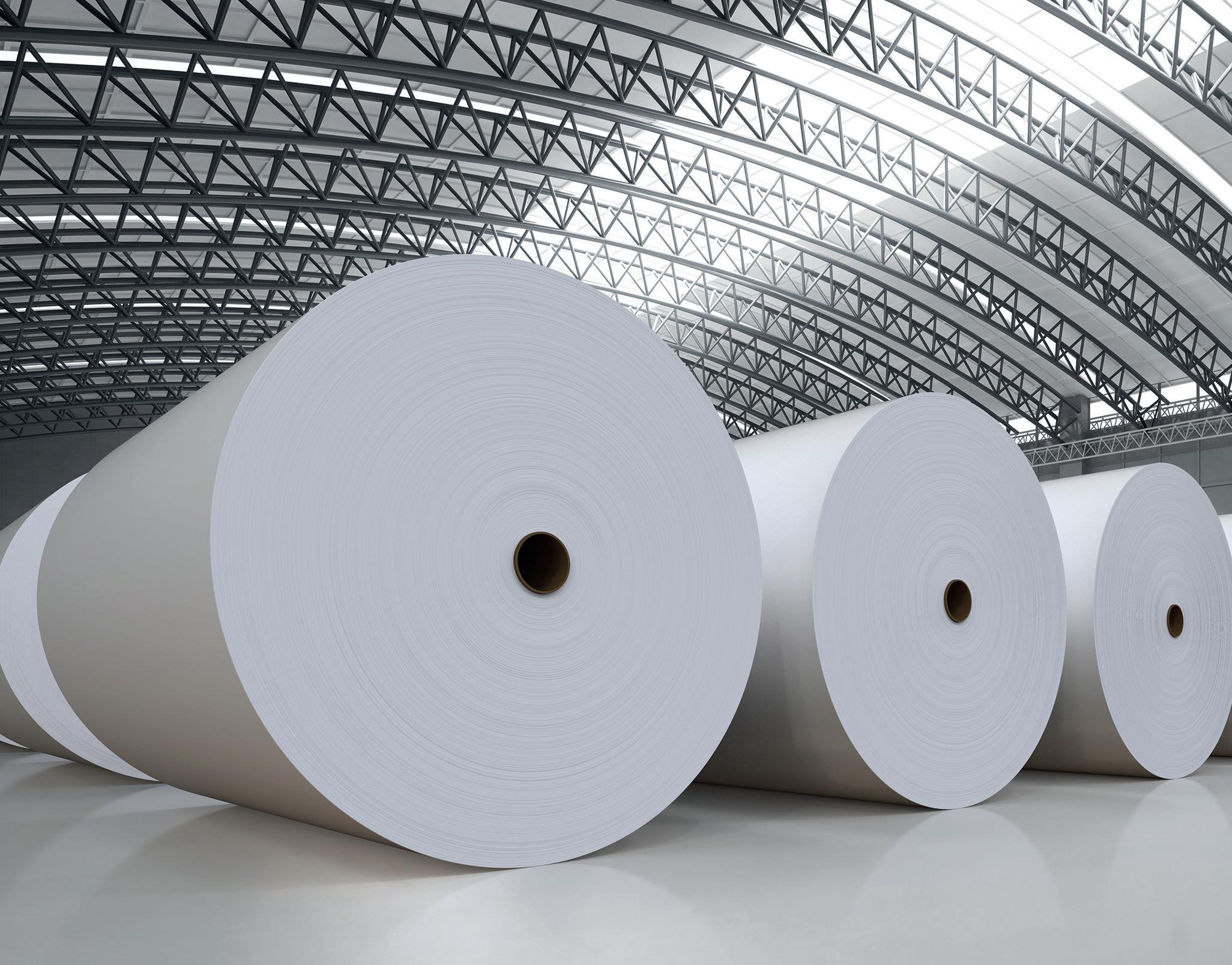
5 minute read
Insight from connected motors boosts mill efficiency Insight from motors boosts mill efficiency
Asurvey by ABB in March 2023 found that 92 percent of business leaders around the world see rising energy costs as a threat to competitiveness. High energy prices over the past year have put pressure on businesses to make hard decisions on how to allocate budgets. Many leaders have accepted lower profitability, while others are cutting back on people, marketing and infrastructure.
The energy crisis could also delay the achievement of Net Zero targets. Of the respondents that reported, 58 percent said
Advertisement
Erich Labuda, president of ABB Motion Services, explores how two pulp and paper operators in Sweden are using motor data to improve energy efficiency, cut consumption and reduce carbon dioxide emissions
that the energy crisis will delay their decarbonisation plans by up to five years. In addition, 61 percent stated that reducing energy costs is a top priority, while only 40 percent said the same for decarbonisation.
