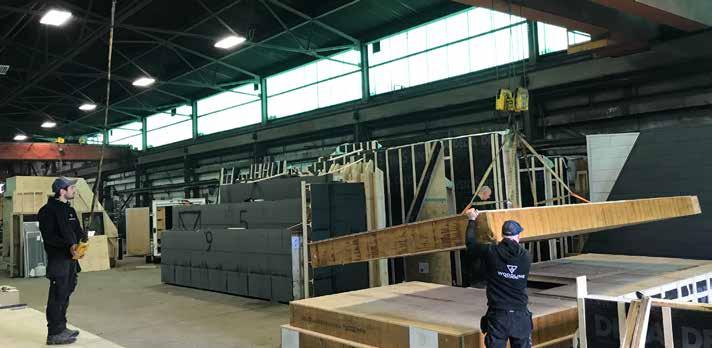
2 minute read
Then-and-now
The prefab manufacturer may have provided a solid skeleton, but interiors sport custom kitchen cabinetry, white oak engineered hardwood and porcelain tile floors.
Intertwined urban town homes Jenga-style living
Advertisement
TAKING ITS CUE from the Jenga wooden block game, Toronto, Ont.,-based design and development company Baukultur/ ca recently completed the construction of two new-build town homes integrated with sustainability in mind. With 25 feet in width available, according to architect Felix Reicher, it was necessary for the project, called zero79 (after near-zero carbon footprint and the street address), to create an innovative concept to realize the two Michael Rafelson ground-bound family homes on one shared infill lot. “I am taking what I am used to in Europe and adjusting it to how to use property or land that is much denser than here (Reicher is originally from The prefab approach minimized Germany). Properneighbourhood disruptions. ties that you can’t sever but you can still build more than one house,” he says. The zero79 project arranges the two 2,000 square foot, three-storey homes intertwined, one behind the other. Both homes are accessible through both the sunny front yard from the street, as well as to the back where each has a private backyard and garaged parking space. The homes share a meandering inner common wall which zones spaces within each home. The concept of arranging two homes behind each other on one lot is new to Toronto. “The city plan30 July/August 2020 30 July/August 2020 ning department was very much in favour of the project,” says Reicher. “But