
4 minute read
CHP and key cost reductions at the £140m Kraft Heinz factory in Wigan
The Kraft Heinz Company site at Kitt Green, Wigan, is a vast food canning plant. It processes 1.34 billion cans of food every year, including the well-known Kraft Heinz Company 57 products such as baked beans. The site processes food on a 24 hour, 6-day shift throughout the year. To maintain production processes, Kraft Heinz Company required up to 99 tonnes of steam per hour. Ind addition management wanted to improve environmental performance, reduce fuel consumption and sustain this steam supply, The company also needed a new energy centre, capable of generating large volumes of steam.
A key driver was optimising the use of technology which is why the Kraft Heinz Company turned to UK-based Veolia.
Advertisement
Veolia has a reputation as an energy specialist who examines businesses in precise detail to ensure a guaranteed supply of sustainable, efficient energy is delivered with budget certainty.


Veolia designed, built, operates and maintains a new 100 MWth steam generation facility for Heinz, the largest and most efficient of its type serving European industry. It currently generates 140 tonnes of steam per hour and incorporates four of the largest shell boilers in the UK, each capable of generating 35 tonnes of steam per hour. Today the £5.3 million facility is able to save up to £1 million per year using CHP and other energy-saving processes.
The Kraft Heinz site garners energy saving costs of up to £500,000 per year and achieves 8% lower CO2 emissions, with 14% less gas used.
The latest software and computer control systems enable the facility to operate unmanned, with 24hour monitoring by Veolia’s Site Monitoring Centre, supported by mobile engineers.
A spokesman commented: “Veolia guarantees the steam supply, maintaining it 24/7 at the required pressure and temperature to support year round production. Veolia’s Replacement Guarantee Scheme also ensures that there are no unbudgeted steam plant replacement costs during the contract.”
The Kraft Heinz Company has signed a Memorandum of Understanding with HyNet, a leading decarbonization project in the U.K., to supply low carbon hydrogen to fuel its Kitt Green facility. Kitt Green is one of Europe’s largest food processing facilities, producing more than 1 billion cans of food per year. The site is pledged to procure the majority of its electricity from renewable sources by 2025. Switching to low carbon hydrogen is a critical piece of the Net Zero puzzle and will enable a switch away from fossil fuels starting in 2025. From 2025, HyNet and North Wales will produce, store and distribute low carbon hydrogen, as well as capture and safely store carbon dioxide (CO2).
Long- Term Renewable Energy Sale and Purchase Agreement
Kraft Heinz has entered into a multi-year virtual power purchase agreement (VPPA) with Repsol. The VPPA, entered into in 2021, is linked to one of the Delta II wind farms, Repsol’s largest renewable project to date, which is already under development and, once completed, will have a total capacity of 860 MW distributed among 26 wind farms located in Aragon, Spain.
This wind farm is expected to start operations in early 2025. Once completed, Kraft Heinz is expected to source the equivalent of approximately 90% of its European manufacturing sites electricity needs through this renewable energy agreement. The VPPA is expected to generate enough renewable electricity to power approximately 25,000 average EU households per year at its peak.
A spokesperson for Kraft Heinz comments:
“In 2021 we announced our pledge to achieve net zero greenhouse gas (GHG) emissions across our operational footprint (Scope 1 and Scope 2) and entire global value chain (Scope 3) by 2050. We also established our major commitment to contribute to global efforts to reduce the ongoing threat of climate change.
“As a milestone on our path to achieve net zero emissions, we will target a near-term emissions reduction of 50 %by 2030 across all three scopes. We anticipate submitting and receiving approval of our quantitative goals from the Science Based Targets Initiative over the next year.”
