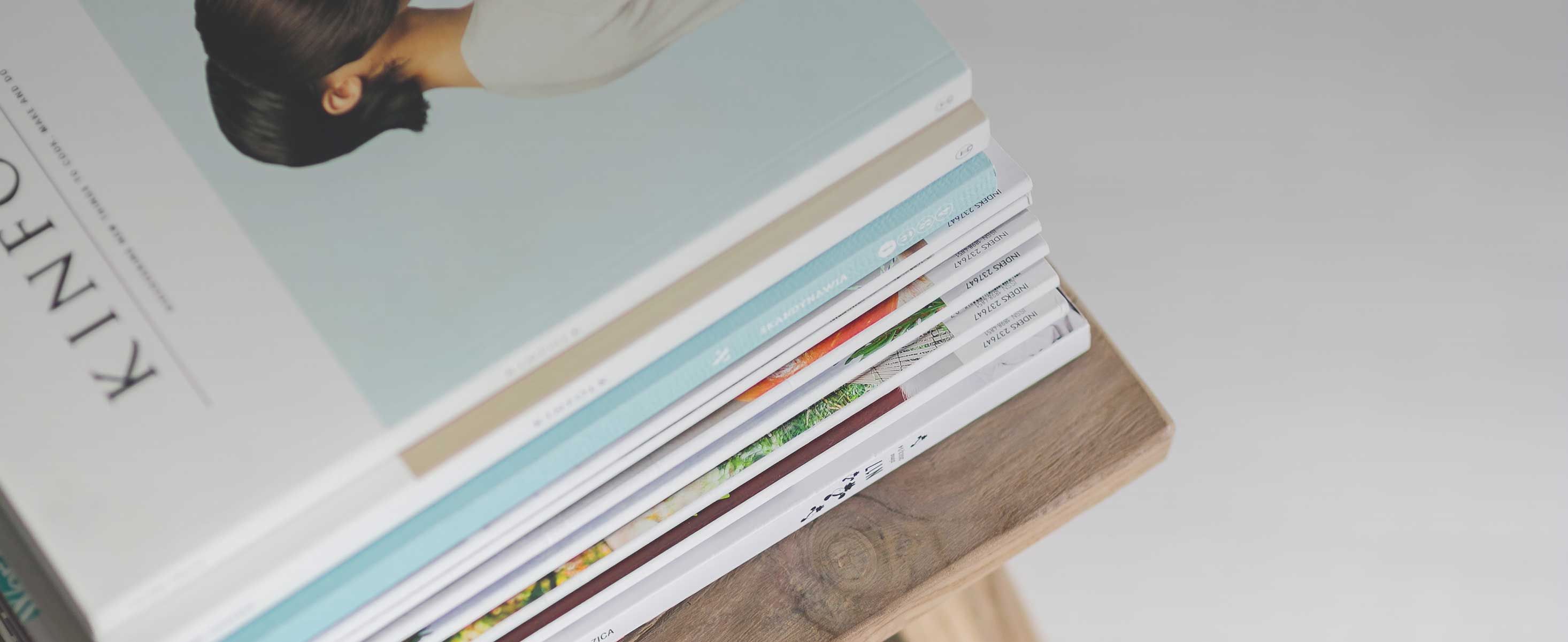
2 minute read
step 3 Optimize Job Onboarding Through Printing
The most efficient job onboarding is when the customer can enter the job specifications, validate them, receive pricing and approve the order on their own. Online ordering through a W2P solution is an excellent example of how customers can self-service standard products, but it is not the only way to streamline ordering.
Larger companies may integrate their entire purchasing software suite to send orders directly to your print MIS through an electronic data interchange (EDI) or application programming interface (API) integration.
Regardless of how it is done, the goal is to onboard standard, and thinking of time and cost savings on an annual basis provides a clear path to the actions required to improve the workflow. repeatable print products with zero touches from the initial request through ticketing. Once the ticket is created, let your print MIS do the heavy lifting.
If put into practice for how the customer submits order specifications to your digital printing workflow, your answers could look like this.
What is needed?
Why is this needed?
When or in what order is it needed?
How is it captured?
Where is the information put?
Who provides the information?
How much in time and labor costs?
If you produced 10 of the jobs in the example per day (2,600 per year), the $150 in labor savings per job to implement online ordering could save $390,000 annually. Those time savings would also allow your sales team more time to focus on selling higher-value solutions, your CSR more time to engage customers, and your estimator more time to focus on estimating higher-value work.
Based on past assessments, it is common to find several hidden yet costly touch points throughout the workflow.
Over time, employees can create processes using generic tools like spreadsheets to help them accomplish their tasks, instead of fully using the workflow tools available.
Identify hidden processes and spreadsheets and fix them in steps two and three when building your workflow stack and optimizing job onboarding.
Purchase orders should be automatically generated if materials are below set inventory thresholds or if more is required for the work-in-progress jobs. Let the system figure out the optimal schedule for production with rules set to minimize changeover in printing and finishing.
Digital orders are commonly printed and finished quickly enough that a first-in, first-out approach can also work in many
Many PSPs already have the building blocks for an optimized and automated workflow, or may only be missing a couple of pieces. It requires a focused effort to improve existing solutions configurations, integrations and use. The key is not what software solutions you own but their level of utilization and integration to support maximum automation.
Now that you have identified and optimized the processes needed for your most common print applications, it is time to determine those that can be automated within reason. Not every process can or should be automated. The goal, especially for the fast turnaround and high number of digital jobs, is to have zero manual touchpoints from the customer request to landing in the queue at the DFE. cases. However, some companies use batching software as part of their tech stack to group similar jobs over a defined period. No matter how you manage jobs after the tickets are created, it should not require the operator’s time unless it is unique or complex.
Taking a product-driven approach to standard work also improves the preparation of the artwork and data content. Repeatable workflow plans can be used based on whether the job calls for direct mail, brochures or business cards. The automated plans should convert files to the format needed for the workflow, preflight, adjust color sets, apply color management, optimize files, impose and output to the DFE.
Again, the goal is zero touch for operators who can then focus on the exceptions that need special processing and work that is not a standard product offering.
At this point, the printer and finishing operators should simply manage their work queues and the needs of the devices to produce the work. Another key element is to capture the times, material counts and key data from the shop floor so it can be monitored, analyzed and used to continuously improve production.