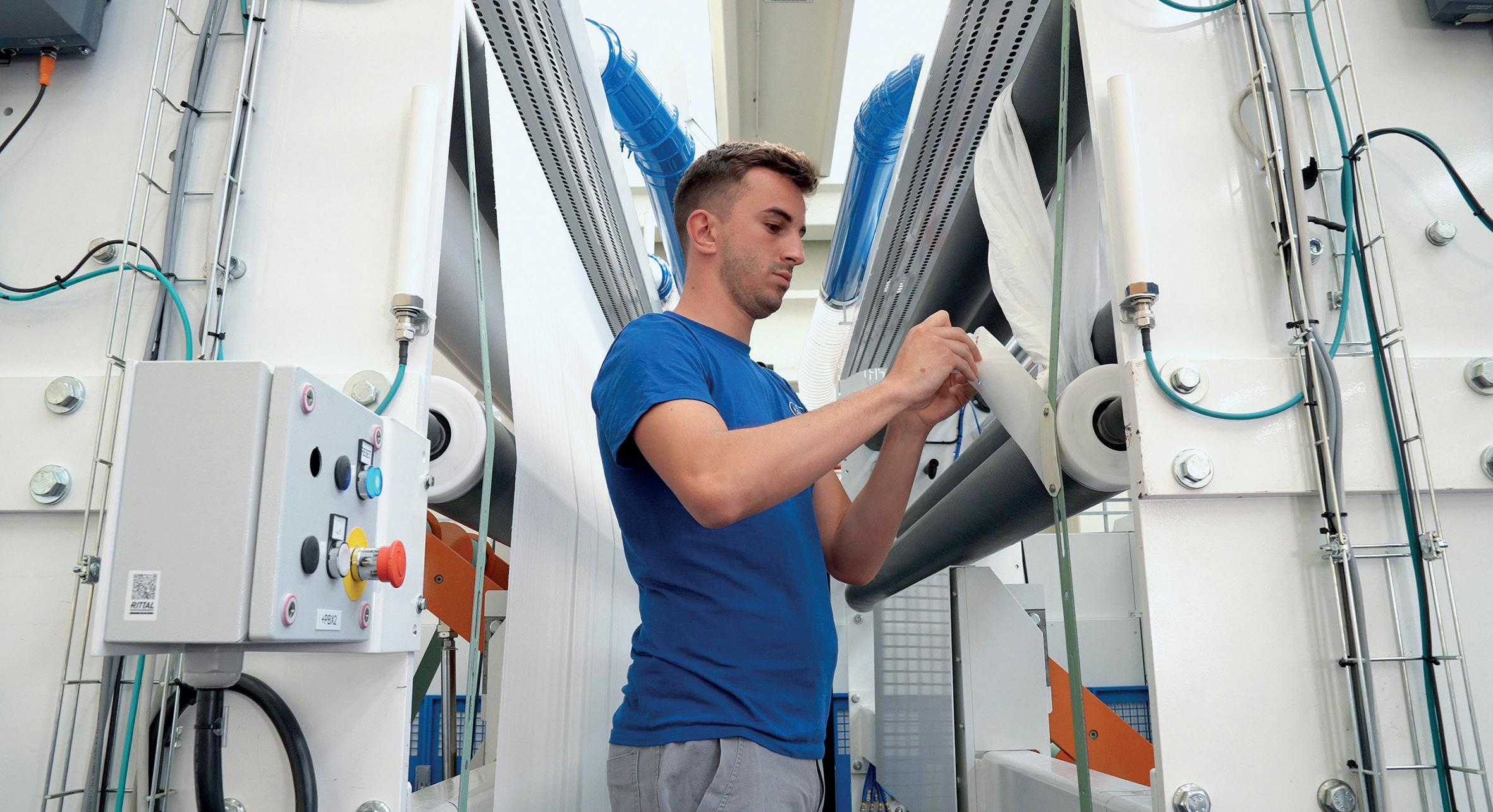
5 minute read
Improvement programmes reduce the total cost of mill ownership
Efficient, safe and easy to use: Körber’s latest Technical Improvement Programs reduce operational costs in tissue and tissue converting systems. PPL reports
In today’s difficult market environment, reducing expenses and production time and effectively managing asset life cycles are essential factors for capitalintensive companies to remain competitive.
