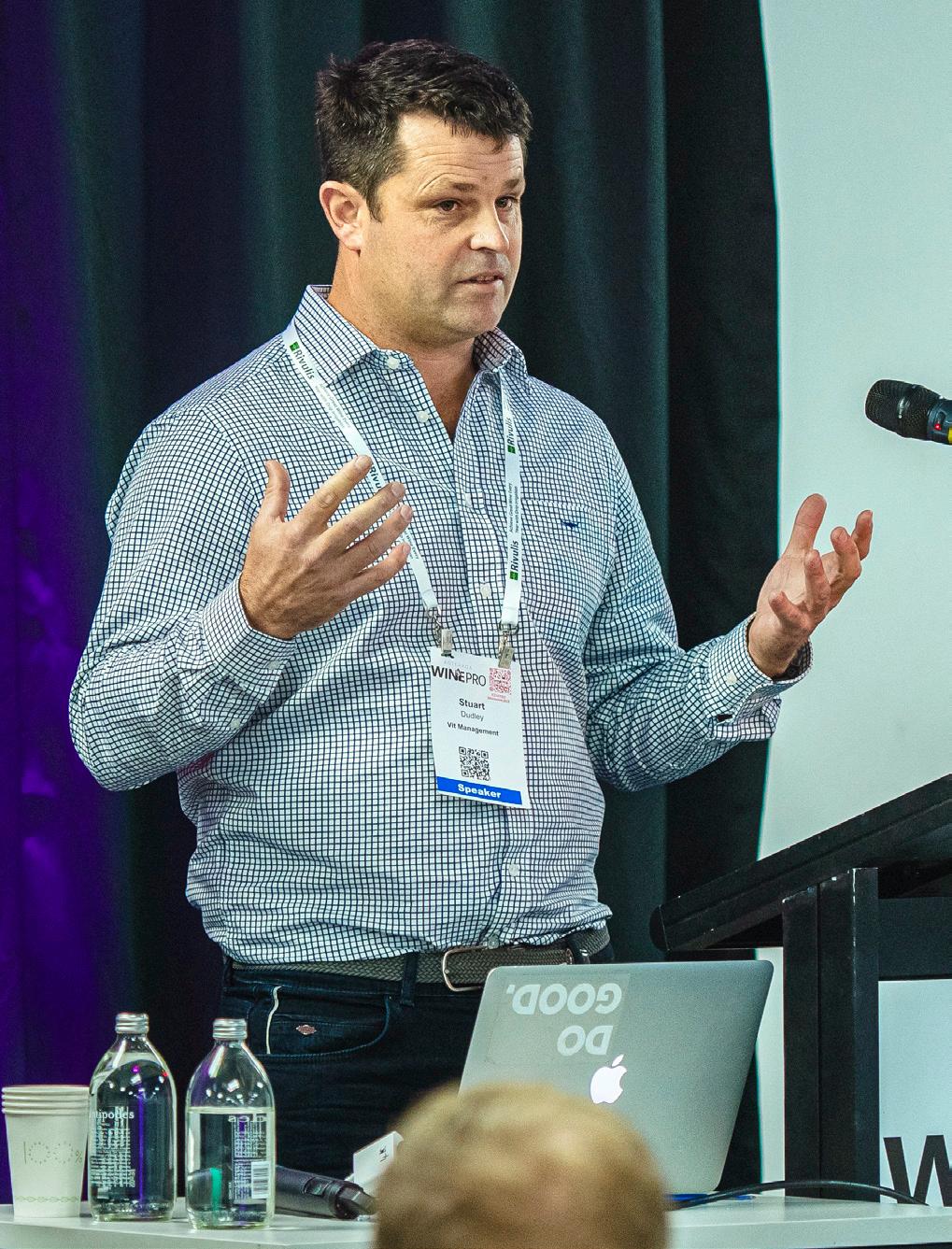
5 minute read
Winepress - October 2024
Out with the old
As original vineyards age, the time has come to replant. Whether filling gaps or starting from scratch, good planning is the key
PENNY WARDLE
THE FIRST Marlborough vineyards were established in the 1970s and amid all the land clearance, field preparation and large-scale planting it would have been hard to imagine ripping out the vines and starting again. Fifty years on, that time has come for more and more winegrowers. Disease, loss of vigour and the need to update varieties are all drivers for the vineyard redevelopment now gathering pace across the plains.
