
24 minute read
CRAFTING BRILLIANCE
Ceramic Artists Perform Alchemy With Glazes And Pigments
BY SARAH E. WHITE
Advertisement
In the world of pottery, where creativity and craftsmanship converge, some artists are not just molding and glazing their clay, but creating their own unique surface treatments. Experiments with glazes lead these artists down rabbit holes to places where earthy elements transform into never-before-seen hues and textures.
At the Center for the Visual Arts in Wausau, the studio produces 35 custom glazes. "It's like cooking," says potter Ron Hay. "There are thousands of recipes."
The Center for the Visual Arts in Wausau (CVA-Wausau) is spreading the joys of glaze-craft in central Wisconsin. Opened in 1976 and now located in a historic arts block in Wausau’s downtown, CVA-Wausau is a dynamic and inclusive space for both emerging and established artists. The Center takes pride in its education program, which offers workshops, classes, and lectures for both aspiring and seasoned artists.
Mara Mullen, Director of Education, finds that students in CVA-Wausau’s pottery classes come in “focused on the clay body— making a mug, a bowl, a vase—rather than thinking about how it might be glazed. They’ve never been exposed to this aspect of ceramics,” she said. “They look at our glaze board and they can be a little overwhelmed.” The studio, where potter Ron Hay has been artist-in-residence since the 1990s, currently produces 35 custom glazes. “It’s like cooking,” Hay said. “There are thousands of recipes. Potters share them, and there are books full of them.” But he noted that outcomes can still be unpredictable. “A lot of times, a recipe doesn’t work when you mix it up, because your chemicals came from a different part of the country than the than the other ceramicists.” A slightly different molecular composition can yield a quite different result. But, said Hay, “You don’t have to be a chemist— you learn to adjust recipes through trial and error.” Because most students want to make functional ware, almost all of Hay’s housemade glazes are designed to be food-safe.
The Science Behind The Surface
People unfamiliar with ceramics may have admired the colorful surfaces of pottery without giving a thought to the “how” and “why” of their glazes. Glaze is a coating applied for both aesthetic and practical purposes, designed to adhere to a fired ceramic object. Glaze attributes vary widely, from glossy to matte, translucent to opaque, glassy-smooth to textural. Its main components are silica, which forms the glassy surface; flux that lowers the melting point to improve adherence; and alumina to stabilize the glaze. Silica comes from quartz, flux is often feldspar or boron compounds, and alumina is an element derived from clay. Additionally, pigments play a crucial role in ceramics, contributing to the rich palette of colors seen in glazed pieces. These finely ground substances are added to the glaze mixture or to the clay itself, to introduce hues and variations. Part of ceramic art’s appeal is the earth-bound nature of the materials involved.
Glaze components react in a kiln during the firing process. As the temperature rises, the glaze transforms from a powder into a molten, glassy substance. The right balance of silica, flux, and alumina, along with additional elements for color and texture, determines the final appearance of the glaze. Understanding this basic chemistry provides a practical foundation for ceramicists to experiment with different formulations to achieve specific effects on their pottery.

Beyond the three main components, a variety of other materials can be added depending on the artist’s vision for the piece. For example, colors and textures can be customized, and glazes can be made to move in certain ways to achieve effects such as cracking, foaming, or dripping. A glaze’s behavior and appearance depend on how it is fired—the same glaze may turn out differently with different temperature, timing, and the atmosphere in the kiln. Adding or reducing oxygen or introducing wood, salt, or other materials will also affect a glazed object’s ultimate appearance.
Beginners can get started in ceramics with just an introductory level of knowledge, or choose to advance as far as they like; the range of knowledge among working ceramic artists is broad. Some, however, who fall down the rabbit hole and discover the intriguing world of pigments and glazes, are driven to learn the chemistry behind this wonderful alchemy.
David Harper, an interdisciplinary artist living near Racine whose work is in the collections of the John Michael Kohler Art Center and The Museum of Wisconsin Art, began working with clay when he realized he was using non-clay materials to create objects that imitated ceramics. “At any point, you can choose to stop or go deeper. Knowing the basics is important, like how hot to fire certain things to achieve certain effects. Then people might get into making their own glazes, achieving effects nobody has ever seen before.”
Some artists introduce pigments into the clay itself, not just the glaze. Michael Ware creates abstract ceramic sculptures and teaches ceramics at the University of Wisconsin-Milwaukee. He began working with stains and pigments to express his interest in “this geological world,” he said. “It was disappointing whenever I broke a little bit off a sculpture and it was white inside. Glaze is just on the surface, whereas when I color the clay, it has color the whole way through—like a rock.”
But, artists advise, do not start making glazes until you know how to do so safely. Understanding material hazards and proper use of studio equipment and tools is critical. Potters need to minimize aerosol particles and exposure to toxins. That means, when mixing clay and glazes, always wear a respirator and work with good ventilation systems; never eat or drink in the studio; wear safety glasses and gloves. Wipe down work surfaces and mop floors. Some glaze ingredients, like barium and lithium, yield beautiful effects but are toxic. The toxicity can range from mild skin irritation to causal factors in cancer. Kilns have their hazards, too. Loading and unloading heavy pieces can cause injury. While firing, fumes are present. It is important to avoid the area and/or use good ventilation and a respirator. Check that no combustible materials are located near a kiln before every firing. When producing functional ware, such as plates and mugs, use only food-safe glazes. Safety guidelines are reassessed regularly— otherwise, we might still use lead in glazes! Check for current information before working with glazes.
WHY GO DOWN THE RABBIT HOLE?
Potters choose to make their own glazes for several reasons including cutting costs, developing greater skill with their medium, and controlling the environmental impact of their work. But the reason most cited for diving into glaze-making is to achieve a specific creative vision.
The cost of commercial glazes often drives beginning potters to make their glazes. Simply setting up a studio requires an initial investment that can be steep even before purchasing dozens of glazes, which frequently cost more than twenty dollars a pint. Mixing glazes requires only common kitchen tools like a scale, mixer, and measuring utensils, and the ability to follow a recipe.
The educational value of learning to formulate and test glazes is undeniable; potters deepen their understanding of materials, chemistry, and firing processes through glaze-making. Mullen said, “With beginning students, we steer them towards our most predictable glazes because they put so much effort into making these precious objects. If they fail, it can turn students away from ceramics in general.” Ceramic-making involves not only experimentation but also failure. Learning to troubleshoot the causes of failures is important to the process.
Increasingly, ceramic artists are considering the environmental sustainability of their art form. Clays and the chemicals used in glazes are mined all over the world. Materials mined in one place are frequently shipped to distant locations for processing and then shipped again to the point of sale. Ware said, “I’ve become more aware of the environmental impact of ceramics and the environmental impact of all that transport.” Historically, potters lived close to sources of clay and mined the clay themselves. Today some potters are working with “wild clay,” finding raw materials nearby and screening out impurities to create workable clay.
Madison-based potter and ceramics teacher Joanne Kirkland makes porcelain sculptural pieces inspired by the pottery of the southwestern United States, Mexico, and Japan. She primarily uses Grolleg, a blended china clay from England, where some Grolleg mines are now depleted. Kirkland said, “I recently started thinking I should use more local materials, what with climate change and the impact of transportation.” She has begun experimenting with wild clay herself. So has Ware, who likes using the local pale-gold clay that, made into bricks, gave Milwaukee the name Cream City. From the sustainability of the raw materials, through managing the risks of the more dangerous chemicals in glazes, to the disposal of waste materials, potters are increasingly choosing materials and processes for their environmental sustainability.
