
11 minute read
Cover Story: Rebound
by WorkBoat
Rebound
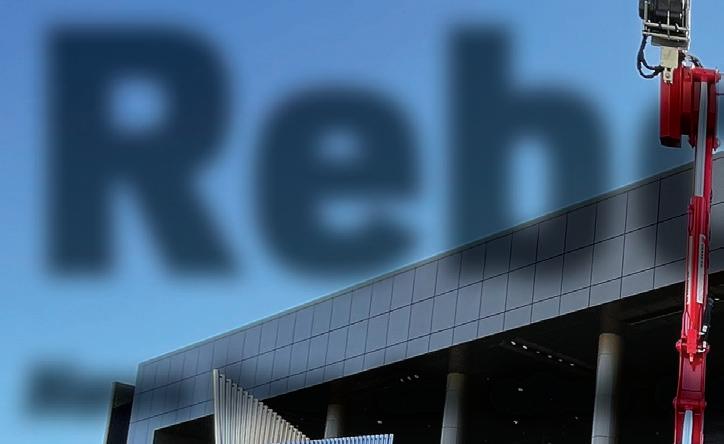
News from the 42nd International WorkBoat Show.
The 2022 International WorkBoat Show, held in New Orleans in December, marked the rst time since 2019 that the show was held while not under the cloud of the pandemic. Last year, the show returned after a two-year hiatus.
And like last year, offshore wind was a major presence. Stability and predictability are two hurdles the U.S. offshore wind industry must clear to build out the new eet it needs, panelists said at a Think Tank session at the show.
“For us, the biggest challenge is seeing these projects permitted and moved forward,” said William Hanson, senior vice president for market development with Great Lakes Dredge and Dock Co. LLC, which is building the rst U.S.- ag subsea rock installation vessel for the U.S. offshore wind market.
“We knew being rst to market with a Jones Act-compliant rock vessel would be attractive,” said Hanson, explaining how Great Lakes studied its plan for several years before having the ship built on spec at Philly Shipyard. The vessel will begin working in 2025 on Equinor’s Empire Wind turbine project off New York Harbor, and has other work lined up into 2030, said Hanson.
After that, “will it be as busy?” Hanson added. “We’ll see.”
