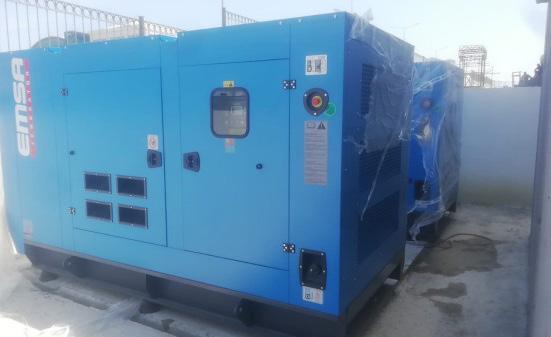
44 minute read
GENSETS IN TURKEY
825 KVA GENERATOR SET SUPPLIED TO VIAPORT MARINA’S ENERGY INFRASTRUCTURE
The ViaPort Marina located in Tuzla, Istanbul features a shopping mall and a port which now relies on an 825kVA set from EMSA Jenerators to complete its energy infrastructure. ViaPort Marina officials specified the set to provide uninterrupted power in case of any power cuts involving the grid. ViaPort Marina purchased a 6M33G825/5 model BAUDOUIN engine with an EGK355-600N model Emsa alternator designed for a 825 kVA diesel generator set - this was rapidly manufactured and delivered, says the company. “Using the generator as an auxiliary power source with the standby mode when there is grid energy infrastructure is extremely important for locations such as ViaPort Marina,” a company spokesman reports. Thanks to a sound insulated external container for the genset both the marina and shopping mall visitors will neither see nor hear the generator.
Advertisement
The 6M33G825/5 model BAUDOUIN engine has 6 / 24 cylinders/valves and a 19.6-litre displacement. A diesel 4 stroke engine with a liquid (water + 50% antifreeze) cooling system and turbocharged and aftercooled aspiration. Engine dry weight 2370kg. Engine wet weight (includes oil, coolant, 2525kg Baudouin variable speed engines draw their robustness, durability and easy maintenance from Baudouin’s marine heritage. They have been perfected for a diverse range of industrial applications such as agriculture, motor pump sets, firefighting, dredging pumps, and with their high tolerance to fuel quality are ideal for use in even the most remote areas around the world. The generators made by EMSA include automatic commissioning in case of a power cut. These means that the businesses at the Viaport Marina can get fast and uninterrupted electricity without any delay and work can continue without any interruptions. ViaPort Marina is using the generator as an auxiliary power source in standby mode when the grid energy infrastructure is stable; this is extremely important for locations such as these. As the name suggests, ViaPort Marina is not just a shopping mall and entertaining location but also a busy marina for vessels. A location which blends both a marina and shopping mall culture needs energy 24/7. The EMSA generator is able to fully undertake its task and is ready to offer support for any other needs, says the manuifacturer.
Akarteks, one of Turkey’s ket textile manufacturers has also chosen EMSA generators to prevent any problems due to energy loss. A company spokesman commented: “A generator is an important element for Akarteks with 5 million textile items manufactured per year. The company selected EMSA,to provide gensets for its manufacturing facilities. “Akarteks will minimise the energy loss level in its key manufacturing facilities and will continue to manufacture without downtime loss.” Akarteks t has been a key manufacturer in Turkey for more than 30 years. It operates four facilities with a total area of 31,000 sqm. Akarteks specified a BF6M1015CP-LAGG3A model Deutz engine, a EGK315-320N model Emsa alternator and 440 kVA diesel generator sets manufactured by EMSA to eliminate potential power cuts. The manufacturing process will be uninterrupted as the EMSA generators can start in a very short time should an outage occur The EMSA spokesman comments: “We have provided the most suitable model and generator set for Akarteks’ manufacturing facilities. Our generators will support manufacturing and decrease time loss with remote intervention, noise insulation and water-cooling properties. “In addition, the generator will also be used as auxiliary power source when there is grid energy infrastructure with standby power mode. Our generator will also issue a warning in case of low fuel levels and provide swift and timely intervention.” For its facility in Söğütlü Organized Industrial Zone in Sakarya, Turkey, a manufacturer of designer products also turned to EMSA for a genset. A major producer and supplier of fashion and wedding dress accessories, MK MODA ATELIER recently purchased a BF6M1015C-LA-G3A model Deutz engine EGK315-320N (model Emsa alternator) 440 kVA diesel generator set. The set has been designed to go into action automatically when the factory needs energy. EMSA generators are emploiyed on six continents and 102 countries. With more than 40 years of experience EMSA continues to fulfil an important role by acting as a bridge between energy and societies.

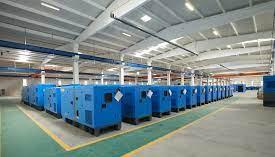
www.emsa.gen.tr

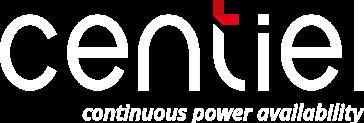
UPS Service and Maintenance

•24/7/365 Technical Support •Comprehensive Maintenance Packages •Nationwide Emergency Cover •Fan, Capacitor and Battery Replacements •Impedance Testing
www.centiel.co.uk
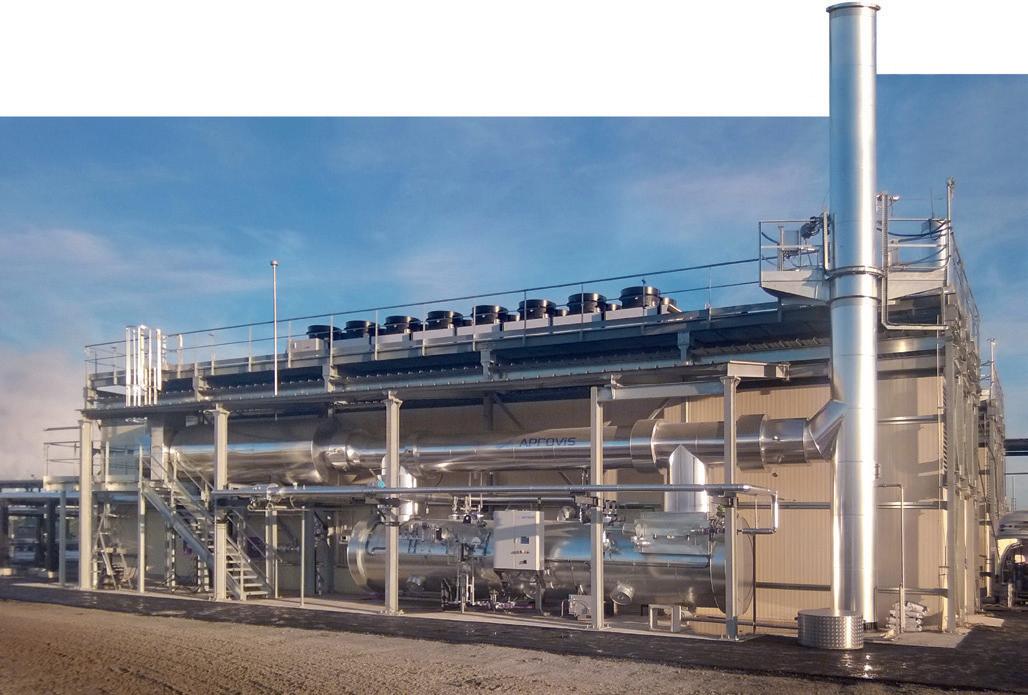
As UK manufacturers of the PEREGRINE and FALCON range of engine pre-heater solutions, we keep engines running in critical industry sectors
Diesel Fuel and In-Line Heaters Hydraulic Oil Heaters Storage Tank Heaters Custom Heaters
High Quality - Durable - Reliable PEREGRINE| Heat At The Heart Of Your Engine
Fire Safety Marine


Generators Fuel Storage
A 3.0MW BIOGAS-FUELLED POWER PLANT FOR A STARCH FACTORY IN UDONTHANI, THAILAND
Inio has supplied a 3MW gas generator consisting of two Jenbacher 420 gas engines. Souer has successfully commissioned the 3.0MW biogas-fuelled power plant which now relies on two Jenbacher 420 gas engines in Udonthani for the starch factory at times of on-off peak demand. Starch production involves the isolation of starch from plant sources. It takes place in starch manufacturing plants. The starch industry is a part of modern food processing perations which depend on using starch as a starting material for production of starch derivatives, hydrolysates, dextrins. Currently main starch sources are maize, rice, wheat, potatoes and sorghum. Applications of starch in non-food sectors include: production of dextrin and adhesives, drilling fluids, biodegradable plastics, gypsum binders and many other. In addition modified starches are used as emulsion stabilizers. Other important fields of starch application are textile sizing agents, excipient in tablets for pharmaceuticals. Based on proven Jenbacher Type 3 and Type 6 engine designs, the Series 4 gas engines are characterised by high power and efficiency. Advanced control and monitoring systems ensure easy maintenance as well as reliability and availability. Combining superb efficiency with an innovative engine concept, Type 4 units save fuel but don’t sacrifice flexibility or reliability. Type 4 is available in 50 and 60 Hz and has the flexibility to choose the gaseous fuel. This makes it an excellent option for more than ten different applications. There are more than two thousand Type 4 systems currently in use around the world, a fact which reflects well on their reliability and high availability. Reduced bearing wear adds to the longevity of the unit. Based on the proven design concepts of Type-3 and Type-6, the modern Type-4 engines in the 8001,500kWe power range are characterised by a high power density and outstanding efficiency. The optimised control and monitoring provides easy preventative maintenance and maximum reliability and availability. Type-4 engine benefits include the highest electrical efficiency in its power class, maximum levels reliability & availability. The engine has been optimised for ease of service. The Type-4 engine has features such as a
LEANOX® lean burn control to ensure minimal emissions. A high-power turbocharger allows optimal operation at higher air intake temperature and altitude. Low NOx emissions versions available for biogas, achieved without the requirement for an exhaust catalyst. At the Udonthani starch factory biogas is being used to fuel two Jenbacher 420 gas engines to provide renewable power using the biogas cogeneration systems. In this case, biogas is formed by the anaerobic decomposition of putrescible organic material from the starch process. Biogas can either be used to generate electricity and heat via a combined heat and power gas engine, or can be cleaned to produce pure biomethane via biogas upgrading. Clarke Energy is one distributor of Jenbacher gas engines designed for robust operation on difficult gases such as biogas, landfill gas or sewage gas. Clarke Energy is also a distributor for TPI’s biogas upgrading plants. Biogas derived from starch products is classed as a renewable fuel as it originates from organic material that has been created from atmospheric carbon by plants grown within recent growing seasons and is part of the short-term carbon cycle. Jenbacher biogas engines are specifically designed to operate on different types of biogas. These gas engines are linked to an alternator in order to produce electricity at high efficiency. High efficiency electricity production enables the end user to maximise the electrical output from the biogas and hence optimise the economic performance of the anaerobic digestion plant. Using biogas from the fermentation of organic waste, INNIO’s reciprocating engines can create heat and power as a reliable energy source to power businesses today, tomorrow, and in the future. Jenbacher biogas generator sets are widely used by farmers and i ndustrial users across the globe. Onsite biogas power plants can be used by businesses to supply their own electricity and heat needs (biogas cogeneration/CHP), or biogas gensets can produce electricity for future off-take to the grid. Biologically-derived gases can be utilised in biogas engines to generate renewable power via cogeneration in the form of electricity and heat. The electricity can be used to power the surrounding equipment or exported to the national grid. Low grade heat from the cooling circuits of the gas engine, typically available as hot water on a 70/90°C flow/return basis. High temperature exhaust gas heat can either be used directly into a drier or waste heat boiler . Alternatively, it can be converted into hot water using a shell and tube exhaust gas heat exchanger to supplement the heat from the engine cooling systems. Waste heat boilers produce steam typically at 8-15bar. Driers may be useful to reduce the moisture content of the digestate to assist in reducing transportation costs. In the event that the local legislation requires for the destruction of pathogens in the digestate (such as the European Animal By-Products Regulations) there may be the requirement to heat treat the waste via pasteurisation or sterilisation. pasteurisation unit. www.innio.com