Artistic expression is the foundation of every aspect of a ceramic artist’s work and the dominant reason for making glazes. Color palettes, surface effects, and where a particular idea for a piece fits on the spectrum from functional to sculptural all factor in, driving choices about pigments and glazes. Experimentation is an integral part of that process, as artists tweak formulas, test new combinations, and push the boundaries of traditional glaze recipes to achieve unique results. Harper said, “Every ceramicist I know has libraries of test tiles where they have added grain after grain of a certain mineral to change a pigment or change how a glaze flows. Control is the draw for a lot of people.”
And yet control must be balanced with openness to serendipity. Scott Draves of Door Pottery in Madison teaches beginning and continuing students through local community programs. “I conceive of a glaze for each piece before throwing it, a process that only a small percentage of potters do. The best work comes out of the surprises and mistakes I make.”
Rachel Imsland, a potter who serves on the board of the Madison Area Potters Guild, said, “I have to remind myself to have no expectations, because when I expect a pot to look a certain way it won’t. You always need to be open and be ready for a surprise.” Imsland set up a home studio during the pandemic. She began making glazes because she missed the ones available at the Midwest Clay Project, a community clay studio in Madison, where she had worked prior to COVID. At first, Imsland saw making her own glazes as a huge hurdle. “As a beginner, you just want to think about making pots. Somebody else, please make the glaze. But with practice, you find, it’s fun!”
Artists Speak
Custom creation of glazes and pigments is taking place across Wisconsin in schools, universities, community spaces, and artists’ studios. Some are working in traditional techniques and some are digging deeper with experiments that erase the line between the clay body and the glaze.
Scott Draves creates functional ware inspired by the Arts and Crafts movement. This international trend in the decorative arts emerged as a reaction against the industrialization of the late 19th century. Its proponents championed craftsmanship, simplicity, and a return to traditional techniques in which the maker’s hand is visible. Draves recreates that style with pigments and glazes he customizes to mimic the originals, minus the deadly lead content used in the glazes of a century ago. Like Draves, many of today’s ceramic artists are drawing inspiration from the ethos of the Arts and Crafts Movement, finding a potent source of creativity in its rejection of mass production and celebration of the handmade.
