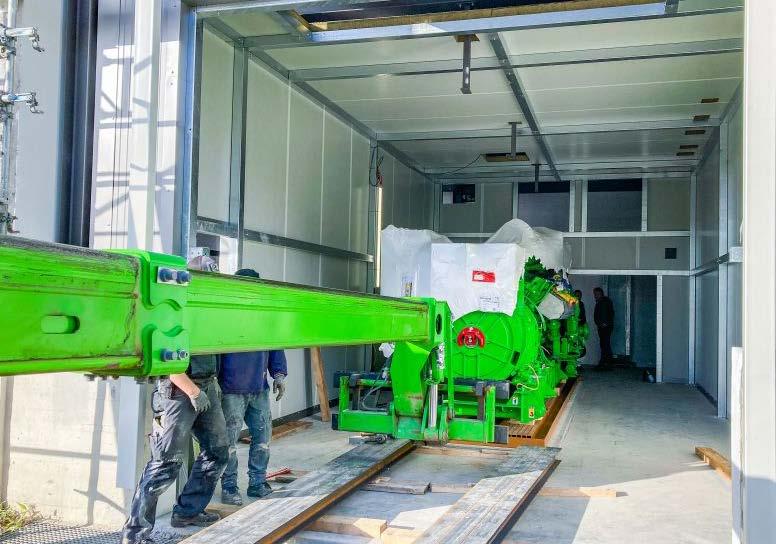
3 minute read
CHP
1,700 KW CHP INSTALLATION AT GERMANY’S MEMMINGEN AIRPORT, BAVARIA

INNIO has been involved in the supply and installation of a 1,700kW CHP unit to a construction site at Memmingen Airport (FMM). The project involved installing a new biogas CHP and installing the 7.6 m high and 7.6 t chimney. The
CHP plant has an electrical output of 1498 kW, as well as a thermal output of 1,702 kW. In addition, it features exhaust gas cooling up to 90°C and has an unladen weight of 17 tonnes. Memmingen Airport, also known as Allgäu Airport
Memmingen, is an international airport in the town of
Memmingerberg near Memmingen, the third-largest city in the Swabia region of Bavaria. It is the smallest of the three commercial airports in the state after Munich Airport and Nuremberg Airport and has the highest altitude of any commercial airport in Germany. It is operated by Flughafen Memmingen
GmbH, a limited partnership of mostly local, medium-sized companies and public shares. Located about 3.8 km (2.4 mi) from the centre of
Memmingen and 110 km (68 mi) from the city centre of Munich, it serves Memmingen and the Allgäu. It provides a low-cost alternative to Munich Airport and therefore is sometimes referred to as Memmingen/
Munich-West Airport. It serves as a base for Ryanair and features flights to European leisure and some metropolitan destinations and handled over 1,7 million passengers in 2019. Cogeneration or CHP (Combined Heat and
Power) solutions from INNIO are designed to generate both heat and power increasing overall power plant efficiency up to 90% and even more. This efficient and economical method of energy conversion achieves primary energy savings of roughly 40% by using a gas engine cogeneration system instead of separate power and heat generation equipment.
Transportation and distribution losses also are reduced or eliminated as the decentralized energy supply is aligned where it is needed. INNIO Cogeneration solutions are used by our customers across the globe, powering applications in variety of economy segments, for example - industrial manufacturing, commercial, municipal applications, greenhouses and many more. Jenbacher onsite cogeneration solutions can help customers to achieve economic targets thanks to one or several of factors, such as: -Decrease of Energy-related OPEX compared to centralised energy sources, or - Launch/extend company’s operations due to new power access in energy-deficit areas, or -Minimise downtime thanks to improved quality of the electricity supply in regions with unstable grid infrastructure, and much more -Type 4 B-Version Upgrade (INNIO) The basic structure of INNIO’s Jenbacher CHP systems includes a gas engine/gas generator unit and heat exchangers that use waste heat. A wide range of heat sources - from gas engine cooling water and oil to an air/fuel gas mixture and exhaust gas - is configured to give each individual customer the greatest possible benefit. INNIO cogeneration plant solutions deliver flexible power generation and a high degree of reliability and availability. Jenbacher CHP modules can be installed inside buildings or packaged into ready-to-use containerized CHPsolutions. Containerised cogeneration power plants allow our customers to start using the benefits of onsite power generation quickly. Cogeneration systems can be supplemented with a boiler system for bridging peak heat demand periods. The connection of a heat storage medium makes it possible to increase system operating time and efficiency. Cogeneration power plant electrical switch and control systems distribute electricity and manage the engine, while hydraulic equipment ensures heat distribution. Generated power is used by a facility or fed into the public power grid. The thermal energy can be used to generate heating water and steam production as well as for various types of process heat. Gas engine cogeneration systems also are used for CO2 fertilization in greenhouses and trigeneration systems (combined generation of heat, cooling and power). Cogeneration systems can be supplemented with a boiler system for bridging peak heat demand periods. The connection of a heat storage medium makes it possible to increase system operating time and efficiency. Cogeneration power plant electrical switch and control systems distribute electricity and manage the engine, while hydraulic equipment ensures heat distribution. Generated power is used by a facility or fed into the public power grid. The thermal energy can be used to generate heating water and steam production as well as for various types of process heat. Gas engine cogeneration systems also are used for CO2 fertilization in greenhouses and trigeneration systems (combined generation of heat, cooling and power).
www.innio.com
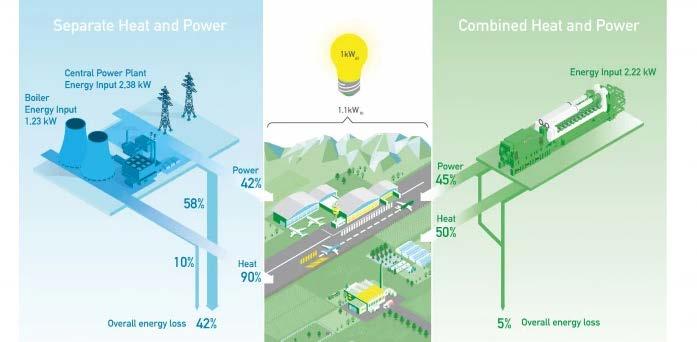