The Biden administration’s march toward a goal of 30 GW of offshore wind energy by 2030 has developers and the Bureau of Ocean Energy Management busy, with the agency planning for projects from New England to the Carolinas.
“The key is going to be establishing durability for this industry,” said John Begala, the Business Network for Offshore Wind’s vice president for federal and state policy. Administration planners “need to stick by their 16 COPs (construction and operations plans) by the end of their term. Then we can say this industry is on a glide path to success.”
It’s critical to make sure all sectors of the U.S. maritime industry can share in that future, said Aaron Smith, president of the Offshore Marine Service As-
sociation.
“Look at the show. Anyone can tell you it’s buzzing, it’s packed,” Smith told the standing-room audience for the Think Tank panel titled “U.S. Shipbuilders, Mariners and Operators Role in Offshore Energy.”
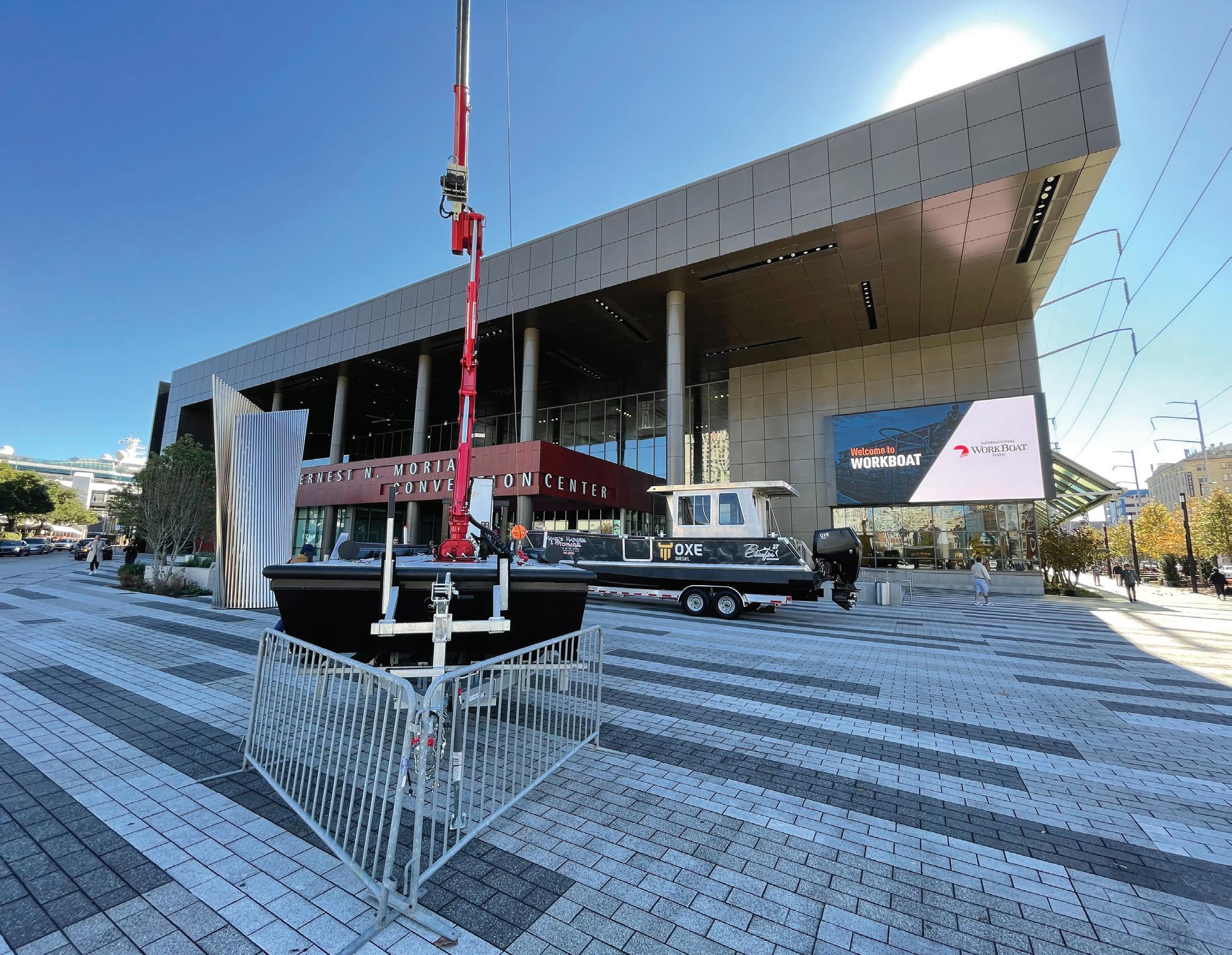

This year’s WorkBoat Show attracted thousands of attendees, marking a return to near prepandemic attendance numbers.
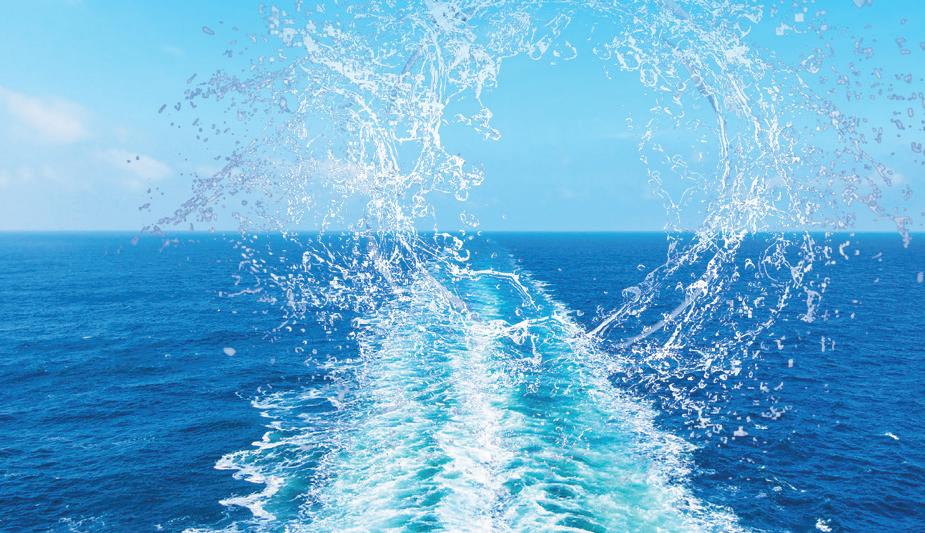
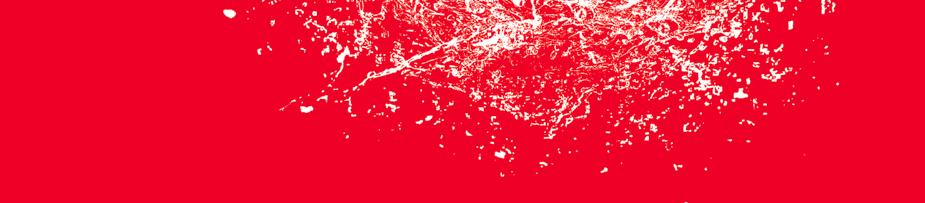
There is a need to “make sure everyone has a level playing eld,” said Smith. “If not, that entire hall is going to be unhappy in a few years.”
