
5 minute read
BLOWIN’ IN THE WIND Banner Finishing Is About More than Aesthetics By Richard Romano
BLOWIN’IN THE WIND
Banner finishing is about more than aesthetics.
By Richard Romano
While “walking” the “show floor” at the ISA Sign Expo Virtual “last week,” (OK, I’ll stop with the quotation marks.) I came across a “booth” (sorry) for Banner Ups/Budnick Converting, which featured a video of a vinyl banner placed in a wind tunnel and exposed to 100-mile-perhour winds (watch it here: https://youtu.be/ L55Jy82edcA). Videorecorded at the National Institute of Aeronautical Research, it was at the time (2017)—and may still be—the strongest banner wind survival ever documented, making it up to 108.2 mph before failure.
The video was demonstrating the strength of Banner Ups’ MegaTape and BravoTabs, but it vividly illustrates an important consideration when producing banners, or any kind of display graphics intended for outdoor installation.
While it’s true that, generally speaking, you probably won’t have to worry about 108-mph winds (although with hurricane season approaching, if you’re based in or near Florida, you may), it’s still important to pay attention not only to the aesthetics but also the strength of finishing and installation techniques.
Sticky Wickets
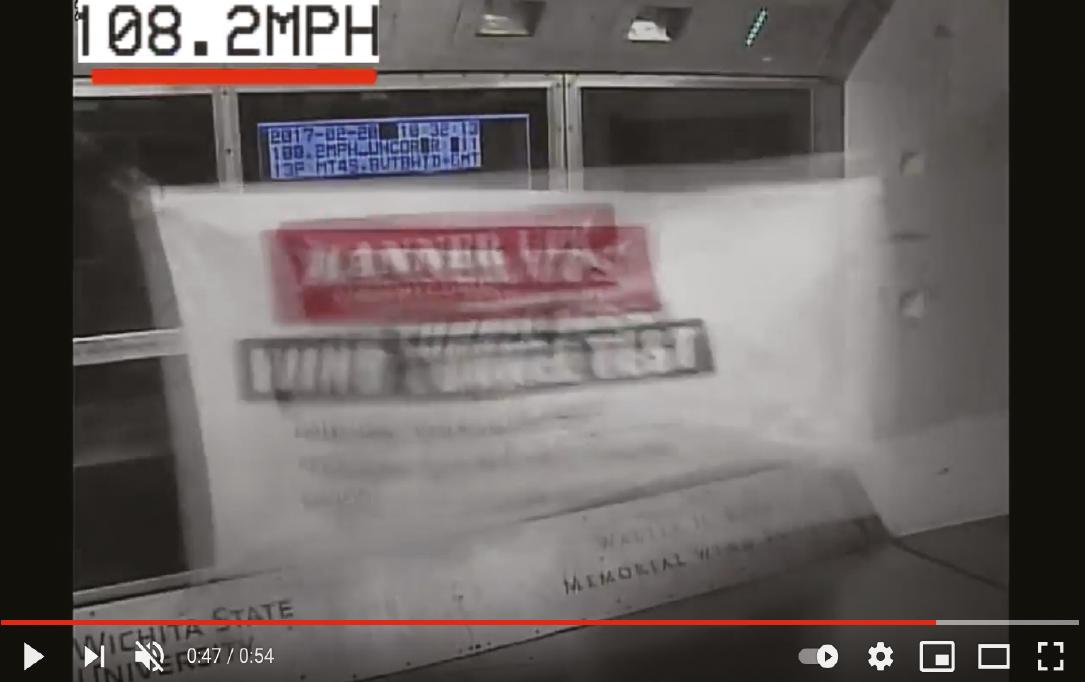
While not as sexy as finishing tools such as cutting tables, laser cutters and engravers, etc., one of the most vital tools in your banner finishing arsenal is something as simple as tape. Doublesided adhesive tape is one simple and inexpensive way to finish banners, be it for hemming, forming pole pockets, seaming graphics for tiling purposes, and/or for physically hanging signs or banners. Now, this kind of tape is not the everyday kind you would pick up at Staples, but is instead known as “heavyduty banner tape,” and is stronger and more durable than the consumer or all-purpose variety. Still, banner tape may not be able to withstand heavy winds—or even winds substantially less intense than those in the Banner Ups wind tunnel test.
