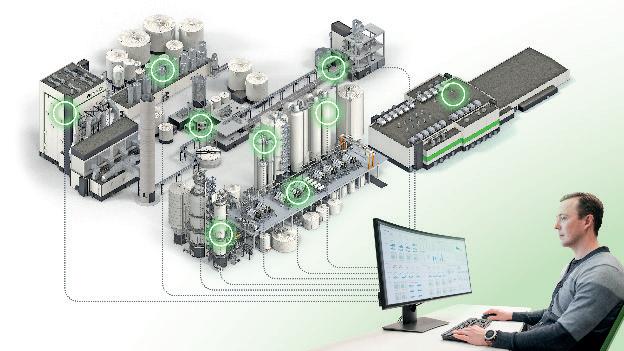
1 minute read
Optimised mill operations steer pulp and paper mills toward shared goals
Launched by Valmet during customer open days in Copenhagen at the end of March, Mill-Wide Optimization (MWO) is said to enhance overall pulp and paper mill profitability. Using MWO, production teams are able to boost a mill’s performance by making better-informed decisions across various process areas towards shared goals.
MWO observes the entire mill balance in real-time and considers both the current and future states of the mill. As a result, individual processes that do not align with mill objectives can be avoided. MWO also provides the ability to balance environmental sustainability with production, quality, and cost, says Valmet.
Advertisement
Greg Fralic, product manager for Mill-Wide Optimization in the automation systems business at Valmet, commented: “The pulp and paper industry is transitioning towards self-governing autonomous operations and towards a younger workforce with new roles and responsibilities.
“Valmet MWO helps to capitalise on these changes and unlock the mill’s full potential.”
Mill-wide production planning helps mills to keep up with the daily changes in production bottlenecks. MWO reflects the mill’s current state and maximises production subject to existing and projected bottlenecks, while stabilising the process and balancing pulp and liquor inventories.
Quality planning throughout the mill helps attain the desired final product quality while keeping the costs low. It adjusts the quality targets at each step from chip to finished product.
To move away from optimising individual processes, pulp and paper mills need to be evaluated as a whole. Valmet’s MWO Audit helps to reveal the true production potential and the corresponding return on investment.
Based on historical data, the audit helps to evaluate production increase potential, identify limitations, and highlight use cases of mill-wide optimization. It also helps to uncover development opportunities required for moving towards fully optimised operations.