Advertisement
To this end, the Total Cost of Ownership (TCO) is a critical decision-making tool with which mill owners can proactively assess how the effectiveness of their plants and their associated components may develop, ensuring their continued functionality. A further benefit of the model is having a clear view of costs and economic benefits deriving from correct maintenance.
In this systemic perspective, technology and automation provider Körber is committed to reducing the TCO by maximising the OEE of paper converters, thanks to its ecosystem, which integrates technologies and services designed to simplify the entire tissue manufacturing and packaging process, whether in the form of rolls or folded tissue.
Alessandro Borelli, customer service director of Körber’s tissue business, explains the scope of the company’s activities: “There are more than 20,000 machines installed by Körber Business Area Tissue worldwide: l 35 per cent in Western Europe l 8 per cent in Eastern Europe l 15 per cent in South America l per cent in North America l 8 per cent in Central America l 8 per cent in APAC countries l 6 per cent in China l 5 per cent in Africa.
“As the leader in this technology, Körber has a structure dedicated to assistance, which, in addition to combining smart services with the capacity for developing the finished product, provides field-tested technical skills capable of maintaining high plant performance in the long term. More and more customers rely on the experience and skills of OEMs and this is testified by the fact that sales of the entire service chain recorded a growth rate of 44.7 per cent from 2018 to 2022.
“For Körber, ensuring maximum continuity of customer operations, first of all, means constantly monitoring the current 3,000 production lines worldwide through its Tissue Performance Center, either with an ongoing diagnostic connection service or on demand. Secondly, Körber guarantees qualified and proactive technical support remotely or on site to minimise downtime and support customers in identifying and solving problems, so that the installed base is always up-to-date and efficient.
“In 2022 alone, over 500 onfield activities were performed. A significant part of them were carried out within the framework of Technical Improvement Programs (TIP). Thanks to this service, technological adjustments are made to new- and oldgeneration systems to guarantee high standards of safety and efficiency.”
The strategic and sustainable role of TIPs
Greater sustainability, safety, efficiency, performance and productivity are the priorities for the customers to whom Körber Business Area Tissue caters with more than 300 standard TIPs, already implemented today, to which those designed according to the specific needs of tissue companies should also be added.
There are six TIP macrocategories aimed at minimising the environmental impact of production and finished products and at guaranteeing operator safety in compliance with the most recent regulations. Activities may range from work on small machine parts to a complete overhaul of the entire line, giving it new life and sometimes a new registration and CE marking based on customer needs. This business model, that keeps the investment of Körber customers tenable in the long term, is also based on design criteria that presuppose the possibility of retrofitting machines with the most recent process and product technologies developed for the new series, even over a large part of the installed base, to keep it always up-to-date.
Efficiency and safety: New electrical cabinet TIP
With the replacement of the entire electrical cabinet for wrappers and bundlers, Körber’s offerings are designed to guarantee a stabilisation and an enhancement of the machine performance, in some cases even by 20 per cent.
