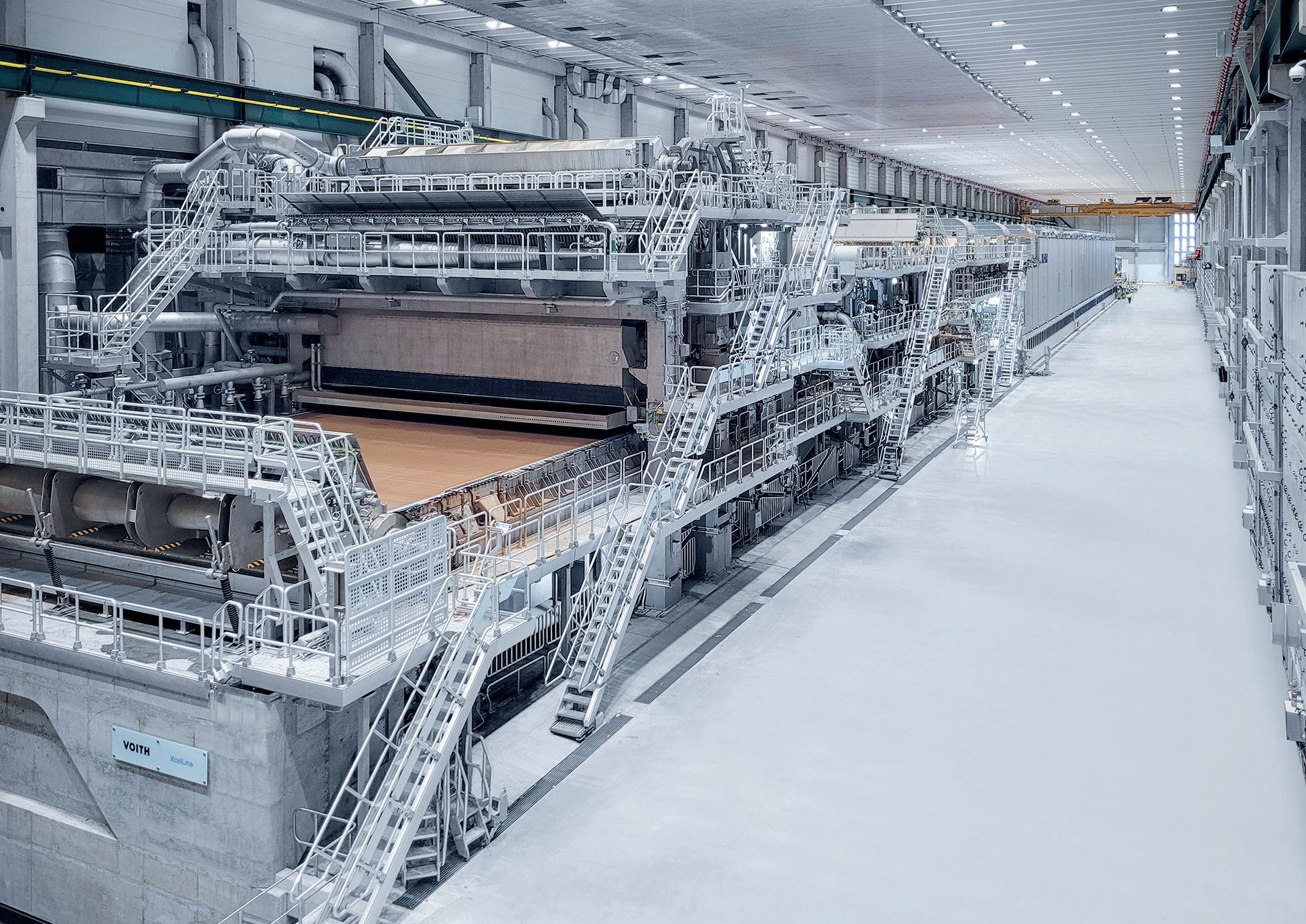
2 minute read
SCA improves efficiency and saves resources at Obbola mill
In Sweden, SCA reports that it is successfully using Voith’s digital and automation systems to optimise the production efficiency of the new XcelLine paper machine at its Obbola mill.
The PM2 line, said to be the world’s largest of its type annually producing 725,000 tons of kraftliner with basis weights between 100 and 200 gsm, was commissioned by the full-line supplier last year. It has a wire width of 10.2 metres and a design speed of up to 1,400 metres per minute.
Advertisement
“The journey for SCA and Voith together has only just begun,” says Gustaf Nygren, manager of the Obbola mill. “We have a long-term partnership in place with the target of reaching the common vision of PM2 in Obbola becoming the new reference for safety, efficiency and digitalisation.”
To achieve its goals, SCA is using more than 10 innovative digitalisation and automation systems throughout the machine, all from Voith’s Papermaking 4.0 portfolio, and its BTG subsidiary.