As a technique with potential to cut both operational costs and carbon dioxide (CO2) emissions, energy efficiency has huge potential. This is particularly true for the efficiency of motor-driven systems.
More than 45 percent of all electricity produced today is consumed by industrial electric motors – and that is set to double by 2040. This transition will place greater demand on electricity resources, which is likely to keep prices high.
In this environment, energy efficiency is perhaps the best opportunity available for industrial businesses like pulp and paper mills that want to reduce their CO2 emissions in line with Net
Zero targets while also cutting operational expenditure (OPEX) by reducing energy demand.
By improving the efficiency of a mill’s electric motors and variable speed drives, an operator’s investment in energy efficiency can pay for itself – an effect that becomes stronger when energy prices are high.
However, the challenge is knowing where to target this investment. A typical pulp and paper mill might have a fleet of hundreds of motors, each of which has a unique set of operating parameters and loading patterns.
Digital energy efficiency audits
Traditionally, operators have used energy audits to find these opportunities. During a traditional audit, an expert will visit to gather data manually before analysing it and providing recommendations that show the return on investment of taking actions. These tend to be used to gain deep insight into the largest motors on the critical line.
New developments in technology are now overcoming this barrier. Today, it’s possible for a mill’s own operators to deploy digital data-gathering through connected motors and variable speed drives (VSDs). A service expert can review this data remotely without necessarily having to travel to site. With this digital approach, it’s possible to extend a digital energy efficiency appraisal to cover many more motors, potentially even entire fleets. It has a secondary benefit of reducing CO2 emissions related to travel.
Analysis of the data from an energy efficiency perspective can show which motors are operating far from their peak efficiency and – crucially – how much energy is wasted. The expert can then identify potential actions to resolve this, and the costs of these. For example, they might suggest adjusting operational parameters so that the motor only operates when it can do so efficiently. Alternatively, they could recommend adding a VSD to a fixed speed motor. A further option is to modernise an entire electric drivetrain, made up of a motor and VSD, to premium efficiency technology and sending the time-served system to be recycled.
Similar data from connected motors can also be analysed to provide insight into motor condition, performance and health. Plant managers can use this as the basis of a conditionbased maintenance strategy that minimises unplanned downtime by identifying and resolving issues before they happen.
Two pulp and paper mills in Sweden are at the forefront of the digital approach and are using digital energy audits to reduce energy consumption and cut emissions.

Data-driven approach
enables SCA Group to target 50 GWh annual savings SCA Group’s kraft paper mill at Munksund in north east Sweden produces 400,000 tonnes of packaging per year and has a strong focus on sustainability. It uses bioenergy to generate most of its electricity and this has enabled it to become 95 percent fossil-fuel-free. However, its managers saw an opportunity to save more energy by targeting the 2,400 electric motors that drive its processes.