Kirkland took a ceramics class while studying fashion design in college, where she fell in love with the physical, tactile, experience of clay. “What drew me in was learning how to throw on the wheel; learning how to center was the hardest thing,” she said. “You have to be pretty centered yourself to do it. When you learn to use your body, that is a very magical experience.” Over the decades, she has evolved from an interest in functional objects to a focus on more metaphorical sculptural vessels. Throughout, her objects’ surfaces have been decorated with geometric representations of natural phenomena. Ancient pottery fascinates her; “I enjoy residing in a continuum of thousands of years of tradition,” said Kirkland. “It’s been a constant evolution and exploration, a dialogue with clay and glazes.”
CVA-Wausau’s Mullen started out primarily sculptural in her art, but after her teaching experience she now leans toward functional ware. “It’s a joy to create things I need and would like to use. But I do still love sculpture. I love rethinking the vase, rethinking the mug— how can I bring sculptural elements to these functional works?”
Harper considers himself not a ceramicist, but an artist who uses clay as part of his vocabulary. Originally from Toronto by way of the Nova Scotia College of Art and Design, he spent two seasons as the Kohler Arts and Industry Artist in Residence in winter 2012 and 2014. “There is a beautiful symbiotic relationship there,” he said. “Working in this very utilitarian environment, watching the grace, the dance of these factory associates working with the same material I use—it still affects the way I work in the studio, based on their model of efficiency.” Harper’s installations are cross-disciplinary and employ both traditional and nontraditional materials. “I make these small worlds that are so bizarre but are grounded by materials I choose because of their familiarity,” he said. “I choose colors and surface textures that are nostalgic.”
Christina West is an Associate Professor in Ceramics in the Art Department of the University of Wisconsin-Madison. While teaching an introductory ceramics class, West found herself growing enthusiastic about what glaze can do that other materials can’t. “In trying to get the students excited about it, I sold myself on it,” she said. “You can change the qualities of an individual glaze, but when you put two or three glazes on top of each other, they do unpredictable things.” She explores the push-pull between unpredictability and replicability. “I’ve found a sweet spot where I know in general what’s going to happen, but I can’t predict exactly.” Her work is sculptural and frequently multi-media; her installations have explored fragmenting human forms and creating surface textures that contemplate mortality. “I feel very much like a painter when I’m glazing,” West said. “I’m thinking about marble, but I want a fleshiness to show through so it’s more humanistic.”
