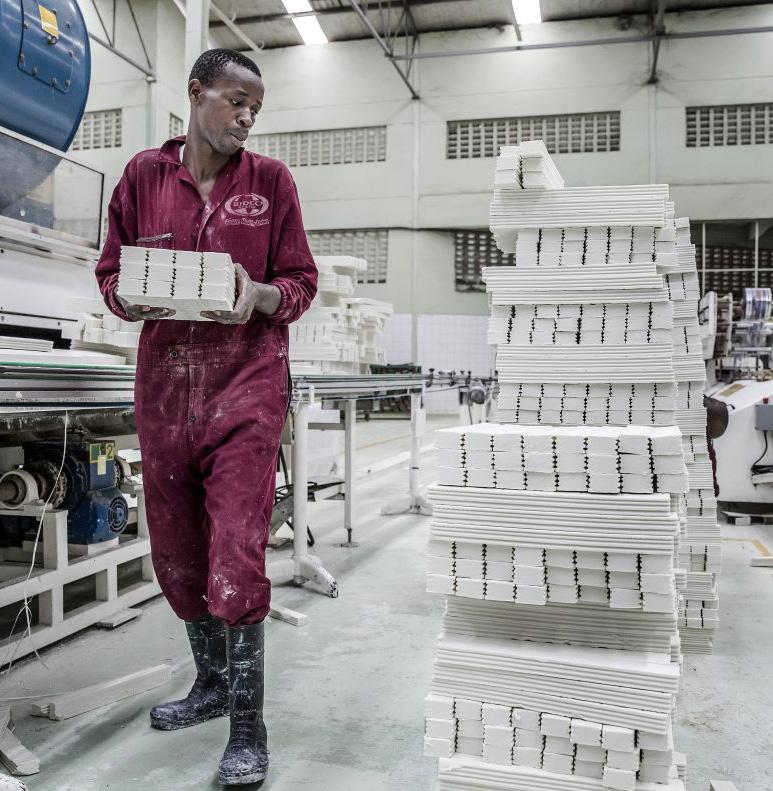
2 minute read
A 406KW CHP SOLUTION AT A SOAP PLANT, SOUTH AFRICA
SustainPower designs and supplies clean energy solutions for domestic & industrial markets. For industry, the company offers biogas, natural gas, & other gas-to-power solutions for continuous, prime, or emergency standby power supply.
With a special focus on energy efficiency, SustainPower’s systems save clients money through power outage protection, peak shaving, & waste heat recovery, displacing environmentally harmful sources of energy such as coal and diesel.
In the domestic and light commercial space SustainPower offer solutions in the form of gas genset and battery technology, providing a clean & quiet back-up alternative to the traditional petrol and diesel options.
One of its clients is a well-known South African detergent manufacturer with international standards of excellence. With a capacity of 8,000 tons per month, and state-of-the-art packaging facilities, this industry leader in environmentally sustainable operations continuously strives to improve the highest level of environmental values. The company even asked Solar Africa Energy to install and operate a Solar PV system in 2022.
SustainPower was keen to reduce the overall carbon footprint of the client’s plant, while providing the company with additional savings on electricity and heat costs.
SustainPower was tasked with building a 406 kW/507 kVA gas-topower unit and to integrate it with the existing solar PV system on the client’s roof.
The client reported a continuous electrical load of approximately 480 kW and a current thermal requirement of 2.3 t/h of hot water, at temperatures varying between 40 and 60°C, depending on the product being made.
Condensate from steam is combined with make-up water from the municipality and is kept at 50°C inside the boiler room hot well. A secondary hot well of 4000 litres is kept at 40°C inside the plant for production processes.
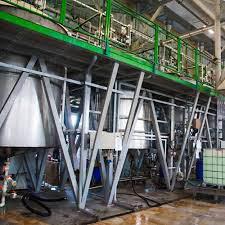
The controller of the new system gives preference to the solar energy due to the driving factor being energy savings. The hybrid controller allows both the CHP unit and the PV system to run.
The power shortfall between them comes from grid power which becomes a top-up when the PV and the generator cannot meet the entire site power requirements.

The CHP system generates 272.9 kW of heat from the water jacket - the client only needs 30% of this for the current facilities, while the remaining 70% of the water jacket heat will be supplied for the plant’s future expansion.
An ultrasonic sensor and a temperature sensor will be installed at the hot well to detect and monitor the water level and provide make-up water from the CHP and ensure that the water inside the boiler room’s well remains at 80°C.
For additional savings, 273.2 kW of heat from exhaust gas will be introduced to the client’s spray dryer.
A temperature sensor controlled by a hybrid controller allows the SCADA system to detect whether exhaust gas is too hot for the product being dried, and a stream of fresh air will be introduced to cool the exhaust before it reaches the product inside the spray dryer.
The hybrid controller ensures the smooth harmonious syncing of the individual hybrid components. The controls will regulate the engine running parameters to ensure that KT Wash receives the desired hot air required for their processes.
Future value to the client from this CHP system includes electricity savings, heat savings, gas usage savings, overall carbon footprint reduction. The client will definitely benefit from the implementation of a sustainable strategic energy management plan, says the company. sustainpower.com