Anders Kyösti, the site’s technical manager, said: “Our objective is to improve energy efficiency through enhancements of at least 50 GWh per year based on the company’s energy consumption in 2020. Electrical motors account for a large part of our electricity consumption. Given higher energy prices and the trend towards electrification, optimising energy use will become even more important in the future.”
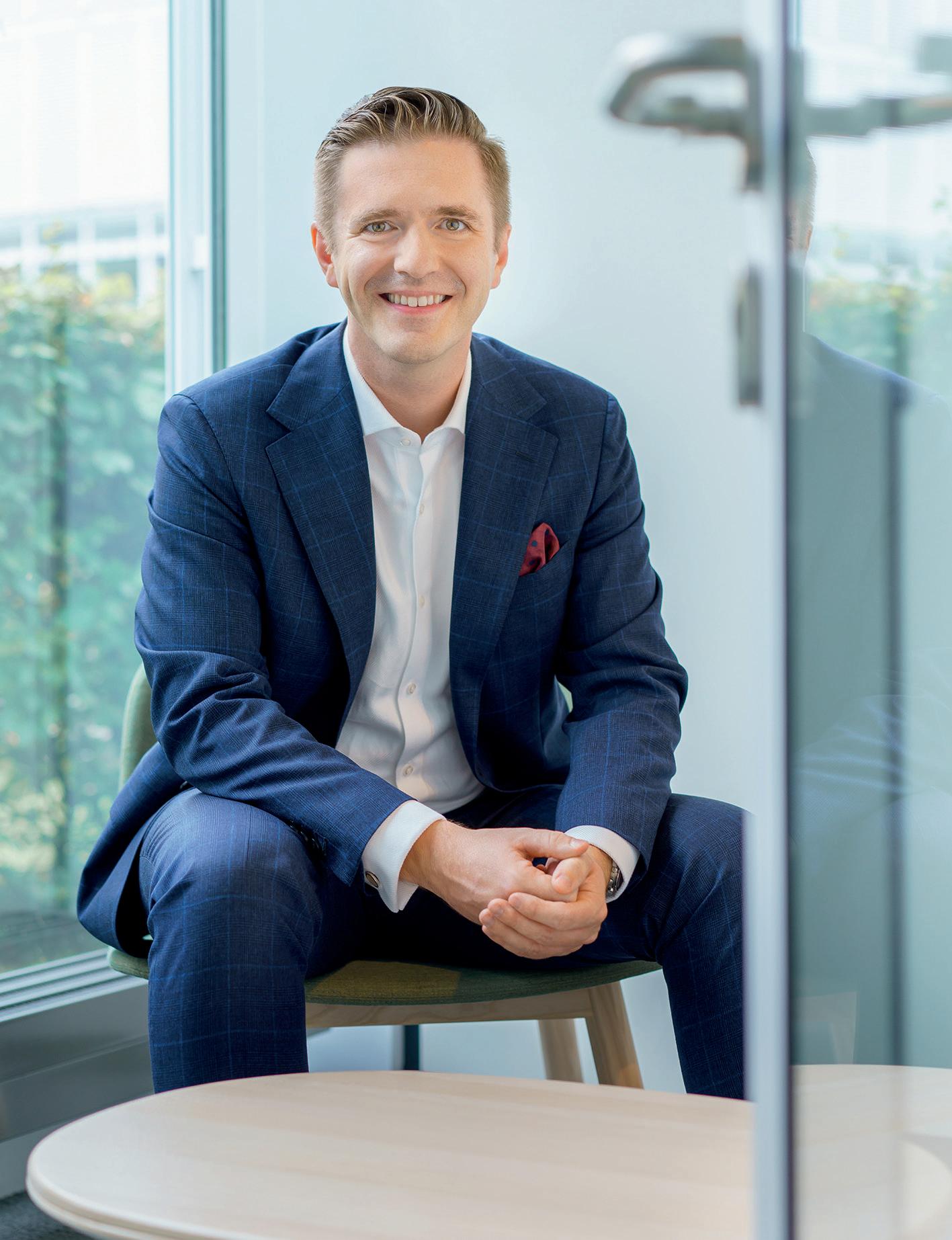
Motor data is gathered and uploaded directly to the cloud, where it is accessed at regular intervals by an ABB energy efficiency experts. They evaluate the energy consumed by individual motors and compare it with the work done. The experts provide a regular report with recommendations on actions, as well as their cost and the return on investment that can be achieved.
This provides evidence for SCA to prioritise investments in upgrading motors, adding VSDs or changing the operating regime to save energy. The advantage of carrying out this review periodically is that as the cost of energy changes, so does the payback period. Therefore, when energy prices are high, the operator can achieve savings by acting quickly.
SCA’s team is also looking at data from the same source to understand and improve the reliability and availability of its machines under a conditionmonitoring strategy. This enables it to carry out predictive maintenance and optimise its operations.
A further benefit of monitoring and evaluating energy efficiency is the sustainable recycling of motors that have been replaced by modern high-efficiency models. By separating old motors into their component materials, ABB’s recycling partner in the Nordics, Stena Recycling, can recover high-value copper and iron. This can then be recycled for use in new products in a circular process that reduces CO2 emissions and water compared with using virgin materials.
Waggeryd Cell boosts energy efficiency
Waggeryd Cell in southern Sweden is another example of a mill that is identifying energy efficiency savings as a secondary benefit to using condition monitoring. The mill produces 190,000 tonnes of bleached chemi-thermo-mechanical pulp (BCTMP) per year for production of paperboard, tissue, printing paper and writing paper using wood chips from its parent company ATA Group, a major producer of sawn timber. Its mill is one of the most modern and efficient BCTMP mills in the world. To build on this, Waggeryd decided to connect its motors to the cloud with the goal of gaining continuous insight and deep knowledge about the equipment serving its critical line. To achieve this, it is gathering data from around 100 critical motors out of a total installed base of 450 motors.
As well as providing insight into the performance and condition of motors to support Waggeryd’s maintenance planning, the data has also identified energy-saving opportunities. An initial report in early 2022 identified 10 motors with low operating efficiency, as well as others that are oversized (and therefore underutilised).
Using this insight, Waggeryd decided to prioritise upgrade of six of these motors. This shows how the data-driven approach can be used to pinpoint energy savings that could be hard to identify in other ways.