AT THE DRIPPING EDGE OF EXPERIMENTAL TECHNIQUE: GLOOPS AND CLAZES
Ceramic artists are embracing the expressive and organic nature of their materials and processes, part of a movement sometimes called “action claying” that exploits the alchemy inside the kiln. Some are
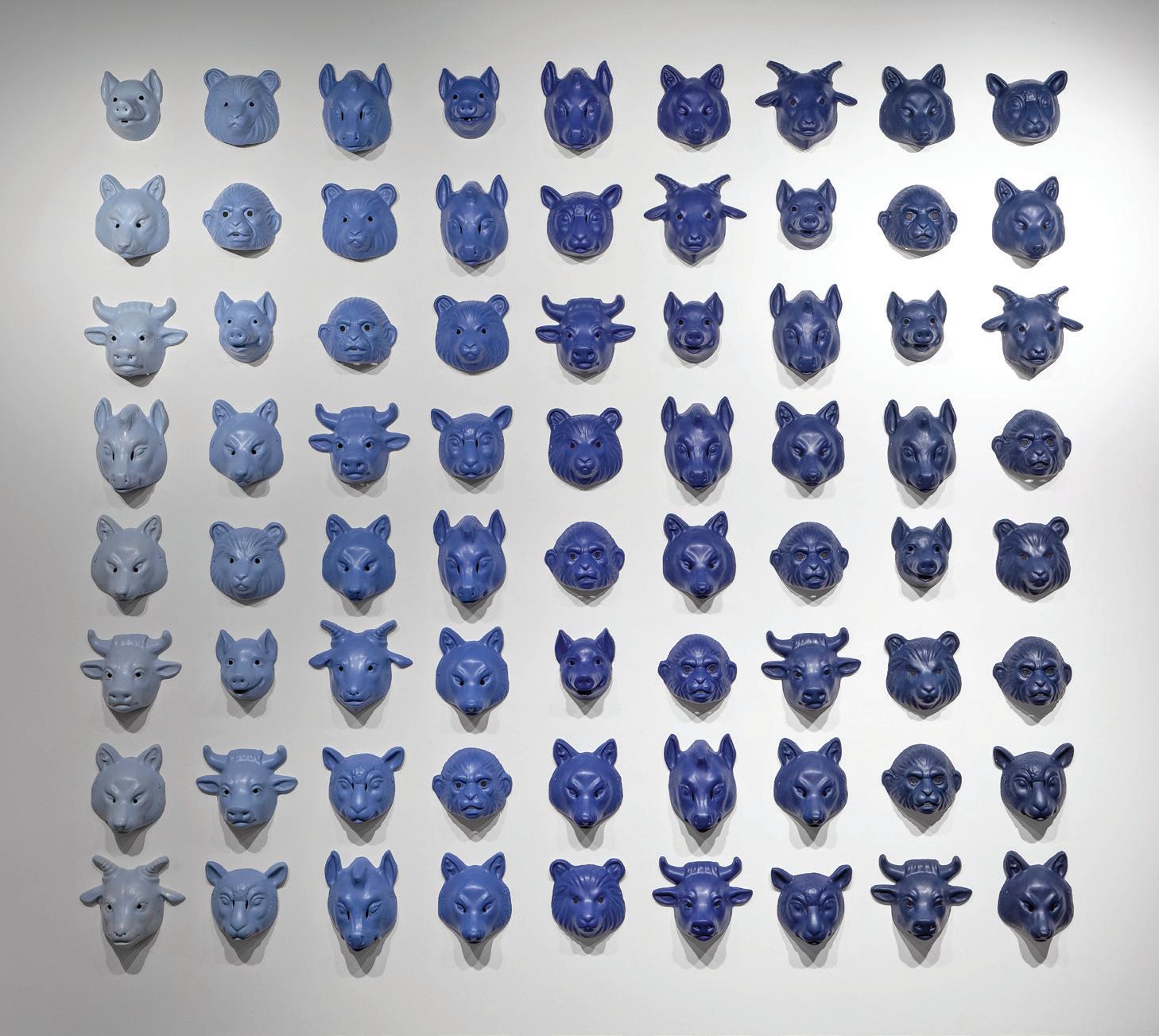
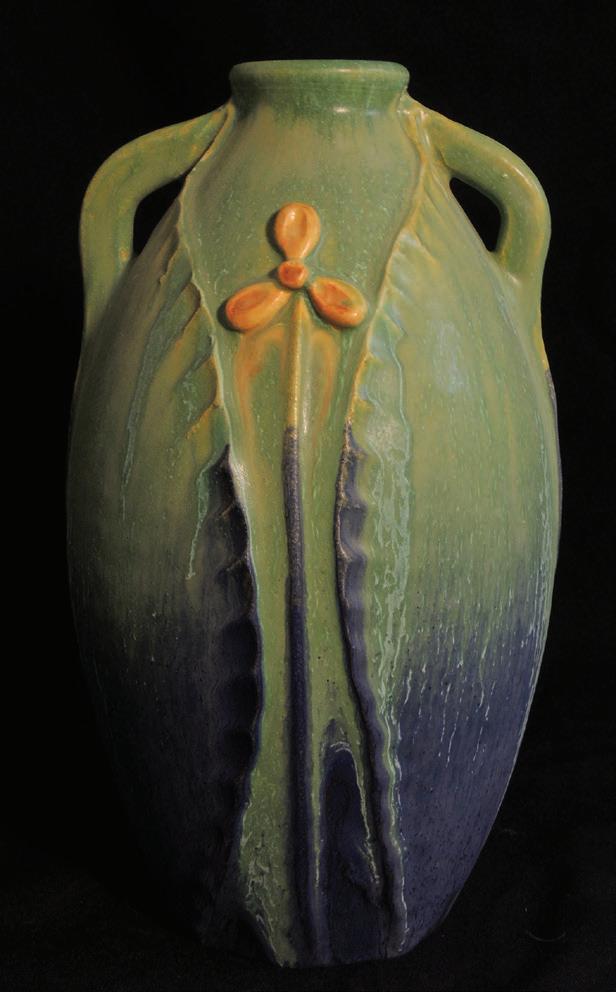
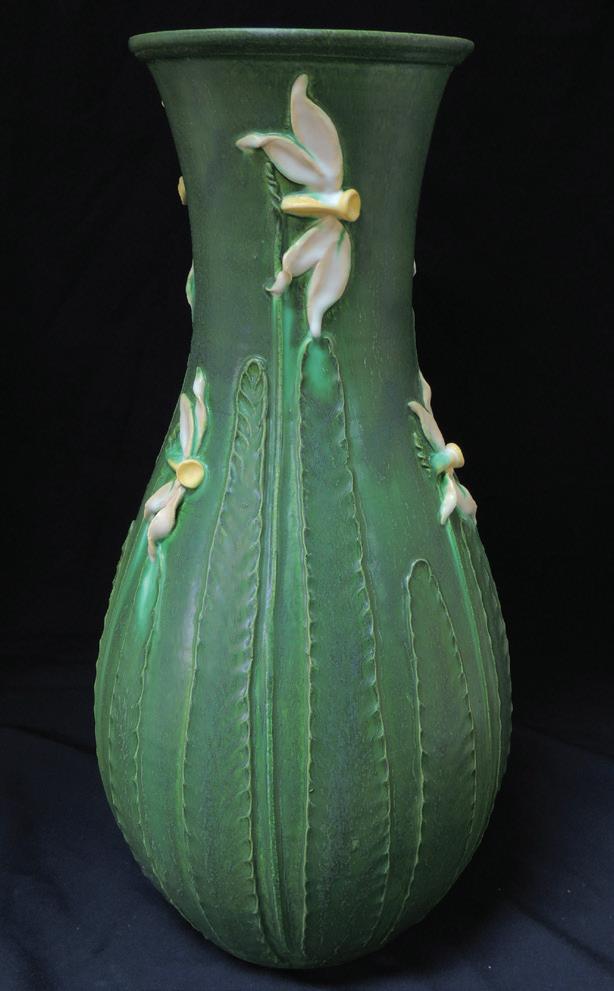
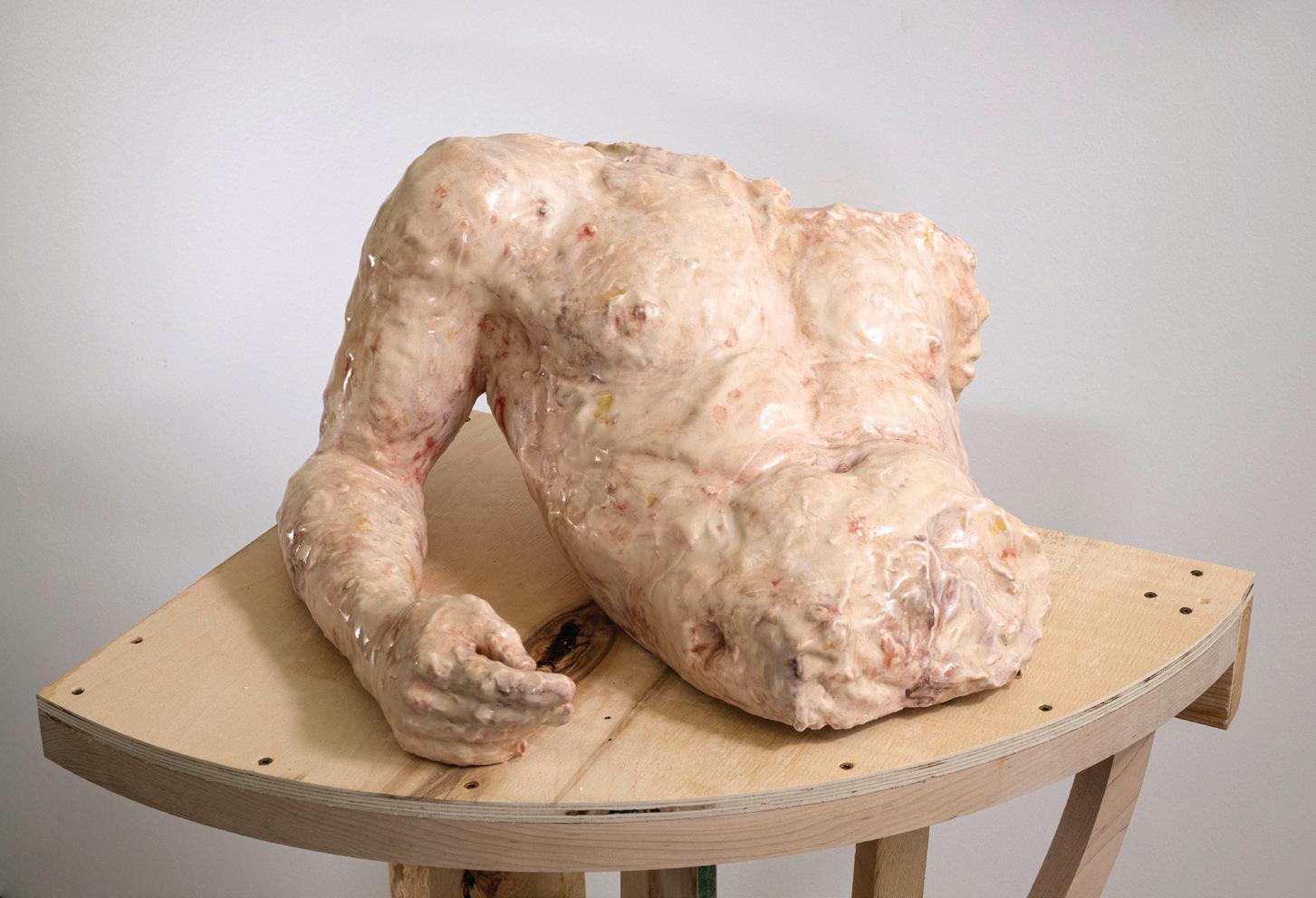
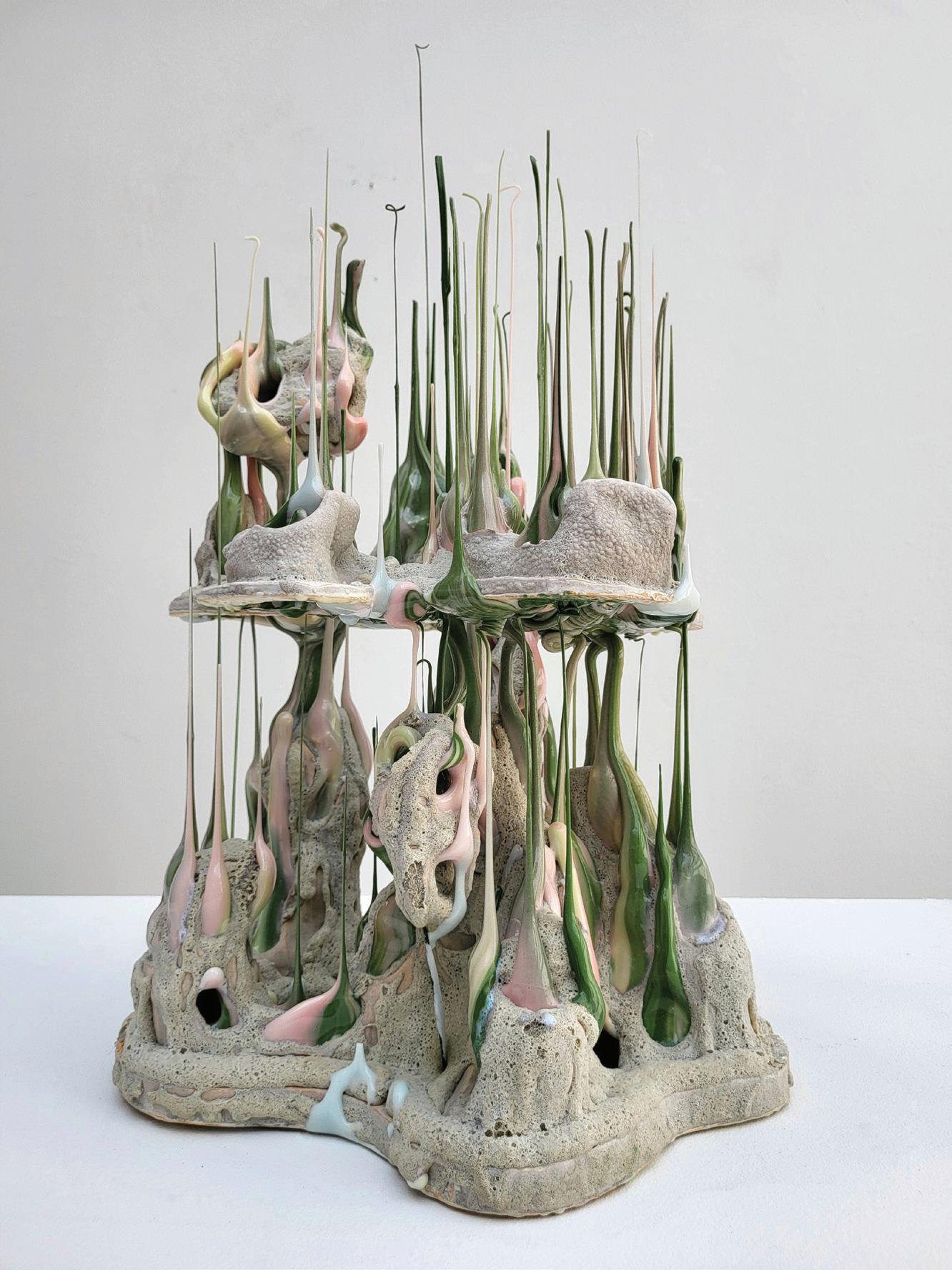

WHERE WILL TOMORROW’S GLAZE-MAKERS LEARN THEIR CRAFT?
A journey down the rabbit hole of custom-made pigments and glazes leads to something akin to the extremes at the earth’s core, where intense heat applied to earth elements produces a magic array of rocks and minerals. One wonders what tomorrow’s ceramic artists will produce, and how they will learn their craft.
Draves, who teaches pottery through Madison School-Community Recreation (MSCR) and at Madison College, observed, “Everything used in ceramics is essentially broken-down rock. The first time students get their hands on that, they just love the feel of the material. Nine out of ten will want to try another class.” But will there be classes for them to enroll in?
using “gloop” glazes, a term coined to describe thick, viscous, unpredictable surface treatments, which represent a departure from the traditional, more controlled glazing techniques. Heat determines whether clay and glazes behave like solids, liquids, or even gasses. Gloop work is characterized by drips, dynamic textures, and vibrant colors. Artists are drawn to the serendipity inherent in a process that leaves so much to the kiln’s environment to complete.
One of West’s graduate students, Morgan Baldinelli, is part of this trend, creating clay bodies with voids that she fills with gloop, then suspends in the kiln so that drips pour from inside the pieces when the kiln reaches its highest temperature. “I’m personally fascinated with glazes and how surface texture occurs,” she said.
“The only thing connecting the two gray pieces is the gloop material. It took a bit to figure out how to suspend it in the kiln so that it would flow as I wanted.”
Ware was drawn to ceramics once he discovered the parallels between the ceramic process and certain geologic processes; in both, materials combine through heat, pressure, and time. Bringing that into his vision for his pieces, he said, “I’m not so much trying to replicate what forms look like but more so to bring out their energy.” Seeking to express energy with color, he began adding pigments to clay when he noticed the colors were even more vibrant than glazes.