No Wallace or Grommet
I mentioned above in the wind-tunnel discussion, BravoTabs, which are Banner Ups’ square-shaped, high-strength variety of grommet tabs, which are, in turn, an alternative to grommets. These are plastic adhesive tabs that are applied over the corner of a banner and reinforce hanging holes. Banner Ups’ PowerTabs They are much like metal or plastic grommets, but they have some advantages over grommets, first among them being aesthetics. Grommet tabs can be transparent, and thus can be a bit less conspicuous than metal or plastic grommets. They can also be stronger than grommets. When the wind billows the banner out like a sail, the rope or other hanging
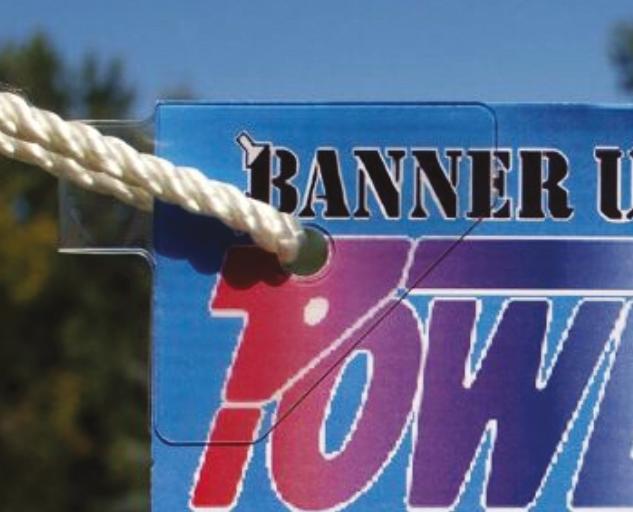
mechanism pull s through the corner of the banner, and the tabs distribute the pulling force over a greater surface area. So it is less likely to tear than with grommets. (Here is a video that demonstrates this: https://youtu.be/mgKVsvZXx9Q.)
Hemming and Hawing

That’s all well and good for vinyl banners, but soft signage—textile-based banners and other display graphics—is a common and growing alternative to vinyl. Soft signage usually requires a finishing step you don’t always need with vinyl: hemming. Hemming a fabric banner is just like hemming trouser cuffs and is done for the same reason: to prevent the fabric from fraying and unraveling. However, hemming is also done to add structural support to the banner if, again, it is designed to be installed outdoors and exposed to wind. If you’re as into watching wind tunnel banner and sign tests as I appear to have become, a clip from Windigo Signs showing a fabric sign in a wind tunnel can be seen here: https://youtu.be/Nte5xTM1Eew. (Windigo Signs manufactures light-pole signs that feature a proprietary wind-release technology.) Hemming is also done to add pole pockets or to support whatever installation hardware will be required—including grommets.
Hemming soft signage can be accomplished in three basic ways: ● Taping, using the same banner tape you would use for vinyl signage, although it doesn’t work as well on fabric. ● Sewing, which is a better and more durable option. This will require an industrial strength sewing machine and perhaps skilled sewists. (Our textiles guru Cary Sherburne tells me that “sewist” has become the preferred term, thankfully replacing the older “sewer.” “Seamstress” is also commonly used, although you rarely encounter the term “seamster” for a male counterpart, which makes some gender assumptions.) By way, vinyl banners can be sewn as well. ● Welding, as the term suggests, hems a fabric using heat. Most of the fabrics used in sign and display applications are some kind of polyester or, essentially, a plastic. As a result, when they are exposed to heat, they melt, so instead of sewing a hem, you apply heat and pressure and fuse the fabric to itself. As with dye-sublimation printing, welding is a function of the combination of temperature, pressure and speed.
There are several different kinds of welding technologies, depending on the specific application, but you get the idea. (See this older Printing News article for a slightly deeper dive: https://bit.ly/3wSs39q.)