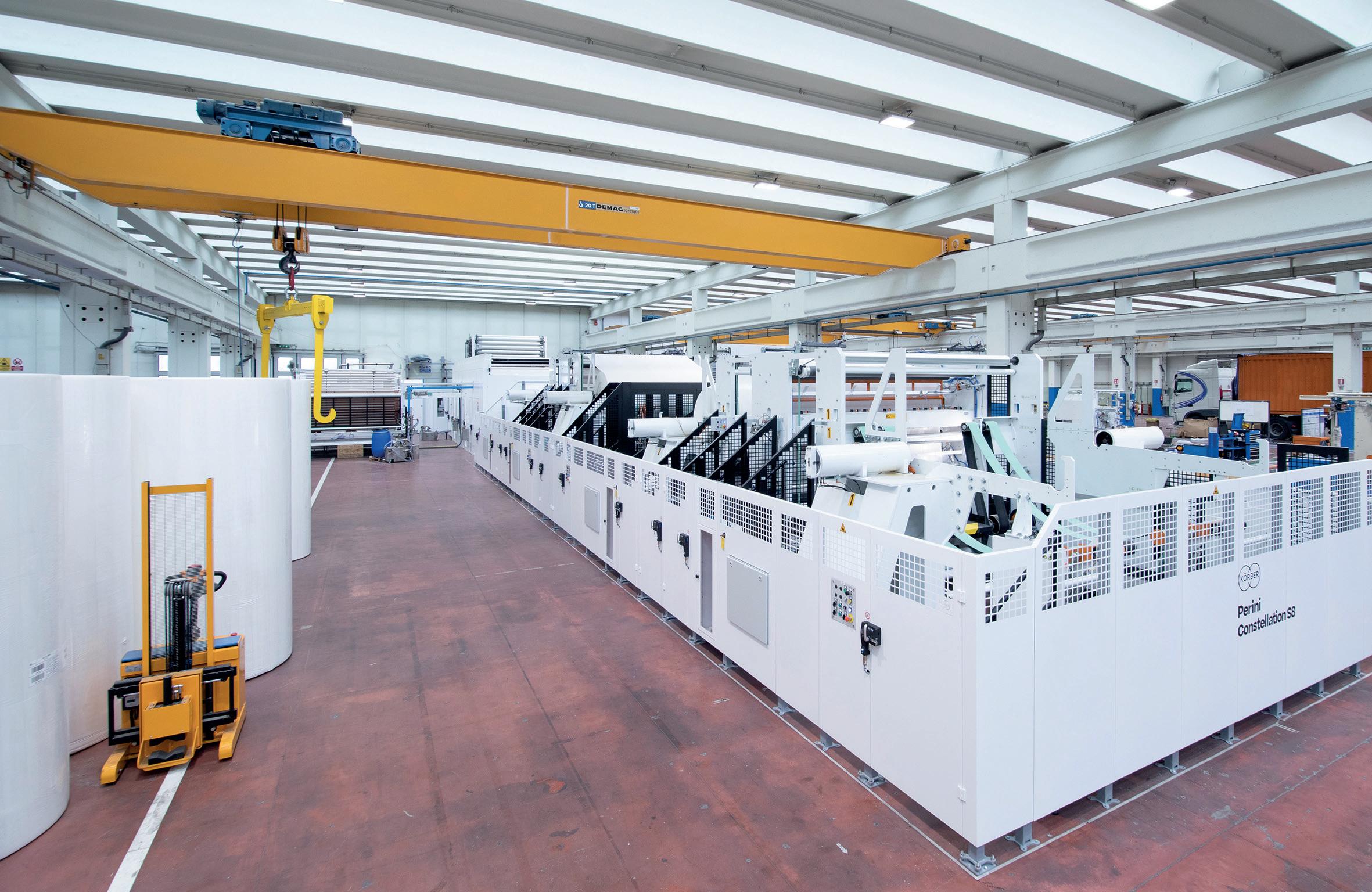
The installation of the latest generation 4.0-ready components ensures the management of the motor logic, of the axis control, and of the on-board machine systems, simplifying the command interface and eliminating any obsolescence. For example, electronic limiters instead of physical systems acquire itself what difference a technology leader can make in a mature market” a higher efficiency in containing some critical forces for a significant reduction in the wear-and-tear of mechanical parts and of the cycle speed.
