
4 minute read
Vessel Report: Independence
by WorkBoat
Independent
The evolution of autonomous technology continues.
By Michael Crowley, Correspondent
Sea Machines
Sea Machines’ AI-ris uses digital cameras and AI processing to detect, track, classify and locate obstacles ranging from containerships to something as small as a swimmer, kayaker or animal in the water.
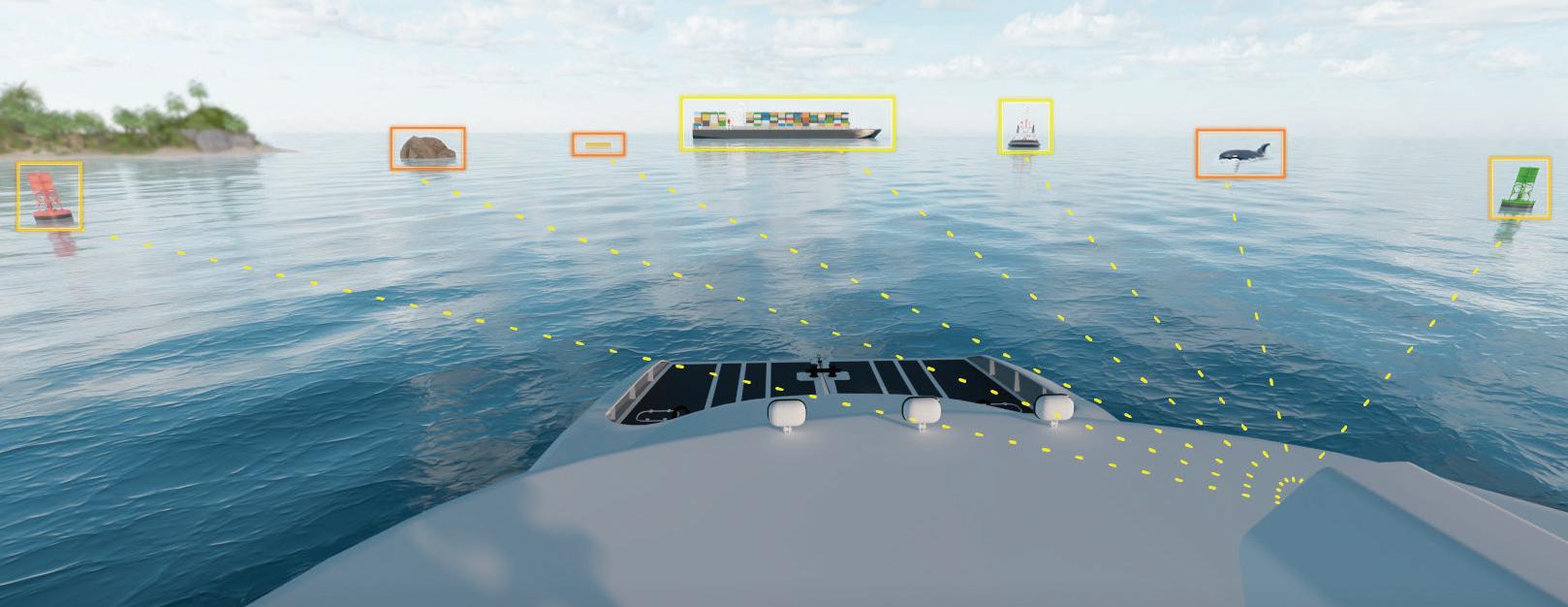
A LOOK INTO THE NEXT GENERATION OF MARINE TECH: At 4 a.m. on March 15, 2019, the Dixie Vandal was pushing a partially loaded fuel barge upbound through the Houston Ship Channel AI-POWERED COMPUTER VISION when it veered off course and struck the moored barge Kirby and its 1,400-hp towboat Trinity.
The cause? Fatigue. The pilot had been on watch for 10 hours of his 12hour shift and did not recall making the course change before falling asleep. There were no injuries. Damages came to $630,230. The Dixie Vandal accident was recounted in the NTSB Safer Seas Digest 2020 along with two other fatiguerelated accidents. Fatigue, which impacts decision-making, reaction time and comprehension, has been a longstanding issue in the commercial marine sector. The accident highlighted a potential weak spot in any vessel. It’s the individual in the wheelhouse, charged with maintaining a constant situational awareness of the vessel and everything around it. Autonomous vessels, with integrated control systems and sensors, don’t get fatigued and have long held the promise of more ef cient and safer navigation and fewer accidents.