Andreas Råvik, mill manager at Waggeryd Cell, said: “We have improved our energy efficiency by working with ABB. By using their energy reports, we can identify assets like incorrectly dimensioned motors, or old motors with poor efficiency, and replace them.”
Data-driven decisions
Although some of its early adopters come from the Nordic pulp and paper industries, this new breed of digital powertrain service can be applied to any industry, anywhere.
It is a potential solution to operators that are under pressure to make the best possible use of energy resources. Digital energy efficiency audits, which are sometimes also known as appraisals, can help by pinpointing the precise location of potential energy savings in mills and other sites.
Ultimately, as a new-generation service that sits alongside remote condition monitoring, digital energy audit services can help pulp and paper mills to cut energy consumption and target investment where they can get the most benefit.

More information from: new.abb. com/service/motion/data-andadvisory-services/energy-appraisal
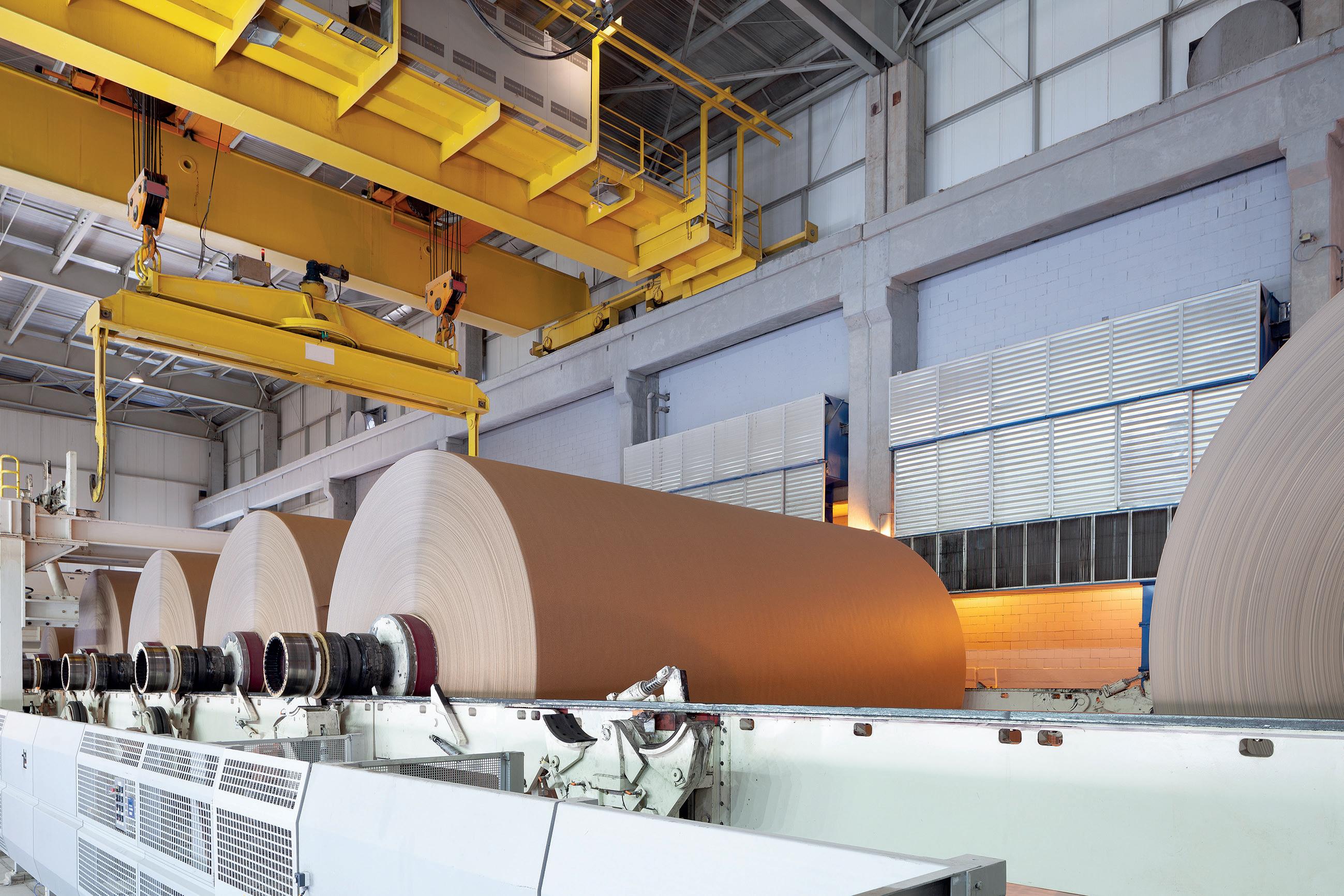