when it came time to obtain the actual building permit, that was tricky to explain.” To build the two, four-level residences (including basements), Reicher decided to pursue the plan to prefabricate the wall- and ceiling-panels off-site. The benefits of off-site construction reduced the impact on the neighbourhood’s residents, created a shortened construction period and provided an efficient use of resources and waste reduction, along with a build where the structural system would never be exposed to the elements.
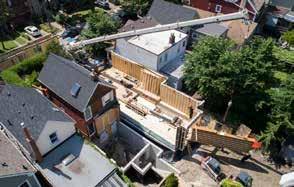
The prefabricated panels were then assembled on-site, and within five days the building was completely sheltered from the elements. Not only was the structural framing in place, when the panels were delivered and assembled on the property, but so were all windows, 6 in. of exterior insulation, the metal siding, and a temporary waterproofing membrane for the roofs. “Our R values are about double than what the building code requires,” says Reicher about his energy conservation philosophy. “We have triple glass windows. The entire house is run on electricity, so we don’t have fossil fuels coming into the house. All of the bathroom fans and kitchen exhaust runs through an energy recovery ventilator. We also used white roof membranes to minimize the heat in summer. “We reduced energy consumption by 60 percent compared to a house built to the building code. “The unit on the street is sold and the other one has an interested buyer,” he says. “The new owners haven’t moved in yet but they like the design and the cool features. ”
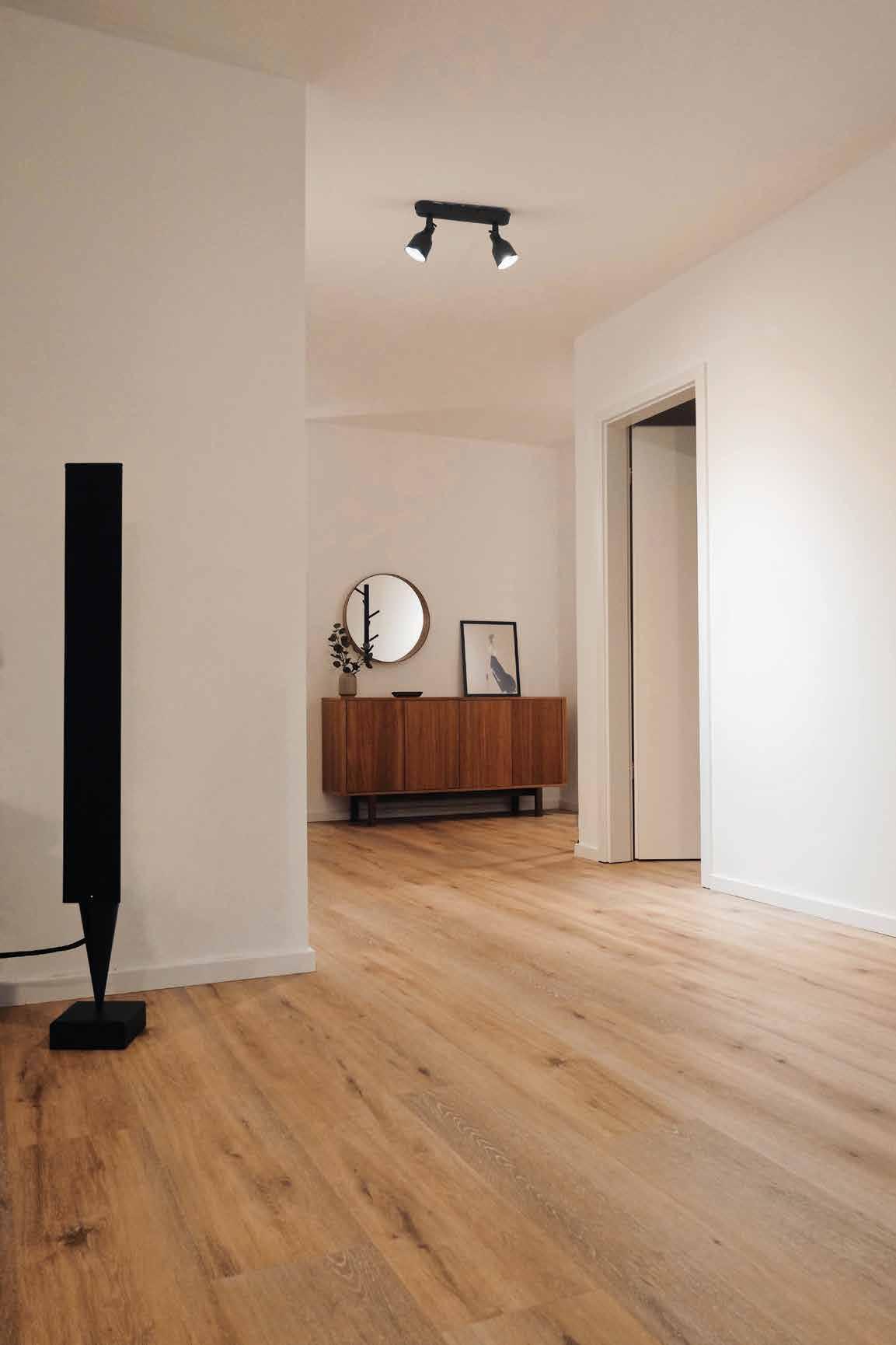
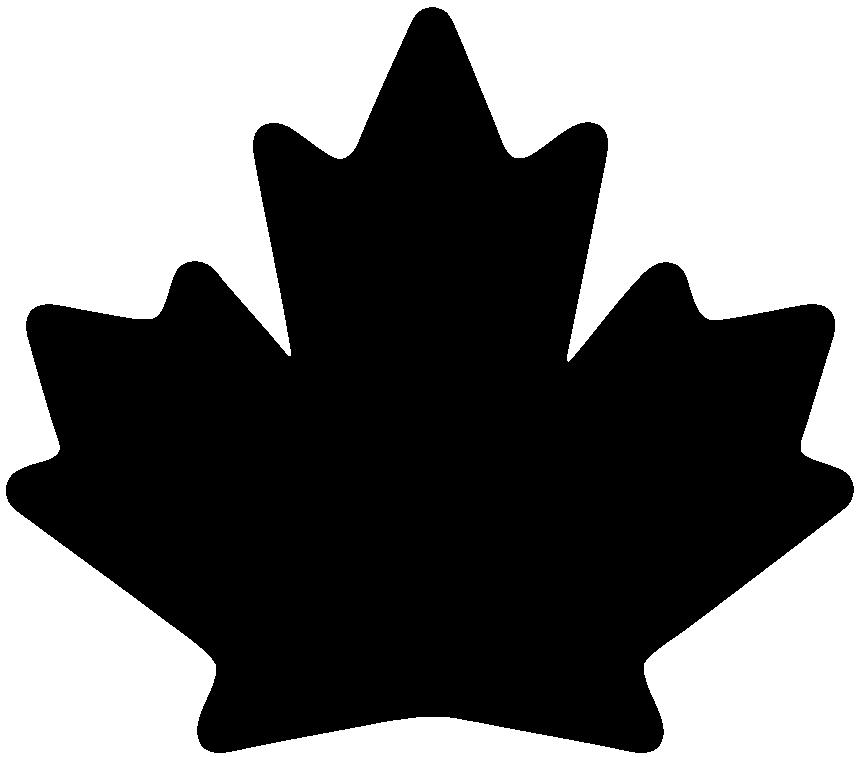