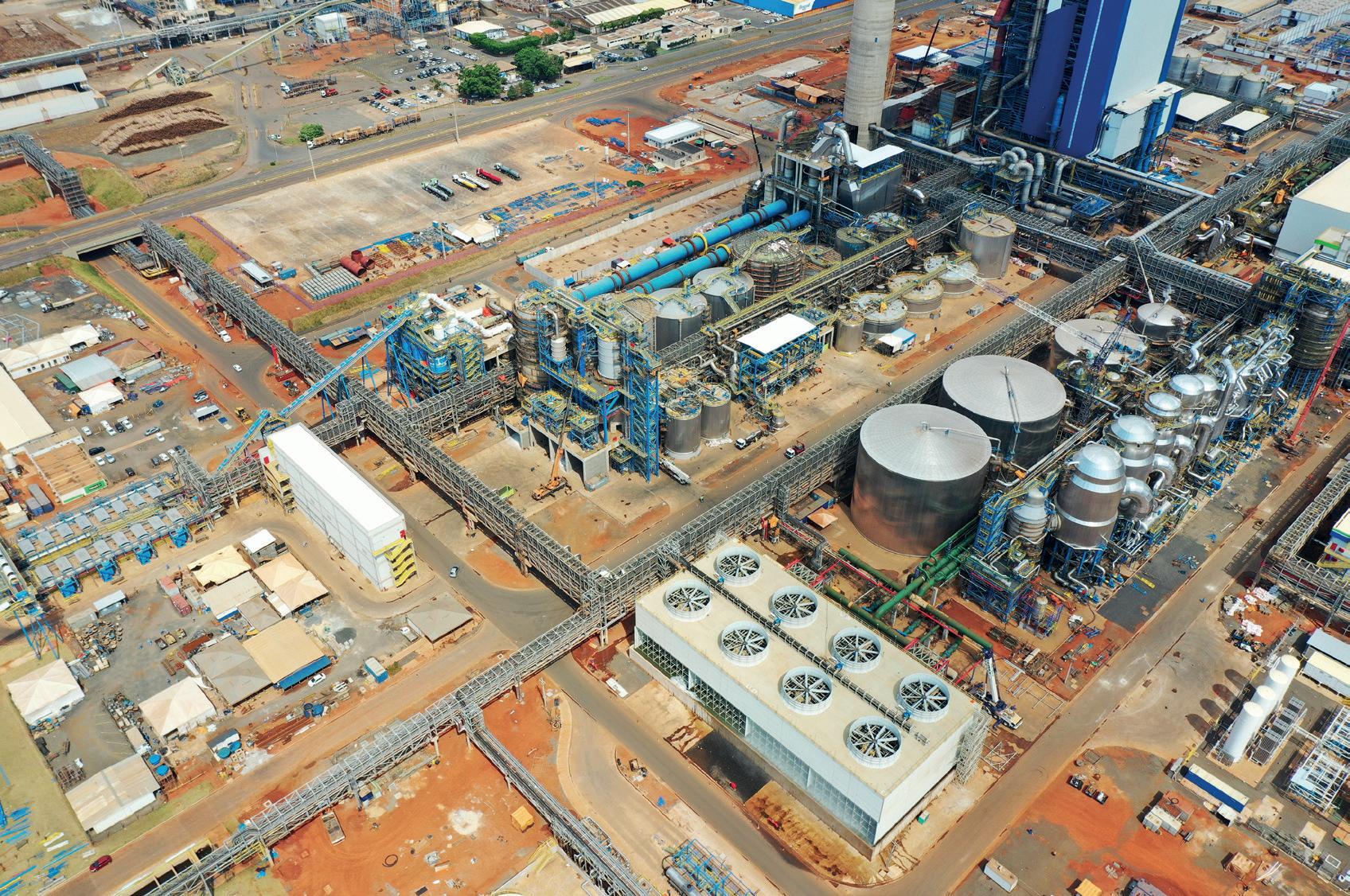
3 minute read
The future of the bioindustry
Bracell’s new mill at Lençóis Paulista in Brazil brings together the most modern and innovative technologies to achieve the highest levels of sustainability in the pulp production process.