Redevelopment may be a daunting prospect, but it’s an opportunity to reset vineyards to thrive for 25 years or more, say viticulturists Stuart Dudley, consultant at End Point Viticulture and David Bullivant, Marlborough viticulture manager for Babich Wines.
Grapevine Trunk Disease is the main driver of falling vineyard productivity as New Zealand’s original vines age, Stuart says. There are two options: renewing the vineyard (replacing individual plants that are not performing while keeping the infrastructure); or biting the bullet and replanting the whole vineyard (with or without new infrastructure). Total removal and replacement of infrastructure and vines enables owners to consider new vineyard layouts in preparation for future developments, such as increasing use of autonomous vehicles for mowing, mulching, weed spraying and leaf plucking.
For those taking the renewal route, the top priority is to extend vineyard life by removing dead and sick vines then filling the gaps, Stuart says. Replacing 2-3% per year, with two to three years of training through to production, costs about $1200/hectare. “Renewal, if done well, is cheaper. But there often comes a time when total replanting is necessary. With a clean slate, I think you tend to get better responses in production and fruit quality.”
Infrastructure such as posts and irrigation lines are often left in place, “but only do this if it’s in good condition”. Stuart and David were part of a WinePro panel on vineyard redevelopment. The presentation showed the estimated cost for redevelopment that keeps existing infrastructure at $35,000 per ha; and full redevelopment at $70,000 per ha. However, these figures can vary depending on conditions at each property.
When making decisions about redevelopment, Stuart urges growers to “honestly assess drivers of falling profitability including increasing costs, poor production, falling grape quality and returns, growing the wrong grape variety or at the wrong density.” He recommends two, five and 10-year planning for vineyard renewal or replacement.
“Disease prevention is key to successful redevelopment,” he says. Old cordons and trunks are a major source of Grapevine Trunk Disease and must not be piled along fences as this could spread the problem to neighbouring vineyards. Removing as many roots as possible was essential to avoid pest and disease carryover.
As demand for removing vines increases, contractors are getting innovative. Where once vines were ripped out with diggers and burned, some operators now use heavy duty machinery to extract whole plants four rows at a time and shake the dirt off their roots. Also, plant material could be fed into a chipper and taken off-site to compost or convert to biochar.
“Redevelopment can create a lot of waste but, thankfully, there are now recycling and re-use options,” says Stuart. “A recent vineyard development reused about 40% of wooden posts thanks to repurposing by Repost.” Future Post, which makes posts from recycled plastic, will recycle driplines at no cost for anyone buying their products. Wire can also be collected and recycled into steel.
Once a block is cleared, there is the opportunity to identify any wet patches and improve drainage to avoid stranded machinery and damaged vines in wet harvests, says Stuart. Test soils and apply fertiliser to address any deficiencies. Crushing stones was an option, to avoid future wear and tear on machinery.
“Ground must not be overworked or compacted, and cover crops can be used to build healthy soil.” The first year after planting, vine care was critical to ensure strong growth and avoid stress that could lead to failure or poor performance. “A strong start often carries through to a strong finish,” says Stuart.
David urges people replanting vineyards to start planning early to avoid time pressures later on. “Work backwards from forecast planting dates, contact key contractors and order vines, posts, wire and dripline early.
“There’s a domino effect… if the ripping isn’t done then often cultivation can’t be done, irrigation can’t be done, and everything slides. It’s a big game of Tetris with one piece connected to the next. The planting contractor is the key guy that the whole vortex of the redevelopment world revolves around.”
Even a week’s delay in surveying could bump planting contractors who might then drop a job to the end of their list. If this pushes the start out as late as November, the project might have to be paused until conditions were suitable the following year.
Stages could be leapfrogged if necessary, or alternative approaches taken such as hand-planting with an augur if machinery was not available, or driving a minimum number of posts and completing the job the following season.
“Communication is everything,” David says, suggesting that contractors are taken to the site well ahead of development to get quotes, check they are accurate and identify any obstacles such as stony ground that would hamper pole-driving. Contractors should then be sent monthly reports increasing to fortnightly then weekly, as everything comes together.