Recently Ware has begun experimenting with the sculptural qualities of glazes. “I call it “claze” because it’s kind of a mixture of clay and glaze,” he said. “I play a lot with that boundary between the two. I try to create some parameters to then experiment within and solve problems.” In some of Ware’s work, he uses claze—and the kiln’s heat—to fuse in the kiln small individual elements built of clay to make larger sculptural pieces. In others, he buries claze in boxes filled with sand, and then excavates the resulting pieces after firing. “That came from my interest in geology,” he observed.
This trend in ceramic arts embraces spontaneity and the imperfections that arise in the creative process. It celebrates the unplanned and the unrestrained. It is only natural that counter-trends will emerge as they always have, pushing the boundaries in different directions. We may next see a deliberate move away from the exuberance of gloop glazes toward minimalist and refined aesthetics, where artists opt for cleaner lines and precise glazing techniques.
While teachers report that classes fill immediately, some schools and universities under pressure from tight finances have closed pottery teaching studios and even ended arts instruction entirely. At CVA-Wausau, Mullen said, “We’re lucky because we have wonderful arts educators within our school system. But I know that access to ceramics equipment and facilities isn’t the case elsewhere, especially in more rural areas. We try to spread what we do here as far into the state as we can.” Rural schools in central Wisconsin bring their students into Wausau for immersion days offered at the Center’s pottery studio.
The Wisconsin Department of Public Instruction’s data indicates that student enrollment in ceramic arts programs declined from 32 percent in 2019 to 28 percent in 2021, while overall arts enrollment dropped by 10.7 percent in that timeframe. To lose more arts programs, especially in ceramics, would be a blow.
Ware observed, “Ceramics inherently creates communities because it’s hard to do alone. Filling and firing a kiln can be very laborious. Also, potters work long hours in a space shared with other people.” At a time when social isolation has been identified as a national health threat and young people are experiencing worsening mental health, arts programs offer a counter-balance. Kirkland said, “When I started teaching at Madison College, so many students told me, ‘This is like therapy.’”
But perhaps the most important reason to call for the continuation of arts education programs is the least tangible. “When students ask me what they can do with a ceramics degree,” Ware said, “I tell them, you’re qualified for everything and nothing. You are learning problem-solving skills, and those are invaluable throughout your life.”
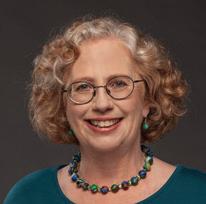
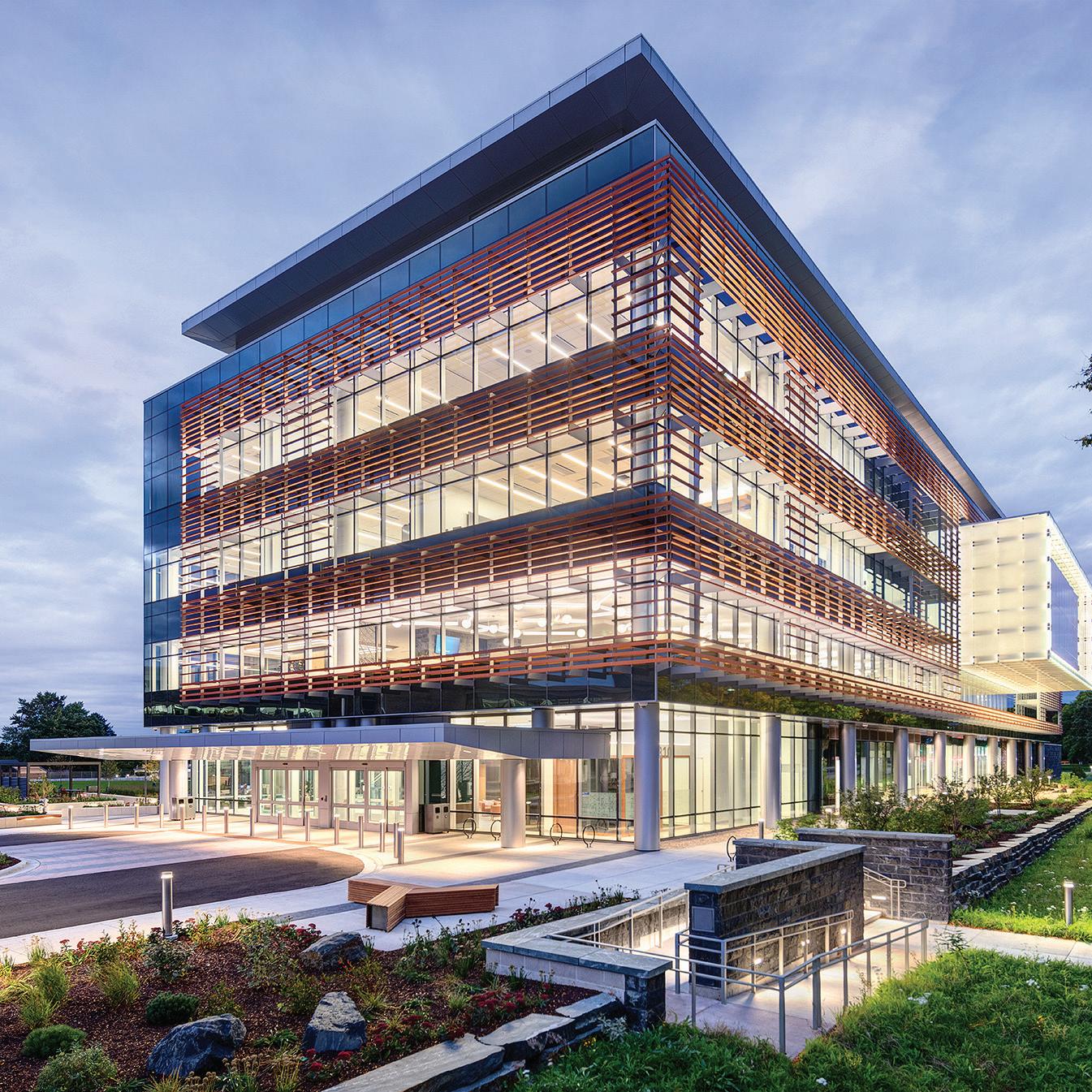

SUSTAINABILITY INC.
BY KRISTINE HANSEN
Wisconsin’s long been a national leader in sustainability.
After all, former Gov. Gaylord Nelson founded Earth Day in 1970. And, in 1968, Madison became the first community in the country to offer curbside recycling. Today, the state ranks number two—only behind California—in its number of organic farms, and has pledged to generate 100 percent carbon-free electricity by 2050. But even before this, Wisconsin’s landscape many environmentalists, including Aldo Leopold, the author of “A Sand County Almanac,” who taught wildlife management at the University of Wisconsin-Madison in the 1930s; and John Muir, who lived on a farm near Portage with his family as a child in the 1850s.