CHP reduces energy costs and improves sustainability for the Alton Towers Resort
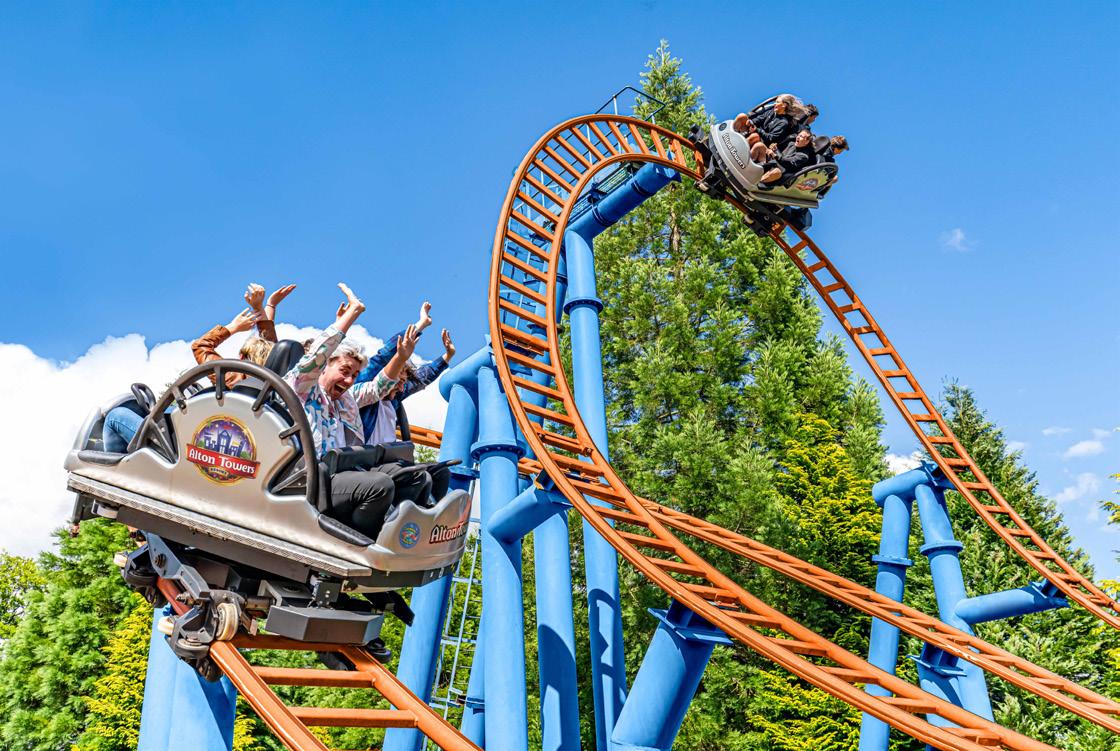
Alton Towers Resort is more than a theme park. The 550-acre site now includes four hotels, a conference centre and Europe’s largest waterpark.
The hotels can accommodate 2,500 guests, with 400 staff on site. This presents a sizeable energy challenge. The facilities team must ensure there is power in every room, the waterpark needs to heat 1,000m³ of water and pump 66m³ of air/second. Plus, the rural North Staffordshire location means the buildings retain little latent heat. With the resort generating a stable demand for energy, Warren Critchley, Head of facilities at Alton Towers Resort began to investigate combined heat & power (CHP) options:
“It became clear CHP would be the perfect model for energy reduction, energy savings, utility cost reduction and carbon reduction.”
Centrica Business Solutions provided a consolidated package, acting as manufacturer, installer and service provider. A CHP unit was installed on site, alongside the waterpark, generating up to 850kWh. If there are any issues with the CHP, Centrica support ensures they are dealt with quickly.
Today the Centrica CHP unit generates energy savings of 12% per annum. Because the unit generates power at source, literally alongside the waterpark, conference centre and largest hotel, there is very little transmission loss. Critchley estimates an energy efficiency of 80%.
“Long term, we have the capacity to accommodate further demand,” says Critchley, “and we’ve protected our future energy costs.”
New biomass CHP set to power Scottish distillery
John Laing and the UK Green Investment Bank (GIB) are to invest in a new £74m green energy facility in Speyside, Scotland developed by Estover Energy Ltd.
The new biomass combined heat and power (CHP) plant near Craigellachie, Moray, will generate 87.4GWh per annum of renewable electricity – enough to power more than 20,000 homes. It will also generate 76.8GWh per annum of renewable heat.
The new CHP facility will contribute to reducing the cost of energy at The Macallan distillery by providing around 90% of all of the steam needed in the distillation process. By using biomass instead of natural gas to generate heat, the distillery will reduce its greenhouse gas emissions by over 17,500 tCO2e. John Laing and GIB intend to make a £26m equity investment in the project. The remainder of the funding, in the form of debt, will come from a bond to be issued by the project company and listed on the London Stock Exchange.