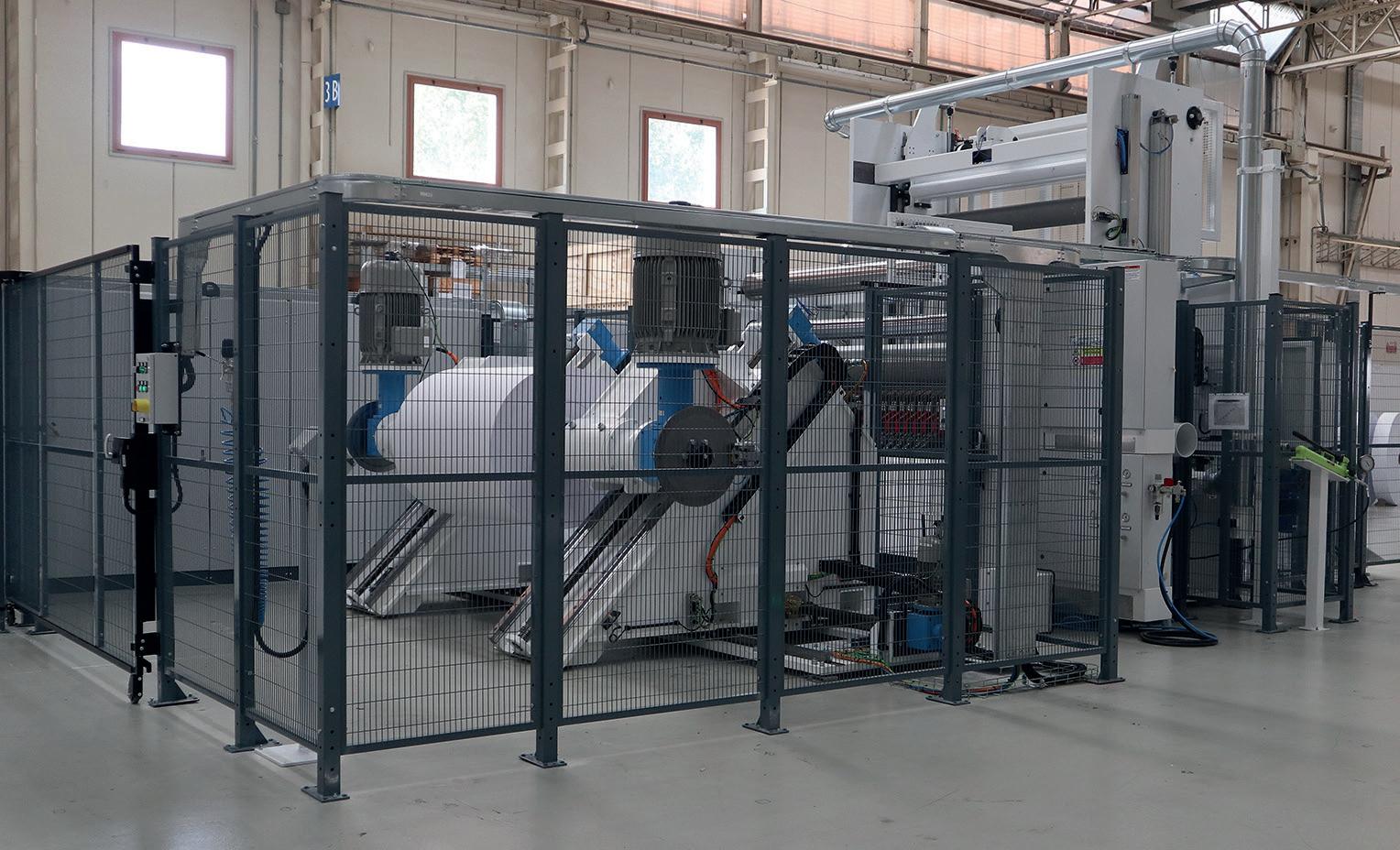
Typically, the OnEfficiency family helps increase line efficiency and stabilise product and process quality. The improved efficiency reportedly also contributes to more sustainable and resourcesaving paper production. SCA uses applications from the OnCare family to monitor productivity and to quickly take optimisation measures.
Machine availability is further increased by digital services such as the OnCall.Video remote maintenance service. The digital portfolio is made available on Voith’s IIoT dataPARC cloud platform, which features the highest security standards.
“With the PM2, we will take our next steps in the digitalisation journey. The applications provided by Voith will help us to monitor the process and make the right decisions,” says Niclas Ahnmark, paper mill manager at SCA.
SCA has also signed a longterm service agreement with Voith subsidiary BTG for process control. BTG’s Lifecycle programme ensures optimum consistency and control with the use of preventive maintenance for all of the consistency sensors, including regular calibration and routine checks. BTG Field Service Engineers assist in the planning, implementation and coordination of the various maintenance services, maximising machine uptime and stability while maintaining SCA’s high safety standards.
The collaboration with SCA is long-term and is particularly evident through the Efficiency Partnership. Throughout the process, the teams work closely together to ensure that the systems are used at the optimum.
Stephan Sicking, vice president of sales for the EMEA region at Voith Paper, explains: “As part of a digitalisation roadmap, we have defined common goals and KPIs in a cross-functional team, developed a customised concept and are now providing support for successive installation and employee training. Already, the benefits from this collaborative approach are clearly demonstrated.”
Record start up time for Kostrzyn mill’s new rewinder
A paper rewinder supplied to Artic Paper’s Kostrzyn mill in Poland by A.Celli has been started up in record time.
The E-Wind P80 rewinder’s installation, commissioning and start up took just 22 days.
The rewinder has since been used with what are “great results” to produce uncoated wood-free paper reels with basis weight from 38 to 170 gsm and width of 1,800 mm, and at a design speed of 1,500 metres per minute.
Michal Jarczynski, chief executive of Arctic Paper, says:
“We are very happy with the work done by A.Celli, both for the rewinder itself and for the very short time between installation and start-up. Performance are also in line with expectations. I can confidently say that A.Celli’s solutions quality is top-notch.”
Arctic Paper Kostrzyn, part of Arctic Paper SA Group, is the largest producer of paper for offset printing in Poland with a capacity of 315,000 tonnes per year. Under the brand name Amber the mill produces uncoated wood-free paper for general printing of books, brochures and documents, as well as modern papers for highspeed inkjet printing.