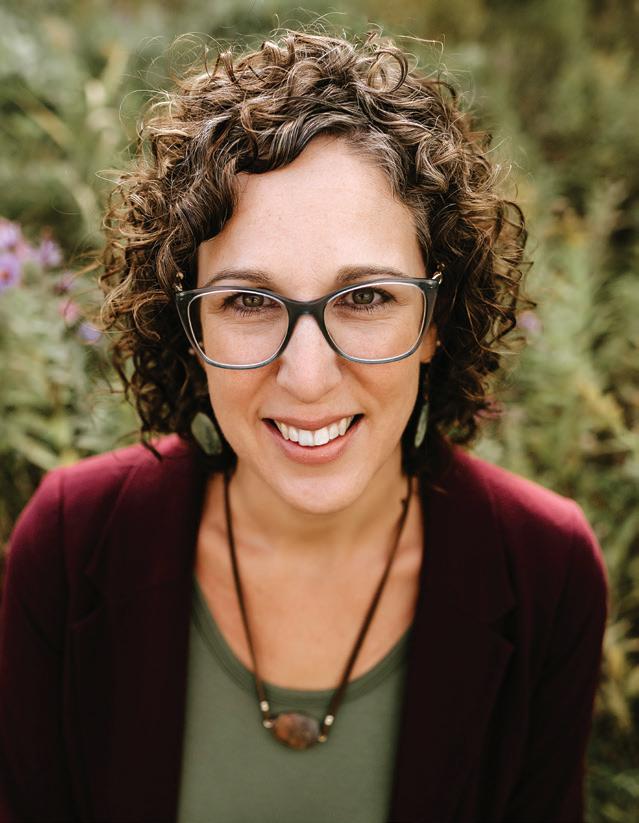
“We have a long history of conservation and outdoor recreation in the state that supports employees and business leaders valuing our natural resources," says Jessy Servi Ortiz, managing director of Wisconsin Sustainable Business Council.
In recent years this sustainability mantra has expanded into the Wisconsin business sector, inching into industries as small and niche as a dental office and a coffee roaster, but also into a major hospital system, a clothing and lifestyle brand, and a manufacturer of boat parts. Whether it’s about adopting renewable energy, offsetting greenhouse gasses, recycling, or using post-consumer recycled materials, earth-friendly innovators are attracting the attention of both their employees and customers.
Organizations like the Wisconsin Sustainable Business Council foster community and conversation within the business sector so that there is a process for sharing both the positives and the pitfalls. One example is the Council’s Green Masters Program®, a virtual tool open to any business wanting to improve its sustainability. Businesses first measure their own performance and then benchmark themselves against the maturing field.
“The tool helps companies define, prioritize, measure and improve their sustainability performance through systems development, best practices and performance improvement,” says Jessy Servi Ortiz, managing director of Wisconsin Sustainable Business Council (WSBC).
Participating in the program entitles them to use the Green Masters Program logo in their marketing. At the Council’s annual conference, businesses convene to continue to learn and share best practices around mitigating risk around climate and improving their environmental and social performance.
“We have a long history of conservation and outdoor recreation in the state that supports employees and business leaders valuing our natural resources,” says Servi Ortiz. “These values often translate to business practices and wanting to leave a legacy for future generations.”
LANDING AN EARTH-FRIENDLY ETHOS
Headquartered in Dodgeville since 1963, the Lands’ End clothing brand is the Midwest equivalent of L.L. Bean and Eddie Bauer, with outerwear, casual clothing, and home goods like towels and comforters. For the company, durability—products that stand the test of time—is built into its DNA.
“From the beginning of Lands’ End, we’ve always had an emphasis on quality products that last for generations,” says Lauren Kasten, the company’s PR manager. “With that in mind, the hope is our customers use our products continuously and don’t have to worry about replacing their items over and over again.” So it was not hard to move toward greater sustainability.
Recently the company issued six product goals to accomplish by 2025. Two have already been met: 100 percent compliance with the Responsible Down Standard (ensures humane treatment of geese and ducks, whose feathers are used for insulation) and 30 percent of garments made with fabric finishes that use less water in manufacture. The three that are left to tackle are: 100 percent cotton from sustainable sources, 100 percent polyester fibers from recycled sources, and—to bring this all together—a product lifecycle component that allows for recycling.
In 2016, Lands’ End started working with Martex Fiber on an innovative project. Material scraps and clothing that can’t be repurposed by Lands’ End are sent to this textile-recycling company and transformed into post-consumer fibers used in a variety of new ways. This includes noise insulation in automobiles as well as bedsheets, socks, knit caps, and home furnishings.
One of the brand’s own products realized through post-consumer recycling is a line of denim pants for women that debuted in 2023. The pants are made of fabric from Recover, a company—like Martex Fibers—that takes textile waste scraps and makes them useful again. Each pair of jeans made from Recover fabric features 20 percent recycled cotton fiber. In addition to this, there is very little indigo dying that takes place in production, another way of limiting water usage in the manufacturing process.
Sustainable Smiles
While much of the sustainability efforts at Madison’s Artisan Dental can actually be put into practice in other office environments, it’s also getting major attention within the dental industry.
Founders Nicole and Scott Andersen—who operate the U.S.’s first carbon-neutral general dentistry practice—were invited to speak at the first Sustainability in Dentistry, a global conference. They’ve also created a no-cost webinar (available on YouTube) for other dentists about how to shift their practice to carbon-neutral status. And, finally, by collaborating with dental-industry suppliers they’re educating others about how dental offices can become even more green.
Their carbon-neutral operation begins with the purchase of 100 percent of its electrical supply through Madison Gas and Electric’s Green Power program, which draws primarily on wind and solar power installations. As for the day-to-day tasks in their office that lean toward sustainability, they include going all-digital with patient records and communications, eliminating toxic cleaning and disinfecting products and also toxic chemicals normally used to develop X-rays, installing low-flow toilets, using low- or no-VOC paints and ceiling tiles, turning to steam sterilization (because it’s nontoxic), and maximizing natural light (using less artificial light) with tons of windows. Carpeting is crafted from 100-percent recycled materials and anybody—not just patients—can bring in toothbrushes, toothpaste tubes, floss containers and mouthwash bottles to be recycled. Artisan Dental partners with the company, TerraCycle, as a public drop-off station for items that don’t qualify for curbside recycling. TerraCycle researches and develops recycling methods for items that would otherwise go in the landfill. The dental office also takes care of recycling clear aligners, a popular product for straightening teeth.
Finally, the company donates one percent of revenue from the Artisan Dental Health Plan to environmental nonprofits, some of which are in Dane County.
The Great State Of Coffee
In the big-wide world of food and drink, locally-owned and community-based coffee roasters have been leading the way when it comes to environmental stewardship and social justice for a long time.
Wonderstate Coffee was founded in 2005 by TJ Semanchin and Caleb Thomas in the agriculturally diverse Driftless Region, which enjoys a flourishing economy for organic and artisanal food. The coffee roaster, originally named Kickapoo Coffee, got its start selling to local coops and boutique grocery stores.
Before launching Wonderstate Coffee, Semanchin worked for seven years at Peace Coffee in the Twin Cities, a leader in organic, Fair Trade coffee since its 1996 founding. That experience has helped Wonderstate Coffee lend more support to coffee farmers to ensure they are paid fair wages. Eighty percent of the farms they work with are smaller than 12 acres and the largest clocks in at 125 acres. Nearly all are family-owned and organic, and keep money in the community. They particularly enjoy working with farms that practice organic fertilization, organic composting, and judicious tree pruning. These practices reduce emissions of carbon dioxide by capturing and keeping carbon in the soil or in the living plants—and out of the atmosphere.
Now keenly aware of how climate change affects these farmers, Wonderstate became one of the world’s first roasters to switch to solar power. This new source of electricity is used for heating, cooling, vacuum systems and lights at the roastery.
As a further commitment to honoring the environmental landscape, including its stewards, in 2019 the co-owners went so far as to change their name—a costly process, as any business owner knows—because they felt Kickapoo Coffee’s name did not belong to them; instead, it belonged to the indigenous Kickapoo Nation.