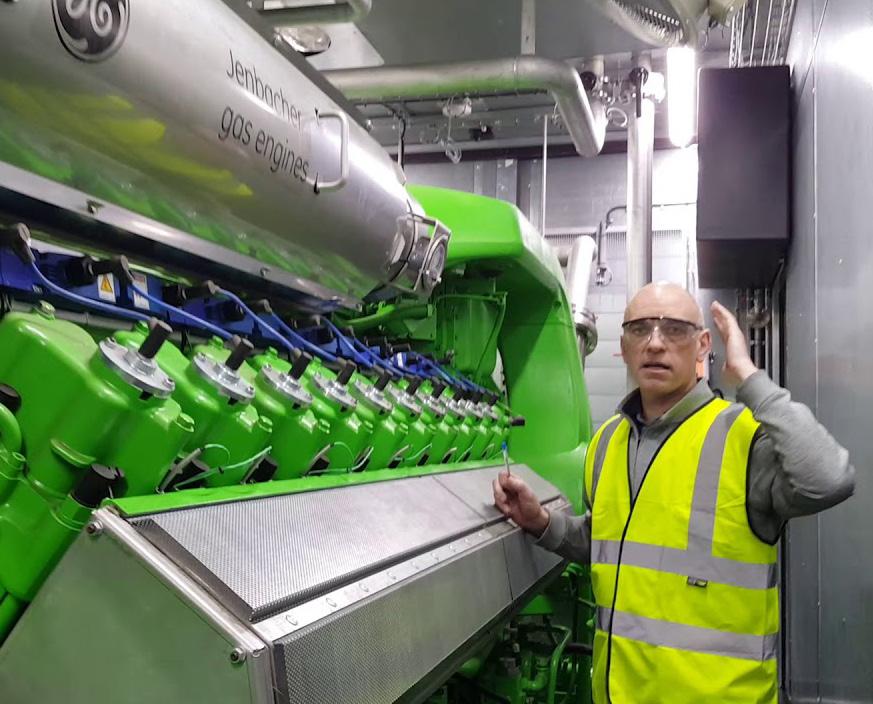

GENSETS FOR MEDICAL CARE: 500 KW GENSET FOR NURSING CENTRE IN SOUTH CAROLINA, USA
Anew 500kW genset has been supplied by Blue Star Power Systems, Inc. to a Nursing Centre in Darlington, South Carolina. This unit will replace the smaller Katolight set which was previously supplying power to critical life support circuits - the new set will now power the entire facility in the event of an outage. The new unit will be connected to the building using ASCO switchgear. The company’s new Blue Star PS Generators come equipped with level 2 sound attenuated and weatherproof enclosures. The VD500’s come fully protected by a 2 year warranty. Model: VD500, Engine: Volvo Penta TAD1641GE-B, Control Panel: DGC-2020, the Fuel Tank offers 24-hour runtime. Blue Star Power Systems, Inc’s Digital Gen-Set Controller (DGC-2020) is described as a highly advanced integrated genset control system. The DGC-2020 icombines rugged construction and microprocessor technology to offer a product which will hold up to almost any environment and flexible enough to meet a client or application’s needs, reports Blue Star Power Systems. This device provides gen-set control, transfer switch control, metering, protection and programmable logic in a simple, easy to use, reliable, rugged, and cost effective package, reports Blue Star Power Systems. The unit is UL Recognized and CSA & CE approved, is microprocessor based and comes with a complete system metering, remote communication options and has a rugged encapsulated construction. The DGC-2020 can provide long distance communication by adding a modem. When a modem is used, the user can access the DGC-2020 from virtually anywhere via a dedicated telephone line. The user can monitor and control the genset as if standing right in front of it. The DGC-2020 can also dial out for pre-programmed circumstances to alert the user of selected situations. When the RS-485 option is selected, the user can send and receive information from the DGC-2020 via the RS485 communications port and A Modbus protocol feature allows the DGC-2020 to be fully integrated into the building management system. In addition to the standard generator protection (27, 59, 81O, 81U) the DGC-2020 can be equipped with a more sophisticated generator protection system. This option provides an overcurrent element (51) with 17 selectable time current characteristic curves and a voltage phase balance protection function. The DGC-2020 monitors utility (mains) and determines if it is providing power that is suitable for the loads. If the utility supply goes outside of predetermined levels, the generator is started and the utility is disconnected from the load and the generator is connected. When the utility returns to acceptable levels for a sufficient time, the generator is disconnected and the utility is reconnected to the load. It also includes appropriate adjustable timers or time delays for establishing stable utility operation. A CEM add-on module increases the contact input and contact output capability adding 10 contact inputs and 24 form C contact outputs. This module communicates to the DGC-2020 via SAE J1939 CANBUS and allows the user to program the functionality of these inputs and outputs in the BESTCOMS programmable logic program. The user can add labels for the inputs and outputs that appear on BESTCOMS front panel, and in the programmable logic. All the functionality can be assigned to these inputs and outputs as if they were an integrated part of the DGC-2020. The CEM-2020 module has all of the environmental ratings, like the DGC-2020, including a model for UL Class1 Div2 applications. The output ratings of the form C contacts are: (12 contacts) 10A @ 30VDC and (12 contacts) 2A @ 30VDC. The 2A rated contacts are gold flash contacts for low current circuits. The CEM-2020 terminals accept a maximum wire size of 12 AWG while the chassis ground requires 12 AWG wire. The CEM-2020 provides the user with the flexibility to use the same model DGC-2020 gen-set controller for simple applications or more complicated applications that require contact functionality or duplication of contacts for remote annunciation. Flexibility is one of the benefits of the DGC-2020, and this add-on module enhances that benefit even further, says the manufacturer. A NetBiter® RTU-TCP Gateway feature connects the fully enhanced DGC-2020 with Ethernet and mobile networks. The gateway acts as a transparent bridge translating DGC2020 Modbus registers allowing control systems, such as PLCs, SCADA, etc. to communicate over Ethernet. One gateway is required per generator allowing multiple generator sets to be accessed and monitored simultaneously. Features include: connectivity between serial Modbus devices and the Modbus TCP; RS-232, RS-485 and RS-422 connectivity; Ethernet and mobile network connectivity; 10/100 Mbit/s Ethernet; web-based configuration; DIN rail mounting; and network and serial status indicators.
bluestarps.com
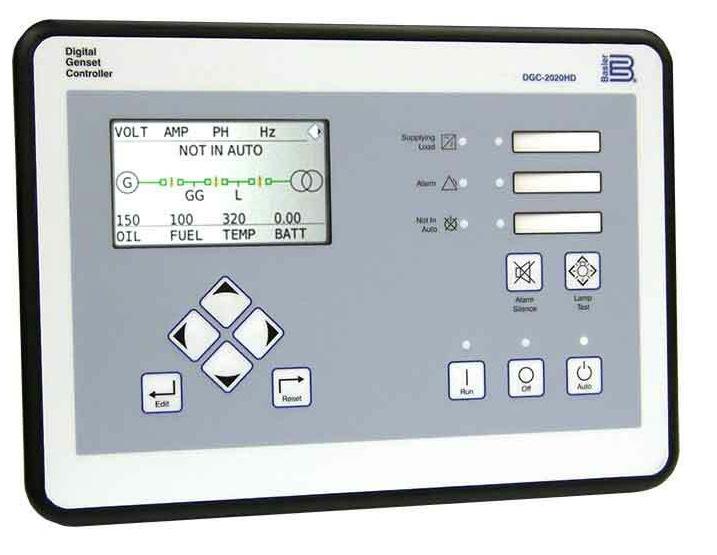

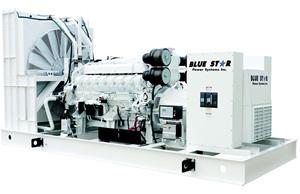
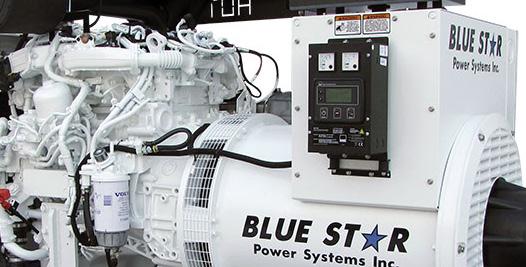

Margen has delivered two 2MW diesel gensets for the Punta Catalina Thermoelectric Power Station in the Dominican Republic. The 752MW Punta Catalina is a coal-fired thermoelectric power plant with two power-generating units located in the Valdesia region of the Peravia province in the Southwest sector of the Dominican
Republic. It is owned by Dominican Corporation of State
Electric Companies (CDEEE) and Patrimonial Fund of
Reformed Companies (Fonper). Punta Catalina is the country’s biggest power-generating facility. It is operated by Central Termoelectrica
Punta Catalina, a commercial company, co-owned by the state-run Dominican Corporation of State Electric
Companies (CDEEE) with 99.2% interest and Patrimonial Fund of Reformed Companies (Fonper) with 0.8% interest. The plant was constructed by the Odebrecht-Tecnimont-Estrella consortium, and the rights to the power plant were transferred to the CDEEE and Fonper in
December 2019. The project involved an estimated investment of approximately $2.45bn. The first unit of the power plant became operational in October 2019, while the second unit completed final test stages in April 2020 and is generating 376MW. The inauguration ceremony of the power plant was postponed due to the Covod-19 pandemic. A total of $600m was issued in sovereign bonds and financing resources from European banks (SACE) to ensure the development of the project in 2016. The plant can meet up to 35% of the total power demand of the Dominican Republic. The project created more than 6,400 direct jobs and 20,000 indirect jobs during the peak period of its construction. Punta Catalina is an advanced power plant, based on clean-fuel technology. It comprises two pulverised mineral coal-fired units with 376MW capacity each, delivering a total combined capacity of 752MW. The nominal efficiency of the plant is 39.2% LHV. Each unit of the plant features a 360MW pulverised coal boiler with an air quality control system, coal pulverisers, air heaters, fans, steam turbine generator, process control, as well as monitoring systems. The units are also equipped with the Plant Balance equipment needed for the plant’s operation. Additionally, the project includes the country’s longest coal handling port terminal with a length of 1,600m, a completely closed building with 200,000t of coal storage capacity, and other associated infrastructure. The coal used as fuel is currently transported through closed transportation systems without the need for human intervention. A spokesman for MARGEN, basedin Marinello, Italy, commented: “We have just completed the overhaul of the plant at the Punta Catalina Thermoelectric Power Station in Santo Domingo. We have provided two generators of 2 MW each, featuring the dummyload system: a load bank has allowed the efficient operation of the station serving the emergency startup of the power station’s turbine.” Two 2MW diesel generators are key to maintaining the ongoing power supplies at the Punta Catalina thermoelectric power station. Most electricity generation in the Dominican Republic comes from thermal sources. Only 14% of the i nstalled capacity is hydroelectric, with this percentage falling to below 9% when all the thermal self-generation is accounted for. The exploitation of other renewable resources (i.e. solar, wind, tidal) is very limited.