This project considerably diversifies and expands Bracell’s
Advertisement
Project Star is one of the largest private investments in Brazil in the last 20 years, and it has made Bracell the largest producer of dissolving pulp in the world. The mill runs without any fossil fuels and can produce up to three million tonnes of kraft pulp per year, report Ana Luiza Branco and Livia Bianco. Photography byThiago Filla production of kraft pulp, increasing it from 250,000 tonnes per year to 1.5 million tonnes per year of dissolving pulp, or up to three million tonnes per year of kraft pulp.
The mill has two flexible lines designed primarily to produce dissolving pulp using the latest production technologies, without the use of fossil fuels. The plant will be self-sufficient in energy production, and the surplus will be used to supply the National Interconnected
System with clean, high-quality electricity.
An industry milestone for sustainability and state-of-the-art technology
After two years of extensive work, the mill started-up in
September 2021. Valmet was one of the project’s main partners and delivered the evaporation plant, which has a capacity of 3,500 tonnes of evaporated water per hour; the recausticising plant, which has a capacity of 31,000 cubic metres of white liquor per day; two lime kilns, which use biogas as fuel with a production capacity of 1,200 tonnes per day; two biomass dryers; and two biomass gasification plants each with a capacity of 87 thermal megawatts.
The project features state-ofthe-art technical, energy and environmental performance equipment. For black liquor evaporation, Valmet provided its Tubel technology in the concentrators and first evaporation effect. This technology is the most robust and reliable on the market, with liquor flow on the outside of the tubes to prevent clogging and maintain the plant’s very high availability. One hundred per cent of the lime kilns’ energy requirements is supplied by gas from the gasification of biomass, significantly reducing production costs and carbon dioxide emissions. This is the first biomass gasification lime kiln technology supplied to a South American pulp mill.
Fernando Scucuglia, pulp and energy director at Valmet South America explains: “Valmet has combined its technical knowledge obtained from investments in R&D and the experience gained in similar projects implemented around the world for Bracell’s new mill. The lime kilns are operated completely with fuel obtained from biomass gasification. This is the first pulp mill in South America that will not use fossil fuels in this process. Our mission is to convert renewable resources into sustainable results, so I’m very happy to have delivered this key technology for Bracell.”
Another sustainable technology
Project delivered by Valmet is the non-condensable gas (NCG) treatment system, which controls and minimises odours from the chemical pulping processes.
One of the largest and most sustainable pulp mills in the world
One of the global leaders in the production of speciality pulp, Bracell has always based its operations on sustainable eucalyptus cultivation and stateof-the-art plants. The company has created around 10,000 jobs in the two states where it operates, including direct and permanent outsourced workers in industrial, forestry and logistics activities. Continuously investing in technology and research to offer high quality products, Project Star is a pioneer in consolidating the company’s sustainable performance.
Alexandre Figueiredo, senior industrial manager at Bracell in São Paulo, says that the new mill is one of the largest and most sustainable pulp mills in the world.
“The project stands out for its sustainable performance, with advanced technology that eliminates the use of fossil fuels and uses renewable raw materials to create biodegradable products. This project has been a significant milestone in Bracell’s history. It’s much more than a pulp mill – it’s the future of the bioindustry, the most modern and sustainable mill in the sector,” he says.
Stop collecting paper samples! SmartScan™ measures paper dryness 24/7, safely .