Wonderstate now has four cafes: in Viroqua, Madison, and Bayfield. At the cafes, efforts are made to compost food waste and offer customers a discount if they bring in a Wonderstate reusable cup—instead of filling yet another paper cup. Bonus: twenty-five cents of each drink purchase supports reforestation efforts at coffee farms. And one dollar from each bag of Organic Canopy coffee goes to a fund that helps plant both shade and coffee trees, with those shade trees protecting the coffee trees from effects of climate change.
Building A True Green Business Model
Known as CUNA Mutual Group until 2022 when they adopted a new brand name, TruStage Financial Group is about more than following the money as most finance-oriented businesses do. While they do sell insurance and investment products to credit unions and their members, the 89-year-old company says it also wants to protect the Earth’s natural resources at the same time.
When building an addition to its west side campus in Madison— dubbed The Lighthouse—TruStage worked with EUA, an architecture firm, to earn LEED Gold certification, the second-highest designation from the U.S. Green Building Council. Earning 72 points, it is the highest point total of any LEED v4 (the newest LEED version) project in Wisconsin with publicly available information.
From triple glazed bird deterrent glass to a 10,000-gallon cistern that collects rain from the roof for reuse, the newly revitalized campus boasts 35 percent restored native vegetation, which also creates a calming environment for workers when coming and going from the office. Energy use was slashed nearly in half thanks to 75 percent of occupied spaces having access to natural daylight and efficient lighting. Indoor water use has also been reduced by nearly 40 percent. The toilets, urinals, and plumbing fixtures alone save an estimated 100,000 gallons of water annually.
Just a peek at the five-story, 125,000-square-foot building reveals this is a smart design. Walls of glass coax in natural light and greenery is abundant, including a living-greenery wall near a floating staircase on each floor. The idea is to make this a healthy and appealing place to work, with a rooftop terrace, auditorium, dining area and collaboration spaces to coax people into conversation and human contact, particularly important after pandemic lock-downs.
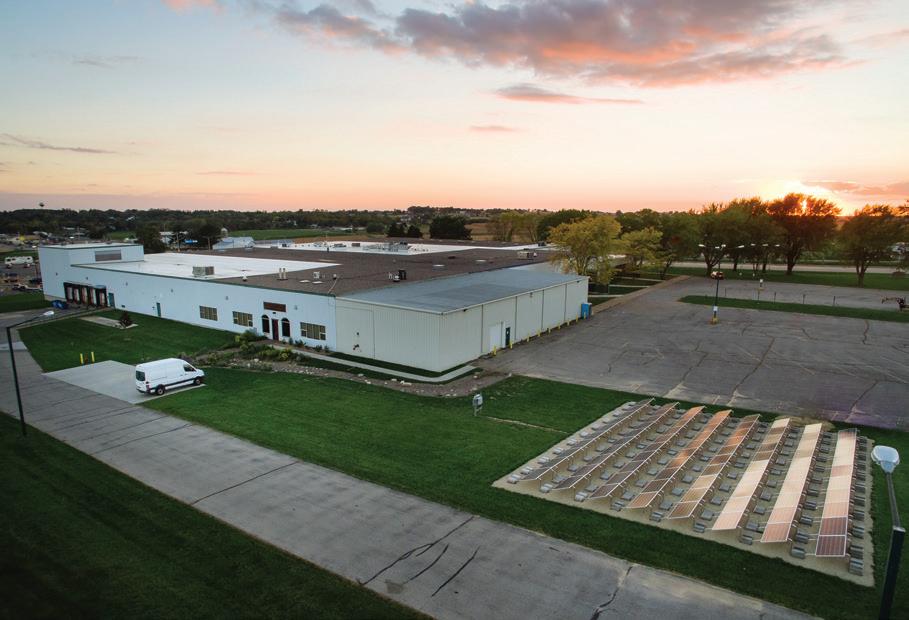
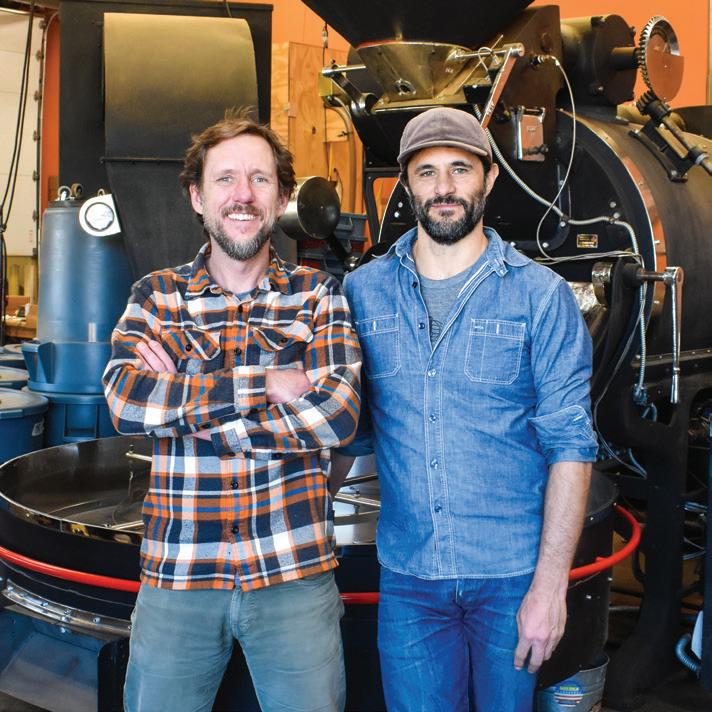
Knowing that asphalt and gasoline are air pollutants, TruStage moved the parking structure underground. They were recently recognized for these efforts by the WSBC’s Green Masters Program.
Gunning For Green
The impetus for this La Crosse hospital and health-care system to include renewable energy in its thinking and planning occurred in 2008. “As an organization, we were building a new hospital and our CEO came to us and said ‘Can we make this a net-zero building?’” recalls Alan Eber. “We said ‘Yes, and we can make the entire corporation net zero.’”
Eber is director of Envision, a wholly owned subsidiary of Gundersen Health System, which functions as its energy and sustainability division. This is a big job since the company operates six hospitals and 70 clinics in Wisconsin, Iowa, and Minnesota.
Instead of the standard way—through a utility—Gundersen Health System was successful in harnessing energy from four other sources: solar installations on-site, biomass (wood byproduct from local wood mills near their northern facilities), biogas from three Dane County farms (cow manure turned into biogas), and local windmills.
It was also important to Gundersen that the energy come from local sources and not out of state wherever possible.
Within the first two years, energy use was reduced by 35 percent at the main campus, in La Crosse. The Legacy Building, completed in 2014, also earned LEED certification.
The company went net-zero for two reasons. One, to reduce costs as a company during a health-care cost crisis. “Today, we’re saving $5.6 million a year,” says Eber. The other reason? If the mission is to keep people healthy and from getting sick, then creating healthy environments free of toxins easily falls in line with that reasoning.
Efforts to incorporate sustainability into one’s business also opens up opportunities that weren’t otherwise there. “It’s helped put us at the table where we might not normally be,” says Eber. “It helped us recruit new staff. We had physicians calling Gundersen to say ‘One of the reasons I want to interview is the sustainability effort,’ especially the younger people.”