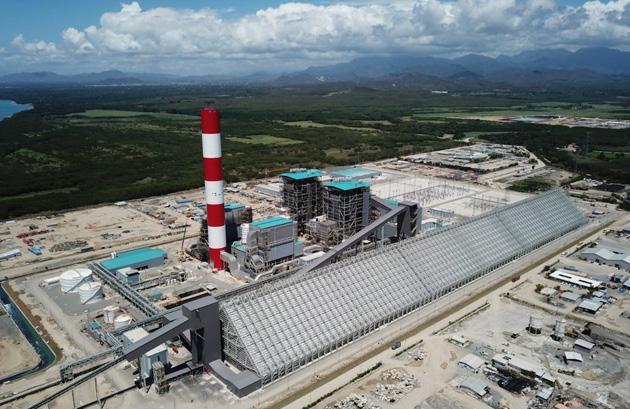
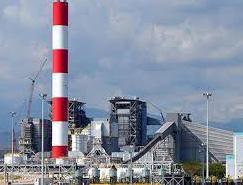
National capacity
The Dominican Republic has a total installed capacity of 3,635 MW with peak demand of 1,800 MW.8 Renewable energy generation in the Dominican Republic only makes up 14% of total electricity (nearly all of which is provided by hydroelectric facilities), while the remaining 85% of electricity is generated from imported fossil fuels. Despite recent growth in the country’s generating capacity, 18.4% of its demandhave gone unmet.. Due to grid unreliability, many industries and private individuals generate their own electricity using inefficient small-scale fossil fuel-based units. The Dominican Republic also had high transmission and distribution losses of more than 30% - in some years - which have been attributed mostly to electricity theft, blackouts, inadequate investment in capacity upgrades, and limited regulatory capacity.
HEAT RECOVERY TECHNOLOGY SUCCESS IN THE COLD OF THE CANADIAN ARCTIC
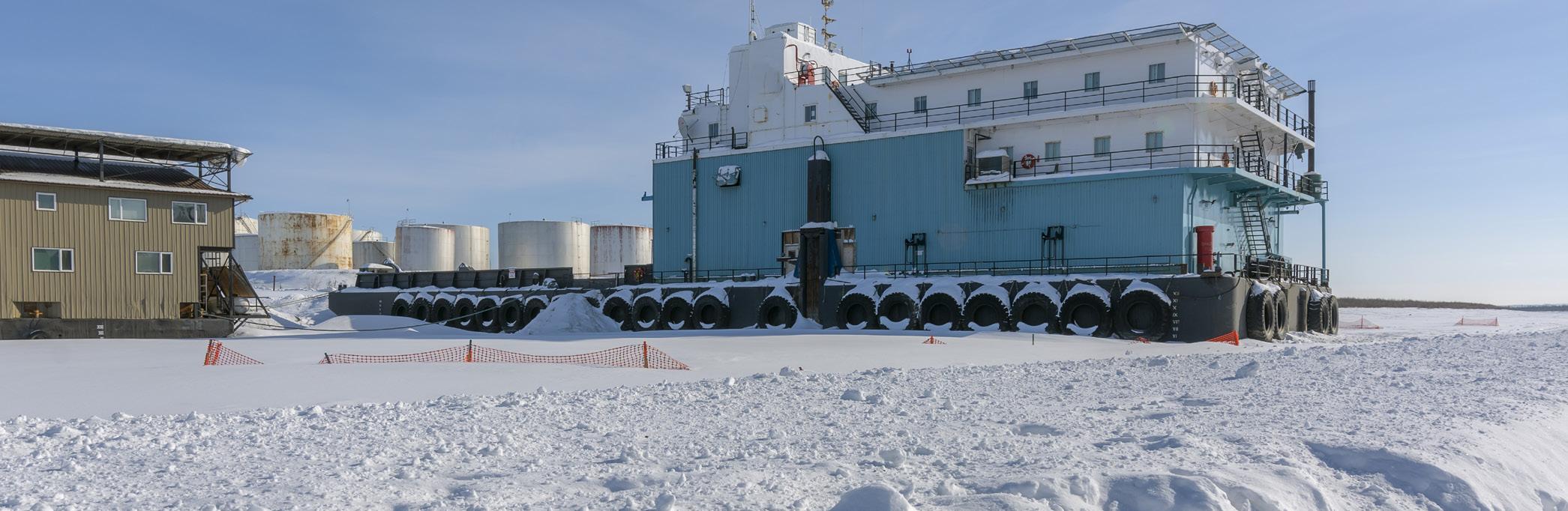
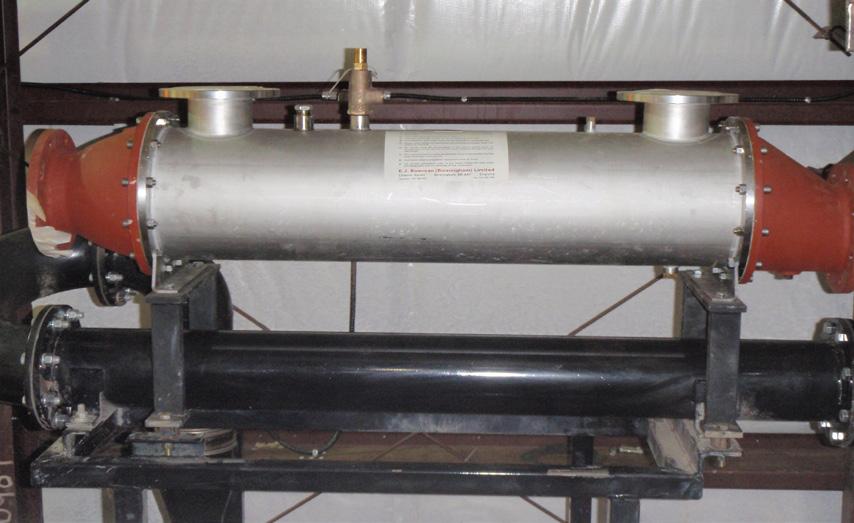
As Summer turns in to Autumn and before the great Mackenzie River freezes over, several large barges are transported along the river’s icy waters. Once secured in position, they form an oil and gas exploration camp which operates from October through to June each year and has done so for the past 12 years. With the approach of Winter, temperatures fall dramatically so that the barges are frozen fast into the ice-covered river. Due to its remote location, for the next six months the only way in or out of the camp is by helicopter, or ice roads constructed on top of the frozen river. The barge facility is now home and base camp for Horizon Marine’s 88-person crew, who will work throughout the winter months in one of the most remote oil and gas exploration facilities on earth. With seasonal temperatures ranging from -17°C to -40°C, the working days are long, extremely cold and very dark in this North Canadian Winter wilderness. Supporting life in these freezer like conditions is the ‘Arctic Star’; the base camp barge where the crew retreat for warmth and light during those dark winter days and nights. Heat and power are valuable, vital resources, without which, the crew would surely perish in this hostile environment. To ensure there is adequate provision of both, Frontier Power Products were commissioned by Horizon to design and build a Combined Heat and Power (CHP) system to replace the previous two independent 400 kW gen-sets, which had no heat recovery system. The solution proposed by Frontier used three 150 kW (270hp) John Deere generating sets, arranged to operate in parallel, with automatic controls enabling the units to start up and shut down individually, to cater for the varying electrical demands of the camp. A heat recovery system was also required for the gen-sets engines and here, Frontier relied on Bowman’s technical expertise to provide the correct specification heat exchangers to harvest heat energy from the engines cooling and exhaust systems. Bowman proposed a solution comprising three shell and tube heat exchangers to cool and recover heat from the engines jacket water, plus three exhaust gas heat exchangers to recover the high levels of waste heat generated from the engines exhaust stream. Heat that would normally be rejected from the cooling and exhaust systems is recovered by the Bowman units and then piped to and dispersed throughout the camp. The Bowman heat recovery solution has proved to be extremely reliable, as the original heat exchangers have now been in operation for around 25,000 hours, since installation 12 years ago. During that time, fuel costs for the ‘Artic Star’ have reduced by around 33%, thanks to the addition of the heat recovery system. Adding heat recovery to an engine powered genset is an effective way of recovering a cost-effective energy source that would otherwise go to waste, whilst increasing engine efficiency from around 30% (power only) to in excess of 80% (combined heat & power). Around 50% of all fuel input into the engine can be recovered as heat energy and Bowman manufactures a range of heat exchangers that can recover this from virtually every part of the engine, including the exhaust stream, jacket water cooling, turbo charged induction air, plus oil lubrication and fuel cooling. Recovered heat can be used for a wide range of domestic, commercial or industrial uses, including district heating, hot water, process heating, generating additional electricity, grain drying, fuel pre-heating, or running a chiller for comfort cooling. Excellent heat transfer efficiency, UK manufacture and high quality standards are just some of the reasons why Bowman are leaders in waste heat recovery solutions for gensets. As a leading UK-based manufacturer of shell and tube coolers which deliver highly-efficient cooling solutions for a wide range of applications, including compressors, pumps, engines, hydraulic power packs, plastic injection moulding machinery and much more. Bowman Heat Exchangers and Oil Coolers provide high quality, thermally-efficient heat transfer solutions for a variety of demanding applications worldwide. Bowman offers one of the widest product ranges available covering a multitude of water-cooled applications. Backed by 100 years of heat transfer experience, Bowman heat exchangers can today be found in some of the most extreme and demanding applications known.