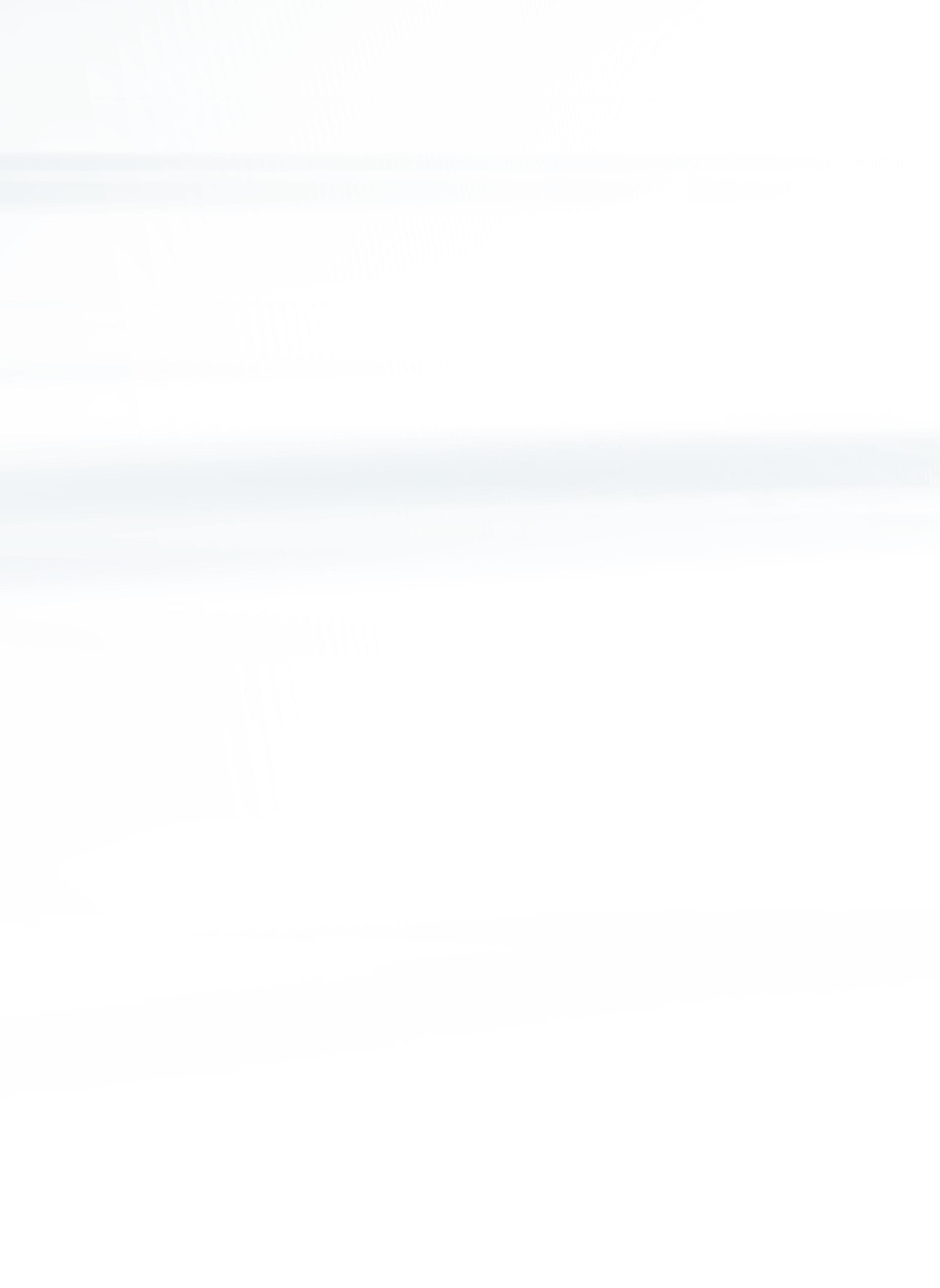
Miller Weldmaster 112 Extreme hot air welder for fabric applications.
Don’t Get Blown Away
There are few places that don’t experience high wind (or even extremely high wind) conditions, but even moderate winds can be destructive to outdoor graphics if they have been insufficiently reinforced. These may not be the sexiest Read More… Find article at finishing techniques in the PrintingNews. world. We are probably not com/21151365 going to feature banner tape on our cover any time soon. But they are important considerations when producing outdoor graphics that are designed look good as well as last. ●
Richard Romano has been writing about the graphic communications industry for 20 years. He is an industry analyst and author or coauthor of more than half a dozen books.