In addition to ongoing efforts in La Crosse, Gundersen has since implemented a dozen similar projects centered around renewable energy. Nearly every facility has solar power now. Clinics range in size from 5,000 square feet to 90,000 square feet. In 2014 they became the first energy-independent hospital system in the country—essentially producing an energy surplus.
In January, Gundersen opened a clinic in downtown Elroy as its first on-site, net-zero energy building. This is different from all the other clinics, which rely on energy generated off site, and it represents the company’s movement toward even greater self-sufficiency.
Partnering with local businesses that had waste biofuels to sell was also an important strategy for Gundersen. Examples were a brewery that had a methane byproduct useful for producing electricity, and a county landfill that generated methane gas that could be tapped and used for heating.
A Sea Of Sustainability
As a maker of propulsion systems for boats, and operating as Brunswick Corporation’s marine engine division, encouraging people to get out and enjoy the water is built into all of Mercury Marine’s marketing. So why not also do their best to keep Wisconsin’s waterways as clean as possible?
Looking back to last year, three product introductions are in perfect pitch with those sustainability aims. All are Avator electric outboard motor platforms, the first of which debuted in early 2023 at the Consumer Electronics Show: Avator 7.5e. The process of developing these electric outboards took two years. Swap-in, swap-out batteries charge overnight in a standard household outlet.
According to Brunswick’s 2022 environmental report—the latest data available—Mercury Marine has also made significant progress toward meeting three environmental goals with deadlines in 2025: reduce water consumption by a quarter, energy consumption by 25 percent, and emissions of outboard engines and sterndrive/inboards.
For all of its efforts, the company just received its 13th consecutive Green Masters Level Award, a designation awarded by the WSBC.
In addition to weaving sustainability into their products and services, supporting sustainable-minded initiatives through charitable giving is another mantra for these Wisconsin businesses. Many choose to align with projects close to home, to further preserve the communities in which they are located. For example, Lands’ End became a founding corporate partner of the Clean Lakes Alliance of the Dane County area in 2010 by donating clothing, volunteer hours and money—and continues to be a partner. And, in 2022, Mercury Marine donated $5,000 to Winnebago Waterways Program, whose conservation efforts focus on Lake Winnebago.
“We will continue to see a rise in opportunities for businesses to add value through sustainability,” says the WSBC’s Servi Ortiz. “Exasperated with inflation, climate, and social challenges, consumers are rewarding companies for reducing costs and environmental impact, increasing worker retention and satisfaction, and collaborating with customers and stakeholders for solutions. In turn, those businesses are growing through new customers and markets with whom they didn’t previously have access.”
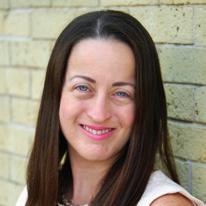
Based in Milwaukee, writer Kristine Hansen loves supporting Wisconsin businesses that advocate for sustainability and climate change, whether it’s wearing her Lands’ End cheetah-print fleece pullover or buying coffee from a coffee roaster like Wonderstate Coffee that pays farmers a fair wage.
PAIRED SOLO EXHIBITIONS
FEBRUARY 23 – MAY 5, 2024
LISA MARIE BARBER Playground
JAYNE KING unearthed
MAY 24 – AUGUST 5, 2024
5-10-100: WOMEN ARTISTS FORWARD FUND
Jennifer Angus, Adriana Barrios, Mary Bero, Yeonhee Cheong, Angelica Contreras, Lilada Gee, Katherine Steichen Rosing, Alice Traore, Babette Wainwright
AUGUST 23 – OCTOBER 20, 2024
NIRMAL RAJA
A Question of Thread
Learn more and register at wisconsinacademy.org/gallery
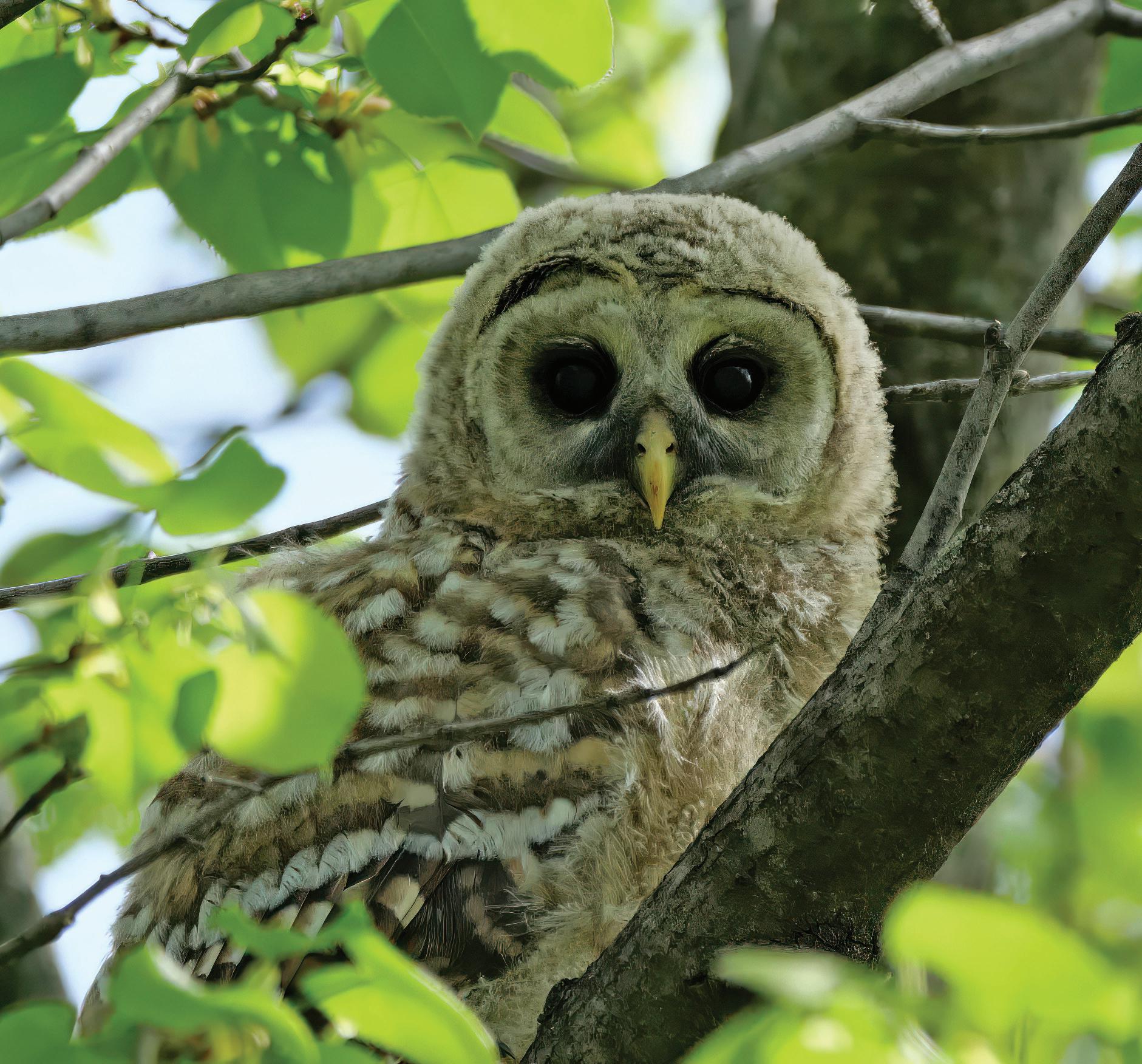