“When a foreign- ag vessel is operating in U.S. waters, they can basically hire whoever they want,” said Smith, whose group advocates for tighter enforcement and new legislation to regulate how oil and gas and wind developers can use foreign vessels on projects. All companies have “investors and boards to answer to,” and won’t spend to hire U.S. mariners unless the rules compel them, he stressed.
“The problem comes with exceptions and enforcement that have evolved over time, said Robert Vosbein, executive vice president of Harvey Gulf International Marine.
Crewing an offshore service vessel with a U.S. mariner can cost $700 a day, compared to using a foreign national who works for $100 a day, said Vosbein.
“These are not exaggerations,” Vosbein added. “It’s a completely unlevel playing eld.” Smith cited wind developers’ help-wanted postings on LinkedIn social media pages that explicitly call for non-U.S. mariners.
“We’re very heavily regulated” and foreign vessels and crews need not conform to the same U.S. rules, said Vosbein. It is “incredibly more dif cult” in comparison for a U.S. company to simply move containers on an OSV, he said. The prospect of developers using foreign- ag vessels is a disincentive for U.S. companies to invest in new vessels for the wind market, Vosbein and Smith said.
For U.S. shipbuilders “offshore wind is a generational market,” said Paula Zorensky, vice president of the Shipbuilders Council of America.
Demand will create the market, but the industry needs “stability and predictability … and on-time budgets,” said Zorensky. Much of that certainty needs to come from the government and Customs and Border Protection, with its interpretation of Jones Act questions and related regulations, she said. — Kirk Moore