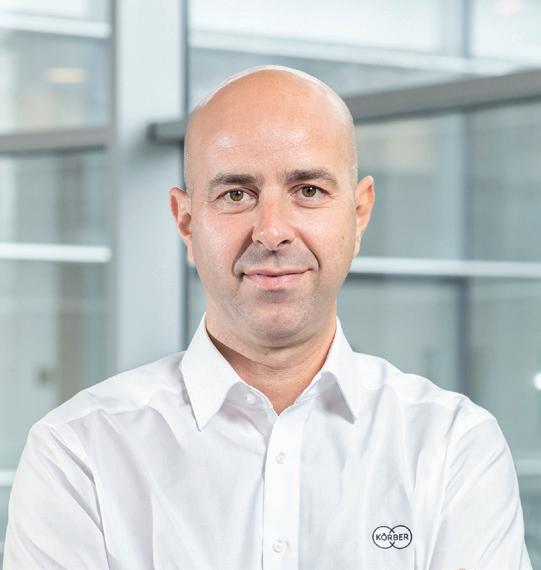
Furthermore, the installation of the Mguard system for the Expert Online connection simplifies troubleshooting in favour of prompt remote work by Körber technicians.
Asset protection and fire detection: Thermo-cameras
TIP plus Fire fighting system
The main advantage of this improvement programme by Körber is the prompt detection of anomalous heat concentration on all converting and packaging lines by using thermo-cameras. This technology ensures a high level of detail in thermal images, which are sharper and make it possible to identify any components prone to malfunction more quickly and in real time and to take action promptly.
The intelligence applied to these systems is also able to determine whether, under the same production conditions, there are drifts in the expected temperature parameters, giving advance information so as to anticipate serious breakdowns and machine downtime.
In addition to thermo-cameras, an advanced fire detection system based on a simple but highly stable and functional technology can be installed on all lines. This excludes the use of optical sensors, which are typically unsuitable for the paper environment, and is free of dust, oil, water and dirt. Finally, extinguishing is achieved with a low-pressure water mist system. The latter can also be integrated into the machine’s logic functions in order to prepare all the necessary actions for the reduction of unexpected problems. These are solutions that safeguard operators and the capital invested in high-value equipment and play a crucial role in industrial production.
Easy to use: Auto web starter and Easy Reel change
Simplifying tasks for operators and reducing downtime are Körber’s additional goals. Easy reel change and Auto web starter stand out among the most requested TIPs from customers.
The first allows the replacement of finished reels on traditional unwinders and the restart of production in just 90 seconds with standardised and repeatable procedures. This option may be installed on Körber medium and high-level tissue unwinders without automatic reel change systems.
The phase in which the paper passes through the machine following an unexpected paper break, or a restart due to a production change, is by far the most critical moment in terms of safety, as well as a costly one in terms of machine downtime.
The new Auto web starter has revolutionised the process of the manual web thread-up through the machines.
This automates and facilitates the process by combining three systems in succession. In the first one, the insertion of the flap of paper into suitable plastic shuttles hooked to the belt enables operators to govern the machine’s start-up from the HMI panel outside the perimeter casing, with doors closed. In the second system, provided that the line configuration is suitable, the shuttles carrying the paper are automatically swapped on distinct belt branches.