ej-bowman.com
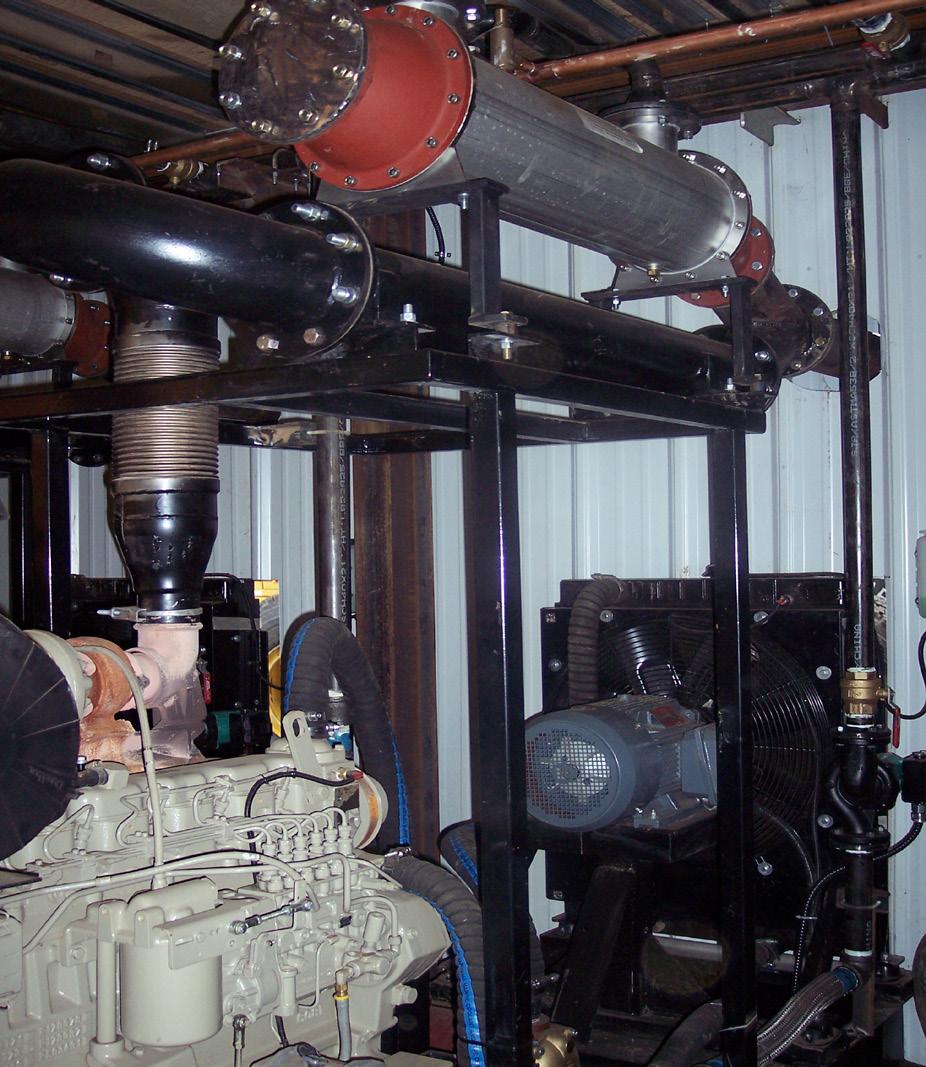
NEW CONTRACT: 1,100 KVA DIESEL GENSET INSTALLED AT MAJOR HOSPITAL IN THE UK
Genesal has provided a GEN1100CC diesel genset for a hospital in the UK’s northwest region. A company spokesman commented: “At Genesal Energy, we have just supplied emergency power to one of the main hospitals in the Northwest of the UK through the design, manufacture and supply of a 1100 kVA standby generator set ready to work in parallel with the mains.” NHS hospitals need a reliable source of power - the electrical demands of a hospital far outweigh those for most other building types. One reason is that hospitals have unique equipment with very large power requirements, such as magnetic resonance imaging (MRIs), computer tomography (CT) scanners, and other imaging equipment. Monitoring of patients, supplying lighting, heating and ventilation - all require a high quality energy supply in life-critical situations where people could be at risk, The generator designed by the Genesal Energy engineering team guarantees the continuous electricity supply and therefore, the uninterrupted operation of the hospital’s health services in the different areas. “Generator sets must be designed for a quick response – a few seconds – in the event of a mains failure or any other reason involving a power outage. “This is the case of the equipment we designed for this particular British hospital as its main goal is to ensure the electricity supply in all the medical care facilities. This includes operating rooms, hospitalisation plants and other health areas with the greatest precision.” The spokesman comments: “In addition, noise pollution has been reduced to the minimum levels considering the importance of peace and quiet for patients in this kind of buildings.” “Our extensive experience in developing on-demand solutions for hospitals, regardless of their size and/or location, is one of Genesal Energy’s highlights both in Spain and internationally, as well as the best guarantee of the quality of our equipment.” Genesal Energy’s R+D+I department stated: “There is a common denominator in hospitals: they treat convalescent people. This consequently implies a challenge for the company, as the safety and precision of Genesal’s equipment must reach their highest levels, especially in these buildings. “Our generator sets are designed under the premise that nothing can fail, and there cannot be any failures in the process. It is fundamental for every unit which leaves the factory to be utterly reliable so that energy is provided quickly and with the necessary power”, The genset features a Comap InteliGen NTC BaseBox controller with InteliVision 5 display unit. The ComAp InteliGen NTC, a successor of ComAp’s bestseller – InteliGen NT, is a high-end controller suitable for any complex single or multiple gensets paralleling application operating in standby or island mode. The InteliGen NTC is a comprehensive genset controller able to provide parallel operation for up to 32 gensets. According to the manufacturer, ComAp’s InteliGen range of controllers offer unparalleled value, reliability and flexibility. As one of the company’s most popular products, the InteliGen range has become an industry standard for use with single or multiple gensets operating in standby or parallel modes. The Comap InteliGen NTC BaseBox controller can be used indenpendently or in conjunction with detachable / external colour displays InteliVision 5, InteliVision 8, InteliVision 12 Touch, or InteliVision 18Touch According to ComAp it can offer a complete integrated genset solution and signal sharing via CAN bus with minimum external components needed. It offers many communication options - Ethernet connection (RJ45), USB 2.0 slave interface, 1× RS232 / 2× RS485 interface with Modbus protocol support; Analog / GSM / ISDN / CDMA modem communication support; SMS messages; ECU Modbus interface; isolated secondary RS485. The unit features automatic synchronising and power control (via speed governor or ECU), AMF function, Baseload, Import / Export, Peak shaving, Voltage and PF control (AVR) There are selectable measurement ranges for AC voltages and currents – 120 / 277 V, 0–1 / 0–5 A. True RMS (TRMS) is used with Voltage, Current and Power measurement Inputs and outputs configurable for various customer needs. Bipolar binary outputs also provide the option of using BO as High or Low side switch.