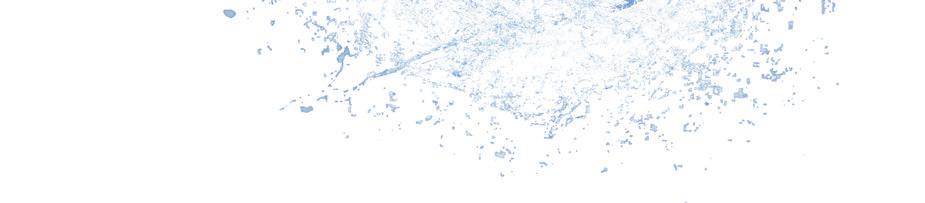
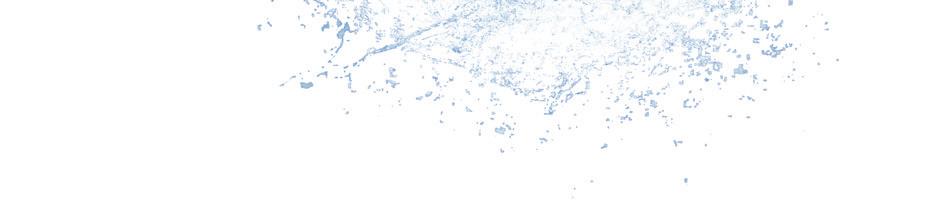
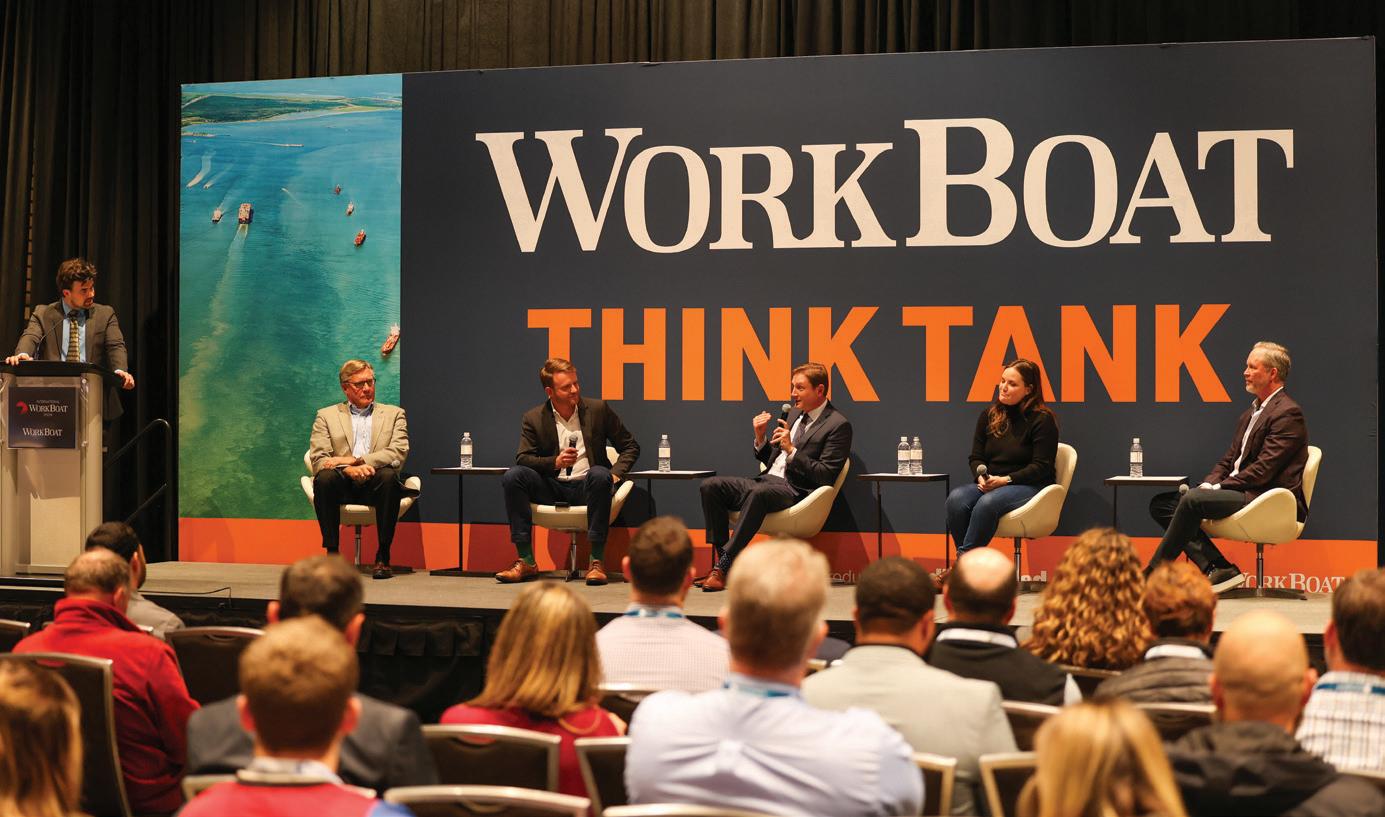
Speakers at a Think Tank session on off shore energy said that the off shore wind energy sector needs stabililty, predictability and on-time budgets.
*** OFFSHORE WIND ADVOCATES SEE GULF OF MEXICO FUTURE
The mega-population centers that attract offshore wind energy companies to the U.S. East Coast are spread farther along the Gulf of Mexico. But the Gulf’s immense industrial appetite for energy is making it look like a good bet for the wind industry’s future.
Two wind energy areas – one 24 miles off Galveston, Texas, with 508,265 acres, and another 56 miles south of Lake Charles, La., with 174,275 acres – are the rst laid out by the Bureau of Offshore Energy Management.
The Gulf states’ industry, with its deep experience in offshore energy work, is already involved in the East Coast wind projects. Some 20% of those contracts have gone to Gulf states, according to the non-pro t Business Network for Offshore Wind, which says half of its new members are from the region.
There are now around 1,200 offshore wind supply contracts in the domestic U.S. market, said Liz Burdock, CEO and president of the Business Network for Offshore Wind during a Dec. 2 update at the WorkBoat Show. Some $12.7 billion invested in the U.S. so far includes $5.38 billion paid to BOEM for leasing.
The investments include upgrades and new construction at 21 ports on the East Coast, and “I don’t think we’re done on the East Coast by any means,” said Burdock. To serve those projects 23 vessels are now under construction or being retro tted, she said.