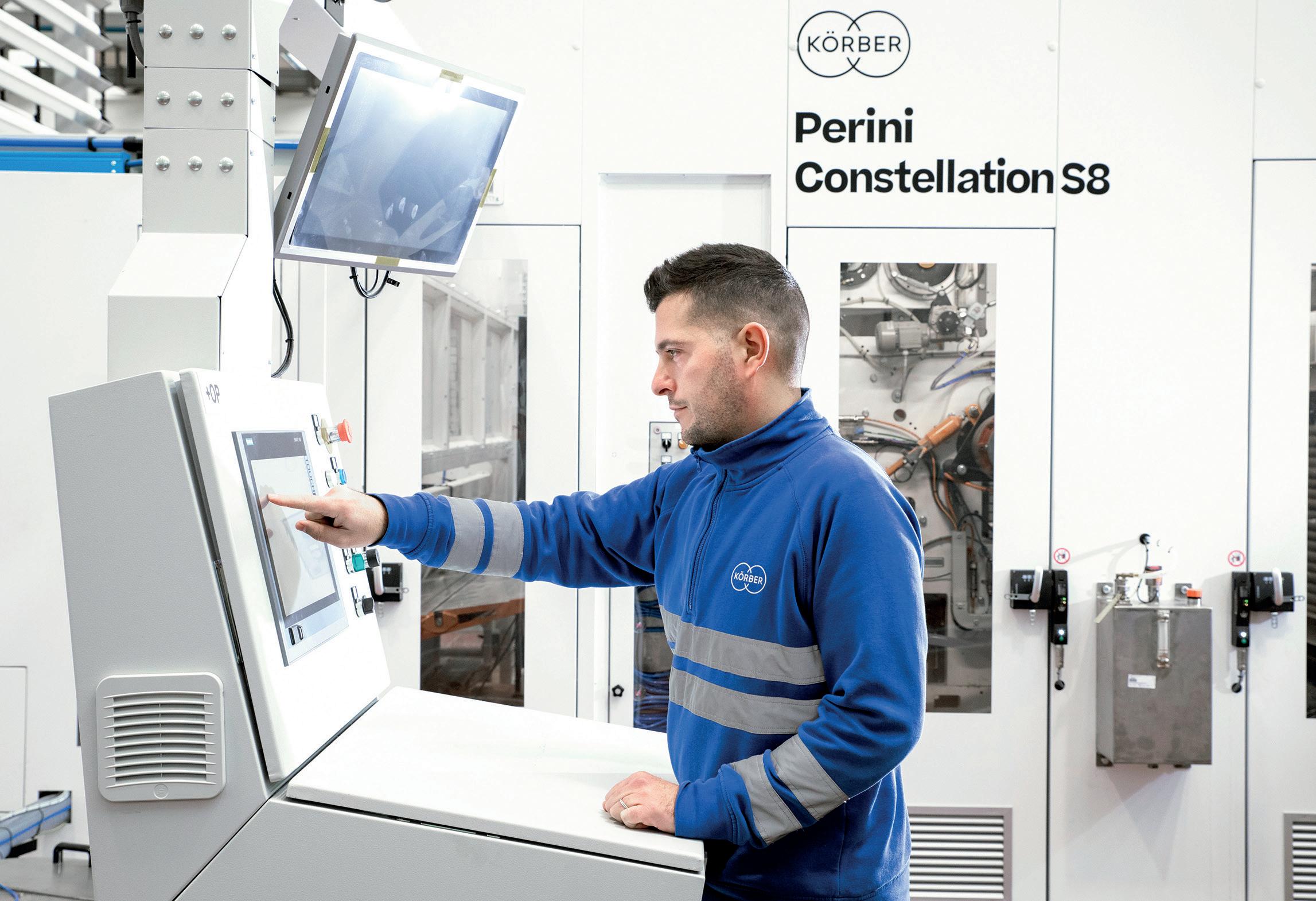
Ultimately, the line can be restarted with the doors closed and in a fully-automated manner without requiring any intervention from the operator. This standard technology for new plants is available to be customised on existing lines.
“The volatility of the cellulose market, the lack of skilled labour and the challenges generated by an increasingly global and sustainability-oriented sector are encouraging tissue companies to seek ever-more scalable solutions,” says Borelli.
“Every day Körber asks itself what difference a technology leader can make in a mature market. The answer lies in its ecosystem in terms of new plants and in terms of customer service experience. A unique supply of its kind which, in addition to making Körber a strategic partner, integrates innovative technologies, digital services and supply chain solutions fostering the customers’ competitiveness in terms of product differentiation and profitability over time.”
More information from Körber Tissue SpA, Via Giovanni Diodati, 50, 55100 Lucca, Italy.
Website: www.koerber-tissue.com
About Körber
Körber is an international technology group with annual sales of about €2.5 billion, more than 12,500 employees and more than 100 locations worldwide that work in Digital, Pharma, Supply Chain, Tissue and Tobacco.