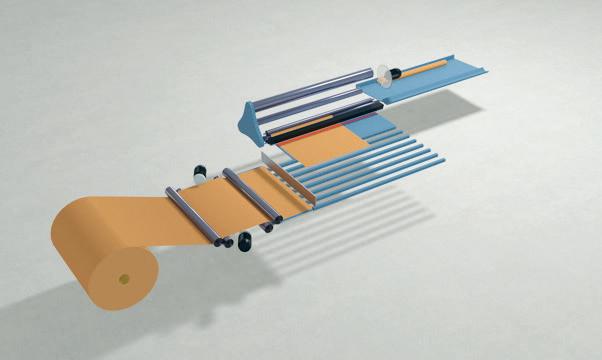
5 minute read
CFE NORDIC
20 ABB CFE NORDIC
The core handling revolution
Advertisement
Could the techniques used in the paper making industry for producing and handling cores be made more cost-effective? Karl-Henrik Axelsson* suggests a completely new concept
Imagine the savings that
could be made if the paper industry was able to replace the traditional way of managing the production, storage and handling of cores.
What if a completely new and revolutionary process could be devised that enabled paper mills to produce their cores in-house and just-in-time only a few metres away from the winder?
Imagine the savings this could produce for the mill, and the savings for the environment?
For the last 50 years or so, the core handling process has been more or less unchanged. Cores are produced at some distant plant where they need to be stored until they have hardened enough to be loaded up on trucks and transported to the paper mill. At the paper mill, the cores have to be unloaded, stored in large volumes and finally cut into different lengths before they are transported to the winder and used to produce the desired width of paper rolls. This has been the standard for many years and mills have become accustomed to the costs that result from this.
The paper industry is not resistant to change. It knows that in Europe alone cardboard cores cost several hundred million euros per year, so mills are eager to find new ways to reduce the environmental impact, reduce the cost, improve the working environment and reduce the use of raw material. But if the traditional suppliers have nothing new to offer, what are the May/June 2022 Making paper roll cores as required using CFE Nordic’s ‘Lean core concept’ could save
alternatives?
But now there is a new development in the pipeline, the ‘Lean core concept’.
Supported by Sweden’s innovation agency, Vinnova, CFE Nordic has been developing its patentpending ‘Lean core concept’ to meet these needs from the industry.
The ‘Lean core concept’ offers the possibility for paper mills to manufacture the cores themselves, adjacent to the winder only when cores are needed and to the precise length so the cores can be used directly in the winder.
The winder sends information to the core system as to which lengths of core are needed in the next time period. The system will then start to cut a preset number of sheets from a paper roll and from these sheets the system will form a core with the desired thickness and diameter.
The core is then trimmed to the precise length and fed to the winder. The core does not need to be stored or hardened, because the idea is to use it immediately. The process is repeated until the ordered number of cores has been made.
The ‘Lean core concept’ offers a number of advantages for the paper industry. There is need to purchase cores from a distant third-party core supplier, and cores have to be transported, often over long distances, before they reach the paper mill.
The ‘Lean core concept’ eliminates a lot of the problems mills are facing when managing a modern core handling system. Problems such as lack of suitable facilities and floor space, the need for large areas for storing cores and equipment, problems with logistics and trucks needing to have mill access for delivering truck load after truck load with cores. Then comes the question where to place all the equipment for cutting cores and transporting the cut cores to the winder.
Many of these challenges and problems will no-longer exist when using the ‘Lean core concept’. In contrast, the ‘Lean core concept’ offers a completely new way of thinking and managing the core handling of tomorrow and offers the possibility of automating the core handling even further. Automatic core handling offers cost savings, improved competitiveness, and a better working environment for staff.
What this adds up to is reduced
Pulp Paper & Logistics ABB CFE NORDIC
cost: for a typical board mill, the cost reduction could be hundreds of thousands of euros, just focusing on the cost for cores. But there are also a lot of other possible savings. For example, the floor space that is currently used for storing cores can better be used for more important activities. Furthermore, the concept entails several environmental benefits, such as eliminating the energy consumption which is needed when storing and drying newly manufactured cores and reduced carbon dioxide emissions through less road transport.
There will be no need for the mill to invest in core handling: no more core cranes or core storage, no core cutter, no handling of cut cores, etc, etc.
Instead, there is a significant possibility to make stronger cores using less material and therefore further reducing the costs.