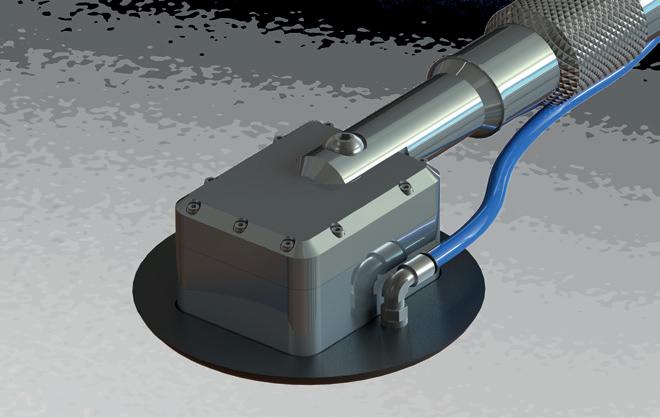
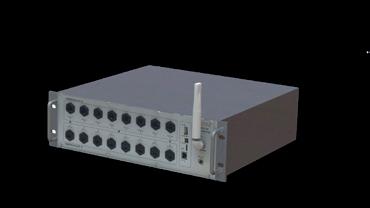
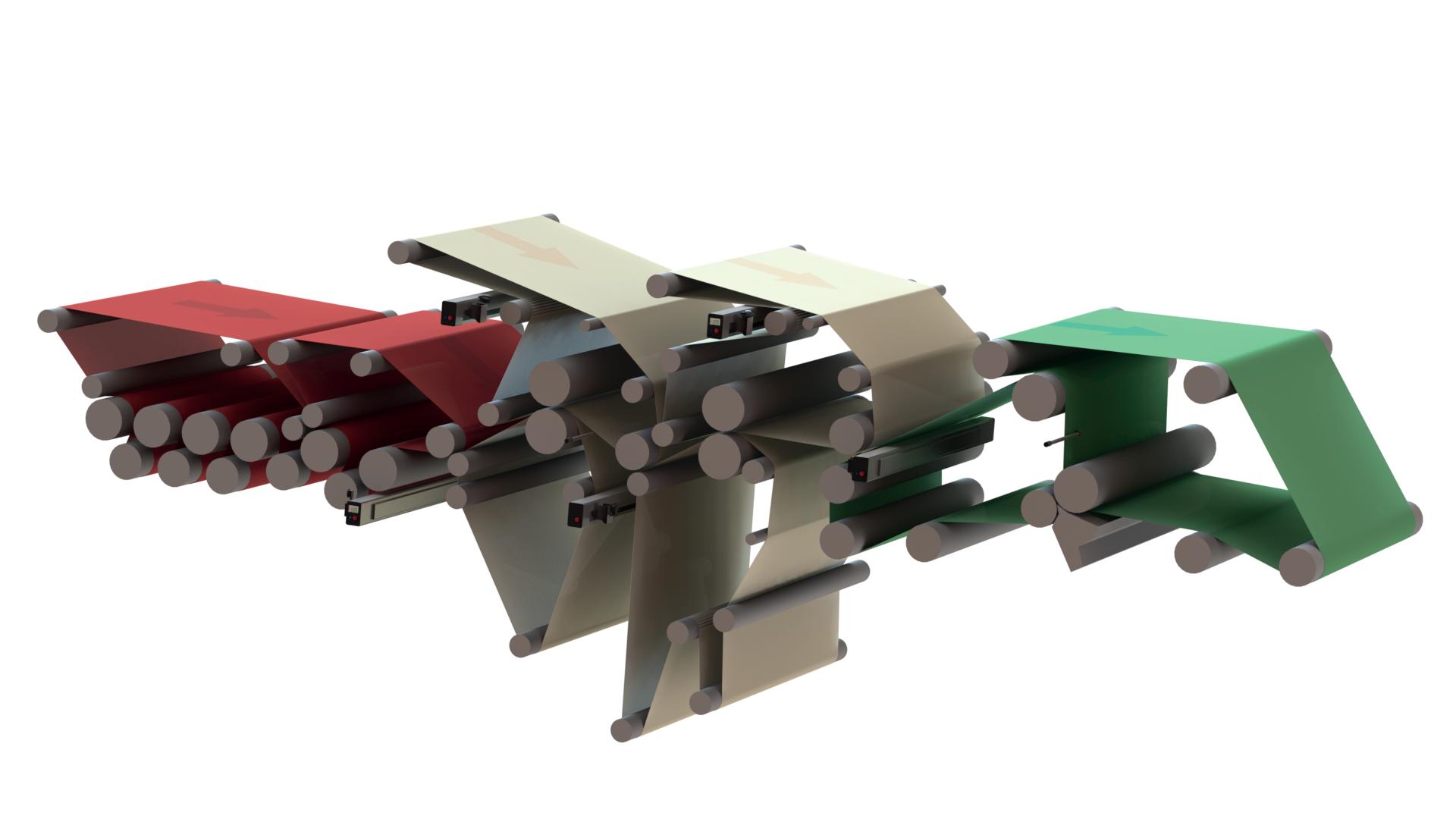
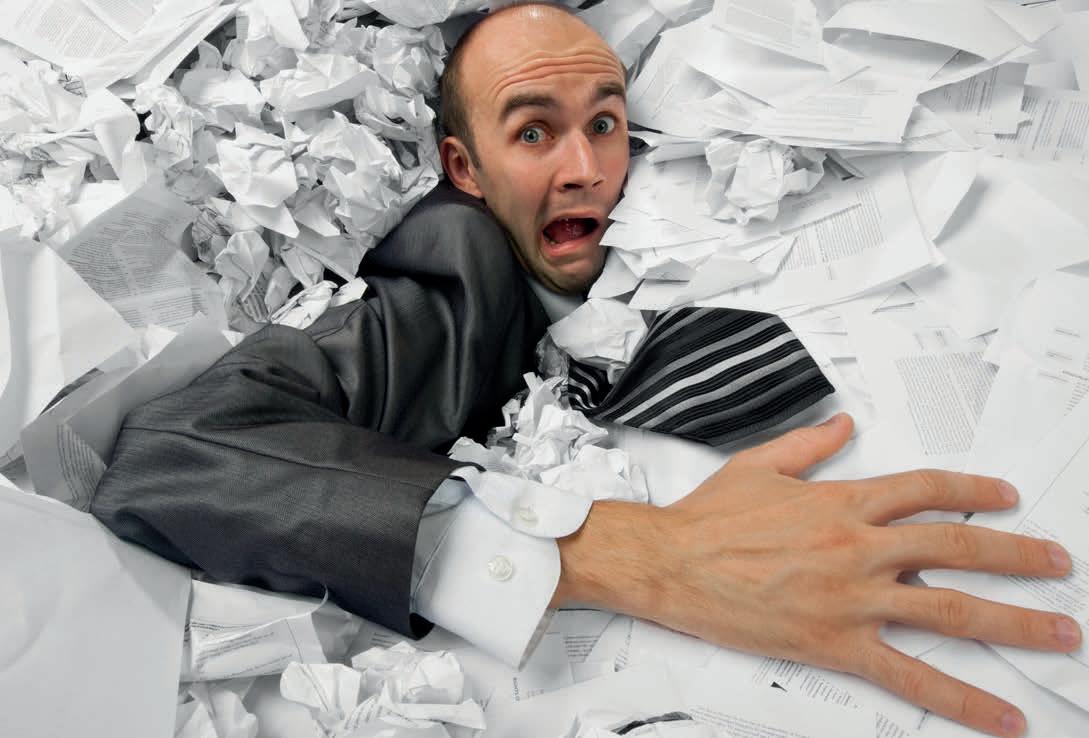
Improve your press section efficiency! SmartScan™ contactless sensor accurately measures paper web dryness after the press section 24 hours a day, 7 days a week. Using a proprietary microwave technology, it is developed to overcome the typical limits of the NIR (near-infrared) sensors. SmartScan™ is available both for fixed point positions or traversing web scan. To save hundred of thousands of Euros in energy costs, stop collecting samples, choose the safe accuracy of SmartScan™ technology.
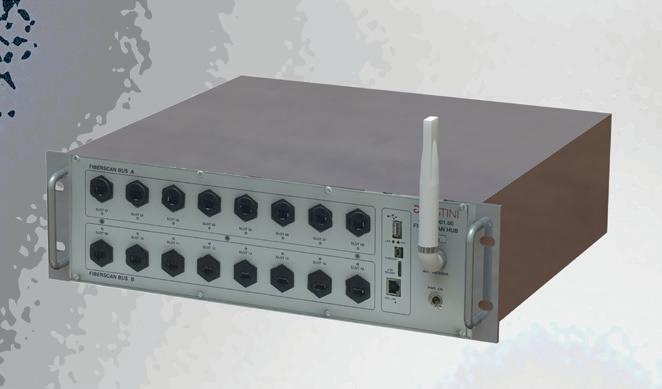