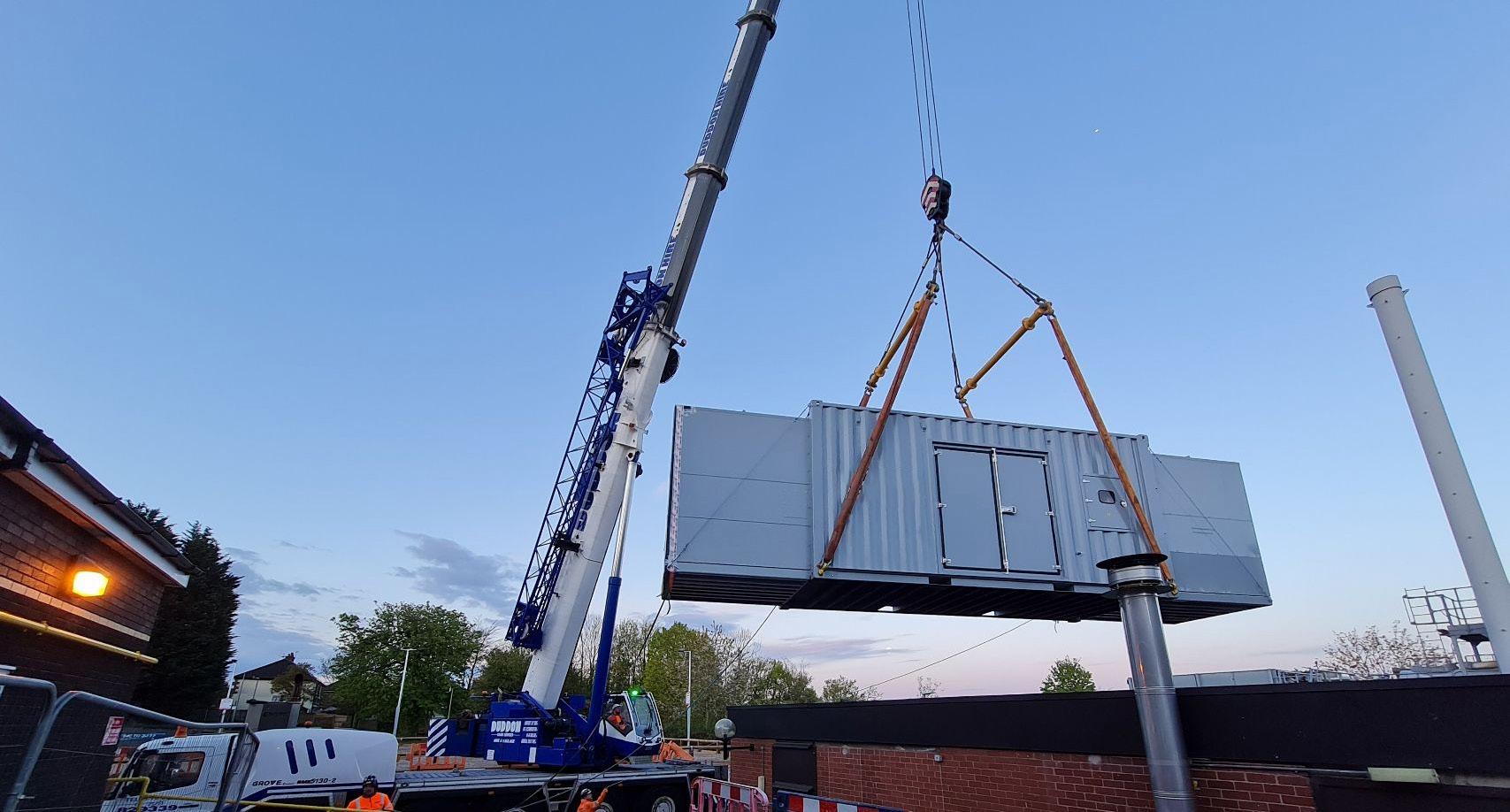
genesalenergy.com
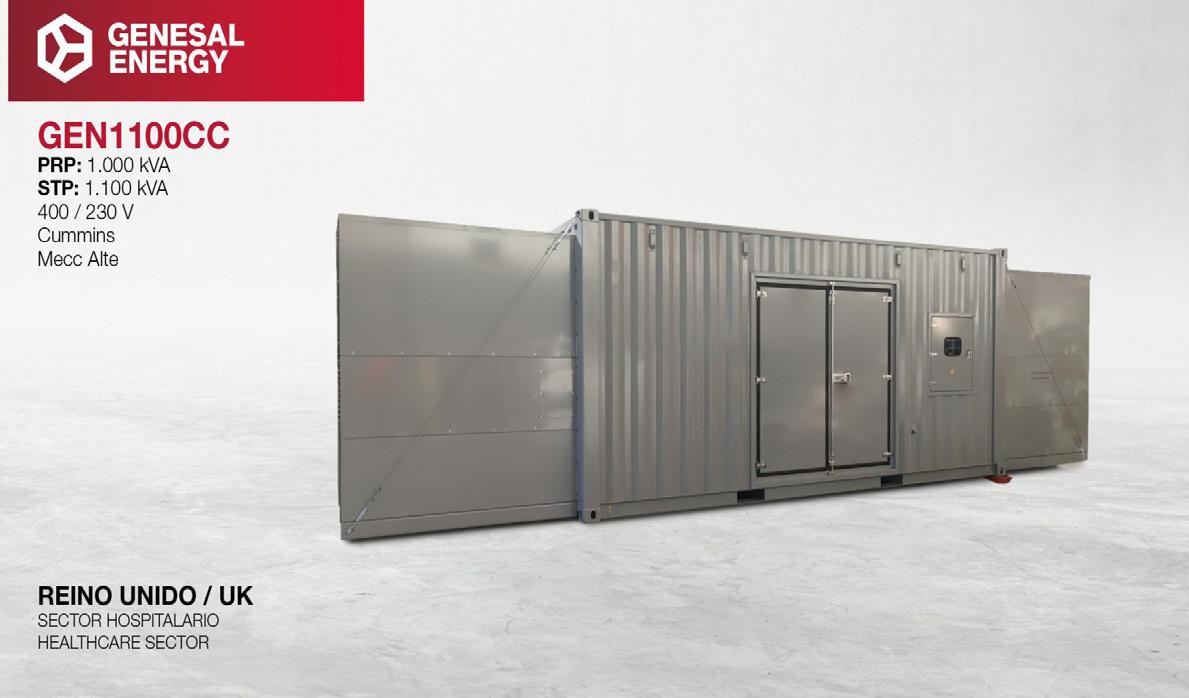
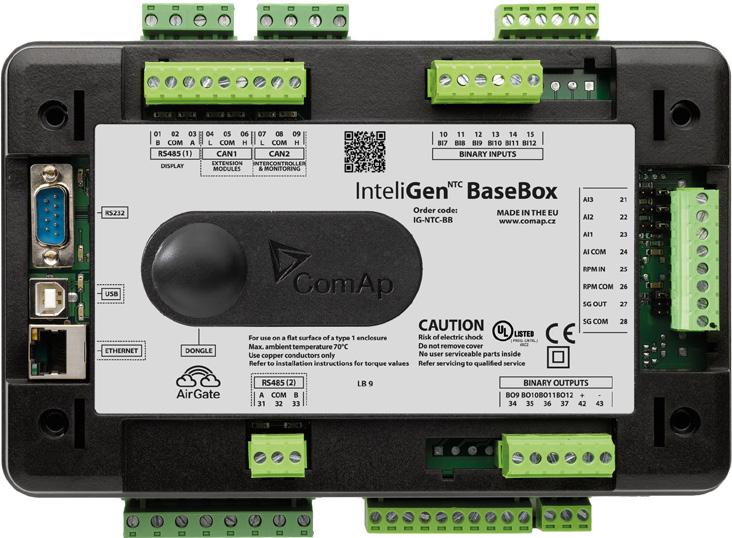
TRANSFORMERS, SWITCHGEAR & CONTAINERISED MODULAR SUBSTATIONS FOR SOUTH AFRICA
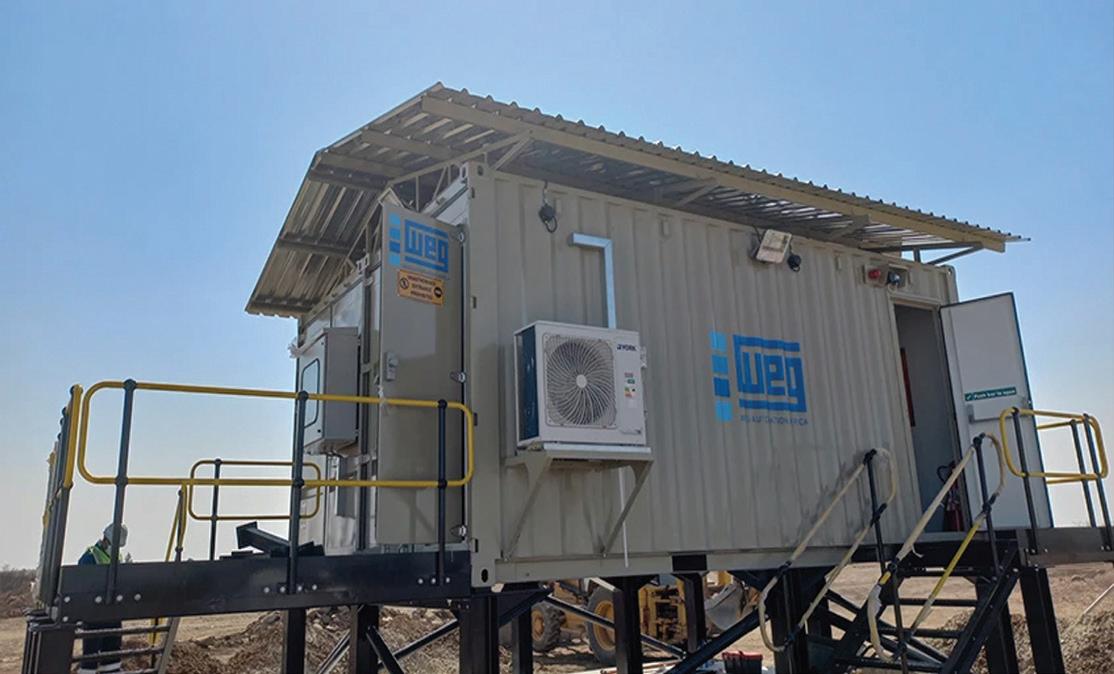
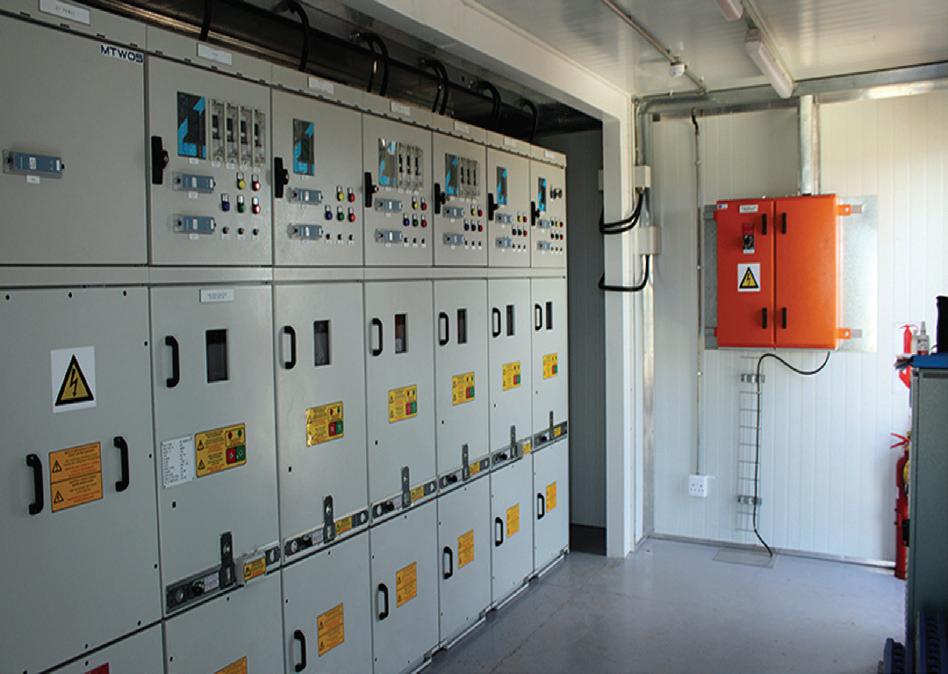
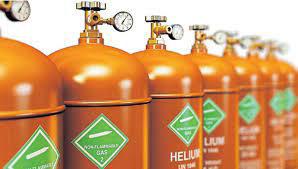
South Africa’s exciting onshore natural gas and helium project Tetra4 is being supplied with transformers, switchgear and containeriSed modular substations by local commercial operation Zest WEG. Developed by emerging producer Renergen, Tetra4 is the country’s first and only holder of an onshore petroleum production right. Located near Virginia in the Free State province, the natural gas in the deposit reportedly contains world-beating concentrations of helium – up to 12% compared to typical levels of around 0,5%. The first phase of the project is advancing well, with the construction of the liquid natural gas (LNG) an helium plant scheduled for completion by the end of 2021 or early in 2022. According to Lukas Barnard, Zest WEG’s sector specialist - oil and gas business development, the equipment ordered from Zest WEG is on track to be delivered and installed in the third quarter of this year. “The transformers we have been contracted to supply are a 7MVA 33/11KV unit and two 1.5MVA 6.6/0.4KV units, being manufactured locally at our transformer facility in Wadeville,” says Barnard. “We will also supply the 33kV, 11kV and 6,6kV medium voltage switchgear, which will be installed into two six-meter containerized substations, being locally manufactured by Zest WEG at its Heidelberg facility.” He explains: “The medium voltage switchgear will be installed in the modular substations in Heidelberg, where a factory acceptance test will be conducted before equipment is transported to site. The complete package is managed with a single point of contact – a project manager – at Zest WEG, easing the customer’s administrative burden.” Renergen says it wanted a supplier with the necessary experience and expertise, but more than that it needed a partner who could meet the tight delivery requirements, with enough flexibility to find solutions to the challenges related to a project of this nature. “There have been many benefits working with local companies including additional flexibility and control, while allowing us to react quickly to changes and challenges that arise as we roll out the project,” says Nick Mitchell, Renergen Chief Operating Officer. “Any support of local business has far reaching economic benefits for the communities in which they operate and this remains a critical balance for us to achieve in a project, where not all the components can be manufactured locally or available locally. It also reduces currency risk by minimizing our exposure to exchange rate fluctuations.” Renergen also emphasizes the advantage of Zest WEG’s package solutions capability, especially in a project like this with multiple streams of work that need to be coordinated across multi-disciplinary teams. Barnard says this is where Zest WEG’s project manager added considerable value in terms of management, procurement and project flow. “When multiple contractors and suppliers are involved, the project flow becomes very difficult and can generate significantly more risk,” he says. “Our project manager was able to work with the customer to mitigate these risks and streamline the roll-out.” He also notes the advantages of the containerized and E-House modular substations in fast track projects. By manufacturing the units in a dedicated facility, Zest WEG provided an efficient solution while reducing the on-site responsibilities of the project developers. “Building a brick-and-mortar substation means more personnel and activity on site over an extended period, with all the related health and safety implications such as inductions and medical checks,” says Barnard. “It is quicker and far more convenient to build it in a wellequipped facility such as ours where it is also possible to run factory acceptance tests before delivery.” Today, WEG offers a complete line of generators for the most diverse applications, from the simplest to the most dedicated, in different environments conditions. Used for power generation, its high quality transmission and distribution equipment is employed by energy & utility companies and substations in large industries around the world.