In Europe there are between 200 and 300 paper mills producing more than 100,000 tons of paper or board per year, paper mills that could benefit from a system like this. The concept offers huge opportunities for paper mills as well as for leading machine suppliers.
You don’t have to wait any longer for the core handling of tomorrow: the ‘Lean core concept’ is already here.
More information from CFE Nordic AB, Skärslidarna 118, SE311 78 Falkenberg, Sweden. Tel: 46 705 19 32 71. Website: www. cfenordic.com Typical storage of paper cores: space hungry and potentially damaging
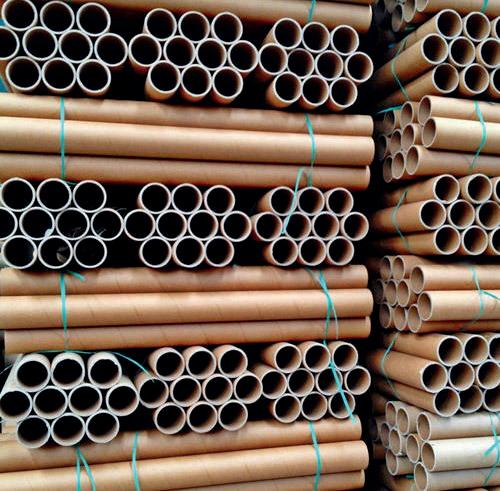
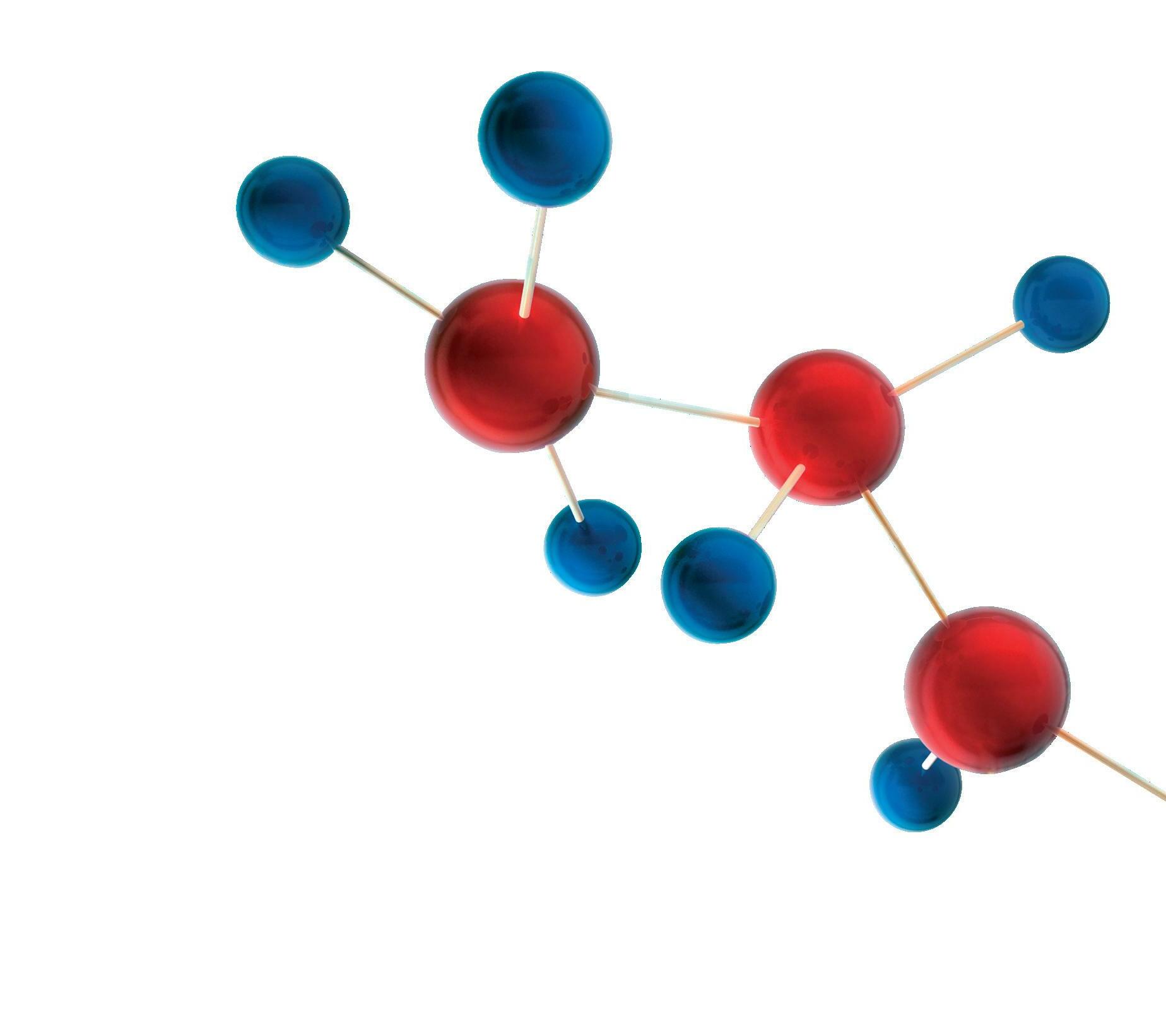
7–9 June 2022
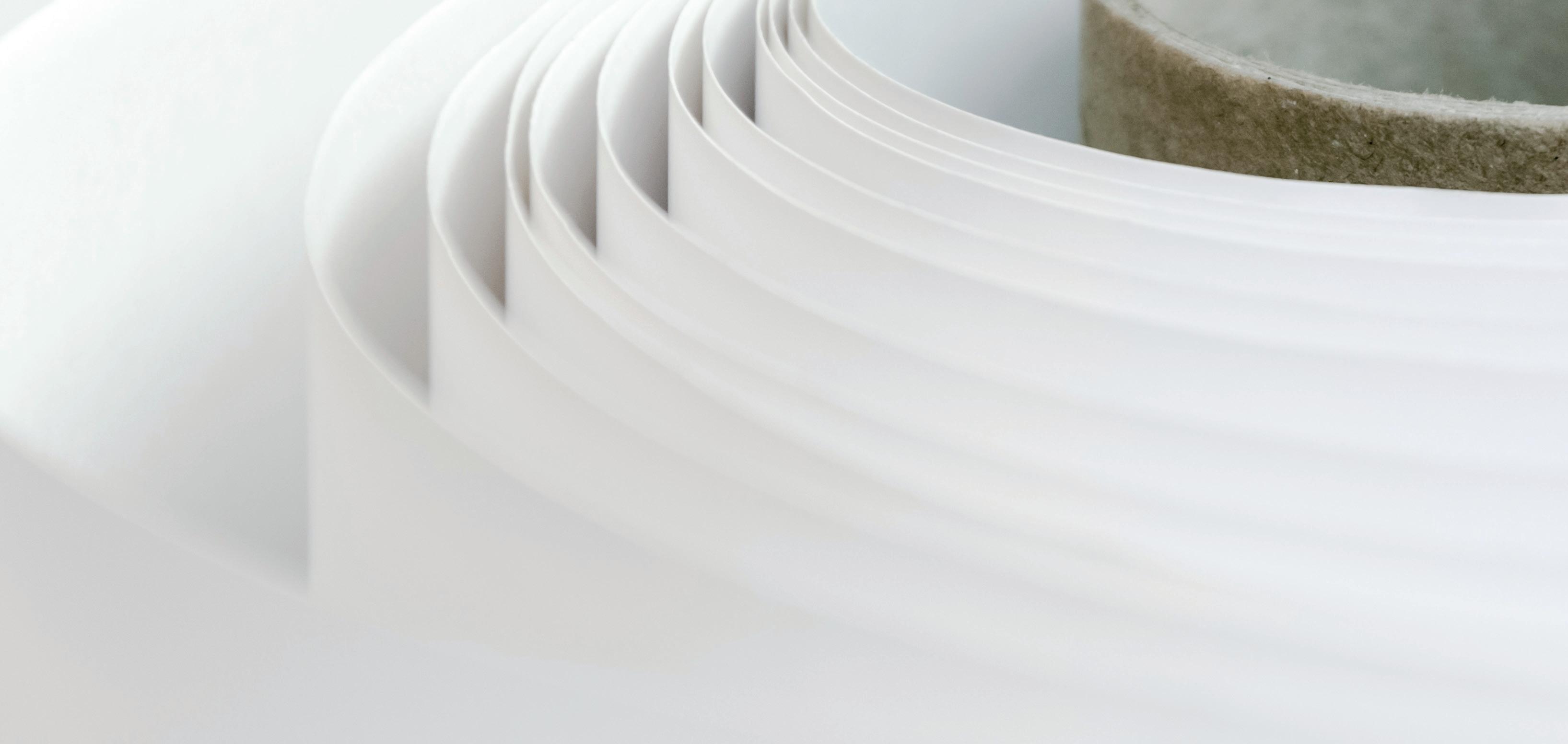
HELSINKI, FINLAND
BUILDING TOMORROW’S BIOECONOMY
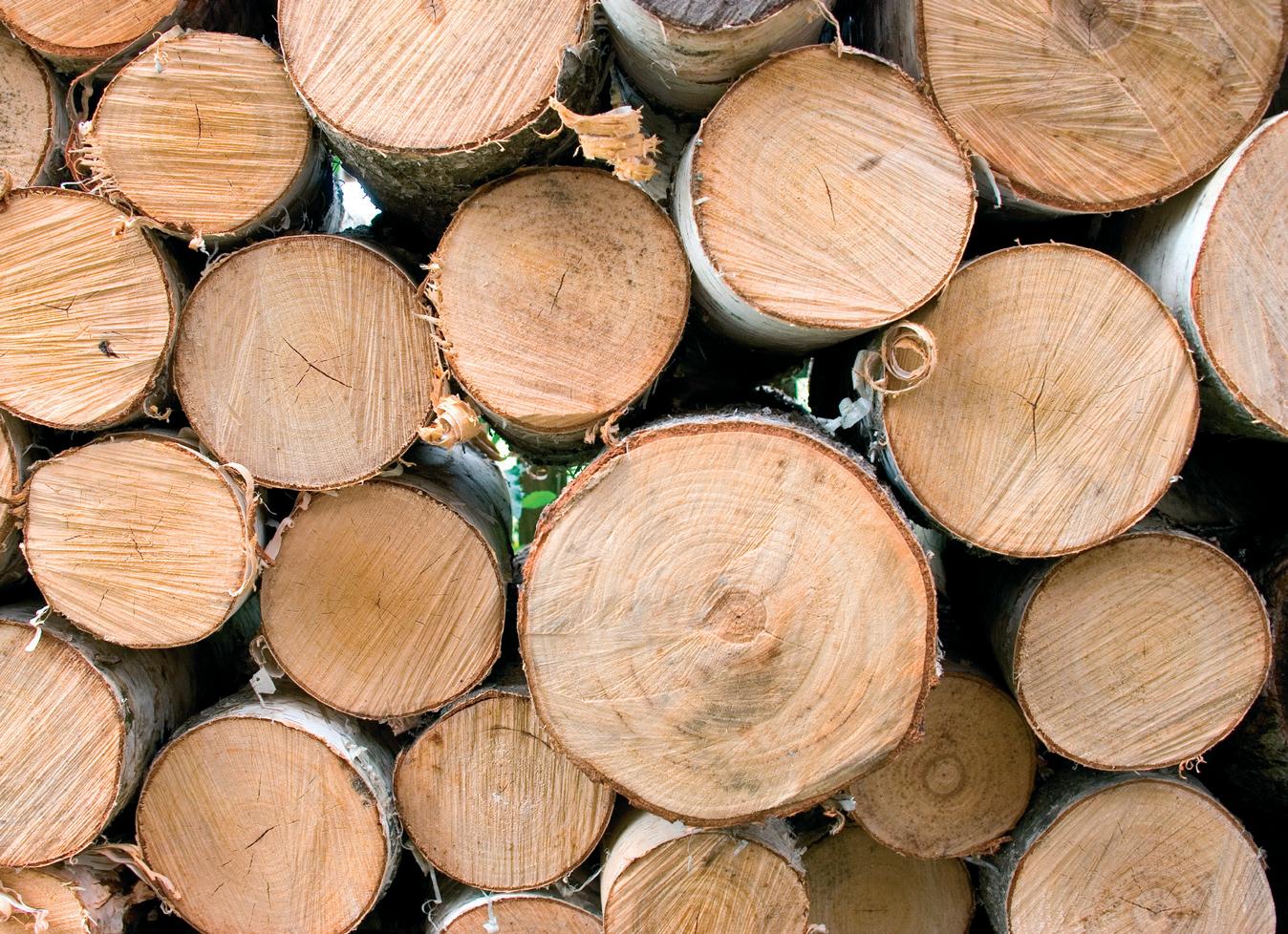
PULPAPER IS ORGANISED AT THE SAME TIME WITH the leading Nordic chemistry and biotechnology event ChemBio Finland and the international chemistry conference Helsinki Chemicals Forum.
Welcome to the leading international event for the forest industry
PulPaper is the forum for the latest technology and offers optimal business and networking opportunities in a multinational environment. The global industry will once again be gathered in Helsinki.