AN ALTERNATIVE
BALLAST WATER TREATMENT SYSTEM
InVoyage™ + InControl™ = InTank®
NO FILTERS TREAT AT SEA CONTROL COMPLIANCE
www.intankballast.com intank@sciencofast.com
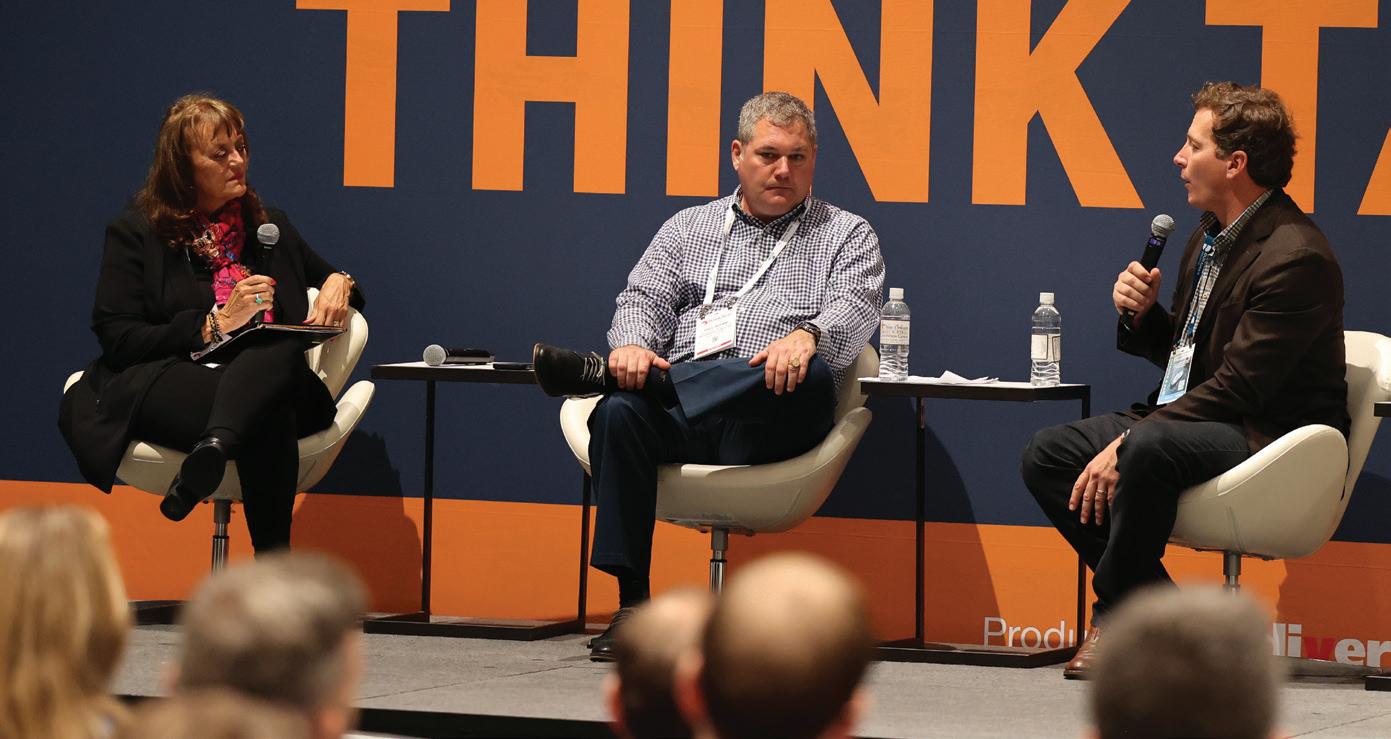
Speakers at a Think Tank panel on the state of the inland waterways said that river conditions in 2022 were reminiscent of 2012.
The industry’s top vessel needs are: wind turbine installation vessels, cable laying ships, feeder barges to carry turbine components, service operations vessels and rock laying ships to place armoring around turbine foundations. Looking at the pace of planned U.S. projects and the supply of vessels, 2026 could be a year of bottlenecks, said Burdock. — K. Moore
*** LABOR SHORTAGE, LOW WATER PLAGUE INLAND OPERATORS
At an International WorkBoat Show Think Tank panel on the state of the inland waterways, much of the discussion centered on the tight labor market and low water levels.
WorkBoat’s Washington, D.C., correspondent Pamela Glass moderated the panel that featured Austin Golding, president of Golding Barge Line, Vicksburg, Miss., and Paul Rhode, Midwest region vice president at the Waterways Council’s St. Louis of ce.
Rhode noted that river conditions this year are reminiscent of 2012, with the caveat that 2022’s low water came earlier than the one a decade ago, and with worse effects at points. He also said the increased media focus around this year’s situation stemming at least in part from the public generally being more focused on the entire supply chain.
Golding said the “stressed” areas were dredging capacity and approachability of docks. He said inland operators have had to deal with variances of as much as 40 or 50 feet over a 12-month period.
The labor shortage is being felt by both marine and land-based companies. It’s something that Golding said is affecting his own business, though he mentions that it’s not really from a lack of workers, but rather workers that are shifting industries. He said they may give the barge industry a try, but then quickly move to other industries like manufacturing and trucking. That leads to retention being the biggest issue rather than simply nding workers, something that can be most effectively solved by ensuring your company provides real opportunities for growth.
Golding and Rhode said that companies need to meet prospective employees where they are by targeting job postings on social media sites and hosting job fairs in more rural areas.
Golding also highlighted the ability to grow within a company, and the path to earning six- gure salaries being much quicker than in most other industries. He also stressed the importance of making vessels as comfortable as possible, ensuring that living spaces “feel like home” by including amenities such as internet access in all bunk rooms. — Matt Collins

Rough Water Performance. Mission Specific. Reliable. Proven.