www.weg.net
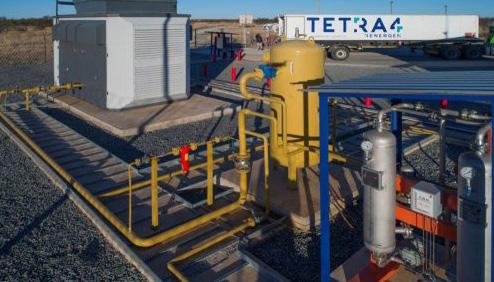
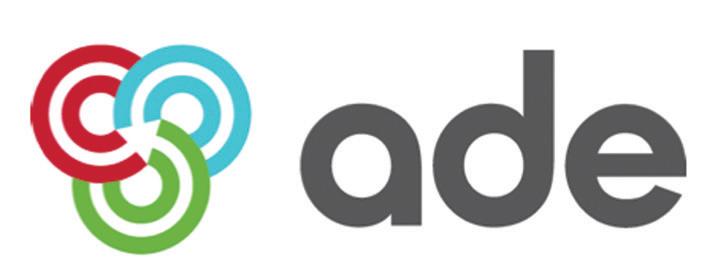
SOCIAL ENERGY CLOSES ELECTRICITY AND GAS SUPPLY BUSINESS, CONTINUES IN SOLAR BATTERIES
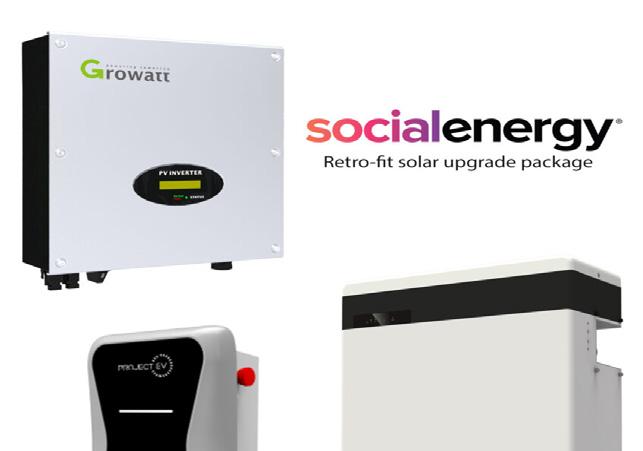
Renewable energy scale-up Social Energy has taken the decision to close its electricity and gas supply business in light of untenable current market conditions, but will continue to operate as a solar battery optimisation company, selling smart battery systems and providing ongoing savings to its customers.
The cleantech company with 7,100+ connected solar battery customers acted as the energy supplier for 5,600 of its customers, helping them to keep their bills as low as possible, in addition to the savings that they make from their solar and battery systems. With the current spiking costs across wholesale electricity and gas, Social Energy has been forced to close its retail energy supply business, and like numerous other suppliers, enter Ofgem’s Supplier of Last Resort (SoLR) process. Since its launch in 2019, Social Energy has always had a different business model to many other supply businesses, has never appeared on switching websites or offered loss-leading tariffs. However, with energy suppliers forced to now sell energy at a loss under the Ofgem price cap, the management team have concluded that the UK supply business is no longer viable.
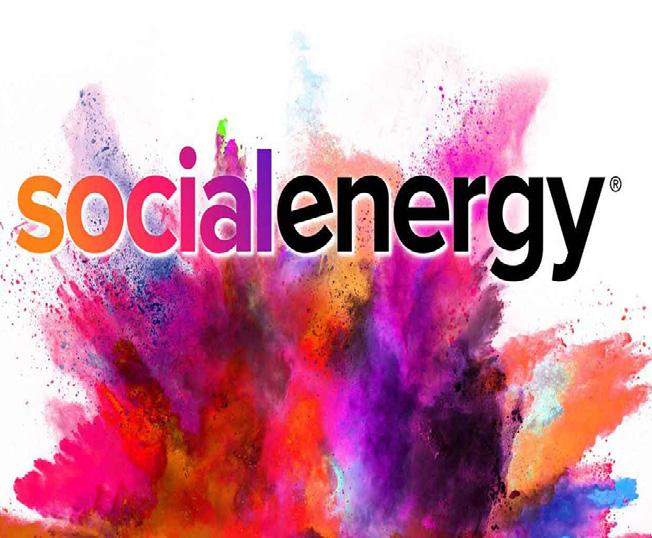
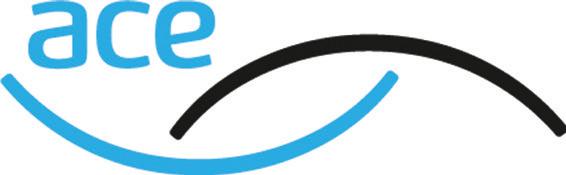

STEPHEN MARCOS JONES APPOINTED CEO OF THE ASSOCIATION FOR CONSULTANCY AND ENGINEERING
Stephen Marcos Jones has been appointed new chief executive of the Association for Consultancy and Engineering (ACE), the business association for those who design, deliver, and manage our infrastructure and built environment.
He replaces Hannah Vickers who left ACE earlier in the year. He will take up his new role on 31 January 2022. Stephen joins following more than a decade in senior leadership roles representing the UK’s energy sector on the global stage. He joins ACE after four years at the helm of UKPIA, the trade association for the UK’s downstream fuel sector. While at UKPIA, Stephen led significant change across this important manufacturing sector, spearheading a cross-industry response on issues such as environmental regulation and promoting the sector’s opportunity to deliver decarbonisation in pursuit of Net Zero, while helping to articulate a vision for a sustainable future for the sector. He has led on issues such as the energy transition, the role of hydrogen, fuel quality, forging proactive and collaborative relationships with the UK Government and the devolved administrations at ministerial level. Most recently, he has promoted the concept of industrial clustering and is a strong advocate of the Government’s levelling up agenda. Prior to this Stephen held a number of senior leadership positions at OGUK, the representative body for the UK offshore energy industry,

Technology Seminar and 73rd Annual Luncheon
Thursday 28 April, 2022 Leonardo Royal Hotel Tower Bridge,London 20/20 Vision: Powering a New Decade
IPowerE’s 2021 Technology Seminar and Luncheon is to be held at the Leonardo Royal Hotel London Tower Bridge. The day will commence at 10.00am with a technology seminar, followed by a 3-course luncheon and guest speakers in the afternoon. The morning seminar will comprise a multistream programme covering a range of technologies and subject matter. The annual seminar and luncheon is well- established as a key event in the calendar of the power and prime mover industries and is an occasion not to be missed. Catch up on the latest technology developments and hear and engage with internationally renowned speakers, network with other members, clients, colleagues and friends, old and new.
Principal Guest: Dr Cathy McClay, Head of Strategy at Sembcorp Energy
Guest Speaker: Mandy Hickson, Former Royal Air Force Fast Jet (Tornado) Pilot
IPowerE’s Operational Report New Submissions Welcomed
The IPowerE Annual Operational Report is an important report and a unique compilation of data of value to the Power Industry worldwide, including owners, operators, financial bodies, manufacturers and consulting engineers.
The report is made available to all contributing Power Owners/ Operators and all IPowerE members. Our objective is to encourage the sharing of information within the power industry for improved availability, reliability and safety of operations in the industry as a whole. Contributors provide data for the report covering engines and all forms of generating plant including reciprocating engines, gas turbines, combined cycle plants, conventional steam plant, hydro plants and renewables including solar, wind, and hydro plants. We invite you to review the Operational Report page: https://www.ipowere.org/operational_report. html
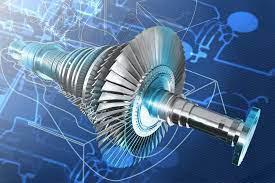
ENERGY DAY AT THE UN CLIMATE CHANGE CONFERENCE UK 2021, SUSTAINABLE TECHNOLOGY & NATURAL GAS
Six years ago, in 2015 COP21 took place in Paris. For the first time ever, every participating country agreed to work together to limit global warming to not more than 1.5 degrees, to adapt to the impacts of a changing climate, and to make money available to deliver on these aims. The Paris Agreement was born. They agreed that every five years they would come back with an updated plan that would reflect their highest possible ambition at that time. So, the run up to this year’s summit in Glasgow was the moment (delayed by a year due to the pandemic) when countries updated their plans for reducing emissions. But, the commitments laid out in Paris have not come close to limiting global warming to 1.5 degrees, and the decade running up to 2030 is seen as crucial. November 4th 2021 was Energy Day at the UN Climate Change Conference UK 2021. The headlines of the day were all about the commitment to phase out coal as the largest single contributor to climate change, although other announcements included the intention to deliver clean, renewable energy to 1 billion people in developing and emerging economies and create 150 million green jobs by 2030. AMPS members have been making the transition to cleaner energy for some time, and although emergency power, particularly in certain situations, may still rely on diesel as a fast and reliable fuel source, there are now dependable greener and cleaner options available. Like it or not the power industry is undergoing a big change. We take a closer look at three AMPS members to discover how they are taking steps to address the problem. The technology has been designed and developed inside PUNCH Flybrid’s premises at Silverstone Park. PUNCH Flybrid Managing Director Tobias Knichel commented: “It takes courage to be first. Select Plant Hire was the first company to approach PUNCH Flybrid for a technical collaboration to integrate flywheel energy storage directly onto tower cranes. “Working together with the Select team for the last few months demonstrated that Select not only understand the technical aspects of tower cranes very well, but they have also shown an outstanding level of support and forward thinking to their impressive customer base. “This has convinced us that partnering with Select is the right next step for PUNCH Flybrid.” Alex Warrington, Select’s Managing Director, said: “At one of our London sites we reduced the generator size on our CTL1600 (66t luffer) from 800kVA to 500kVA, with the opportunity for further reduction. It instantly generates substantial CO² savings and saves significant costs of rental – it makes sense on every level. This is yet another example of Select’s investment in sustainable plant.”