David also recommends looking over the fence to see what redevelopment jobs could be shared with other growers in the area. “Scale is king… a contractor doesn’t want to travel from the Awatere to the upper Wairau for 2ha but will for 20ha.”
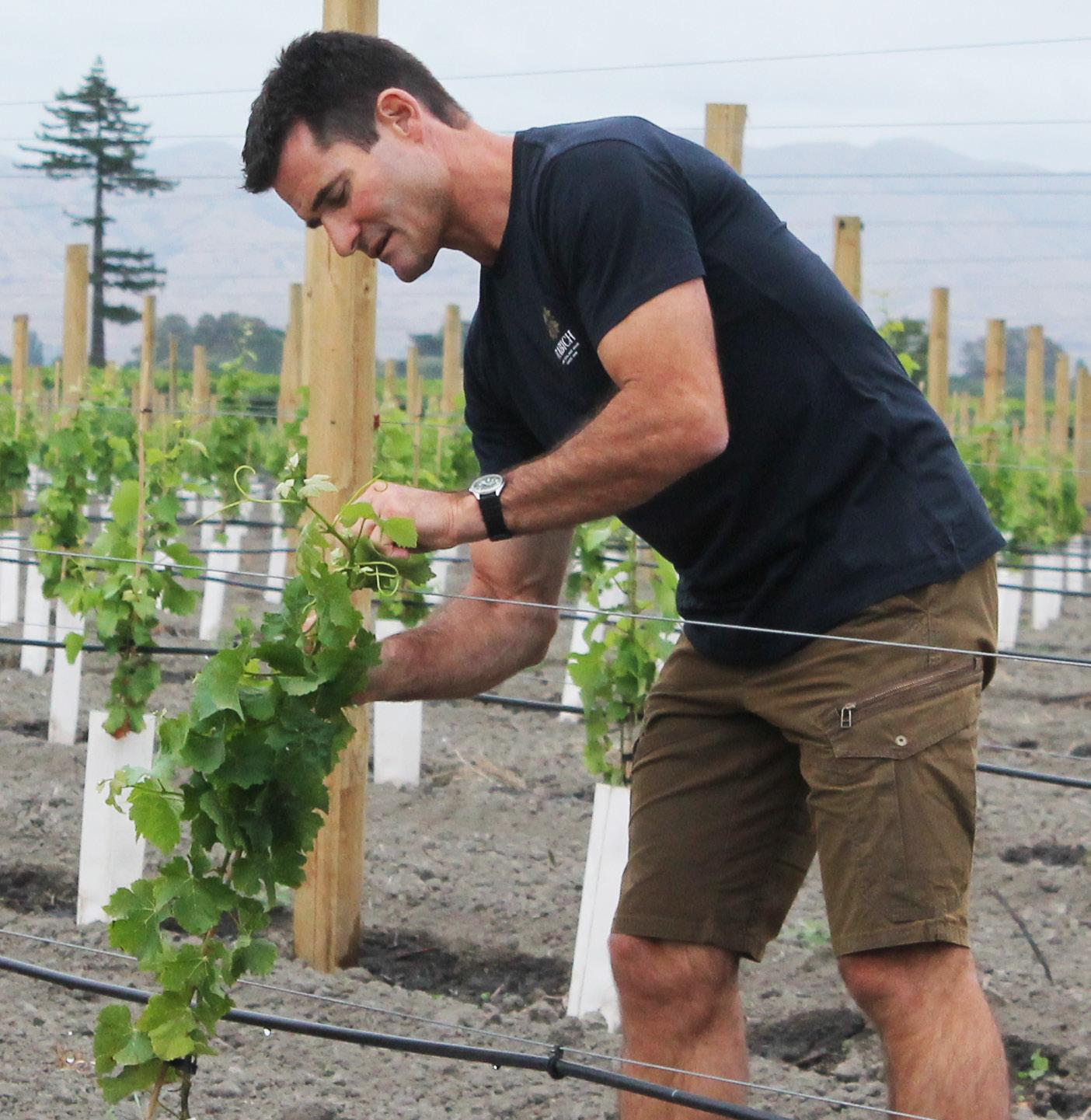
“[Vineyard redevelopment] is a big game of Tetris with one piece connected to the next. The planting contractor is the key guy.” David Bullivant