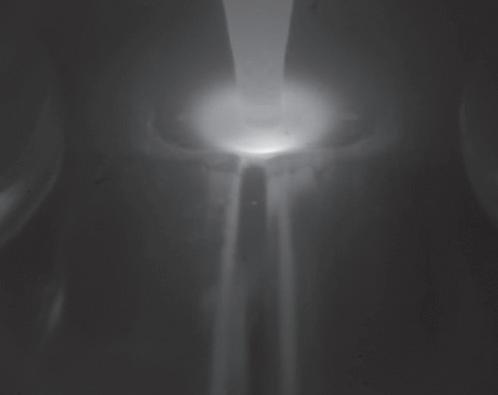
1 minute read
Xiris unveils SeamMonitor™ system for precise TIG tube welding
from PIM Metals April/May 2023
by ASTAC
Xiris Automation introduces the new SeamMonitor™, a real-time measurement tool that monitors torch tip to weld seam alignment and weld seam size on TIG welded tube mills. With this, fabricators can achieve highquality welds and minimize production losses. Written by Cameron
Xiris Automation, a leading provider of innovative camerabased solutions for quality control in the metal fabrication industry, has announced the launch of SeamMonitor™, a camera-based measurement tool that provides real-time monitoring of the the torch tip-to-weld seam alignment and weld seam size on Tungsten Inert Gas (TIG) welded tube mills.
Advertisement
Metal tube fabricators who use TIG welding know that precise alignment of the welding torch to the welding seam is critical to achieving high-quality welds with clean edges and minimal weld bead. Occasionally, the seam to torch tip alignment can move over time due to various tensions in the tube, causing it to twist as it is pulled through the weld head. As a result, the weld seam can rotate in and out of position with respect to the welding torch, which may result in defects and production losses.
To solve this problem, Xiris has enhanced its SeamMonitor™ system, which provides a robust solution to monitor ttip-to-weld seam alignment on TIG Tube mills. The SeamMonitor™ combines a High Dynamic Range (HDR) weld camera that can clearly capture the torch, weld arc, and surrounding environment with powerful machine vision measurement software that enables real-time monitoring of the weld seam size, torch tip location, and relative offset between the torch tip and its seam.
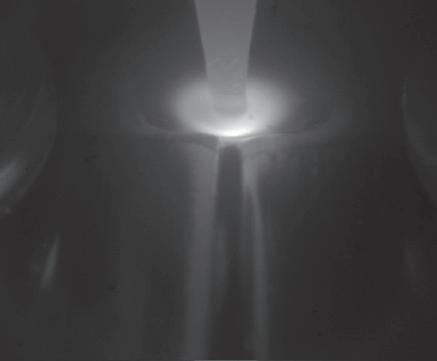
The SeamMonitor™ provides a system solution for use on TIG Tube mills providing warning and error alerts on key
Serles
measurements to operators or external equipment for process control. The system includes data analysis tools and onscreen graphing of key measurements that can be sent to external equipment using OPC, analog or digital interfaces.