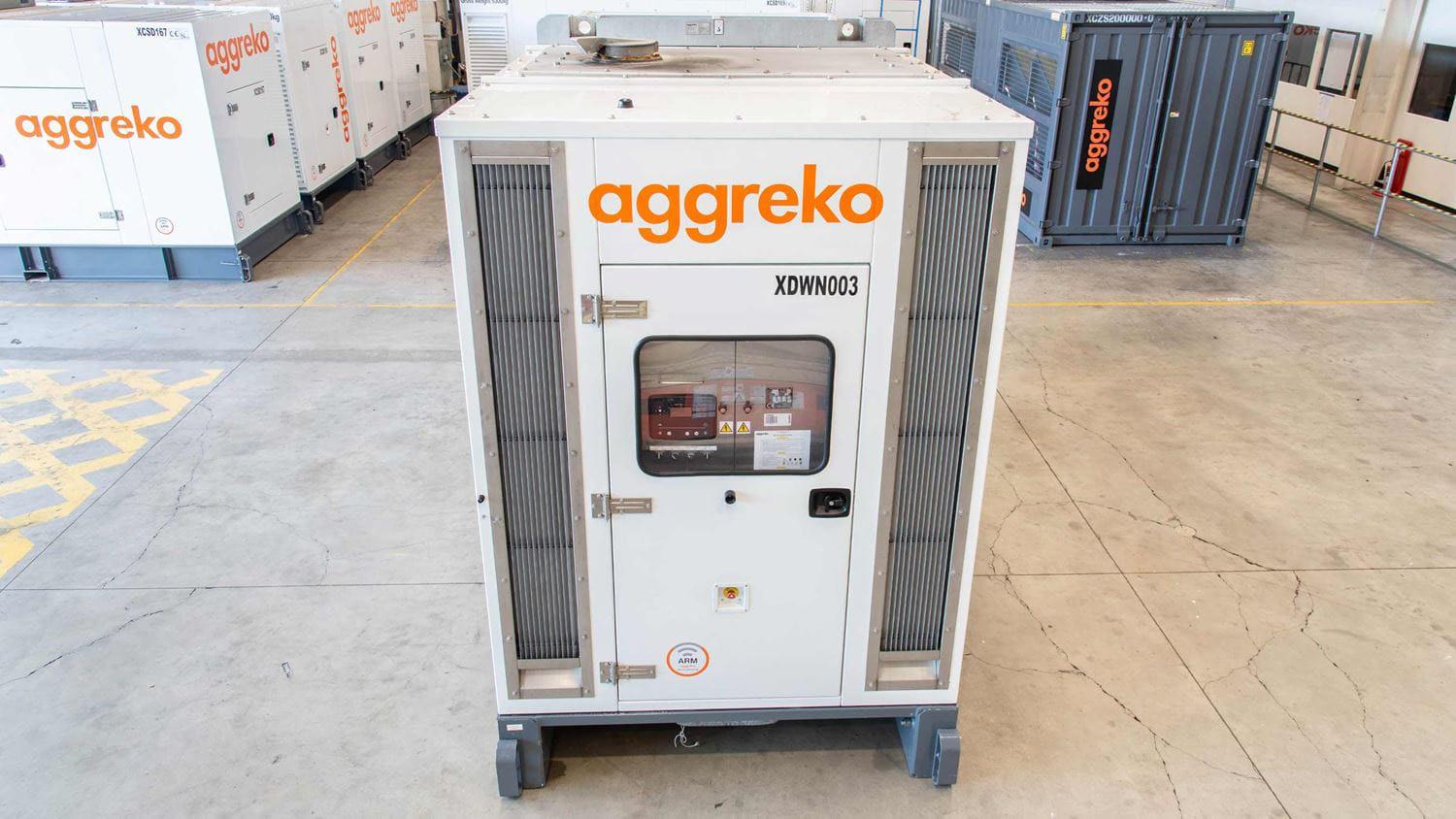
SUSTAINABLE TECHNOLOGY DEVELOPED AT SILVERSTONEPARK SAVING FUEL & EMISSIONS IN CONSTRUCTION Silverstone Park business PUNCH Flybrid entered into a new partnership with Select Plant Hire Ltd. In September that could transform the way generators are utilised on construction sites across the country.
In a trial on one of its sites in London, Select, a leading plant hire specialist, connected a crane’s generator set to a PUNCH Flybrid energy storage flywheel. In just one month (equating to 213 hours), the technology achieved a 50% fuel saving (over 1,300 litres) and prevented close to 3,500kg of CO² being released into the atmosphere. That is the equivalent to the emissions of 30 passenger cars per month (based on average annual statistics per mile in the UK).
AGGREKO: HOW VIRTUAL GAS PIPELINES CAN HELP TO UNLOCK A GREENER FUTURE Conor Dooley, Director of Business Development – Energy Sectors - Aggreko reflects on what’s ahead for natural gas.
Up until now, natural gas has sometimes been viewed in the same category as diesel. The general verdict has been that companies need to ditch all non-renewables as they transition towards lower emissions. Natural gas emits up to 40 per cent less CO2, 80 per cent less NOx, and 99 per cent less SO2 than diesel. Because of this, natural gas will be the strongest growing fossil fuel from 2020 to 2035. It is the only fossil fuel expected to grow beyond 2030, peaking in 2037 before then being replaced by renewable solutions. It can be a key first step in reducing emissions and a stepping-stone on the net zero journey. For hard-to-abate sectors, such as heavy industry and heavy-duty transport, it provides an ideal bridging solution—offering a lower-emission alternative to other fossil fuels. In addition to producing fewer emissions than other fossil fuels, some of its other benefits include: •Its environmentally safer to store than other fossil fuels. •At its present levels, natural gas has enough recoverable resources to last around 230 years according to certain estimates. Up until recently, however, there was one major challenge: Natural gas was only accessible to projects located in close proximity to pipelines. But this is changing. Sectors which have sites in remote locations, such as mines, need to overcome the hurdles of access before they can consider how they begin to reduce their emissions footprint. Traditionally, diesel has been seen as the fuel of choice—due to its inherent energy density, reliability, availability, and relative cost advantage. But when it comes to remote off-grid projects, virtual pipelines provide an innovative and eminently reliable source of LNG. By embracing natural gas, companies operating in hard-to-abate sectors or running remote projects can take the first step towards lowering emissions.
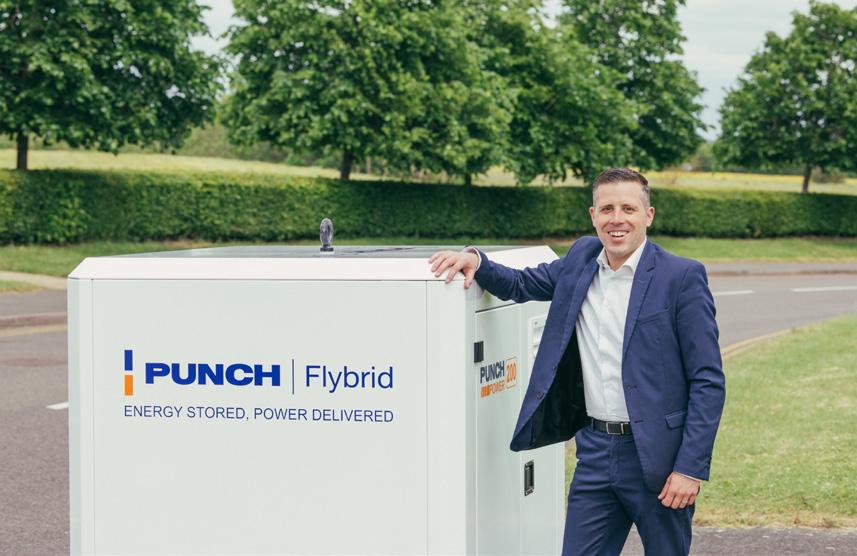
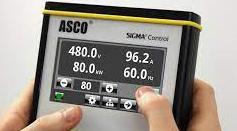
LOAD CONTROL SYSTEM FOR LOAD BANKS
Asco Power Technology is offering the SIGMA - a multifunctional embedded load control system specifically designed for ASCO load banks.
SIGMA is the leader in simplicity, ease of use and accuracy. SIGMA brings market-leading solutions to today’s power testing requirements which can require high-level instrumentation, data capture and verification. SIGMA is currently available in two forms each with various control interfaces * SIGMA LT is an entry-level control system for selected 2000, 3000 and 5000 purely resistive load banks. It provides simplistic load test capabilities for single and networked load banks. SIGMA LT has two user interfaces: * Digital toggles are fitted as standard to all SIGMA LT load banks and provides local control. Digital toggles are perfect for fast load testing when a SIGMA LT hand-held is unavailable. The digital toggle switches provide 3 phase instrumentation on a seven segment LED display located on the load bank. * The SIGMA LT Hand-held is an optional touchscreen remote control that allows the user to utilise all SIGMA LT features and benefits. 25 SIGMA LT load banks can be connected in a network and controlled by a single hand-held. The hand-held allows individual load bank control and total network control with the ability to capture load test data to a USB flash drive.control. * SIGMA 2 is fitted as standard to all 3000, 6000 and 8000 series load banks and can be specified on the majority of other ASCO load banks. SIGMA 2 is the most comprehensive load bank control with high-level instrumentation and data acquisition. www.ascopower.com
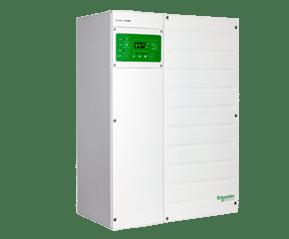
SCALABLE ENERGY STORAGE SYSTEMS
SimpliPhi Power and Schneider Electric now have a UL 9540 safety certification for AccESS and BOSS energy storage systems with Schneider Electric’s XW Pro hybrid inverter charger and SimpliPhi’s PHI 3.8 advanced lithium ferro phosphate (LFP) batteries.
UL 9540 is an important certification and fire safety standard for the design and installation of residential and commercial energy storage systems. Completing UL 9540 certification and related testing enables streamlined system design and simplifies the fire and building code approval process, making energy storage installations simpler, faster and less costly. Approved system designs include both SimpliPhi’s PHI 3.8 kilowatt-hour (kWh) LFP batteries and AmpliPHI 3.8kWh with integrated advanced communications capabilities. SimpliPhi’s trusted LFP batteries do not use cobalt oxides, meaning they are not hazardous and are not prone to thermal runaway and fires like other lithium-ion battery chemistries, says Schneider.
solar.schneider-electric.com
MAHLE SUPPORTS LIEBHERR IN DEVELOPING HYDROGEN-FUELLED HEAVY-DUTY ENGINES
MAHLE Powertrain, the development service provider of automotive supplier MAHLE is supporting Liebherr Machines Bulle SA in their research aimed at developing hydrogenfuelled internal combustion engines, potentially for generator applications.