SEA MACHINES ROBOTICS | 1
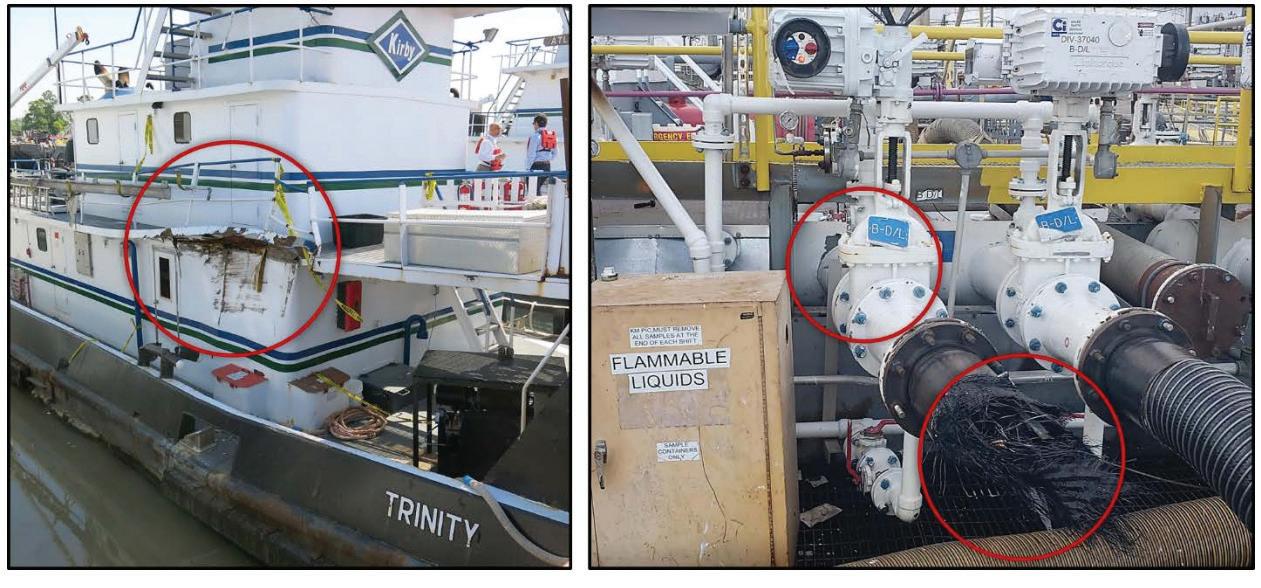
(Above left) Damage to the Trinity’s starboard side from the impact of barge Kirby 29751. (Above right) Damaged shoreside cargo hose and deformed piping at the manifold at the Kinder Morgan Pasadena Liquids Terminal in Pasadena, Texas. SEA MACHINES AI
In June, Sea Machines Robotics introduced one of the most recent examples of autonomous technology’s ongoing evolution at Seawork in Southhampton, England, the largest European commercial marine exhibition. There Sea Machines unveiled AI-ris (arti cial intelligence recognition and identi cation system), which uses digital cameras and AI processing to detect, track, classify and locate obstacles ranging from containerships to something as small as a swimmer, kayaker or animal in the water.
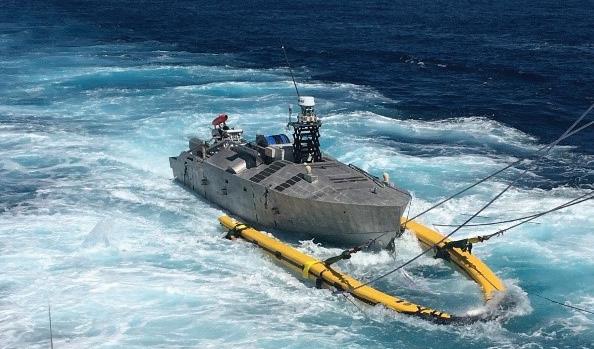
Sea Machines
Sea Machines and HamiltonJet have combined to create JETsense. It uses the Sea Machines autonomus platform with HamiltonJet’s waterjet propulsion. Pictured is a HamiltonJet test boat outfitted with the JETsense platform.