Professional Grade Rigid Inflatable Boats and Inflatables
*** WORKFORCE DEVELOPMENT CONCERNS TAKE CENTER STAGE

Hiring and retaining workers was on top of everyone’s mind at the WorkBoat Show. Although no one has a silver bullet to solve the workforce problem, training schools and maritime companies have developed new approaches to at-
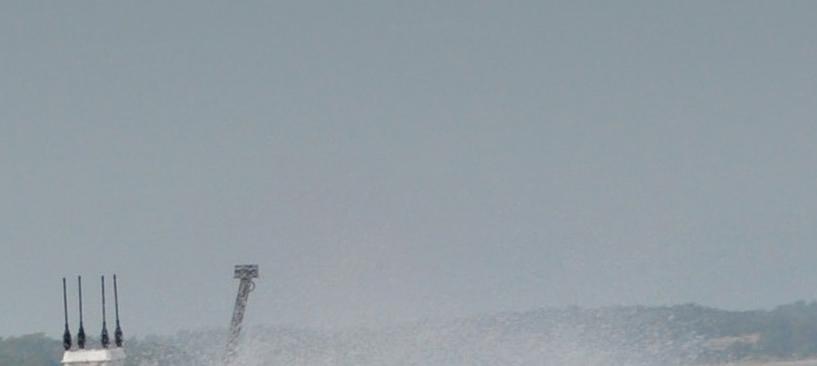
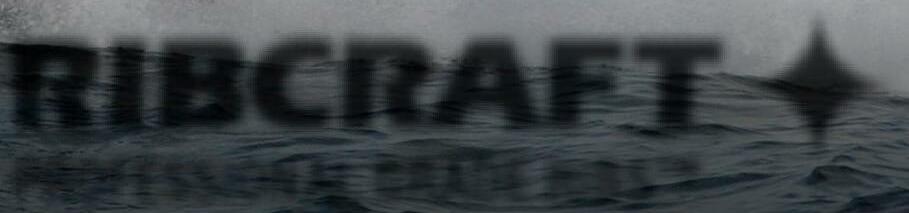
www.ribcraftusa.com • 781.639.9065 • info@ribcraftusa.com PROFESSIONAL GRADE RIBS™
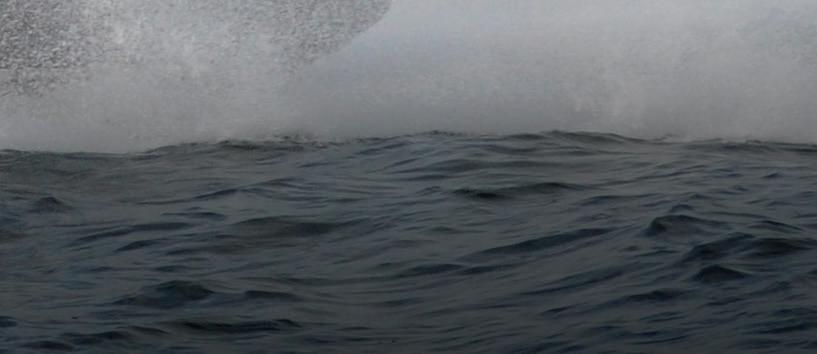
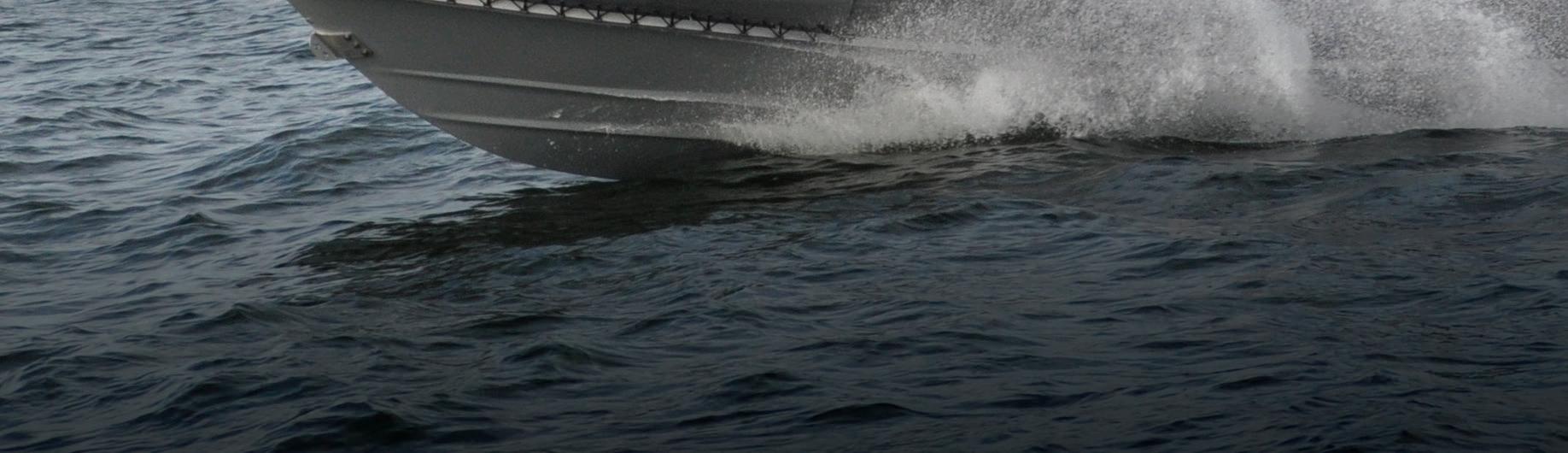

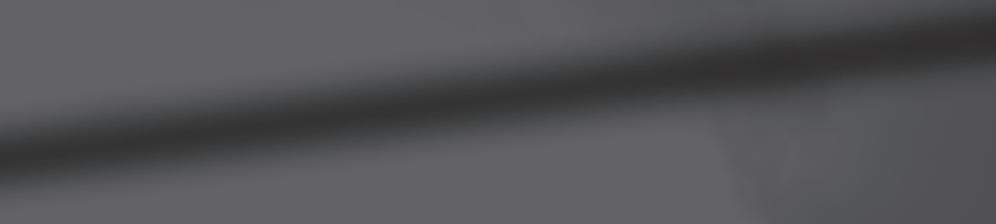

tract new talent and retain those they have.