Their work involves the use of MAHLE’s prechamber jet ignition system (MJI). Engine tests have shown that by using this technology, the mixture of hydrogen and air can be ignited and burned at a high compression ratio, which makes the combustion process very efficient and stable. This paves the way for hydrogen generated in climate-neutral processes to be used in heavy-duty and off-road applications, such as excavators, track vehicles, and wheeled loaders. “The use of hydrogen as a combustion fuel has the potential to make many heavy-duty and off-road applications climate-neutral quickly,” says Peter Wieske, Director Corporate Advanced Engineering at MAHLE. “A large number of studies in recent decades have shown that hydrogen can be used in internal combustion engines without any problems.” “The expertise of Liebherr’s engineering teams in off-highway engine combustion and research on alternative fuels has been critical in this project,” adds Bouzid Seba, Head of Predevelopment at Liebherr Machines Bulle. He underscores Liebherr’s open approach to all technologies, whereby the company explores various methods of energy conversion and the fuels that are most suited to them. “The challenge is to stop engine knocking and premature ignition without reducing the compression ratio and thus efficiency and performance yield. Our joint tests suggest that we have found the right solution with MAHLE Jet Ignition,” notes Mike Bunce, Head of Research for MAHLE Powertrain US. In order to to achieve stable operation with a high compression ratio whilst avoiding engine knock and pre-ignition, hydrogen engines must be operated with a large amount of excess air.
www.mahle.com
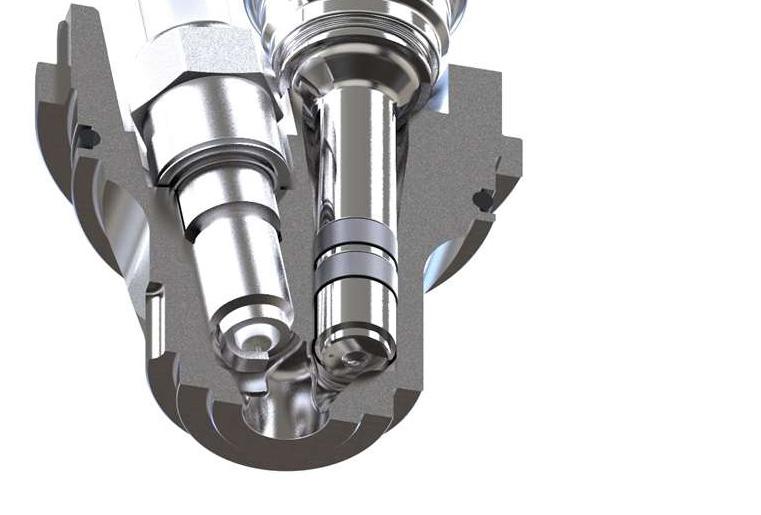
MECC ALTE & THE NEW THE NEW ECP4 ALTERNATOR
Mecc Alte recently introduced the ECP4 C-Type 18 and 20kVA alternators - a technically advanced type designed to suit power generation applications. Whether standby or prime power, this alternator is equipped to suit the demands of the market that requires cost-effective solutions without any compromise on performance.
The alternator range features 12-wire stator output leads, allowing reconfiguration of voltages to suit the usual worldwide requirements: 50/60Hz capable. A damper cage is included which means that any distorted loads and 1phase loads do not create a problem. With parallel capability from standard, together with the damper cage and 12 wire reconnectable there is maximum flexibility for any application. Fitted with a class leading digital AVR that ensures you can get the most accurate voltage regulation and provides alarm history, so you know what the generator has been doing, how often and how long. The industrial range has the advantage of the unique Mecc Alte MAUX (Mecc Alte Auxiliary Winding Power Boost System) which can provide 300% forced current for 20 seconds as standard. This enables each alternator to take transient overload ability much higher than its nominal rating.
www.meccalte.com

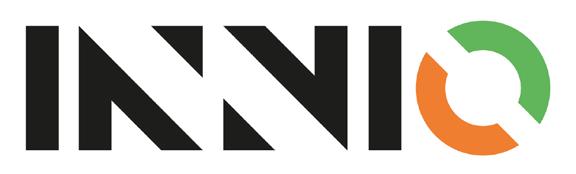
INNIO Jenbacher gas engines
Headquarters: A-6200 Jenbach (Austria) T +43 5244 600-0 F +43 5244 600-527 jenbacher.info@ge.com www.gejenbacher.com Manufacturer of gas driven generator sets and cogeneration systems in a power range from 0.25 to 3 MW.
Model Fuel rpm Pel Pth
JMS 208 GS g 1,500 330 358 JMS 208 GS g 1,800 335 406 JMS 312 GS g 1,500 625 731 JMS 312 GS g 1,800 633 808 JMS 316 GS g 1,500 834 988 JMS 316 GS g 1,800 848 1,079 JMS 320 GS g 1,500 1,063 1,190 JMS 320 GS g 1,800 1,060 1,313 JMS 412 GS g 1,500 844 892 JMS 416 GS g 1,500 1,131 1,194 JMS 420 GS g 1,500 1,415 1,492 JMS 612 GS g 1,500 1,820 1,792 JMS 616 GS g 1,500 2,433 2,399 JMS 620 GS g 1,500 3,041 3,020
Ratings natural gas standard, NOx ≤ 500 mg/ m3N. Dry exhaust gas; based on 5% O2. For engines with 1,200 rpm please contact GE Energy’s Jenbacher product team.
TAD1242GE 352 409 TAD1640GE 393 462 TAD1641GE 433 509 TAD1642GE 485 570
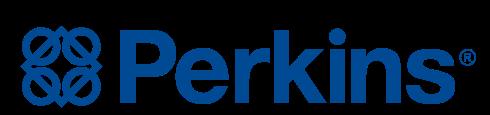
Perkins Engines Company Limited
Peterborough PE1 5FQ Contact name:- Simon Gray Tel: +44 (0) 1733 583000 Email: gray_simon_j@perkins.com Perkins is one of the world’s leading suppliers of off-highway diesel and gas engines, offering dependable cost-effective power up to 2500 kVA in dieselor 1000 kWE prime in gas.
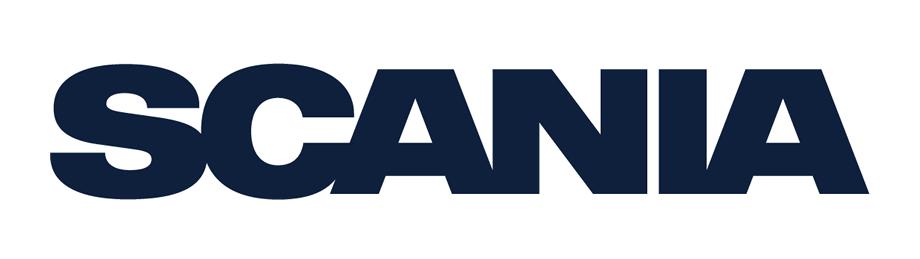
SCANIA ENGINES
SE-151 87 Sodertalje Sweden Tel +468553 81000 Fax +468553 898 12 E-mail engines@scania.com Web www.scania.com
UK Contact – Mark Swindell Scania GB Ltd Tel +44 1908 329386 E-mail mark.swindell@scania.com
Diesel & Gas engines for power generation Prime power 250kVA to 700kVA Stand by power 250kVA to 770kVA
Engine range prime power 50hz & 60hz at (70% mean load factor)
Scania produce diesel and gas powered engines for various Industrial and Marine applications, superior quality and reliability, offering exceptionally low fuel consumption. All models are available to meet current emissions requirements, Scania engines are now available to meet both Tier 4F and EU Stage V. Alternative fuels Many of our engines can also operate on Bio-diesel conforming to EN14214 and HVO conforming to EN159540 R Schmitt Enertec GmbH
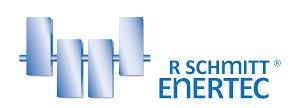
56743 Mendig, Germany T +49 2652 9351810 F +49 2652 9351822 info@rschmitt-enertec.com www.rschmitt-enertec.com Manufacturer of gas driven engines,generator sets and cogeneration systems in the range from 100 - 500 kW. RSE Engines for natural gas and biogas
Model fuel Freq. Electric output
M06-G/B T0D41 g 50 140 kW M06-G/B TID41 g 50 200 kW M06-G/B T2D41 g 50 250 kW M08-G/B TID41 g 50 260 kW M08-G/B T2D41 g 50 333 kW M12-G/B TID41 g 50 400 kW M12-G/B T2D41 g 50 500 kW M06-G/B T0D41 g 60 150 kW M06-G/B TID41 g 60 210 kW M06-G/B T2D41 g 60 250 kW M08-G/B TID41 g 60 280 kW M08-G/B T2D41 g 60 333 kW M12-G/B TID41 g 60 420 kW M12-G/B T2D41 g 60 500 kW RSE engines for LPG M06-PT0D41 g 50 115 kW M06-PTID41 g 50 173 kW M06-PT2D41 g 50 205 kW M08-PTID41 g 50 233 kW M08-PT2D41 g 50 260 kW M12-PTID41 g 50 350 kW M12-PT2D41 g 50 450 kW M06-PT0D41 g 60 130 kW M06-PTID41 g 60 173 kW M06-PT2D41 g 60 205 kW M08-PTID41 g 60 233 kW M08-PT2D41 g 60 260 kW M12-PTID41 g 60 350kW M12-PT2D41 g 60 450 kW RSE engines for Woodgas M06-HT2D41 g 50 122 kW M08-HT2D41 g 50 166 kW M12-HT2D41 g 50 250 kW M06-HT2D41 g 60 140 kW M08-HT2D41 g 60 180 kW M12-HT2D41 g 60 275 kW
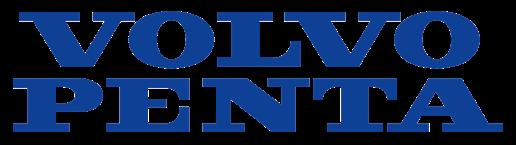
Volvo Penta
405 08 Gothenburg, Sweden Tel +46 31 235460
Model Spec RPM kWm kVA TAD530GE Diesel 15002) 75 85 TAD531GE Diesel 15002) 88 100 TAD532GE Diesel 15002) 113 130 TAD550GE1) Diesel 15002) 76 86 TAD551GE1) Diesel 15002) 89 101 TAD730GE Diesel 15002) 113 130 TAD731GE Diesel 15002) 132 152 TAD732GE Diesel 15002) 162 186 TAD733GE Diesel 15002) 175 201 TAD734GE Diesel 15002) 213 245 TAD750GE1) Diesel 15002) 114 131 TAD751GE1) Diesel 15002) 13 152 TAD752GE1) Diesel 15002) 158 182 TAD753GE1) Diesel 15002) 173 199 TAD754GE1) Diesel 15002) 217 250 TAD940GE Diesel 15002) 241 277 TAD941GE Diesel 15002) 280 326 TAD1341GE Diesel 15002) 271 315 TAD1342GE Diesel 15002) 303 352 TAD1343GE Diesel 15002) 325 378 TAD1344GE Diesel 15002) 354 412 TAD1345GE Diesel 15002) 388 451 TAD1351GE1) Diesel 15002) 279 324 TAD1352GE1) Diesel 15002) 314 365 TAD1354GE1) Diesel 15002) 328 381 TAD1355GE1) Diesel 15002) 355 413 TAD1640GE Diesel 15002) 392 461 TAD1641GE Diesel 15002) 430 505 TAD1642GE Diesel 15002) 503 591 TWD1643GE Diesel 15002) 536 630 TAD1650GE1) Diesel 15002) 393 462 TAD1651GE1) Diesel 15002) 430 505 Engines are also available for1800rpm/60Hz