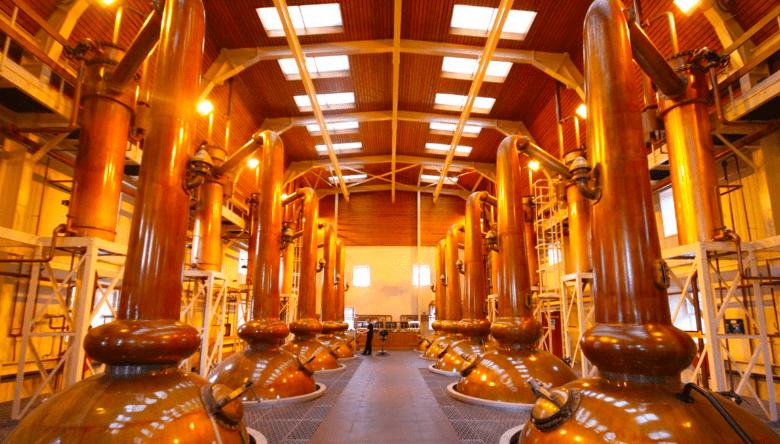
State-of-the-art components providing more power: the compact design, a focus on a wide range of applications and high efficiency values make sure of that. Controlled by the smart and secure TPEM (Total Plant & Energy Management), the new TCG 3020 series offers highest profitability and reliability. www.mwm.net/gas-engine-TCG-3020
Discover the new models
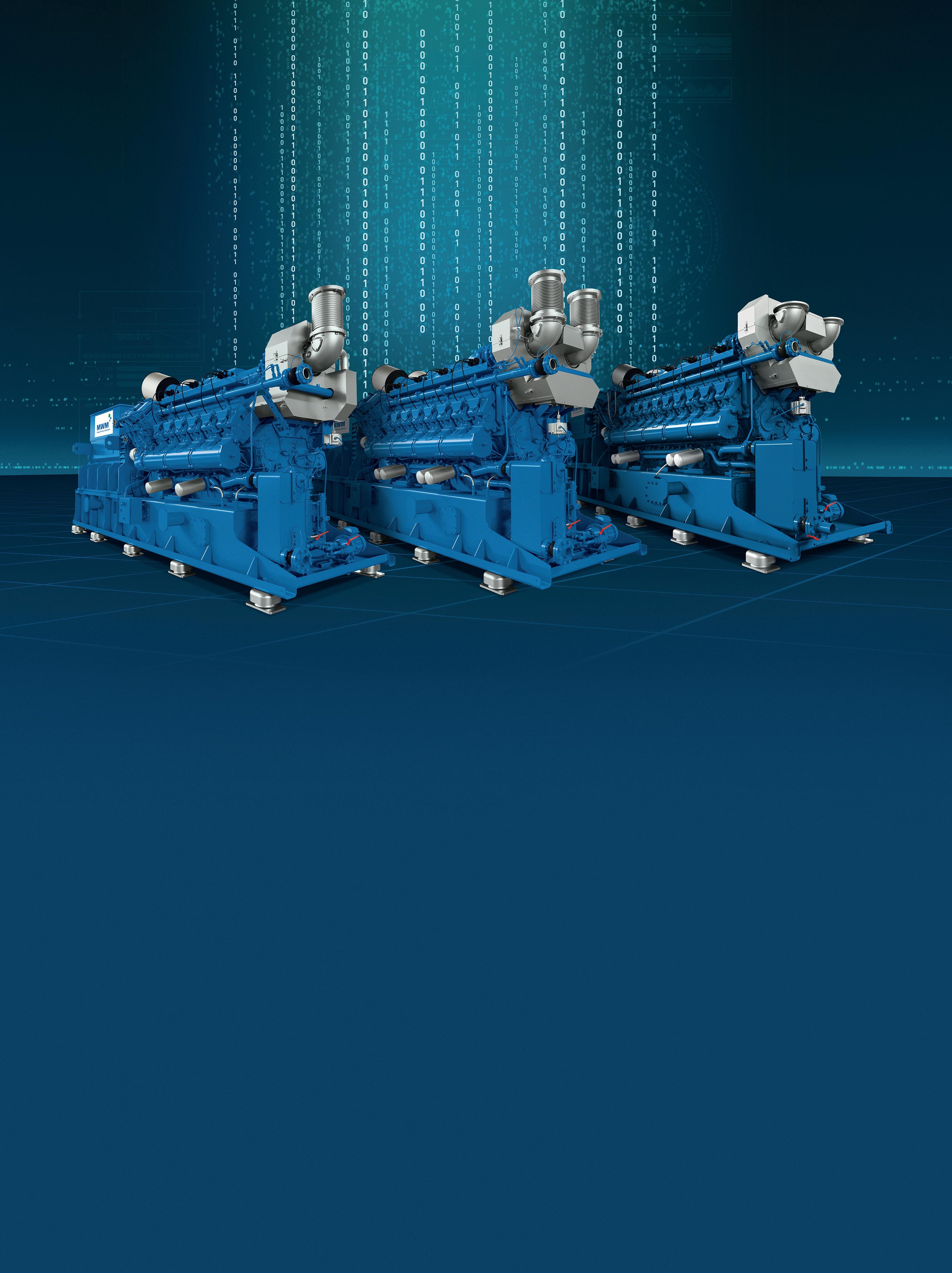