They cited efforts to reach out early to young kids and their parents (and grandparents), offer good internet connections and comfortable living quarters on vessels, assure strong career paths within a company, make mental health services available, promote jobs as a unique adventure with good pay and bene ts, and retool training to offer a digitalsavvy generation more online instruction when appropriate.
Most agree that the industry does a poor job of promoting itself as a great place to work, and that people beyond the rivers or coasts or those who don’t already have a family maritime connection know little about the profession or the importance of maritime jobs to the economy.
“We need to promote it as an industry that’s exciting,” said Martin Glenday, president of Moxie Media, a New Orleansbased media design and production company that works with maritime clients. “The PR has not been good. This is a great story that doesn’t get a lot of attention.”
Maritime schools are also rethinking how they recruit students, casting a wider geographic, demographic and age net for recruiting, and moving into training students for jobs in emerging energy elds.
Massachusetts Maritime Academy (MMA) has developed a new niche in training for the edging offshore wind industry, promoting it as a new and exciting career opportunity, and explaining to potential students the excitement of being able to train on a new, state-of-the-art training ship that is due to be delivered to MMA in 2024.
The academy, located on Cape Cod, has also extended its outreach programs to students, starting in the fth grade. “We invite them to campus, we are going into schools,” said Maryanne Richards, director of career and professional services at MMA told a WorkBoat Show session on workforce development. “Because of the changing demographics, with not as many students graduating from high school, we are doing more initiatives to children and their parents.”
