & Bauer every machine is custom built to their individual needs.
WTT: A market where Koenig & Bauer used to be very strong is webfed offset. This is probably different now. Where does that market stand for Koenig & Bauer?
KR: With the demand for newspapers declining the market size has reduced. However, we are happy to be installing one newspaper press in Florida right now, but this is definitely not a growth market. We also have ongoing retrofit and upgrade projects for both newspaper and commercial applications.
WTT: A growth market is certainly digital printing. There has been a number of installations in Europe, how about installations in the U.S.?
KR: We have digital print on various platforms. We have had the RotaJET for quite a while and we currently have one installation going on in the U.S.
We are very excited about the VariJET 106 sheetfed press for the folding carton market. We

Continued on page 62
Ralf Schlözer has over 20 years of experience in the Graphic Arts and Graphic System Manufacturing industries. He has extensive knowledge of traditional and direct imaging presses as well as non-impact printing technologies.
KOENIG & BAUER DURST ANNOUNCES BETA TESTING FOR VARIJET 106

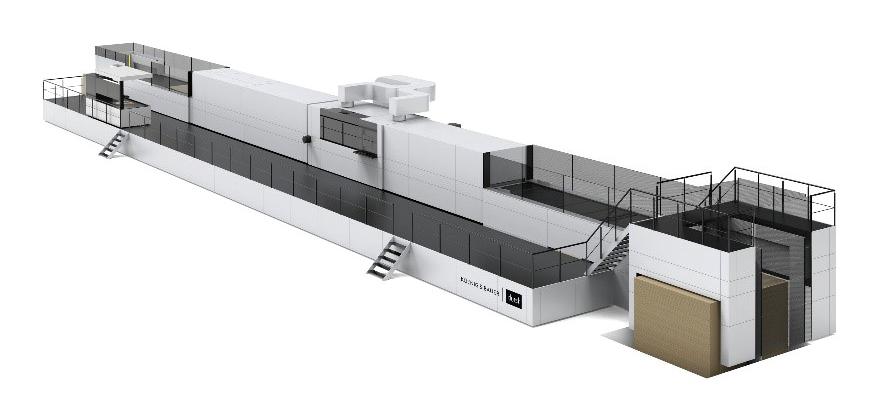
Koenig & Bauer Durst GmbH has announced plans to bring the VariJET 106 to market with the first installation of the single-pass digital printing press at a customer site early next year prior to a formal unveiling at the rearranged drupa in Dusseldorf, Germany, from April 20-30.
Targeting the folding carton industry, the much-anticipated B1 6,000sph VariJET 106 is at the heart of the collaborative development between Koenig & Bauer and Durst. It integrates inkjet technology into the platform of the high-performance Rapida 106 offset press.
The VariJET 106 combines the strengths of digital inkjet with those of classic offset printing and inline finishing. It is this unique flexibility which defines the VariJET 106 as a productive and cost-efficient hybrid printing system for digital packaging printing. The VariJET 106 can produce personalised and individualized print products or alternate between short and medium runs.
The VariJET 106 offers: modular integration of upstream and downstream processes; combination of digital print with proven modules of the Rapida platform; perfect register accuracy thanks to inline production; highly competitive TCO; efficient production of ultra-short to medium runs; reduced resource consumption, storage costs and waste; absolute flexibility for test packaging and new campaigns; fastest possible response to market demands.
The announcements from the joint venture company, which was set up by Durst and Koenig & Bauer in 2019, have also included updates on its single-pass corrugated presses – the Delta SPC 130 and the CorruJET 170 – which have a specific focus on delivering for the stringent requirements of the packaging sector.
A digital priming unit for uncoated media will broaden the applications customers can address on the Delta SPC 130, as well as extend the range of media that can be used for printing. And special colours being introduced for the fifth and sixth colour stations will enable converters to meet brand colour requirements.
The Delta SPC 130 FlexLine Automatic combines a well-engineered mechanical design with easily accessible sub-assemblies and selected components to guarantee durable quality, high performance and reliability. It can manage small formats from 500 x 600mm through to very large formats with maximum dimensions of 1,300 x 2,100 (optionally 1,300 x 2,800 mm) and print a maximum thickness of 12 mm with water-based, food safe inks. The Delta SPC130 FlexLine machine includes feeder, six-colour single-pass printing, cooling section and stacker.
For the CorruJET 170, successful beta testing has been completed at the Kolb Group in Bavaria, Germany, a company that develops and produces packaging, packaging materials and specialist products made in corrugated cardboard. Based on Koenig & Bauer’s RotaJET inkjet web press for commercial printing, The CorruJET 170 postprints sheets of corrugated up to 1.7m wide at up to 137m/min on water based, food safe inks.
All three presses meet the stringent requirements for food safe primary packaging utilizing proprietary water-based ink technology. The VariJET 106, Delta SPC 130 and CorruJET 170 are designed with core technologies to provide automated, productive, food safe printing systems. They deliver shorter response times, more variants, shorter run lengths, individualization and enable more small value orders.
Robert Stabler, Managing Director, Koenig & Bauer Durst, said: “We’re really excited by the opportunities and progress with our much-anticipated VariJET 106. Successful companies need to be able to embrace the trends that are occurring and offer solutions. We deliver on this.”
VariJET 106
(Left) Robert Stabler, Managing Director, Durst and Koenig & Bauer
SPC_130 CorruJET