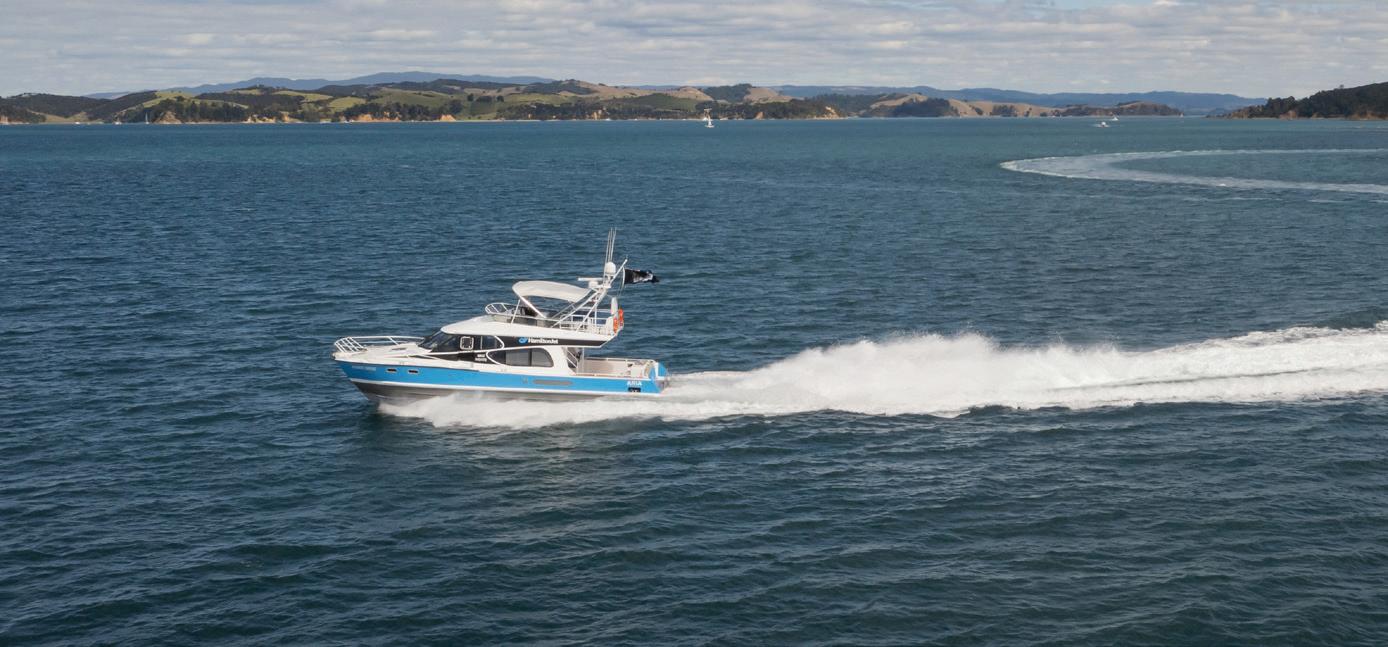
It’s all done much quicker and in a more thorough manner than if your vessel depends on having someone constantly checking the radar and looking out wheelhouse windows.
Al-ris relies on optical sensors and AI processing that continually scans the surrounding water to locate and classify other vessels or objects, be it day or night, and then alert the operator.
“AI-ris integrates with the vessel’s MFD to showcase what the system detects, classifies and tracks,” said Sea Machines marketing director Vanya Banjac.
AI-ris calculates the range and bearing of each target, whether it’s floating or fixed. Each target is then assigned an ID, and a guard zone radius is created around each target. An alert signal is released if your vessel enters the guard zone.
“With the ability to detect, classify and geolocate such targets via optical sensors, Al-ris augments and surpasses the capabilities of existing marine sensor technologies, like radar and AIS,” said Sea Machines CEO Michael Johnson in a press release.
On another level and taking autonomous vessel technology a step further by bringing waterjet propulsion to the forefront of 21st century navigation, Sea Machines Robotics and HamiltonJet introduced JETsense at the 2021 International WorkBoat Show in New Orleans. JETsense combines Sea Machines’ autonomy platform with HamiltonJet propulsion systems and vessel controls.
“JETsense is the first product in the market to incorporate Sea Machines’ advanced vision package,” said Ben Reed, HamiltonJet’s managing director. “It pairs onboard autonomy with enhanced situational awareness in a way that is highly desirable in many manned applications. We prioritized helm integration and the ease-of-use for mariners.” JETsense works with HamiltonJet’s AVX electronic controls. Together they are designed to reduce onboard workload and increase safety. In the commercial marine market, JETsense is viewed as a good product for “fast moving applications, for example, the ferry market,” said Banjac.
UNMANNED NAVY VESSELS
In April, Bollinger Shipyards announced that it is building mine countermeasure unmanned surface vehicles (MCM USVs) for the Navy designed to detect and destroy undersea mines. The MCM USV will replace the Navy’s
U.S. Navy Avenger-class minesweeping ships and the MH-53E Sea Dragon helicopters.
Initially three vessels will be built, though there could be options for 24 additional vessels and a contract potentially worth $123 million. Most of the work will be at Bollinger’s Lockport, La., facility.
The Bollinger contract is one of the most recent moves by the Navy to develop fleets of large and medium-size USVs.
Back in 2019, the Navy solicited large unmanned surface vessel (LUSV) design proposals for autonomous navigation and afloat strike missions. The designs combined current warfare systems with commercial technology platforms. The unmanned vessels would have to be able to operate with manned warships for at-sea combat. The LUSVs would work by remote control and meet international regulations for avoiding collisions.
A year later, in 2020, six companies (including Bollinger) were awarded twoyear contracts potentially worth $59.5 million to conduct studies for the Navy’s LUSV development program.
In May, the Navy established the Unmanned Surface Vessel Division for the Pacific Fleet. It’s designed to be “the catalyst for innovation as we employ unmanned surface capabilities in the Pacific fleet,” Vice Adm. Roy Kitchener said in a statement. “The implementation of unmanned systems will increase decision speed and lethality to enhance our war fighting advantage.”