MMA also offers a summer camp that gives youngsters a avor of life on campus. They experience a navigational simulator, board the school’s training ship and learn about jobs after graduation, she said.
At Delgado Community College in New Orleans, which has a Maritime and Industrial Training Center, the emphasis is on educating “parents, grandparents, brothers and sisters” as well as well as potential students as young as the fourth to seventh grades about maritime careers, according to Rick Schwab, senior director of workforce development and education.
“We let people sit in on navigation class, visit simulators,” he said, adding that the school has prepared a list of quali cations for certain maritime jobs to match a job skill to training requirements. “We have a list of qualities to be competent in a job like mate or tankerman, and we show it to a parent or counselor. They didn’t realize that these vessels are multimillion dollar technical machines. We’re trying to get them to think out of the box of skilled labor being a more






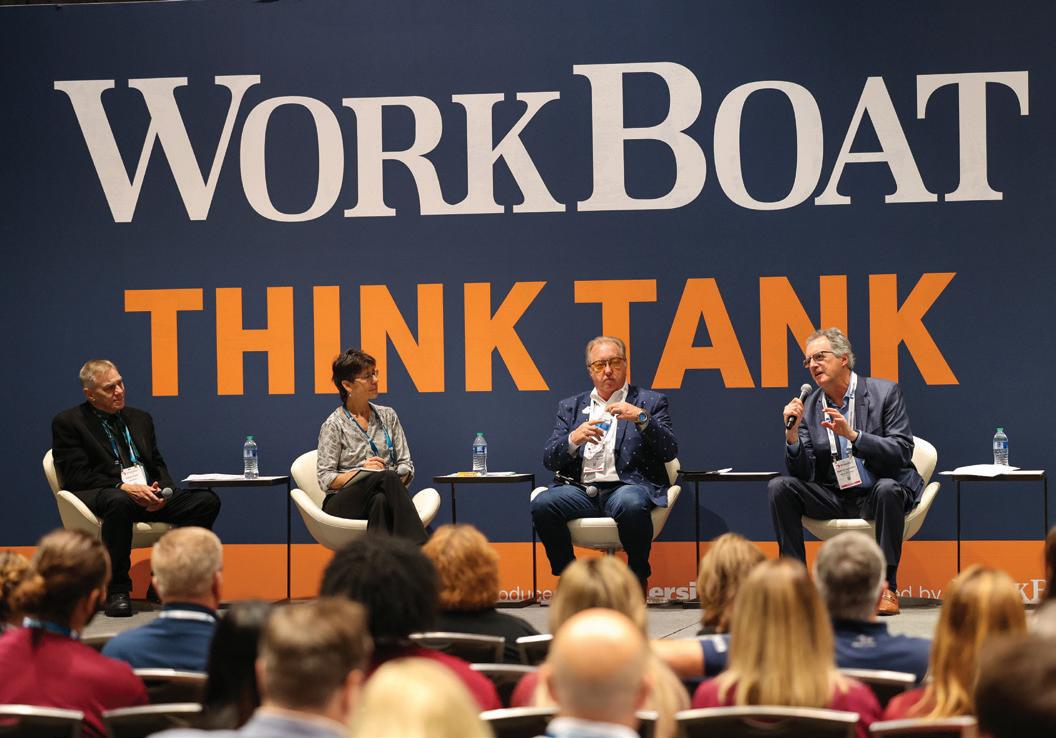
To help address the workboat industry’s ongoing workforce problems, speakers said that the industry must do a better job in promoting itself as an exciting place to work.
technical expertise.”
Schwab said it’s important to show students that there’s a progressive career path in the industry. “You need to give them goals to attain, give people promise and motivation,” he said. “We treat a deckhand like a captain because one day (he or she) will be a captain.” — Pamela Glass
WINCHES
SPECIALTY WINCHES FOR THE MARINE & FISHING INDUSTRY
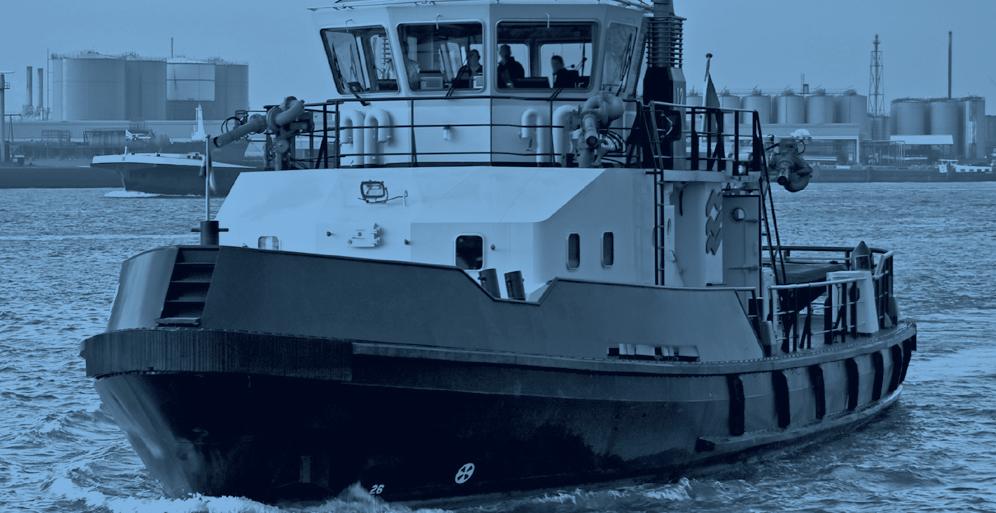
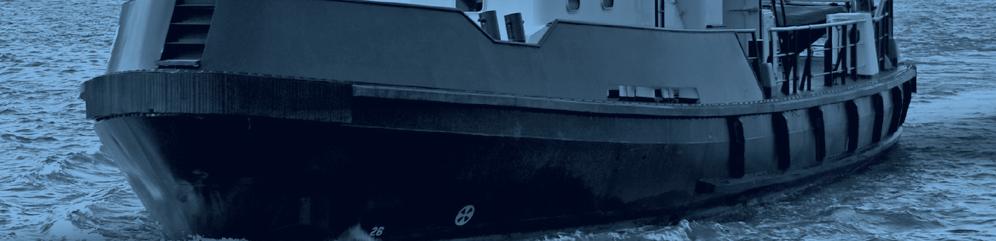


BLOOM MANUFACTURING LLCMANUFACTURING LLC
Custom Engineered Solutions Since 1910Solutions Since 1910
Independence, IA 50644, USA | www.bloommfg.com P: 319-827-1139 | 800-394-1139 | F: 319-827-1140